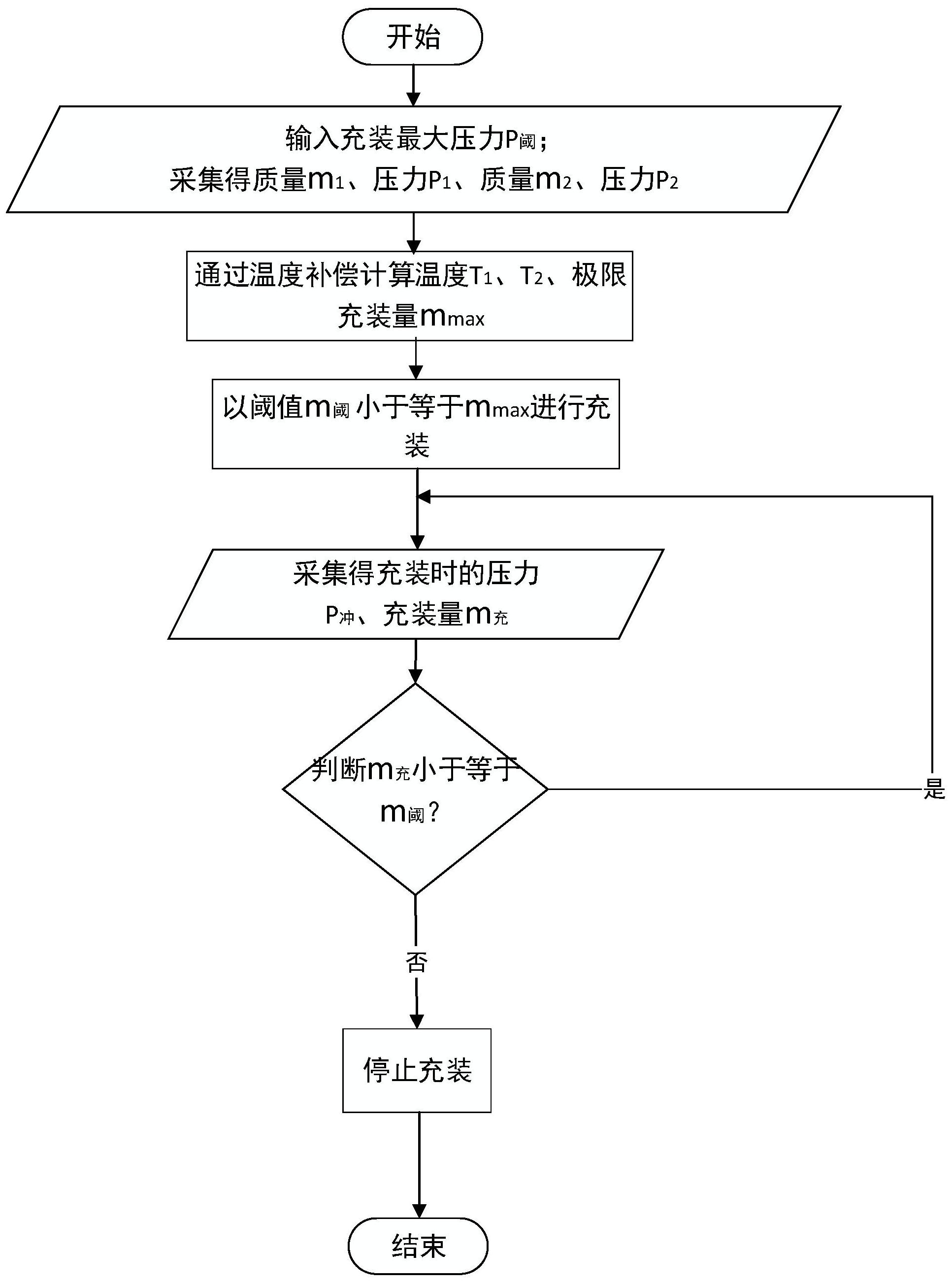
技术摘要:
本发明公开了一种限压式气体充装系统及充装方法,涉及气体充装技术领域,所述限压式气体充装系统包括数据采集模块、预充装计算模块、实时监测模块以及执行模块;所述限压式气体充装方法包括,预充装步骤、数据采集步骤、数值计算步骤、正式充装步骤和充装监控步骤;通 全部
背景技术:
随着国家对清洁能源的大力政策支持和发展推进,目前以天然气为重点的充装站 点在不断的增多,应用上有着广泛应用场景,但行业上采用的气体充装系统和气体充装方 法不能准确地计算出压力容器具体最大充装阈值,在气体的充装过程中存在诸多的安全隐 患。 例如专利号为200880024843.8,申请日为2008年4月17日公开的给罐填充加压气 体的方法,其仅通过缓冲容器形成压力差实现对气体的填充,但该方法不能实时监测压力 容器内气体的压力、温度,无法得知压力容器的体积、压力容器内的初始质量,不能够根据 不同的指定压力得知压力容器能够充装的最大充装量,在充装压缩气体时,容易产生因过 量充装和超压充装带来的安全风险,无法确保设备的使用安全和相关人员的人身安全。
技术实现要素:
本发明的目的在于:针对上述存在的问题,本发明提供一种限压式气体充装系统 及充装方法,解决了充装压缩气体时,容易产生因过量充装和超压充装带来安全风险的问 题,能够实时监测压力容器内气体的压力和温度,能够根据预充装工序计算得到压力容器 的体积、压力容器内的初始质量,根据不同的设定压力得知压力容器充装的最大充装量。使 气体在充装时更为安全,突破了在气体充装时只能根据指定压力容器进行定值充装的局 限,适用于各种压力容器在不同压强下的充装,应用范围更广,应用场景更为多样化。 本发明采用的技术方案如下: 一种限压式气体充装系统,包括数据采集模块、预充装计算模块、实时监测模块以 及执行模块,数据采集模块分别连接预充装计算模块和实时监测模块,预充装计算模块和 实时监测模块之间信号连接,所述实时监测模块信号连接执行模块,所述执行模块连接电 磁阀;所述数据采集模块通过质量流量计和压力传感器采集并向预充装计算模块传送预充 装n次测得的mn、Pn数据值(其中n≥2);所述预充装计算模块基于mn、Pn、P阈数据值,计算得出 极限充装量 mmax值。 