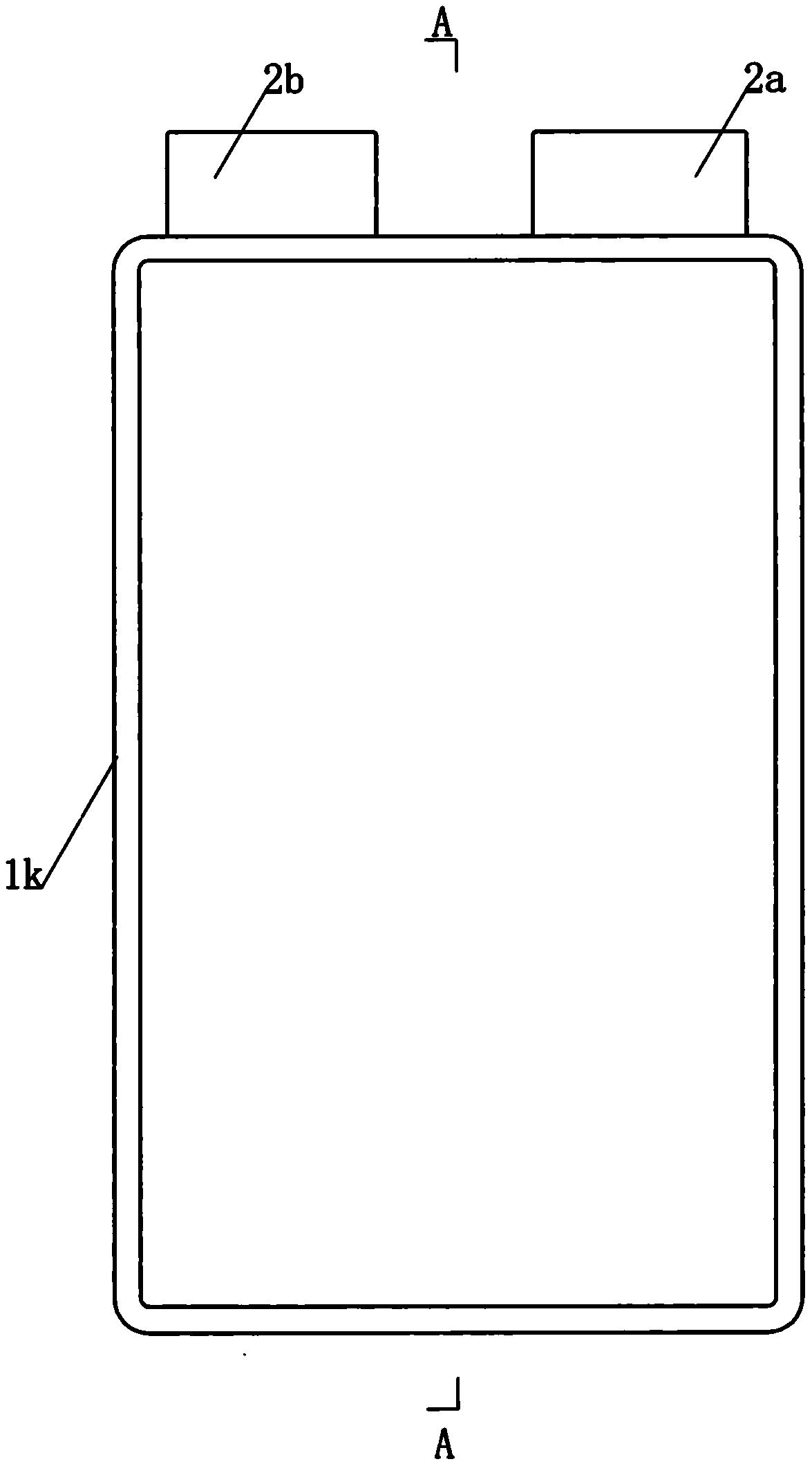
技术摘要:
本发明公开了一种交错极耳结构锂电池技术方案,主要由,电芯、前置外壳、后置外壳、分切开槽导电正极、分切开槽导电负极,邻边正极极片耳、邻中正极极片耳,邻边负极极片耳,邻中负极极片耳,泄压阀组成;通过改进极片极耳,以交错极耳结构,与现有电芯极片极片耳相比 全部
背景技术:
锂电池外形结构主要有圆柱、矩形刚性外壳、矩形软包系列,单体电池能量密度比 较,圆柱>矩形软包>矩形刚性外壳;但是,单体电池集成电池系统之后,圆柱、矩形软包类 型电池能量密度的优势并不显著,三种类型各自优缺点都很突出; 圆柱电池的优点是设备和工艺较为成熟、生产效率高、成本低、一致性较好;由于 圆柱电池采用电池极片螺旋卷绕,径向层层围绕包裹,径向导热性能差,仅有圆柱电池的端 头;电池正极片、负极片的两条边对外导热。为了克服电池内部的温度分布不均匀,需要合 理的布置电池正极片、负极片极耳位置、极耳个数,通过极耳和电池正极片、负极片的端边, 对圆柱电池的端头导热,电池的卷绕层数也不能太多,层数越多,圆柱电池的圆心温度越 高,因而,单体圆柱电池容量较小,在电动汽车上应用时,需要数千上万个单体圆柱电池集 成,大量单体圆柱电池串联、并联集成的连接接点电阻损耗,庞杂的热管理、能量均衡管理 系统,管理系统自身能耗大大增加。不但导致系统成本高,还会大幅度降低系统的可靠性。 矩形软包电池以铝塑复合膜为外壳,常为矩形叠片、或椭圆卷绕。 椭圆卷绕;由单片正极片、负极片叠层卷绕,再通过矩形模具定型。 叠片式;是由多层矩形正极极片、隔膜、矩形负极极片,叠层而成。 矩形软包电池的优点有以下几个方面: (1)电池的矩形正、负极极片之间平面,相向紧贴受力较为均匀,使得电池的极片 上的电流密度分布较为均匀,内阻较小,可以降低电池内阻的自耗电; (2)与圆柱电池不同,矩形软包电池各层电池的矩形正、负极极片四条边,以及矩 形电芯的两个平面对外导热,且散热面积大,因此散热性能具有优势; (3)矩形软包电池在温升引起产气,导致内压增高,增高至铝塑复合膜封装结构耐 压临界时,能胀裂矩形软包的封装粘接结构而泄压,起到安全保护作用; 但是这一特点也是矩形软包电池缺陷,电池内压力增大时,铝塑复合膜的热熔粘 接结构总是处于抗撕裂应力状态,这对于电池有效使用寿命带来负面影响。 矩形软包电池缺点: (1)由于矩形软包包壳非刚性结构,在制造工艺过程机械定位性差,生产效率较 低; (2)由于矩形软包包壳非刚性结构,包壳结构强度较差,定位与测量误差大,机械 加工尺寸公差难于保证一致性; (3)由于制造环境的四季、昼夜温差,铝塑复合膜热熔温度因四季、昼夜温差有所 不同,封口工艺难控制,容易发生漏液; (4)矩形软包电池使用场所温度较高时,高温耐受性差,机械强度低; (5)矩形软包电池内的绝缘膜可靠性差,大多数电芯极片周边有铜箔和铝箔毛刺, 3 CN 111613837 A 说 明 书 2/11 页 矩形软包电池封装抽真空工序,矩形软包在负压作用下收缩,电芯极片的铜箔和铝箔毛刺 可能会刺破铝塑复合膜外壳内绝缘膜,引发短路;毛刺刺破铝塑复合膜外壳内绝缘膜,导致 电芯内的电解液腐蚀铝塑复合膜的金属铝,金属铝溶解进入电解液中,改变电解液的成分 组成,甚至改变电解液的性能。 (6)铝塑复合膜制造工艺复杂,材料成本较高; (7)虽然矩形软包电池能量密度相对较大,但是,软包结构电池集成系统时,由于 铝塑复合膜外壳非刚性结构,需要克服相邻电池膨胀的挤压效应,相邻电池热膨胀体积增 大,厚度方向尺寸增大,这种膨胀性挤压可能直接导致电池内部隔膜破裂引发短路,造成危 险。 (8)矩形软包单体电池集成系统必须将软包结构进行补强,以满足抗震、抗冲击的 安全强度需要,补强结构,会降低其矩形软包单体电池能量密度优势。 (9)矩形软包电池还存在单体电池容量不允许大规格的技术约束,如:矩形软包电 池,铝塑复合膜材料制作包壳时,电芯的安装坑位,限于铝塑复合膜拉伸深度,现有的铝塑 复合膜材料制作包壳时不能将电池设计厚度大于12mm;因为,现有铝塑复合膜的拉伸深度 不得大于6mm,两片拉伸6mm的电芯包壳,相向组合最大的坑深12mm。安装电芯的坑深仅有 11.7mm;单体电芯正、负极极片数量受到限制,这就限制了单体矩形软包电池大容量。 由于铝塑复合膜限于制造外壳时拉伸深度,无法装入更多层数极片的电芯,设计 更大的单体电池,需要展宽极片平面方向的尺寸,极片平面方向的尺寸展宽,会因铝塑复合 膜材料刚度性能差,导致矩形软包电池变形,甚至整体松垮,尤其是用于电动汽车,震动环 境下抗冲击、抗震性能更差。 矩形刚性壳电池;矩形刚性壳电池其外壳,有不锈钢、铝合金、碳钢、塑料;其电芯 有卷绕式,层叠式; 与前两种结构相比、矩形刚性壳电池封装可靠性、抗震动,抗冲击机械性能较好。 矩形刚性壳电池的外壳,不同于矩形软包电池的铝塑复合膜材质受限拉伸,安装 电芯坑深的尺寸,允许比铝塑复合膜制造外壳更大深度,矩形刚性壳电池的外壳允许安装 更多层数极片的电芯,使得单体电池以更大容量; 由于刚性壳的机械强度优势,允许单体电池平面方向更大尺寸,从而提高单体电 池容量,降低系统集成成本。 但是矩形刚性壳电池也存在制造工艺瓶颈;电池的电芯极片外型尺寸,与壳体内 必须无活动间隙,以避免电芯在壳体内的自由晃动,在震动或冲击环境下,电芯在壳体内自 由晃动,必然导致电芯垮塌,这种垮塌是毁坏性的。 矩形刚性壳电池也存在制造工艺瓶颈还在于;矩形刚性壳通常为竖井式结构,制 造工艺的电芯入壳装配;一方面需要做到电芯在壳体内无活动间隙的配合,另一方面需要 避免电芯入壳装配挤压电芯,导致电芯的正极极片、负极极片错位。 竖井式矩形刚性金属壳结构的顶盖封装,通常采用激光焊接,焊缝位于竖井式矩 形金属壳口沿与顶盖相切的顶角四条边沿,依据焊接工艺特性,这种边沿角焊缝难于形成 密封接头,焊缝接头易泄漏,导致矩形刚性壳电池成品率大幅降低。 