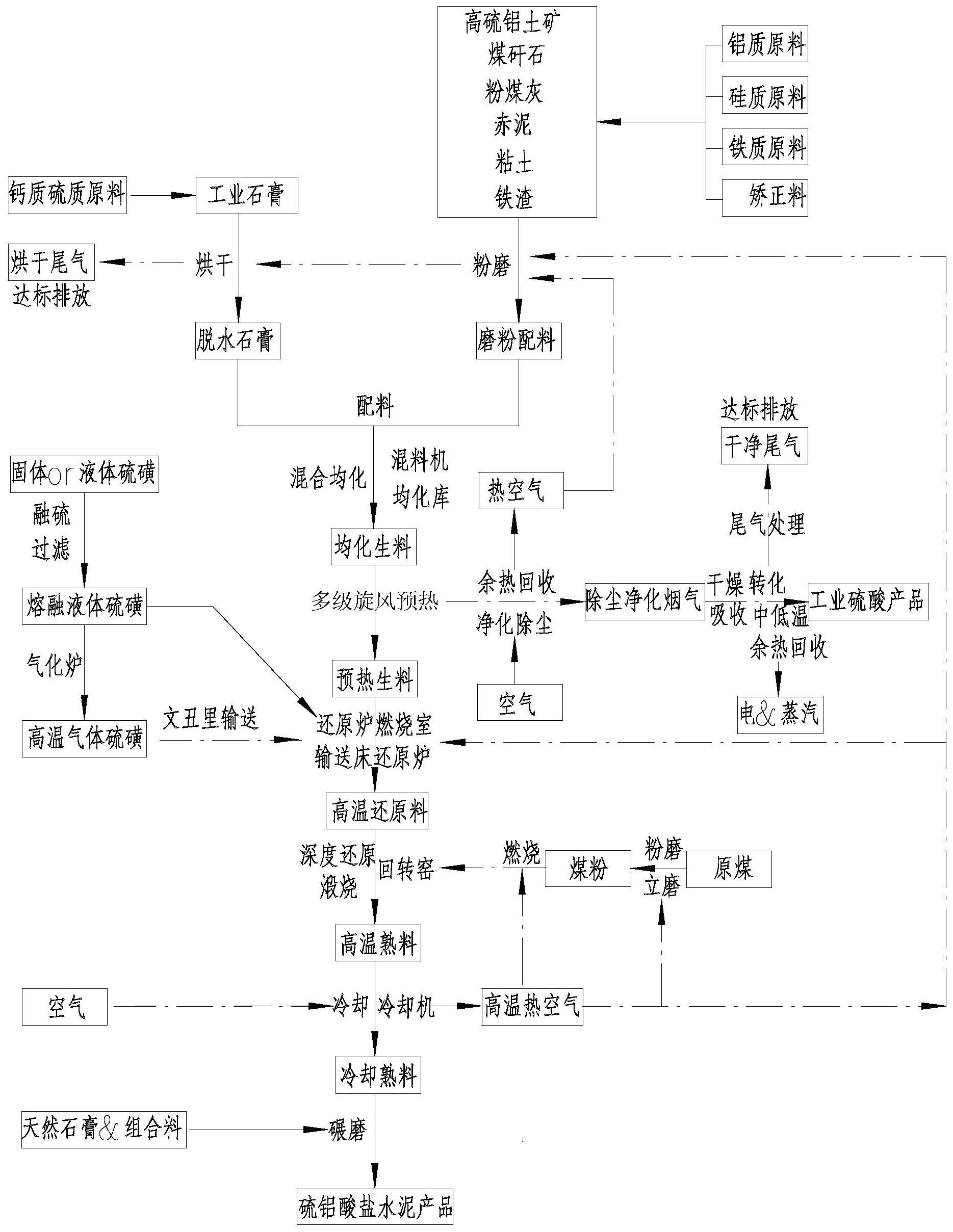
技术摘要:
本发明涉及一种气体硫磺和高硫铝土矿协同还原石膏制硫铝酸盐水泥联产硫酸的方法,该方法以工业副产石膏为主要原料,以气体硫磺和高硫铝土矿中的硫化铁为还原剂,以高硫铝土矿为主要配料,制备硫铝酸盐水泥联产硫酸。与现有技术相比,本发明既能获得水泥生料中石膏的高 全部
背景技术:
硫铝酸盐水泥具有低碱度、高早强、微膨胀、耐腐蚀和抗冻性能好等优点,特别适 合沿海和寒冷地区及应急抢修工程使用需要。传统硫铝酸盐水泥采用石灰石、铝矾土、石膏 为原料经高温(1200~1350℃)烧结而成的以硫铝酸钙 硅酸二钙(C2S)为主要矿物相 组成,再掺入少量石膏并经研磨获得硫铝酸盐水泥产品。与普通硅酸盐水泥相比,由于原料 石灰石用量降低、烧成温度也比硅酸盐水泥1300~1450℃要低100~150℃,因此,在能耗和 CO2排放方面也具有明显优势。但是,现有传统硫铝酸盐生产因对含铝质原材料Al2O3含量 (大于60%)的要求相对较高,不仅增加了原料成本,而且原料来源及取材范围也受到限制, 导致国内硫铝酸盐水泥的年产量并不高,该系列水泥的应用也受到了一定程度的影响,传 统硫铝酸盐水泥的产量无法满足市场和工程需要,另外以石灰石为钙源也增加了CO2排放; 如何提高硫铝酸盐水泥原料的适应性、减少排放、降低能耗和原料成本已成为业内外科研 人员研究的重点。 现有化学工业生产及烟气脱硫副产大量的工艺石膏废渣,其中脱硫石膏和磷石膏 的产生量占工业副产石膏的85%以上。目前,我国脱硫石膏年产量约8000万吨,综合利用率 约83%;磷石膏年产量约8000万吨,综合利用率不足40%;其他副产石膏约2500万吨,综合 利用率约40%。目前工业副产石膏中磷石膏堆存量最多,达5亿吨以上。工业副产石膏大量 堆存,既占用土地,又浪费资源,含有的酸性及其他有害物质容易对周边环境造成污染,已 经成为制约我国燃煤机组烟气脱硫和磷肥企业可持续发展的重要因素。 我国已探明高硫型铝土矿约占资源储量5.6亿t。高硫铝土矿中硫质量分数0.7~ 20%,其中80%~95%的硫以黄铁矿(FeS2)状态存在。铝土矿中的硫会造成溶出碱液中Na2O 损失、腐蚀钢材、造成管道结疤并危害产品质量,无法直接有效利用。目前,针对高硫铝土矿 的研究和应用主要是通过湿法或者火法脱硫,使脱硫产品满足拜耳法生产工艺的要求。 目前,我国工业副产石膏的主要利用方向是水泥缓凝剂、外售或外供、石膏板和石 膏砌块、筑路或充填、建筑石膏粉等,仍然是以初级化、低值化、小规模利用为主。对于工业 副产石膏综合大规模高效利用技术的研究应用主要集中在石膏分解领域,即“硫为硫用、钙 为钙用”,可大致分为两个方向,一是石膏分解方法的研究,一是利用工业副产石膏分解制 备高附加值产品的研究。 石膏分解方法有碳还原法和硫还原法。