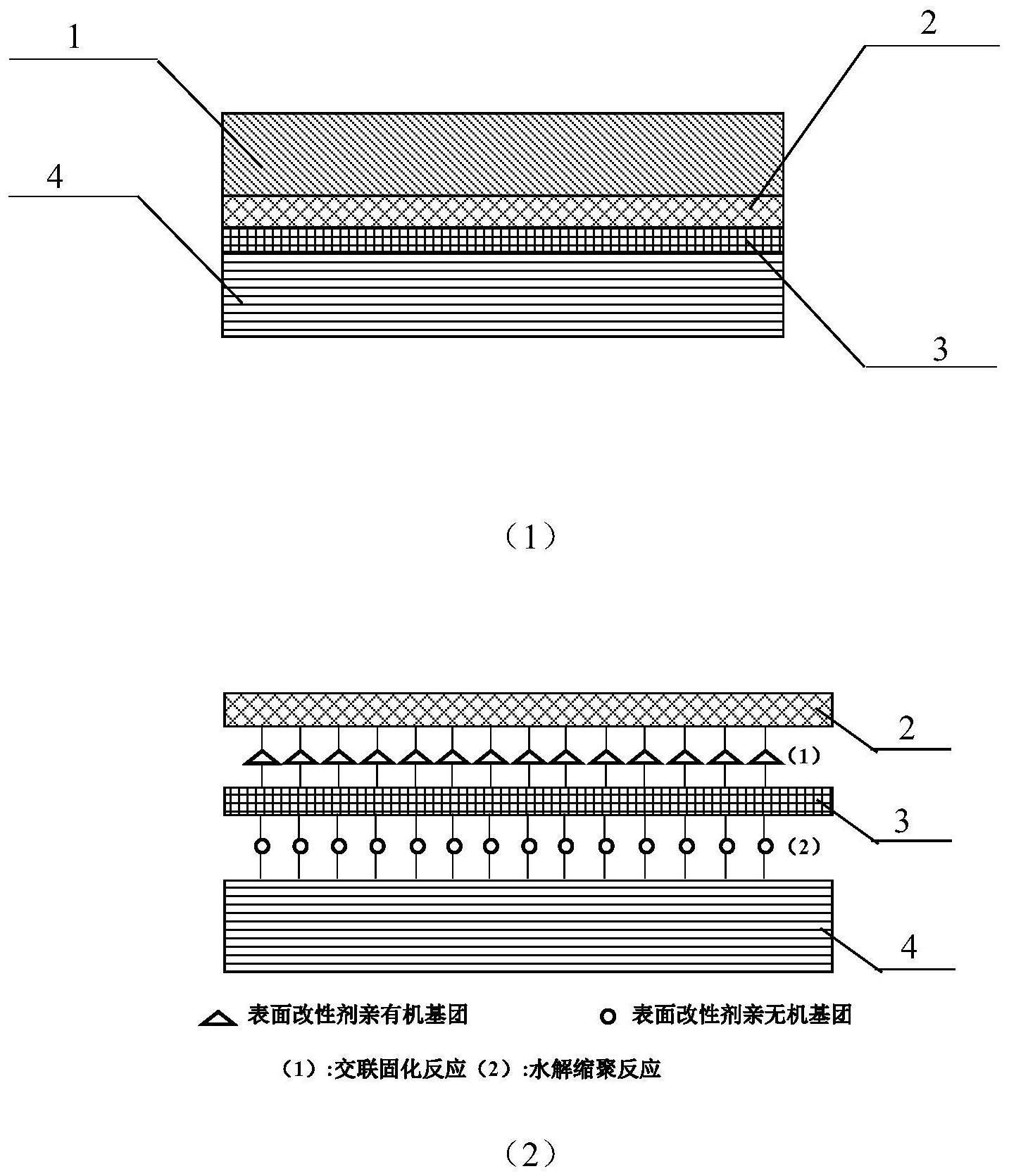
技术摘要:
本发明涉及一种氮化铝陶瓷基板表面处理方法,包括如下工序:1)前处理:去除基板表面的油污和杂质后,将其浸没于有机溶剂液中,处理后取出烘干;2)界面偶联剂处理:将经步骤1)处理后的氮化铝陶瓷基板浸没于界面偶联剂和无水乙醇的混合溶液中常温处理5~10min,而后取出 全部
背景技术:
氮化铝陶瓷基板(ALN)因其介电常数低、导热性能优良、与芯片匹配的热膨胀系数 低等优点,被广泛应用于半导体器件功率模块的衬板。当采用活性金属钎焊技术(AMB)实现 氮化铝陶瓷基板金属化时,需要在氮化铝陶瓷片表面印刷活性金属焊料。 活性金属焊料在氮化铝陶瓷片表面的附着性是决定覆铜陶瓷基板焊料结合层质 量的重要因素之一。AMB工艺中,活性金属焊料中会加入成膜剂等有机物,而ALN陶瓷的表面 性质与有机基体相差很大,无法直接结合。为了实现二者结合,目前使用NaOH溶液、混合酸 溶液、甚至等离子体轰击的技术粗化陶瓷表面,增强金属焊料与瓷片机械嵌合力,从而间接 解决陶瓷与有机基体相容性差的问题。 按照化学键合理论,若在氮化铝瓷片表面涂覆表面改性剂或许可直接增强瓷片和 有机基体的相容性。相比来说,陶瓷片表面采用表面改性的处理方法时,效率更高,成本更 低,因此,在AMB技术领域,亟待开发一种针对氮化铝陶瓷基板表面处理方法。
技术实现要素:
为解决现有技术的不足,本发明提供了一种氮化铝陶瓷基板表面处理方法,包括 杂质去除、界面偶联剂处理两道处理工序,通过该处理方法,增强氮化铝陶瓷基板和有机基 体间的直接相容性。 为了实现上述目的,本发明通过以下技术方案实施: 本发明提供的氮化铝陶瓷基板表面处理方法,包括如下工序: 1)前处理 去除基板表面的油污和杂质后,将其浸没于有机溶剂液中,处理后取出烘干; 2)界面偶联剂处理 将经步骤1)处理后的氮化铝陶瓷基板浸没于界面偶联剂和无水乙醇的混合溶液 中常温处理5~10min,而后取出烘干,界面偶联剂和无水乙醇的体积比为1:100~200。 优选的,本发明的处理方法还能够和陶瓷基板的表面粗化处理工序连用,在步骤 1)前,先进行粗化处理,使陶瓷基板表面粗糙度达到0.3-0.4。 氮化铝陶瓷基板表面粗化处理方式包括:碱性溶液处理或混合酸溶液处理氮化铝 陶瓷片表面。