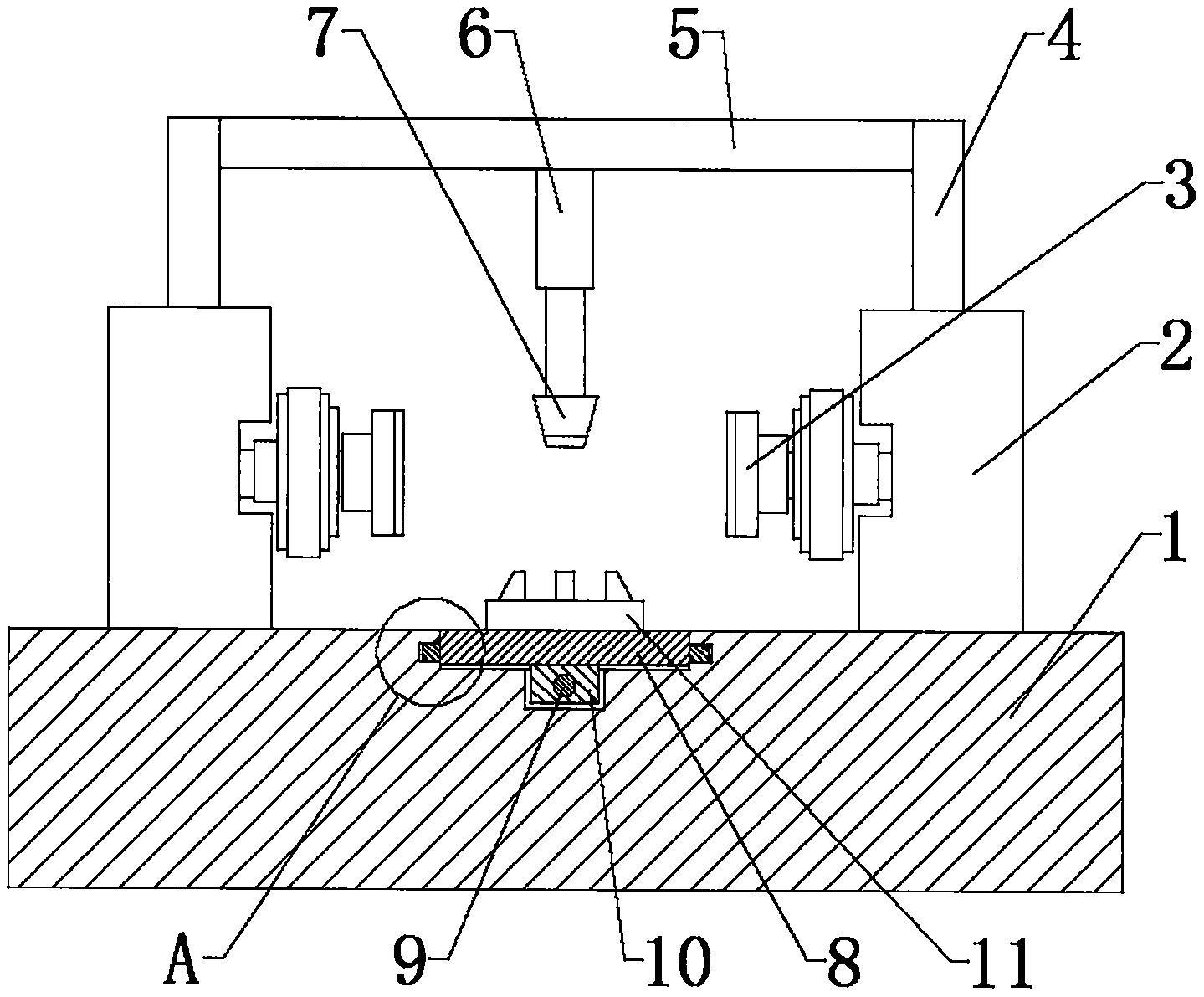
技术摘要:
本发明涉及铣床技术领域,尤其涉及一种双头铣床,其中铣床用铣刀表面具有两种不同的激光表面织构组织,该铣刀在切削加工时不易产生微熔的切屑,可以保证加工件表面的光滑度。
背景技术:
铣床通常指使用铣刀对工件表面进行加工的机床,铣刀通常以旋转运动为主运 动,它可以加工平面、沟槽,也可以加工各种曲面、齿轮等。 常用的铣刀在切削硬质合金时,尤其是干切的条件下,切削的热量集中在切削刃 的小范围内,这样持续的加工不利于散热,会使产生的切屑微熔而粘附在加工工件的表面 或者加工用铣刀上,从而导致加工表面的粗糙度增加,产品质量不合格。
技术实现要素:
表面织构技术是改善铣刀切削加工工况的有效技术。 本发明提供一种双头铣床,其特征在于所述铣床用铣刀表面具有激光表面织构组 织。 所述激光表面织构的形貌至少包括圆弧形凹坑和矩形凹坑。 所述圆弧形凹坑的孔径的大小在微米级别,孔径深度在3-10微米,孔径直径在3- 10微米,相邻两孔径圆心距离在200-300微米之间。 所述矩形凹坑的孔径大小在微米级别,孔径深度在5-10微米,孔径边长在5-10微 米,相邻两孔径中心距离在100-200微米。 优选在铣刀表面同时具有圆弧形凹坑和矩形凹坑的织构形貌。 优选圆弧形凹坑的孔径的大小一般在微米级别,孔径深度在3-5微米,孔径直径在 3-5微米,相邻两孔径圆心距离在50-300微米之间。 优选圆弧形凹坑孔径的大小与孔径深度的比例为1∶1。 优选矩形凹坑的孔径大小在微米级别,孔径深度在7-10微米,孔径边长在7-10微 米,相邻两孔径中心距离在50-300微米。 优选矩形凹坑的孔径大小与孔径深度为1∶1。 优选圆弧形凹坑在第一方向上平行分布,且相邻两个圆弧形凹坑之间间距相同。 优选矩形凹坑在第二方向上平行分布,且相邻两个矩形凹坑之间间距相同。 优选第一方向和第二方向的交叉角度在30-60°之间,最优选45°。第一方向和第二 方向之间设置夹角在对表面进行加工时避免加工的盲区,使加工表面更光滑。 优选每单位面积内圆弧形凹坑和矩形凹坑的数量比例大于1,最优选每单位面积 内圆弧形凹坑和矩形凹坑的数量比例介于2-4之间。不同尺寸和形貌的凹坑可以弥补单种 织构组织的缺点,而两种凹坑组织的合理数量分布也是利于加工表面的光滑性。 对于凹坑的加工方法,激光加工是表面织构加工中最广泛的应用手段,织构组织 加工的深度和深径比取决于激光加工的时间、波长、功率等因素。激光加工方法包括而不限 于飞秒激光、皮秒激光、二极管Nd:YAG激光或光纤激光。 3 CN 111590125 A 说 明 书 2/4 页 激光在不同功率进行加工产生不同直径和深度的圆弧形凹坑和矩形凹坑,激光功 率的增加,凹坑增大。激光加工的功率不应超过10W,不得低于3W。 在激光加工功率低于3W时由于能量密度过小,导致产生的凹坑过小而失去加工的 意义。在激光加工功率高于10W时由于能量密度过大,导致凹坑尺寸过大而损坏刀头,最终 影响铣刀产品质量。