工业副产石膏碳还原烧制硅酸盐水泥熟料 联产硫酸已经得到工业应用,石膏原料多采用磷石膏,我国以鲁西化工、鲁北化工、贵州金 5 CN 111574079 A 说 明 书 2/19 页 正大等企业为代表,目前建成运行的生产线达到11条,年产硫酸80万吨、水泥120万吨,单条 最大规模是贵州金正大的15万吨硫酸 20万吨硅酸盐水泥生产线。经过三十多年的发展, “第三代”碳还原生产硅酸盐水泥熟料的技术已经较为成熟。石膏碳还原能耗高,尾气中含 有大量的CO2,尾气含SO2浓度偏低,制酸成本较高。硫还原方法“以硫代碳”,用硫磺代替焦炭 作还原剂,相比于碳还原法具有可观的节能减排效益。 中国发明专利CN101708826A“一种硫磺还原分解磷石膏的方法”,该发明公开了采 用多段分解工艺,以气态硫磺还原磷石膏,最终得到CaO固渣产品用于水泥熟料生产,基本 步骤是:高温惰性气体预热磷石膏(500~900℃、10~30min)→通入摩尔分率为10~50%的 气态硫磺还原与磷石膏进行还原反应(60~120min)→冷却后的CaS块料研磨制粉并与磷石 膏按摩尔比(1~1.5:3)混料→CaS高温还原CaSO4 (1000~1400℃、30min~180min)制 得CaO固渣冷却后作为水泥熟料用于水泥生产;但该方法中气态硫磺摩尔分率低,气态硫磺 与石膏的反应时间长,高温CaS需要在惰性气氛下冷却才能防止空气侵入对CaS的氧化,冷 却后磨粉又要与石膏再次加热生产高温固渣CaO,CaO固渣冷却后再去按水泥配料生产水泥 产品,多次加热冷却,工艺流程长且复杂,能耗高,工艺过程及热量组织不合理,也没有如何 获得高温气态硫磺的具体方法,运行操作难度较高,工业化可实施性差。 中国发明专利CN 104555946 B公开的由硫磺气体还原石膏制硫酸联产水泥熟料 的方法,将直接气化产生的500~900℃硫磺气体送入还原炉,将含石膏生料中 的25~ 27%还原成为CaS,出炉物料送入回转窑中完成深度还原和熟料烧结,全系统由制备硫磺气 体、生料配置和旋风预热、石膏还原、石膏还原产物制水泥熟料和尾气制酸构成;该方法是 利用气体硫磺还原石膏生料制硫酸联产硅酸盐水泥熟料的方法,硅酸盐水泥熟料矿物相形 成要求生料石膏中 近100%分解为CaO进入水泥熟料,而熟料中要求几乎不含CaS,需要 控制工业石膏中的磷和氟含量,避免其对水泥性能的影响,对磷石膏通常需要预处理,工艺 操作控制难度较高,产品质量波动较大。 利用工业副产石膏大规模分解制备高附加值产品的研究主要也分为两个方面,一 是以氧化钙为产品,一是以水泥熟料为产品,上述鲁西化工、鲁北化工、贵州金正大等企业 即是采用碳还原法烧制硅酸盐水泥熟料,上述CN101708826A专利产品即是硫还原石膏制固 渣CaO,上述CN 104555946B专利产品即是硫还原石膏制硅酸盐水泥熟料。