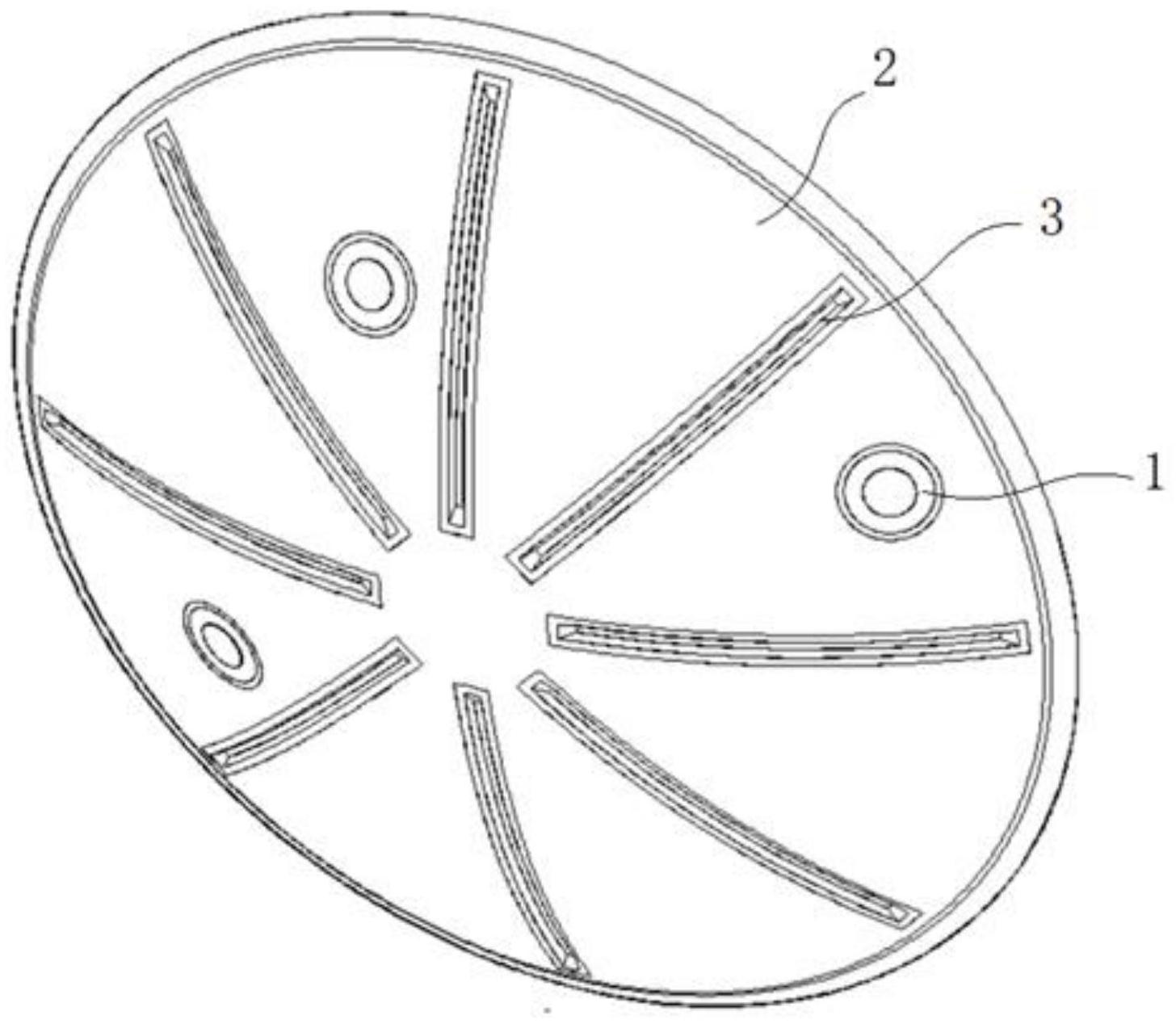
技术摘要:
本发明公开了一种飞机大曲率球面框的共胶接固化成型方法,包括一下步骤:步骤一:泡沫夹芯的机加成型;步骤二:长桁预浸料的铺贴固化;步骤三:球皮的自动铺放成型;步骤四:帽型泡沫夹芯长桁预成型体和预浸料片球皮的组合与定位;步骤五:共胶接固化成型。其提高铺贴 全部
背景技术:
球面框是飞机中后机身的后端框,主要承受气密压力作用。传统的球面框大多采 用金属结构,零件重量大,逐渐被比强度、比刚度高的复合材料取代。目前复合材料球面框 多使用树脂膜熔浸成型(RFI)工艺或利用真空辅助液体成型(VARTM)工艺成型,例如A380、 B787的球面框,虽然这些工艺形式简单易操作,但是树脂液体在注胶的过程中,由于纤维的 表面状态不尽相同,造成树脂浸润性差异很大,最终造成零件固化后孔隙率较大,纤维体积 含量低,抗疲劳、耐腐蚀性能较差。 树脂基碳纤维复合材料具有比强度、比刚度高,可设计性强,抗疲劳断裂性能好, 耐腐蚀,尺寸稳定性好等优越的性能,是目前航空、航天、交通等领域中应用十分广泛的高 性能结构材料。
技术实现要素:
为了克服现有技术中的缺陷,本发明实施例提供了一种飞机大曲率球面框的共胶 接固化成型方法,其提高铺贴效率,缩短制造周期。 为实现上述目的,本申请实施例公开了一种飞机大曲率球面框的共胶接固化成型 方法,包括: 步骤一:将泡沫坯料使用夹具固定,启动五轴机床,按照零件数模对所述泡沫坯料 的外形面进行机械加工成型,所述泡沫坯料机加后为横截面呈梯形的长条状泡沫夹芯; 步骤二:在所述泡沫夹芯表面铺贴预浸料片,得到帽型泡沫夹芯长桁预成型体,将 所述帽型泡沫夹芯长桁预成型体放入热压罐固化成型; 步骤三:以球面框的外形面为基准制造球面框成型工装,所述球面框成型工装上 设有定位孔,通过所述定位孔将所述球面框成型工装精确定位在自动铺丝机的坐标系中, 根据自动铺丝机规划程序自动在所述球面框成型工装上铺放预浸丝束成型球皮; 步骤四:使用激光投影仪在所述球皮的表面上投影出所述帽型泡沫夹芯长桁预成 型体的理论位置,根据所述激光投影仪的激光边界线对所述帽型泡沫夹芯长桁预成型体进 