采用塑料材质的矩形刚性壳电池,虽然可以采用非激光焊接封盖工艺,避免焊缝 接头泄漏问题,但是,塑料材质的矩形刚性壳在热胀变形之后,矩形刚性壳的尺寸被胀大, 4 CN 111613837 A 说 明 书 3/11 页 属不可逆变形,导致电芯在壳体内的自由晃动。 矩形刚性壳电池允许安装更多层数极片的电芯,使得单体电池容量增大提供了可 能,但是及片层数又受到超声焊接极耳工艺限制,层数太多,无法在现有超声波震动能量穿 透,导致电芯的极片极耳与导电连接焊接接头层间虚焊。 电芯的极片极耳与导电连接焊接接头层间虚焊;会导致电池充放电时,因超声波 焊接区局布电阻增大,电芯的极片极耳与导电连接的超声波焊接区发热严重,当高温热传 导至极耳从矩形刚性壳引出密封处时,导致极耳密封绝缘材料受热变形而失效,直接导致 电池损坏,甚至引发安全事故。 单体锂电池容量增大,有助于减低系统成本,有助于提高系统安全性,但是现有的 单体电池结构都存在缺陷;矩形软包限于铝塑复合膜拉伸性能,矩形刚性壳电池存在超声 焊接极耳工艺限制,圆柱结构的螺旋层层围绕电芯散热不良,现有的技术提高单体电池容 量存在瓶颈。
技术实现要素:
本发明针对现有单体锂电池结构缺陷,改进极片极耳,改进矩形刚性壳结构,改进 封装结构,改进泄压阀,提供一种交错极耳结构锂电池技术方案。 实现本发明一种交错极耳结构锂电池的技术方案 一种交错极耳结构锂电池,主要由,电芯、前置外壳、后置外壳、分切开槽导电正 极、分切开槽导电负极,邻边正极极片耳、邻中正极极片耳,邻边负极极片耳,邻中负极极片 耳,邻边负极保护片、邻中负极保护片、邻中正极保护片、邻边正极保护片、泄压阀组成; 电芯安装于由前置外壳、后置外壳组成的密封矩形壳内; 电芯的分切开槽导电正极、分切开槽导电负极,从前壳右位电极凹槽、前壳左位电 极凹槽、后壳右位电极凹槽、后壳左位电极凹槽引出; 泄压阀,安装于后置外壳上方的注液孔; 邻边正极极片耳,置电芯的右上方外侧; 邻中正极极片耳,置电芯的右上方内侧; 邻边负极极片耳,置电芯的左上方外侧; 邻中负极极片耳,置电芯的左上方内侧; 分切开槽导电正极,与邻边正极极片耳、邻中正极极片耳紧贴; 导电正极的分切开槽两边是超声波焊接位,采用超声波焊接。将分切开槽导电正 极与邻边正极极片耳、邻中正极极片耳组成导电良好的连接; 分切开槽导电负极,与邻边负极极片耳、邻中负极极片耳紧贴; 导电负极的分切开槽两边是焊接位,采用超声波焊接。将分切开槽导电负极与邻 边负极极片耳、邻中负极极片耳组成导电良好的连接; 分切开槽导电正极,与邻边正极极片耳、邻中正极极片耳紧贴; 邻边正极极片耳的焊接位对称背面,是邻边正极保护片; 邻中正极极片耳的焊接位对称背面,是邻中正极保护片; 分切开槽导电负极,与邻边负极极片耳、邻中负极极片耳紧贴; 邻边负极极片耳的焊接位对称背面,是邻边负极保护片; 5 CN 111613837 A 说 明 书 4/11 页 邻中负极极片耳的焊接位对称背面,是邻中负极保护片。 