近些年国内学者 在利用石膏生产硫铝酸盐或贝利特硫铝酸盐水泥方面开展了大量的研究工作:早期的硫铝 酸盐水泥生产其原料石膏大都采用天然石膏,后来有报道采用工业石膏如磷石膏或脱硫石 膏替代天然石膏生产硫铝酸盐或贝利特硫铝酸盐水泥,但这些技术中石膏在烧成矿物相中 主要用作无水硫铝酸钙 中的 及少量高温烧结游离 石膏用量仅为10~30%; 近年来,也有专利和文献报道采用工业石膏为原料经煅烧分解制取硫铝酸盐或贝利特硫铝 酸盐水泥,石膏在矿物相中不仅用作熟料矿物相的无水硫铝酸钙 中的 及少量 高温烧结游离 还可替代原料石灰石作为水泥熟料中CaO的来源,如此可以最大限度地 提高原料石膏的使用量,并可减少或避免由于不用或少用石灰石原料而带来的CO2排放。硫 铝酸盐水泥与硅酸盐水泥相比,除了居多水泥产品的优越性能外,还可使用更多的原料石 膏,生料中石膏不需要像硅酸盐水泥那样要求~100%分解,其中原料石膏仅需要分解60~ 6 CN 111574079 A 说 明 书 3/19 页 90%转化为CaO,其它以 和游离 的形式保留在熟料矿物相中,资源化利用工业石膏制 硫铝酸盐或贝利特硫铝酸盐水泥比制硅酸盐水泥其优势更为显著。但是,如何解决石膏的 有效分解问题,气相中SO2能否得到足够高的浓度,能否满足联产硫酸需要的气浓要求,是 否需要对气相中的SO2进行另外的脱硫处理来满足环保要求,都困扰着相关技术的应用和 发展。刘娜等在实验室中将活性炭与磷石膏按C/S=3配料,在CO2气氛950℃下煅烧1h,然后 切换到空气气氛1000℃下煅烧1h,再升温到1200℃煅烧30min,获得磷石膏的分解率 91.5%,磷石膏的分解产物为CaO,不含CaS,烧结熟料矿物相及性能达到了贝利特-硫铝酸 盐水泥熟料指标要求。中国发明专利CN106630701 .B、CN106630702 .B、CN106603703 .B、 CN106431030.B、CN106431031.B、CN106365476.B、CN106365477.B、CN106365478.B等公开了 采用磷石膏或脱硫石膏完全代替石灰石和天然石膏,再辅以铝矾土、铁渣和/或硅石、无烟 煤为原料按一定比例配置成水泥生料,然后以碳还原经分段或直接煅烧制取硫铝酸盐水泥 熟料,煅烧尾气联产硫酸。中国发明专利申请号CN201810964708.7“一种磷石膏煅烧贝利特 硫铝酸盐水泥熟料的方法及水泥熟料”,该发明公开了配料时按75~80%磷石膏、10~15% 铝质原料、10~15%硅质原料配比混合均匀,首先在1000~1100℃预热并进行脱硫160~ 180分钟,然后再在1320~1350℃烧结60~80分钟形成水泥熟料矿物。上述发明方法目的都 是最大限度地利用了工业副产石膏作为钙质和硫质原料,为工业副产石膏的资源化利用提 供了很好设想,工艺上能打通;但以上方法大都采用活性炭或固体焦炭或无烟煤作为固体 还原剂,将石膏、粘土、高品质铝矾土、粉煤灰、铁渣、高硫煤等一起配料煅烧生产硫铝酸盐 或贝利特硫铝酸盐水泥熟料,碳还原总体上投资能耗高、高CO2排放、炉气SO2浓度偏低、联产 硫酸“二转二吸”困难、运行成本高,存在运行操作、环保和经济成本方面的问题。 