也就是使用较高的激光功率制造大孔径的凹坑,使用较小的激光功率 制造小孔径的凹坑。 使用激光发生器照射材料表面,高能量光子束轰击材料表面产生大量的热能,材 料吸收热能变成熔融态,随着激光照射的持续,熔融材料气体,而由于高能量激光束照射产 生的压力,可以使熔融材料溅射出来,从而形成微孔形貌。 但我们应该知晓,由于激光能量高斯分布局限性,激光在基材上的加工深度不会 无限度增加,在激光加工功率不变的情况下,通过控制脉冲的次数来制备不同深度的凹坑。 在加工前,先通过计算机对需要加工区域进行设计,如果圆弧形凹坑与矩形凹坑 区域重合或部分重合,均采用矩形凹坑的设计方案。 加工后的铣刀需要进行清洗,使用丙酮为清洗介质,超声清洗15-20分钟。 由于激光织构形貌对材料表面的动压润滑性有影响,在雷诺参数较高时,圆弧形 织构表面的表面动压润滑性较好,而矩形凹坑的承载能力较好,两者的的结合可以有效结 合各自的优势,从而产生极佳的效果。 对于铣刀表面的织构组织分布的密度通过以下方式计算得出。 在切削过程中,切削刀主要来源于刀头与切屑,或者刀头与工件之间的摩擦力。 对于铣刀表面织构组织的密度的计算方法如下: 刀头与切屑之间的摩擦用下式表示: 其中 表示刀头与切屑的实际接 触面积,τs表示摩擦剪切强度,Ff表示摩擦力。而当刀具的前刀面接触区域置入表面织构后, 刀头与切屑的实际接触面积为: 其中S表示每个表面织构的面积,n为刀头与 切屑挣脱的表面织构的数量,Aa为刀头与切屑的理论接触面积。因此可以计算得出,表面织 构刀具的摩擦力为:Ff=τs(Aa-nS)。 从上式可知,表面织构组织可以减少刀头与切屑的实际接触面积,从而减少两者 之间的摩擦力,减少切削力的产生,而切削刀的增大可以加剧刀具的磨损。磨损后的刀具会 使切削环境发生变化,使粘结加重,导致工件表面粗糙度增大,因此,表面织构刀具可以有 效改善工件的表面粗糙度。 另外,需要考虑的因素还包括,织构结构中对工件表面粗糙度影响大小的顺序:孔 径直径>孔径间距>孔径深度,在对直径、间距和深度三者进行调节时,应按照三者的影响 大小依次进行考虑。 有益效果: 1、切削实验表明,在干切条件下,切削热可以在切削刃的极小范围内有效扩散,减 少铣刀刃由于热量集中产生的损伤。 2、表面织构形貌有效减少了粘结现象的产生,表面织构的设计在一定程度上改变 了切屑流动方向,使已加工表面粘结现象改善。 3、具有表面织构的铣刀最高加工转速相对于没有表面织构的铣刀提高20%左右。 4、交错排布的织构组织具有更高的面积率,具有更好的摩擦学性能, 4 CN 111590125 A 说 明 书 3/4 页 5、混合构成的织构表面不仅源于二者作用的相互叠加,也得益于两者之间的协同 耦合作用,能够有效降低切削或者钻削力,增大钻屑的卷曲,同时能够捕捉或者容纳极细小 的钻屑,减小铣刀头的磨损。 附图说明 图1为双头铣床的主视剖面结构示意图。 图2为双头铣床的侧视剖面结构示意图。 图3为双头铣床的A处放大结构示意图。 图4为铣刀表面织构两种凹坑的SEM图。 图5为实施例中四种铣刀平均摩擦系数对比结果。