电芯的: 邻边正极极片耳,各片对齐; 邻中正极极片耳,各片对齐; 邻边负极极片耳,各片对齐; 邻中负极极片耳,各片对齐; 隔膜置邻边正极耳极片、邻边负极耳极片、邻中正极耳极片、邻边负极耳极片之 间,使正、负极片分隔,并且绕裹四周。 后置外壳,包括,后壳右位电极凹槽、后壳左位电极凹槽、后壳框沿平边、熔胶排气 孔、后壳矩形凹坑、注液孔、注液孔内翻边、后壳胶衬、后壳金属外壳; 前置外壳,包括,前壳右位电极凹槽、前壳左位电极凹槽、前壳框沿平边、前壳矩形 凹坑;前壳胶衬、前金属外壳; 泄压阀安装于后置外壳的注液孔,注液孔内翻边与泄压阀的径向凹槽胀紧密封。 所述的电芯,由邻边正极耳极片、邻中正极耳极片、邻边负极耳极片、邻中负极耳 极片、隔膜组成; 依照,从第一片起; 邻中负极耳极片、隔膜; 邻中正极耳极片、隔膜; 邻边负极耳极片、隔膜; 邻边正极耳极片、隔膜; 邻中与邻边极耳极片交错顺序叠层,根据电池容量需要,决定叠层总数。 所述的后置外壳框沿平边的后壳胶衬、前置外壳前壳框沿平边的前壳胶衬,相向 贴紧,通过热熔粘接密封。 后壳框沿平边的熔胶排气孔,在胶衬热熔密封封装时,后壳框沿平边与前壳框沿 平边受压紧作用,排出熔胶产生的气体,有利提高后置外壳与前置外壳构成置放电芯容器 的密封性能。 所述的后壳胶衬、前壳胶衬,将后置外壳的后壳框沿平边、前壳框沿平边、后壳右 位电极凹槽、后壳左位电极凹槽、前壳右位电极凹槽、前壳左位电极凹槽、前壳矩形凹坑、后 壳矩形凹坑全覆盖; 分切开槽导电正极、分切开槽导电负极,从后壳右位电极凹槽、后壳左位电极凹 槽、前壳右位电极凹槽、前壳左位电极凹槽引出位,被胶衬粘接密封。 所述的胶衬,其材料是乙烯-醋酸乙烯共聚物(EVA)热熔胶,属一种热熔粘接胶膜, 常温下无粘性,便以操作,经加热一定温度便发生熔融,冷却后交联固化。 EVA热熔胶熔的熔融态表面张力小、流动性好,不需溶剂,不含水份,常温下为固 体,对环境影响小、粘着力强,固化后胶层既有一定柔性、又有一定的韧性和硬度;具有优良 的耐化学腐蚀性、热稳定性、耐候性和电气性能,具有优良的结构胶的抗拉强度,文献记载, EVA热熔胶粘接铝片的抗剥离强度可达4.1kN/m[韩友泉等,EVA热熔胶膜的制备及在金属与 陶瓷复合中的应用[J]粘接,2017年第7期],现有的锂电池所用的铝塑复合膜的抗剥离强度 仅有0.6kN/m左右。 6 CN 111613837 A 说 明 书 5/11 页 所述的分切开槽导电正极,是采用超声波焊接连接电芯的邻边正极耳极片、邻中 正极耳极片的邻边正极极片耳、邻中正极极片耳导电器件; 由于分切开槽导电正极分切开槽消除了超声波焊接震动的传导,避免了邻中正极 极片耳超声波焊接震动影响邻边正极极片耳; 所述的分切开槽导电负极,是采用超声波焊接连接电芯的邻边负极耳极片、邻中 负极耳极片的邻边负极极片耳、邻中负极极片耳导电器件; 