还有一些专利或文献报道,采用磷石膏或脱硫石膏或钛石膏等工业副产石膏与石 灰石共同作为水泥配料中钙和硫的来源,与铝矾土等其它原料配置要求的水泥生料,经煅 烧制取硫铝酸盐水泥熟料或贝利特硫铝酸盐水泥熟料,这些方法都是小部分利用石膏分解 来替代一部分石灰石中的CaO,不能大规模有效地利用工业废渣石膏,煅烧烟气中SO2浓度 也达不到常规工业化生产硫酸的浓度要求,石膏分解的SO2也增加了环境保护的负担。 查新现有文献和专利,有采用硫磺或硫磺气体还原石膏制取氧化钙或硅酸盐水泥 的方法的报道,还没有查到关于采用硫磺气体与高硫铝土矿协同还原石膏制硫铝酸盐水泥 联产硫酸的工艺技术或方法的报道。
技术实现要素:
本发明的目的就是为了克服上述现有技术存在的缺陷而提供一种气体硫磺和高 硫铝土矿协同还原石膏制硫铝酸盐水泥联产硫酸的方法,可解决上述问题,既能获得水泥 生料中石膏的高分解率,完全利用石膏分解的CaO替代石灰石中的CaO,又可利用目前很难 被氧化铝、耐火、建材水泥工业直接利用的高硫铝土矿作为原料,其中的Al2O3作为水泥中的 铝质原料,硫化铁作为铁质原料和石膏分解的辅助还原剂,并通过进一步补充还原剂硫磺 气体,使石膏的分解反应快速高效进行,并获得高浓度的气相SO2烟气,为后续联产硫酸生 产提供最佳工艺条件。 对于本发明的描述,除非另有特除说明,使用下列缩写符号指定水泥的矿物组成: C代表CaO; 7 CN 111574079 A 说 明 书 4/19 页 A代表Al2O3; F代表Fe2O3; S代表SiO2; 代表SO3; 代表CaSO4; C2S代表贝利特,即硅酸二钙2CaO·SiO2; C3S代表硅酸三钙3CaO·SiO2; 代表硫铝酸钙3CaO·3Al2O3·CaSO4; C4AF代表铁铝酸四钙4CaO·Al2O3·Fe2O3; 本发明的目的可以通过以下技术方案来实现:一种由硫磺气体与高硫铝土矿协同 还原含石膏生料制硫铝酸盐水泥联产硫酸的方法,该方法以工业副产石膏为主要原料,以 气体硫磺和高硫铝土矿中的硫化铁为还原剂,以高硫铝土矿为主要配料,制备硫铝酸盐水 泥联产硫酸。 具体包括以下步骤: A.气体硫磺制备 将固体或液体硫磺导入熔硫槽采用蒸汽或导热油或电间接加热至120~160℃熔 融成粗硫磺液体,经硫磺过滤器过滤,得到精硫磺液体,再通过输送泵并计量后送入气化炉 内加热气化至450~900℃制得高温气体硫磺,经文丘里引射器将气体硫磺送入还原炉。 B.烘干、粉磨与配料 石膏置于输送床干燥炉内于120~300℃烘干脱水,配料(包括高硫铝土矿、硅质校 正料和铁质校正料)在磨机中烘干粉磨并初步混合,烘干热源是冷却机排出的高温富余空 气、第一级旋风预热器出口烟气余热回收所得的热源和联产硫酸中低温余热回收所得的热 源;将脱水石膏与高硫铝土矿、硅质校正料和铁质校正料在混料机中混合均化,并在均化库 中进一步均化,得到成分均匀的生料。脱水石膏与高硫铝土矿、硅质校正料和铁质校正料按 硫铝酸盐水泥熟料工艺通常要求的三个率值碱度系数(C)、铝硫比(P)、铝硅比(N)计算配料 比,用这些率值来调节硫铝酸盐生料配比和控制硫铝酸盐水泥熟料组分,生产不同品种的 硫铝酸盐水泥熟料。 