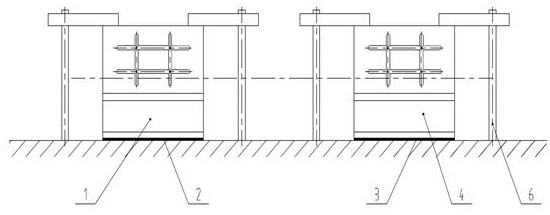
技术摘要:
本发明公开了一种冷轧机辊系轴承座加工及检验方法,步骤一,将铜滑板留加工余量,装配在轴承座上;步骤二,装配铜滑板传动侧轴承座和操作侧轴承座按照辊系安装状态摆放,以传动侧轴承座及操作侧轴承座轴承安装孔母线找正;步骤三,按照图纸设计及最终检验要求对传动侧 全部
背景技术:
金属的轧制工具很多,而对于钢带的轧制离不开冷轧板带轧机,冷轧板带轧机因 为其具有极强的辊型控制功能,能轧制更薄的钢带,并且可以轧制更高强度及较高硬度的 材料,以及具有较高轧制速度的特点,目前已成为冷轧带钢领域中最热门的冷轧机形式,无 论是在无头全连轧生产线中还是在单机架往复式冷轧机组都占有主导地位。冷轧板带轧机 包括:轧线标高调整装置、机架装配、压上装置、辊系装配、轧机平台与排烟罩、传动部分、万 向接轴托架及轧机配管等设备。辊系是冷轧板带轧机中的关键部件,是冷轧机的核心,冷轧 带钢产品最终是要靠轧辊轧制成成品,因此辊系的精度直接影响着最终产品的质量。冷轧 板带轧机因为需要轧制更薄的带钢产品,因此,冷轧机辊系的轧辊要求精度非常高,所要轧 辊必须紧密贴合,那么安装轧辊的轴承座及铜滑板与机架贴合的精度相应要求就非常高, 从而进一步要求,辊系轴承座铜滑板相对于轧辊的对称度,以及传动侧、操作侧铜滑板相对 轧辊的公差一般不超过0.05mm。 常用的辊系轴承座对称度及尺寸公差检验方法,是在轴承座、铜滑板加工完成以 后,与轴承、轧辊等件装配成成品,在机床上进行机检(依靠机床打表的方法进行检验)。但 是这种方法往往存在一些问题,如:1、调整找正过程困难,即使将轧辊沿母线找正完成,但 轴承座由于已经安装了轴承,轴承存在游隙,因此,往往两个轴承座的四个铜滑板外表面都 不正,这样很难判断是产品质量问题,还是调整找正问题;2、由于轴承游隙的存在,即使强 行将轴承座铜滑板调整到检验要求的精度,但可能存在轴承游隙不均问题,在生产使用过 程中就有可能存在烧毁轴承,或者缩短轴承使用寿命的隐患。 因此,为了解决上述技术问题,本发明提供了一种不同于现有技术的冷轧机辊系 轴承座加工及检验方法。
技术实现要素:
本发明提供了一种冷轧机辊系轴承座加工及检验方法,本发明打破传统的先加 工,再装配,最后检验的常规思路,采用先简单装配,再精加工,并直接进行对称度及尺寸公 差检验,避免最后整个辊系再上机床进行机检的麻烦,解决了装配时调整难度大、多次返修 的问题,节约大量人力物力,并有效改善了产品精度,提高了产品质量。 本发明的技术方案是:首先,一种冷轧机辊系轴承座加工方法,先对辊系轴承座及 铜滑板装配,再对装配后的轴承座及铜滑板加工,主要包括以下步骤: 步骤一:将铜滑板在厚度方向上留有加工余量,将留有加工余量的铜滑板装配在轴承 座中心孔的两侧,所述轴承座包括传动侧轴承座和操作侧轴承座; 步骤二:在安装有铜滑板的轴承座底部放置垫片组; 3 CN 111604647 A 说 明 书 2/6 页 步骤三:对轴承座中心孔找正并共线,用工装对轴承孔完成装卡; 步骤四:装卡完成后,确保轴承座母线轴线共线,再对轴承座留有加工余量的的铜滑板 进行加工。 通过上述方案,铜滑板安装在辊系轴承座的两侧,具有保护安装面和导向的作用; 先留有加工余量,避免铜滑板先加工完成后再安装,可能存在尺寸误差不能达到有效的与 轧辊紧密贴合,安装轧辊的轴承座及铜滑板与机架贴合的精度会受到影响;另外,对于轴承 座的位置先进行调整,使得轴承孔共线,保证轴承在辊系水平方向上及轴承座的高低均保 持一致,再对轴承座装卡,装卡的目的是为了固定轴承座,避免在工作过程中轴承座的位置 变化,方便下一步对于最初留有的加工余量加工,确保加工精度,加工完成后松开装卡的工 装。 