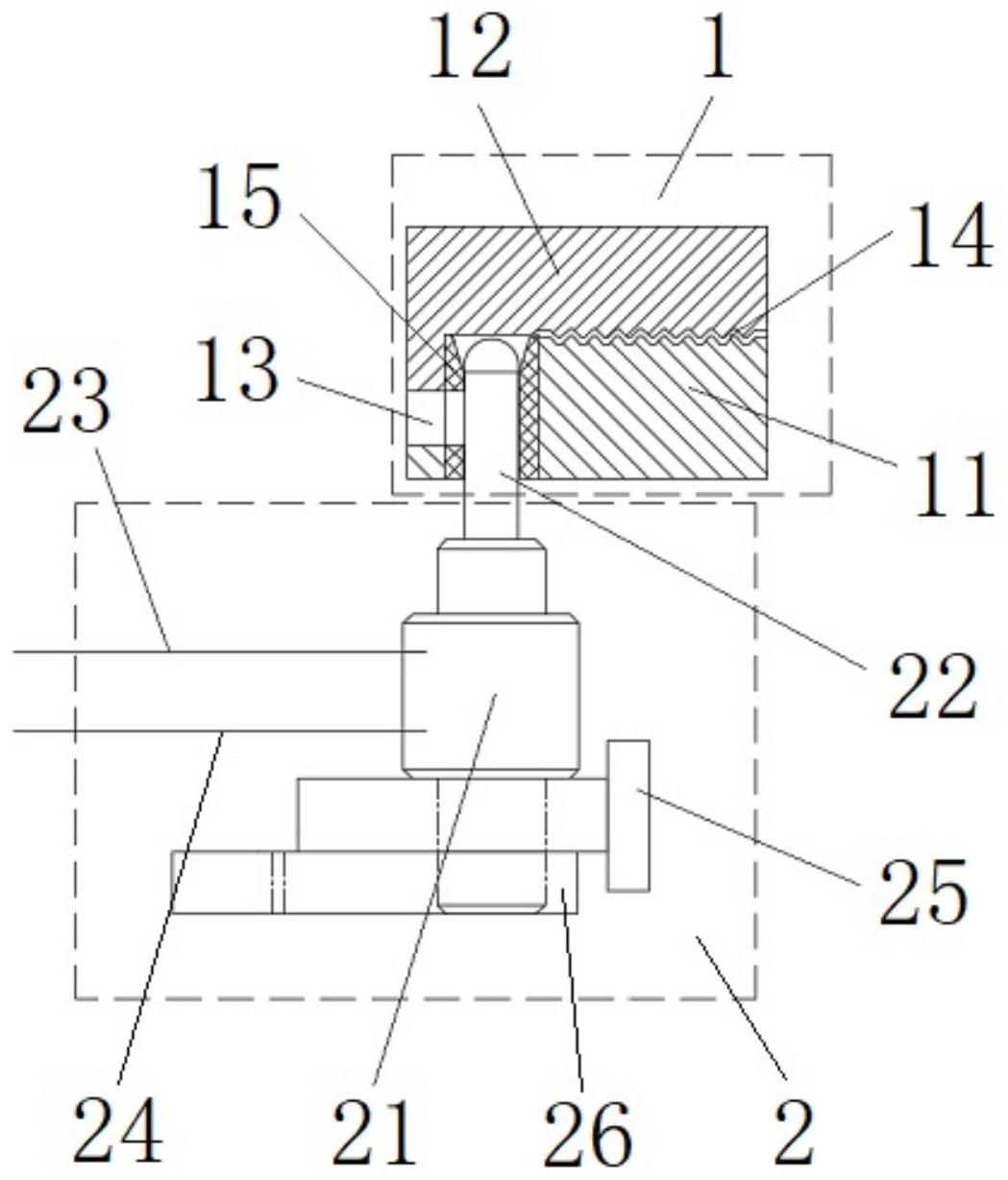
技术摘要:
本发明属于压铸技术领域,涉及一种高真空压铸模液压真空阀,包括模具和液压驱动器,所述模具包括动模板和定模板,动模板和定模板互相拼合后中间留有模腔和能连通模腔的真空吸气口,真空吸气口到模腔之间设有能被真空阀芯关断的真空阀座;所述液压驱动器包括连接打开油 全部
背景技术:
真空金属压铸成型技术现已普及应用到新能源汽车、5G通讯、传统汽车铸件的改 善、电子、家用、航空等领域,真空压铸技术是将金属液在冷却成型前把型腔内的空气抽出, 降低压射比压,降低气孔率,提高产品的致密度,增强机械性能。真空阀在真空压铸工艺中 是个非常重要的部件。 现有的真空阀的机构如图1所示:主要由一个模具动模阀体流道A1、闭锁阀芯A2、 受压阀芯A3组成。高压压铸过程中利用金属液推力原理,金属液高速通过动模阀体流道A1, 利用流道的弯曲阻力降低液体流动速度,金属液的运动能由于撞击弯道、金属流逐渐减弱, 金属液会被后面继续充填注入的金属液推挤向前流动,储备足够的力撞击和推动受压阀芯 A3,利用杠杆原理带动闭锁阀芯A2达到关闭。但是现有技术存在以下问题: ①现有真空阀受压阀芯和闭锁阀芯与阀套之间为间隙配合,例如CN108580833A提 到的控制装置。金属液在正常生产过程中温度达到650℃以上。间隙过大容易使金属液进 入,使阀芯不能正常关闭,导致堵塞或损坏;间隙过小,受温度的影响,受压阀芯和闭锁阀芯 与阀套之间的不能正常滑动,很容易造成堵塞或损坏。 ②在压铸过程中,需要利用真空阀在金属液未到达模具型腔前0.5~1s内将气体 抽出,真空阀的响应关闭时间需要得到精确控制。但真空阀的设计与模具之间的配合相当 复杂,当真空阀损坏或堵塞时,更换及清理时间也非常的长,从而造成生产成分的浪费。真 空阀的成本也非常昂贵,也增加了生产的使用成本。 ③现有真空阀的真空抽气面积设计也非常的局限,压铸过程中时间非常的短,当 截面积设计局限时严重影响了抽真空效果,气流在负压状态下,通过受限的截面积,流导非 常小,压力损坏非常大,无法到达生产过程中理想的真空压力。 所以需要改进控制方式,以避免以上问题。
技术实现要素:
本发明的主要目的在于提供一种高真空压铸模液压真空阀,能够提高压铸的吸气 效率和可靠性。 本发明通过如下技术方案实现上述目的:一种高真空压铸模液压真空阀,包括模 具和液压驱动器,所述模具包括动模板和定模板,动模板和定模板互相拼合后中间留有模 腔和能连通模腔的真空吸气口,真空吸气口到模腔之间设有能被真空阀芯关断的真空阀 座;所述液压驱动器包括连接打开油路和关闭油路的液压油缸,所述真空阀芯在液压油缸 内伸缩运动,所述真空阀座具有上方连通模腔的通孔,所述真空阀芯的上部穿过通孔,所述 真空吸气口位于垂直于通孔的方向。 具体的,所述通孔的下部内径与真空阀芯的外径匹配,所述通孔的上部扩大。 3 CN 111590045 A 说 明 书 2/2 页 具体的,所述真空阀芯的顶端缩小。 具体的,所述液压油缸固定于以固定板上,所述固定板上还设有能对真空阀芯开 启位置限位的限位开关。 采用上述技术方案,本发明技术方案的有益效果是: 本机构不仅采用灵敏的真空阀控制压铸模的吸气通断,而且通气面积大,吸气效 率高,同心度不受影响,安装容易,密封性可靠。 附图说明 图1为现有技术压铸模的结构图; 图2为实施例高真空压铸模液压真空阀的结构示意图。 图中数字表示: A1-动模阀体流道,A2-闭锁阀芯,A3-受压阀芯; 1-模具,11-动模板,12-定模板,13-模腔,14-真空吸气口,15-真空阀座; 2-液压驱动器,21-真空阀芯,22-液压油缸,23-打开油路,231-第一电磁阀,24-关 闭油路,241-第二电磁阀,25-固定板,26-限位开关。