进一步地,水泥生料的率值为碱度系数C:0.96~0.98,铝硫比P:3.7~3.82,铝硅 比N:3~3.20。选择高硫铝土矿、粉煤灰、煤矸石、赤泥、铁渣、粘土等至少一种或一种以上的 混合物作为配料; 满足上述率值的生料采用的原料包括以下重量份组成:石膏70~95份,高硫铝土 矿3~35份,粉煤灰0~15份,煤矸石0~30份,赤泥0~10份,铁渣0~8份,粘土0~20份,所述 石膏为二水石膏或半水石膏;所述高硫铝土矿Al2O3质量分数为40~75%,S的质量分数0.5 ~20%; 进一步地,所述的石膏为含硫酸钙的钙质和硫质原料,包括工业副产石膏、天然石 膏中的一种或一种以上的混合物,工业副产石膏包括磷石膏、脱硫石膏、盐石膏、钛白副产 石膏、氟石膏、镍石膏、锰石膏中的至少一种或几种混合物,优先采用磷石膏、脱硫石膏。 C.预热预还原 8 CN 111574079 A 说 明 书 5/19 页 由步骤B来的生料计量后送入多级悬浮预热系统的最顶层第一级旋风预热器中, 与还原炉来的热气流在第一级旋风预热器内迅速完成气固传质、换热和分离,再依次通过 下层各级旋风预热器在20~60秒内完成梯级传质、预热和分离;预热后的生料进入还原炉 中,在由回转窑来的高温烟气的携带下与气体硫磺在2~45秒内反应,硫磺与生料中 中 硫的摩尔比为(0~0.7):1,炉内温度700℃~980℃,出还原炉的生料中硫化物与未分解的 的摩尔比为(0.10~0.35):1;生料随烟气离开还原炉后,进入旋风分离器完成气固分 离,温度为700~950℃的预还原生料进入回转窑,烟气进入多级悬浮预热系统,最顶层第一 级旋风预热器出口温度为200~400℃,烟气氧含量0.3~2.0%(v/v),优选0.3~1.5%(v/ v)。所述硫化物为硫化钙(CaS)和硫化铁(FeS)。 进一步地,所述多级悬浮预热系统的预热器级数4~6级,旋风预热器组是单列或 双列,料流是单列串行或两列交叉串行。 进一步地,所述的还原炉为气固同流式输送床还原反应炉,是单次通过式的输送 床反应器或外置分离器的外循环式输送床反应器。 进一步地,所述的还原炉,其底部设置燃烧室,其燃料是由A来的液体硫磺或气体 硫磺的一种或二种的组合。还原炉底部设置燃烧室,补充提供 预还原所需的热量,出回 转窑的高温烟气部分通过燃烧室进入还原炉,其余部分走旁路直接进入还原炉,该燃烧室 所需氧一部分来自回转窑尾气中带来的氧气,另一部分通过补充冷却机排出的热空气。 进一步地,所述的还原炉出口旋风分离器,其出口烟道设置成补氧燃烧室,补充空 气用于消耗还原炉烟气中剩余的气体硫磺,通过检测顶级预热器出口烟气中的氧含量0.3 ~1.5%(v/v)来调节控制补充进入燃烧室的空气量,保证旋风预热器系统为弱氧化气氛及 顶级预热器出口尾气中不含有单质硫,燃烧室补充的空气采用冷却机排出的热空气。 D.