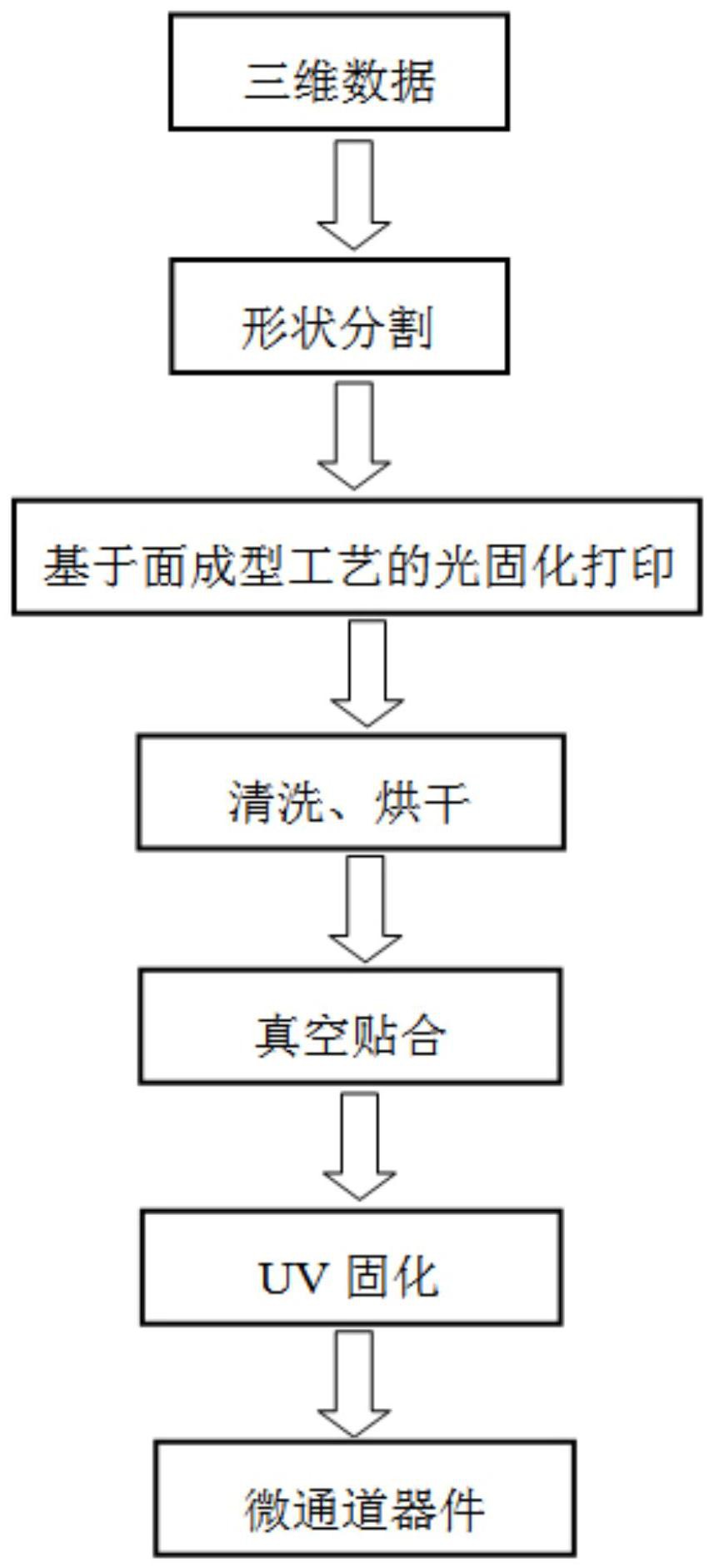
技术摘要:
本发明涉及一种微通道器件加工工艺,依序包括以下步骤:在计算机内建立待加工的微通道器件三维数据模型;使用光固化打印机按照所得三维数据模型打印凹型板及平面板,所述微通道器件的微通道凹槽打印在所述凹形板表面,所述平面板表面平整无凹槽;对凹型板及平面板进行 全部
背景技术:
微通道器件又称微流控芯片,是生化分析、医疗诊断的重要器件,可以将生物、化 学、医学分析过程的样品制备、反应、分离、检测等基本操作单元集成到一块微米尺度的芯 片上,自动完成分析全过程。从材质上主要包括玻璃芯片、高分子聚合物芯片及金属材质芯 片等种类,其中高分子聚合物芯片中又以PDMS(聚二甲基硅氧烷)芯片最为常见。 现有的微通道器件的加工方式主要有包括湿法腐蚀、光刻及倒模、CNC(数控机床) 设备加工和开模及注塑。湿法腐蚀主要应用于制作玻璃芯片,该工艺的加工精度可至10-25 微米,但是通常需要结合光刻等工艺来进行加工,加工成本高昂且操作繁琐。光刻及倒模工 艺主要应用于PDMS芯片的加工,其加工精度可以达到几微米,但是该工艺需要使用光刻胶 制作模具,工艺过程复杂,且模具成本高昂。CNC设备加工可以用于加工聚合物材质芯片及 金属材质芯片,其加工通道宽度的最小极限为100微米左右,但是CNC设备自身价格高昂。开 模及注塑工艺则受限于模具的加工工艺,对通道形状有限制,难以加工较为复杂的结构,且 使用该方法加工需先加工模具,耗时长且模具价格昂贵,灵活性差,芯片结构变动时需要重 新开模,模具成本较高。 上述四类加工工艺均无法兼顾加工灵活性及低成本,加工工艺过程复杂、配置成 本高,主要适用于微通道器件的批量化生产,但在针对单件、小批量的微通道器件加工时, 加工效率低、加工工艺繁琐,难以在满足个性化定制需求的前提下降低成本。
技术实现要素:
本发明的目的在于克服现有技术中的缺点与不足,提供一种可以满足个性化定制 需求且成本低廉的微通道器件加工工艺。 一种微通道器件加工工艺,依序包括以下步骤: S1:在计算机内建立待加工的微通道器件三维数据模型; S2:使用光固化打印机按照步骤S1所得三维数据模型分别打印出凹型板及平面 板,其中,所述凹型板表面上打印有微通道器件的微通道凹槽,所述平面板表面平整无凹 槽; S3:对S2所得的凹型板及平面板进行清洗干燥; S4:将经过步骤S3处理的凹型板及平面板进行真空贴合,其中,所述凹型板上打印 有微通道凹槽的面为贴合面; S5:对步骤S4所得的真空贴合后的凹型板及平面板进行UV固化处理。 