由于分切开槽导电负极分切开槽消除了超声波焊接震动的传导,避免了邻中负极 极片耳超声波焊接震动影响邻边负极极片耳; 所述的前置外壳,包括,前壳右位电极凹槽、前壳左位电极凹槽、前壳框沿平边、前 壳矩形凹坑、前壳胶衬、前壳金属外壳; 所述的后置外壳,包括,后壳右位电极凹槽、后壳左位电极凹槽、后壳框沿平边、熔 胶排气孔、后壳矩形凹坑,注液孔、注液孔内翻边、后壳胶衬、后壳金属外壳; 将前置外壳与后置外壳相向,前壳框沿平边与后壳框沿平边贴紧,即,构成前壳矩 形凹坑与后壳矩形凹坑组合矩形容器,组合矩形容器内安装电芯。 所述的前壳金属外壳、后壳金属外壳,前壳框沿平边、前壳框沿平边,是构成前壳 矩形凹坑与后壳矩形凹坑组合容器的刚度、强度结构,采用铝材、不锈钢、碳钢,优选的,铝 材。 所述的前壳金属外壳、后壳金属外壳材料厚度,选取0.2mm、0.3mm、0.4mm、0.5mm, 优选的,0.4mm。 前置外壳与后置外壳相向,前壳框沿平边与后壳框沿平边贴紧,即,前壳右位电极 凹槽与后壳右位电极凹槽、前壳左位电极凹槽与后壳左位电极凹槽构成分切开槽导电负 极,分切开槽导电正极从前壳矩形凹坑与后壳矩形凹坑组合矩形容器容器内引出的通槽 孔。后置外壳的胶衬、前置外壳的胶衬将引出的分切开槽导电负极,分切开槽导电正极于引 出的通槽孔粘接密封。 所述的泄压阀,包括,预制通槽隙、径向凹槽; 泄压阀的径向凹槽与注液孔内翻边相切,泄压阀的材料弹性使得径向凹槽与注液 孔内翻边胀紧密封。 泄压阀的预制通槽隙,在前壳矩形凹坑与后壳矩形凹坑组合的矩形容器内压力增 高时,泄压阀的材料弹性受到气压压强压缩作用引起泄漏,泄漏起到减压作用。 泄压阀,采用合成橡胶材料制造; 所述的合成橡胶采用三元乙丙橡胶、聚氨酯橡胶、氟素橡胶、四丙氟橡胶、优选的, 三元乙丙橡胶。 所述的邻中正极保护片,采用铝片制造,置于邻中正极极片耳的焊接位对称背面, 铺垫于超声波焊头座上面,避免超声波焊头座上面尖齿损坏邻中正极极片耳。 所述的邻边正极保护片,采用铝片制造,置于邻边正极极片耳的焊接位对称背面, 铺垫于超声波焊头座上面,避免超声波焊头座上面尖齿损坏邻边正极极片耳。 所述的邻中负极保护片,采用铝片制造,置于邻中负极极片耳的焊接位对称背面, 铺垫于超声波焊头座上面,避免超声波焊头座上面尖齿损坏邻中负极极片耳。 所述的邻边负极保护片,采用铝片制造,置于邻边负极极片耳的焊接位对称背面, 7 CN 111613837 A 说 明 书 6/11 页 铺垫于超声波焊头座上面,避免超声波焊头座上面尖齿损坏邻中负极极片耳。 本发明一种交错极耳结构锂电池的有益效果 通过改进极片极耳,以交错极耳结构,与现有电芯极片极片耳相比,相同的层数极 片的电芯,仅需焊接1/2的极片极耳层数,突破了超声波焊接极耳工艺限制,使得单体电池 容量大幅度增大。 