深度还原与熟料烧结 预还原生料经下料管进入回转窑,并控制回转窑出口烟气中氧气含量在<2%的 条件下,生料中的硫化物与 在窑内950~1150℃下发生氧化还原反应,物料在窑内还原 时间为5~30min,60~90%的S元素以SO2的形式进入窑内烟气中,其它元素发生初步的固 相反应;深度还原之后的物料在1100~1300℃烧结并形成硫铝酸盐水泥熟料,物料的烧结 时间为20~60min。 烧结燃料包括含硫煤、天然气、燃料油、煤气、液化石油气中的一种或其混合物。 进一步地,深度还原与熟料烧结在一个回转窑或两个串联的回转窑内分段完成: 当采用一个回转窑时,石膏的深度还原与熟料烧结在一个回转窑内完成;首先,预 还原生料经旋风分离器下料管进入回转窑,生料中的硫化物与 在窑内完成氧化还原反 应,该反应段窑内温度950~1150℃,物料在窑内反应停留时间5~30min;然后进入烧成段, 随着窑内温度升高和停留时间延长,完成硫铝酸盐熟料的烧结,该部分窑内温度1100~ 1300℃,物料在窑内停留时间20~60min,入窑风由送煤风和出篦冷机的高温空气组成,窑 烟气中含氧气含量控制在0~1.5%(v/v)弱氧化气氛;回转窑进入还原炉的烟气温度为900 ~1100℃。 当采用两个回转窑串联分段烧成时,深度还原和熟料烧成分别在还原回转窑和烧 结回转窑两个回转窑内完成;生料经旋风分离器下料管进入还原回转窑,生料中的硫化物 9 CN 111574079 A 说 明 书 6/19 页 与 在还原窑内完成氧化还原反应,窑内温度950~1150℃,物料在还原窑内停留时间5~ 30min,入窑风由送煤风和烧结回转窑的尾气组成;出还原回转窑950~1150℃的还原料经 下料管进入烧结回转窑完成硫铝酸盐熟料的烧结,窑内温度1100~1300℃,物料在窑内停 留时间20~60min,入烧结回转窑风由送煤风和出篦冷机的高温空气组成,烧结回转窑出口 烟气中含氧气含量控制在2~10%氧化气氛;入还原回转窑风由送煤风和出烧结回转窑的 高温烟气组成,烧结回转窑进入还原回转窑的烟气温度为1000~1200℃,还原窑出口烟气 中含氧气含量控制在0~1.5%弱氧化气氛,还原回转窑进入还原炉的烟气温度为900~ 1100℃。 E.熟料冷却、热量回用及净化制硫酸 出回转窑的高温熟料进入冷却机中与空气换热冷却至(室温 65)℃,出冷却机的 高温空气一部分进入回转窑中作为燃料的助燃空气,一部分进入还原炉燃烧室和旋风分离 器出口燃烧室作为部分硫磺燃烧的助燃空气,剩余部分作为石膏烘干和其它原料的烘干热 源; 出第一级旋风预热器的含硫烟气经余热回收、除尘后进入后续常规的硫酸生产工 序进行洗涤净化、干燥、转化、吸收、中低温余热回收、最终尾气处理制取工业硫酸产品。 所述冷却机为篦冷机、滚筒冷却机、立式冷却机中的一种。 F、水泥的制备 由步骤E冷却机来的冷却熟料,添加石膏和组合料、再经后续碾磨加工获得不同性 能要求的硫铝酸盐水泥产品,产品细度为碾磨至比表面积320~420m2/kg,优选为360m2/kg。 根据熟料中高温烧结石膏的含量多少,结合试验和计算确定不掺入或少掺入石 膏,即能达到硫铝酸盐水泥产品的性能要求。 