作为方案的进一步优化,步骤一中所述轴承座包括传动侧轴承座和操作侧轴承 座,将安装有铜滑板的传动侧轴承座和操作侧轴承座按照辊系安装状态放置在机床平台 上。 作为方案的进一步优化,步骤二中所述可调垫片组调整轴承座的高低方向,通过 加减轴承座下面的垫片组进行调整;左右方向沿着轴承座中心孔轴线方向移动调整。这是 为了保证两个轴承座先在水平和竖直方向上位置保持一致,传动侧轴承座和操作侧轴承座 前方可以放置水平挡板,调节两个轴承座在同一水平线上,即前后的调节。 作为方案的进一步优化,在轴承座非轴承孔的侧面方向上,步骤四中所述的装卡 工装包括设在轴承座侧面方向两端的横向压板,还包括与横向压板垂直的竖向压板,所述 横向压板和竖向压板通过螺栓连接。该装卡工装固定轴承座,防止轴承座的位置发生变化, 用横向支撑板和竖向支撑板,固定和支撑效果好。 作为方案的进一步优化,在轴承座侧面非轴承孔的方向上,所述横向压板压在轴 承座上方的两端,所述竖向压板用于支撑横向压板,所述一端的横向压板与竖向压板在轴 承座非轴承孔面的前后方向各设置一组,每个所述横向压板与轴承座的接触面积为整体横 向压板面积的1/4。该工装装卡的位置不影响轴承孔找正及铜滑板面修配加工走刀,还能保 证固定轴承座的效果好。 对于最初留有的加工余量加工完成后,再检验,一种冷轧机辊系轴承座检验方法, 步骤如下: 步骤一:装卡完成后,先检验轴承座母线共线; 步骤二:对轴承座铜滑板留有的精加工余量进行加工时,检验加工精度; 步骤三:加工完成后,松开装卡的工装,对轴承座铜滑板相对轴承孔轴线对称度及尺寸 公差进行检验; 步骤四:最后确认都满足设计及最终检验要求后,再将传动侧轴承座和操作侧轴承座 上的铜滑板拆下,进行厚度检验,并作后记录; 步骤五:按原有的对应位置重新装回铜滑板,便于备件更换留余量或选配方便。 作为方案的进一步优化,所述检验方法中步骤二对铜滑板的精加工余量进行加工 时,要确保加工精度,确保加工精度的方式是:其中A1、A2、B1、B2四个尺寸公差在0.05mm以 内。 作为方案的进一步优化,所述检验方法中步骤三所述轴承孔轴线对称度及尺寸公 4 CN 111604647 A 说 明 书 3/6 页 差的检验方法是:先对传动侧轴承座和操作侧轴承座的轴承孔共线要求进行检验确认,再 对已经加工完成的铜滑板面的平面度及平行度,以及尺寸A1、A2、B1、B2进行检验。 本发明和现有技术相比,具有以下有益效果: 1、本发明打破传统的先加工,再装配,最后检验的常规思路,采用先简单装配,再精加 工,并直接进行对称度及尺寸公差检验,避免最后整个辊系再上机床进行机检的麻烦,解决 了装配时调整难度大、多次返修的问题,节约大量人力物力,并有效改善了产品精度,提高 了产品质量。 2、本发明与以往的加工、装配、检验顺序相比,可减少一次最终整体进行检验的过 程,既能节约机检的时间及上机床成本,又排除了轴承游隙带来的误差,有效提高产品精 度,为用户提高产品质量打下基础。 附图说明 图1中图1(a)、图1(b)、图1(c)分别是本发明轴承座装配铜滑板的三视图; 图2是本发明辊系轴承座加工工艺及检验方法放置状态示意图; 图3是本发明轴承座装卡工装位置示意图; 图4是本发明轴承座压板位置俯视图; 图5是本发明辊系轴承座加工及检验内容图示; 图中:1-传动侧轴承座,2-传动侧调整垫片组,3-操作侧调整垫片组,4-操作侧轴承座, 5-铜滑板,6-工装。