通过改进矩形刚性壳结构,以后壳框沿平边相向前壳框沿平边,通过EVA胶衬粘接 组成密封结构,密封结构的抗剥离强度大大超过现有铝塑复合膜粘接强度,与现有矩形软 包锂电池相比起到延长锂电池寿命效果,与现有的矩形刚性壳电池相比,改善了顶角焊缝 结构易泄漏问题; 改进的,前置外壳的前壳矩形凹坑,相向后置外壳后壳矩形凹坑,组成电芯安装容 器;后置外壳包括金属外壳、前置外壳包括金属外壳,其刚性强度大幅增加,有利电芯安装 容器对电芯固定稳定性,使得电池在震动、冲击状态下能避免电芯松垮,能避免正、负极极 片移位,起到提高安全性效果; 改进的,后壳右位电极凹槽、后壳左位电极凹槽,相向前壳右位电极凹槽、前壳左 位电极凹槽,组成分切开槽导电正极、分切开槽导电负极引出的槽孔,该槽孔具有刚性强 度,能更好的固定电芯导电连接分切开槽导电正极、分切开槽导电负极,从而提高电池的可 靠性。 改进的,分切开槽导电正极、分切开槽导电负极,分切开槽,避免了极片耳超声波 焊接震动传动影响相邻的极片耳,提高了超声波焊接接头的质量; 改进的,泄压阀利用了注液孔安装,精简了结构,利用了注液孔内翻边结构与泄压 阀的径向凹槽相切胀紧密封,其圆周径向受力均匀,密封可靠。泄压阀的预制通槽隙,在电 池内压增高时,预制通槽隙受到气压压强作用,泄压阀的弹性被压缩自动泄漏,起到泄压安 全防护作用。 附图说明 图1是一种交错极耳结构锂电池的示图; 图中,1k前置外壳、2a分切开槽导电正极、2b分切开槽导电负极; 图2是图1的俯视图; 图中,1k前置外壳、1j后置外壳、2a分切开槽导电正极、2b分切开槽导电负极、3泄 压阀; 图3是图1的右视图; 图中,1j后置外壳、2a分切开槽导电正极、3泄压阀; 图4是图1的A-A剖视图; 图中,1j后置外壳、2a分切开槽导电正极、3泄压阀、2v电芯; 图5是本发明一种交错极耳结构锂电池的电芯结构示图; 图中,2a分切开槽导电正极、2b分切开槽导电负极、3-1a导电正极的分切开槽,3- 1b导电负极的分切开槽、2v电芯、邻边2caw正极极片耳、邻边2cbw负极极片耳,2D超声波焊 接区位; 图6是图5的俯视图; 8 CN 111613837 A 说 明 书 7/11 页 图中,2a分切开槽导电正极、2b分切开槽导电负极、2can邻中正极片耳、2caw邻边 正极片耳、2cbn邻中负极片耳、2cbw邻边负极片耳、2Faw邻边正极保护片、2Fan邻中正极保 护片、2Fbw邻边负极保护片、2Fbn邻中负极保护片、2G隔膜; 图7是图5的左视图; 图中,2b分切开槽导电负极、2Fbw邻边负极保护片、2cbw邻中正极片耳、2v电芯; 图8是图7的左视图; 图中,2a分切开槽导电正极、2b分切开槽导电负极、3-1a导电正极的分切开槽、3- 1b导电负极的分切开槽、2can邻中正极片耳、2caw邻边正极片耳、2cbn邻中负极片耳、2cbw 邻边负极片耳、2Faw邻边正极保护片、2Fan邻中正极保护片、2Fbw邻边负极保护片、2Fbn邻 中负极保护片、2v电芯; 图9是图5的B-B剖视图; 