进一步地,所述硫铝酸盐水泥产品包括普通硫铝酸盐水泥、高铁硫铝酸盐水泥、高 硅硫铝酸盐水泥、高钙硫铝酸盐水泥,熟料矿物组成为 C2S:8~60%,C4AF: 3~35%,C3S:0~50%, 其他:0~5%。 本发明方法采用硫还原法将石膏与高硫铝土矿应用于硫铝酸盐水泥生产石膏部 分分解获得CaO作为钙质和 原料,高硫铝土矿中的氧化铝作为铝质原料,铁作为铁质原 料,低价硫作为还原剂促进石膏分解反应,过程中存在 与S2生成CaS的反应、 与CaS生 成CaO的反应、FeS2分解生成FeS和S2的反应、 与FeS生成CaO和Fe2O3的反应、以及CaO与 Fe2O3、Al2O3、SiO2、 等进行的硫铝酸盐水泥熟料烧成反应,还原剂形成的气相产物是有用 的SO2一并进入烟气中提高了SO2气浓,有利于后续烟气制酸,产能提高、能耗降低、成本下 降,与碳还原相比可减排大量CO2;利用高硫铝土矿配料可以降低还原剂硫磺气体的用量, 为高硫铝土矿的资源化直接利用找到了新的出路,该方法是一种工业副产石膏和高硫铝土 矿高质高效协同利用的新途径。 与现有技术相比,本发明具有以下的优点和特点: 1、与现有其他利用石膏制硫铝酸盐水泥相比,本发明技术有效将石膏中 分解 第一步转化为CaS的气-固预还原反应控制在窑外还原反应炉内还原气氛下进行,将CaS& FeS与 固-固氧化还原反应控制在回转窑内弱氧化气氛下进行,使生料中60~90%石膏 10 CN 111574079 A 说 明 书 7/19 页 分解成CaO,可以有效的控制石膏分解量,实现石膏分解出的CaO完全替代硫铝酸盐水泥生 产需要石灰石分解来的CaO,确保硫铝酸盐水泥熟料主要矿物相达到相关品质指标要求,加 入石膏量是硫铝酸盐水泥中所有钙源与硫源的总和,可最大限度地资源化利用了工业废渣 石膏,而且也可以多配入工业石膏通过高温烧结转化为硫铝酸盐水泥熟料中高温烧结石 膏,从而可减少水泥产品后掺石膏的量,生产一吨水泥熟料可以使用工业石膏1.1~1,3吨, 既可大量消耗工业石膏,又可节省石灰石和天然石膏资源。 2、以高硫铝土矿作为硫铝酸盐水泥的原料,既利用了其中FeS2的还原性促进了 分解为氧化钙,又充分利用了其中铝、硫、硅、铁资源作为硫铝酸盐水泥矿物相必要的原料, 使高硫铝土矿这一很难被现有氧化铝、耐火、水泥工业等直接利用的废矿渣得到了有效资 源化利用,并降低了硫磺气体的消耗,降低了硫铝酸盐水泥原料生产成本。 3、在高硫铝土矿中FeS2的还原量不足的情况下,“以硫代碳”,用硫磺气体替代现 有工业化生产技术中焦炭或无烟煤作为补充还原剂,使石膏分解的预还原反应由固-固反 应变为气-固反应,预还原反应由窑内成功地移至窑外还原分解炉内,预还原反应温度由传 统回转窑内900~1200℃下降为700~980℃,反应时间由15~40分钟缩短为2~45秒钟,降 低了还原反应能耗,缩短了反应时间,提高了石膏分解效率。 