相对于现有技术,本发明采用低成本的光固化打印机进行面成型,具有成型基板 平整度好、制作效率高、操作简单和成本低的特点。可直接用于单件或小批量的微通道器件 的快速制造,大幅降低了微通道器件的生产成本,简化了微通道器件的生产工艺,该工艺方 3 CN 111589477 A 说 明 书 2/4 页 法针对单件或小批量生产微通道器件非常高效。 进一步,所述步骤S1中的所述三维数据模型在建立好后,沿所述微通道器件模型 的微通道凹槽其中一侧底面所在平面,对所述三维数据模型进行形状分割,分割成带有凹 槽的凹型板模型和不带凹槽的平面板模型。便于后续对凹型板及平面板的打印。 进一步,所述凹型板与所述平面板贴合面投影形状相同,在所述凹型板与所述平 面板贴合面的相同位置,分别设置有相匹配的定位槽与定位凸台,所述定位槽的深度大于 所述定位凸台的凸起高度。便于真空贴合时凹型板与平面板的定位,同时也不会导致二者 无法紧密贴合。 进一步,所述步骤S2中所述凹型板与所述平面板为同时打印。可以保证凹型板与 平面板上下表面具有相同的平面度和材料属性。 进一步,所述步骤S2中所述光固化打印机为基于LCD屏透射式面成型技术的光固 化打印机或DLP光固化打印机。基于LCD屏透射式面成型技术的光固化打印机最高可制造通 道尺寸为100微米的微通道器件,基于面投影成型技术的DLP光固化打印机最高可制造通道 尺寸为50微米的微通道器件。 进一步,所述步骤S3中清洗所使用的清洗剂为无水乙醇。确保清洗过程无毒无害 且成本低廉。 进一步,所述步骤S3中清洗的方式为流动清洗十秒至三十秒。可将所述凹型板与 平面板表面的多余树脂冲洗干净。 进一步,所述步骤S3中干燥方式为鼓风烘干。可以将清洗剂快速烘干。 进一步,所述步骤S4中在进行真空贴合前先对所述凹型板与所述平面板相对应的 所述定位槽与所述定位凸台对齐。可以避免在真空贴合过程中所述凹型板与平面板发生错 位。 进一步,所述步骤S4中的真空贴合在真空贴合机中进行,真空贴合时间至少为5分 钟。确保所述凹型板与所述平面板实现完全贴合。 附图说明 图1为微通道器件加工工艺流程图; 图2为液滴生成器三维数据模型示意图; 图3为液滴生成器模型形状分割示意图; 图4为制得的液滴生成器微通道器件示意图。