图中,2Fbw邻边负极保护片、2b分切开槽导电负极、2cbw邻边负极片耳、2v电芯; 图10是图5的C-C剖视图; 图中,2Fbn邻中保护片、2b分切开槽导电负极、2cbn邻中负极片耳、2v电芯; 图11是图5的D-D剖视图; 图中,2a分切开槽导电正极、2Fan邻中正极保护片、2can邻中正极片耳、2v电芯; 图12是图5的E-E剖视图; 图中,2a分切开槽导电正极、2caw邻边正极片耳、2Faw邻边正极保护片、2v电芯; 图13是叠片电芯示意图; 图中,2cbn邻中负极片耳、2cbw邻边负极片耳、2can邻中正极片耳、2caw邻边正极 片耳、2G隔膜; 图14是本发明一种交错极耳结构锂电池的2a分切开槽导电正极、2b分切开槽导电 负极的结构示图; 图中,导电正极的分切开槽3-1a、导电负极的分切开槽3-1b,导电正极的分切开槽 3-1a、导电负极的分切开槽3-1b共图; 图15是本发明一种交错极耳结构锂电池的邻边正极耳极片示图; 图中,2caw邻边正极片耳、2pp正极活性物质涂层; 图16是本发明一种交错极耳结构锂电池的邻中正极耳极片示图; 图中,2can邻中正极片耳、2pp正极活性物质涂层; 图17是本发明一种交错极耳结构锂电池的邻边负极耳极片示图; 图中,2cbw邻边负极片耳、2np负极活性物质涂层; 图18是本发明一种交错极耳结构锂电池的邻中负极耳极片示图; 图中,2cbn邻中负极片耳、2np负极活性物质涂层; 图19是本发明一种交错极耳结构锂电池的后置外壳结构示图; 图中,1-3后壳框沿平边、1-4熔胶排气孔、1-5后壳矩形凹坑; 图20是图19俯视图; 图中,1-1后壳右位电极凹槽、1-2后壳左位电极凹槽、1-3后壳框沿平边、1-5后壳 矩形凹坑、1-6注液孔; 图21是图19仰视图; 9 CN 111613837 A 说 明 书 8/11 页 图中,1-3后壳框沿平边、1-5后壳矩形凹坑; 图22是图19H-H剖视图; 图中,1-6注液孔、1-7注液孔内翻边、1-8后壳胶衬、1-9后壳金属外壳; 图23是是本发明一种交错极耳结构锂电池的前置外壳结构示图; 图中,1-3k前壳框沿平边、1-5k前壳矩形凹坑; 图24是图23的俯视图; 图中,1-1k前壳右位电极凹槽、1-2k前壳左位电极凹槽、1-3k前壳框沿平边、1-5k 前壳矩形凹坑; 图25是图23的I-I剖视图; 图中,1-3k前壳框沿平边、1-5k前壳矩形凹坑、1-8k前壳胶衬、1-9k前壳金属外壳; 图26是本发明一种交错极耳结构锂电池的泄压阀安装结构示图; 图中,1-6注液孔、1-8后壳胶衬、1-9金属外壳、3泄压阀; 图27是本发明一种交错极耳结构锂电池的泄压阀示图; 图中,3-2径向凹槽; 图28是图27俯视图; 图中,3-1预制通槽隙; 图29是图27的J-J剖视图; 图中,3-1预制通槽隙、3-2径向凹槽; 图30是邻边正极保护片示图,邻中正极保护片、邻边负极保护片、邻中负极保护片 共图;