4、将硫磺气体与回转窑烟气混合加入还原炉底部,通过检测高硫铝土矿中FeS2含 量,并控制硫磺气体的加入量来确保还原气氛,并在维持反应温度下,控制还原反应炉内 部分转化为CaS的最佳摩尔分率0~22%,即有效地控制了回转窑内 的目标分解率, 使石膏分解为CaO的量达到替代石灰石的要求,煅烧分解控制方便,有效保证形成硫铝酸盐 水泥熟料矿物相所要求的CaO和 5、还原反应炉内采用气体硫磺作为固体石膏物料的还原气,石膏预还原所需要的 热量由窑尾烟气和部分液体或气体硫磺燃烧提供,硫磺即是还原剂又是燃料,最终都转化 成为烟气制酸前驱物SO2。尾气中SO2是回转窑 与CaS、FeS反应生成SO2和还原反应炉硫磺 还原生成SO2以及作为燃料的少量硫磺燃烧生产的SO2的叠加,在还原剂硫磺用量控制最少 的条件下获得系统最终尾气中SO2浓度最高,SO2组分的摩尔分率可提高到12~18%,对后续 硫酸生产SO2转化、吸收,系统工艺参数优化及生产能力提高极为有利,有利于降低硫酸生 产系统设备规格或提高装置生产能力,可实现“二转二吸”和中低温余热回收,工艺设备规 格小,综合运行成本低。 6、由于0~22%石膏已经在窑外还原炉中快速转化为CaS,在窑内的分解温度也降 低到950~1150℃,入煅烧窑的物料温度较前提高150℃以上,大大缩短了物料在回转窑内 的停留时间。 7、由于在窑外还原炉内完成了 部分转化为CaS,窑内仅进行 与CaS、FeS生成 氧化钙的深度氧化还原反应,仅需要控制该反应在弱氧化气氛下进行,相比传统的碳还原 窑操作控制容易,反应时间缩短10~30分钟,回转窑长度缩短~1/4,有利于反应效率和回 转窑的容积热负荷提高,使得生产控制易于进行,提高了生产效率。 8、如果采用磷石膏作为原料,磷石膏中含有少量的P2O5、MgO、Na2O、K2O、F等杂质, 在硅酸盐水泥烧成时,P2O5、F等杂质的存在对水泥品质有害,必须对磷石膏进行预处理确保 11 CN 111574079 A 说 明 书 8/19 页 原料石膏中P2O5的量控制在一定范围内;而在硫铝酸盐水泥烧结中,石膏中少量的P2O5、 MgO、Na2O、K2O、F等杂质在烧结过程中作为矿化剂,有利于水泥烧成矿物相形成,在烧成过程 中被固化到矿物相中,而不影响硫铝酸盐水泥的性能,因此不需要对磷石膏进行预处理。 9、从使用工业石膏替代石灰石作为钙源,硫磺气体和高硫铝土矿中的硫化铁替代 焦炭或含硫煤作为还原剂、合理组织工艺过程降低能源消耗等多方面减少了CO2生成和排 放,有利于环境保护。 10、本发明工艺流程简单、系统控制指标可实施性强、操作运行管理方便、工艺设 备先进,装置投资省、能耗低、运行成本低,自动化程度高。 附图说明 图1为本发明总工艺流程图; 图2为本发明实施例1的工艺流程图; 图3为本发明实施例2的工艺流程图; 图4为本发明实施例3的工艺流程图; 图5为本发明实施例4的工艺流程图; 图6为本发明实施例5的工艺流程图; 图7为本发明实施例6的工艺流程图; 图8为本发明实施例7的工艺流程图; 图9为本发明实施例8的工艺流程图。