碱性溶液为质量分数15%~25%的NaOH或KOH强碱溶液,混合酸溶液包括质量 分数为25%~65%硫酸、5%~8%的氢氟酸,余量为水。 优选的,步骤1)中,采用除油剂和纯水去除氮化铝陶瓷基板表面的油污和杂质。除 油剂包括40~70g/L氢氧化钠、20~50g/L碳酸钠、10~20g/L磷酸三钠,其余为水;除油温度 设置为80~90℃,处理时间为3~5min,除油后纯水浸洗时间为1~2min,温度为15~25℃。 3 CN 111548196 A 说 明 书 2/4 页 优选的,步骤1)中,有机溶剂为异丙醇和丙酮的混合液,体积比为3:1,具体的处理 条件为将氮化铝陶瓷基板浸没于异丙醇和丙酮的混合液中,常温超声3~5min;烘干时,烘 箱温度设置为100℃,烘干时间为5~10min。。 优选的,步骤2)中,界面偶联剂包括有机硅、钛酸酯、铝酸酯中的一种或几种。其 中,有机硅和无水乙醇的体积比为1:100,钛酸酯和无水乙醇的体积比为1:200,铝酸酯和无 水乙醇的体积比为1:100。 烘干条件为:烘箱温度设置为100℃,烘干时间为5~10min,优选10min。 优选的,本发明中的氮化铝陶瓷基板为活性钎焊陶瓷基板。 本发明的有益效果如下: 在本发明提供的氮化铝陶瓷基板表面处理方法中,氮化铝陶瓷基板经界面偶连剂 和无水乙醇的混合溶液处理后,实现氮化铝陶瓷基板表面化学改性。界面偶联剂同时具有 亲有机基团和亲无机基团,亲有机基团通过交联固化反应与金属焊料层结合,亲无机基团 通过水解缩聚反应与陶瓷基板表面结合,进而实现金属焊料层和陶瓷基板表面之间的结 合;无水乙醇作为界面偶联剂的稀释剂,易于挥发,且和界面偶联剂不会发生明显反应,有 助于界面偶联剂发挥功效。 因此,本发明中的方法针对陶瓷表面进行化学改性,可改善焊料的附着性,显著提 高焊料层与陶瓷表面的化学结合力从而减少焊料结合层的空洞和空隙,提高覆铜板的抗热 冲击性能且处理效率高、成本低。且该方法可在对陶瓷表面进行粗化的基础上使用,进一步 提高活性金属焊料附着性。 附图说明 图1为本发明中的氮化铝陶瓷基板表面处理流程图; 图2为本发明界面偶联剂的作用机理简化示意图,其中(1)显示了界面偶联剂实现 活性金属焊料层和AlN陶瓷基板间的结合,1为铜箔,2为活性金属焊料层,3为界面偶联剂 层,4为AlN陶瓷基板;(2)为界面偶联剂实现金属焊料层和AlN陶瓷基板间的结合的作用机 理示意图。 图3为本发明氮化铝陶瓷基板产品制造流程图。