行定位,将所述帽型泡沫夹芯长桁预成型体根据定位铺贴在所述球皮上,进一步的,使用真 空袋包覆所述帽型泡沫夹芯长桁预成型体以及球皮,抽吸空气形成真空负压,使得所述帽 型泡沫夹芯长桁预成型体紧密贴附在所述球皮上; 步骤五:使用隔离膜、透气毡以及真空袋对定位好所述帽型泡沫夹芯长桁预成型 体的球面框进行封装,测漏合格后,送入热压罐共胶接固化成型得到球面框。 优选的,所述泡沫坯料为PMI泡沫或PVC泡沫。 优选的,所述帽型泡沫夹芯长桁预成型体的型面由泡沫坯料机加型面保证。 3 CN 111605225 A 说 明 书 2/3 页 优选的,所述预浸料片采用手工铺贴在所述泡沫夹芯的表面,所述预浸料片是使 用裁布机根据Fibersim软件仿真计算后的外形尺寸精确裁剪成型。 优选的,所述球面框成型工装为殷钢制阴模工装。 优选的,所述帽型泡沫夹芯长桁预成型体和所述球皮之间使用结构胶膜进行粘 结。 优选的,所述共固化成型的条件为:最高固化温度174-186℃,升温速率1-3℃/ min,降温速率1-2.5℃/min,最高固化温度保温时间至少2h,固化压力0.6-0.7Mpa。 本发明的有益效果如下: 1、与传统手工铺放成型工艺相比,采用自动铺丝机铺放成型大尺寸的球皮能在保 证零件的成型质量的前提下有效提高铺贴效率; 2、球皮的自动铺丝预成型、泡沫夹芯的机加成型、长桁的铺贴固化成型等工作可 同时进行,大大缩短了零件的制造周期。 为让本发明的上述和其他目的、特征和优点能更明显易懂,下文特举较佳实施例, 并配合所附图式,作详细说明如下。 附图说明 为了更清楚地说明本发明实施例或现有技术中的技术方案,下面将对实施例或现 有技术描述中所需要使用的附图作简单地介绍,显而易见地,下面描述中的附图仅仅是本 发明的一些实施例,对于本领域普通技术人员来讲,在不付出创造性劳动的前提下,还可以 根据这些附图获得其他的附图。 图1是本发明实施例中一种飞机大曲率球面框的结构示意图; 图2是本发明实施例中帽型长桁成型工装的结构示意图; 以上附图的附图标记: 1、机加制孔; 2、球皮; 3、帽型泡沫夹芯长桁预成型体; 4、球面框成型工装; 5、帽型长桁成型工装;51、预浸料片;52、泡沫夹芯。