由于采用了上述技术方案,能够通过n次预充装计算得到压力容器的极限充装量, 解决了气体在充装过程中,无法得知压力容器能容纳的极限气体质量的问题。 进一步的所述预充装计算模块基于极限充装量mmax值,设定并向实时监测模块发 送安全充装量m阈值;所述实时监测模块接收数据采集模块实时采集的m 充值,并将、m充值与 设定m阈值比较,当m充≥m阈时,向执行模块发送执行信号关闭电磁阀。 由于采用了上述技术方案,当充装量到阈值时,即停止充装,对整个充装过程进行 实时监测,能够有效消除因错误充装带来的安全隐患。 进一步的,所述m阈值小于等于极限充装量。 4 CN 111720728 A 说 明 书 2/5 页 由于采用了上述技术方案,将充装阈值小于等于极限充装量,解决了在实际应用 时,因数据采集和计算带来的误差导致的过量充装和超压充装的问题。 进一步的,所述预充装次数n为2,所述预充装计算模块能够基于下述式 (1)计算 出压力容器的初始充装质量m0: m0=P1T2m2/(P2T1-P1T2)-m1 (1) 在式(1)中,“P1”是第1次预充装工序后通过压力传感器采集的压力容器内气体压 力,“T1”是第1次预充装工序后计算的压力容器内气体温度,“m1”是第1次预充装工序后通过 质量流量计采集的充装质量,“P2”是第2次预充装工序后通过压力传感器采集的压力容器 内气体压力,“T2”是第2次预充装工序后计算的压力容器内气体温度,“m2”是第2次预充装工 序后通过质量流量计采集的充装质量;(其中T1和T2通过质量流量计测得温度进行温度补偿 的方式计算得到。) 所述预充装计算模块能够基于下述式(2)计算出压力容器的体积V: V=Z(m0 m1 m2)RT2/P2M (2) 在式(2)中,“Z”为天然气偏差系数,是一个固定值,“R”为通用气体常数,“M”为物 质的摩尔质量。 由于采用了上述技术方案,在充装气体时,采集两次预充装时的充装质量和压力, 即可计算出初始充装质量m0和压力容器的实际体积V,使得根据初始充装质量m0得到的最大 充装量mmax更为精准,在实际应用中,能确保即便压力容器在充装气体前,内部留有一定质 量的气体,也不会出现过量充装和超压充装的现象,同时也能保证在不知道压力容器体积 的情况下,也可以安全得进行气体充装。 一种限压式气体充装方法,它包括以下步骤: 预充装步骤:将压力容器连接充气管路,对压力容器进行n次的预充装(其中n≥ 2); 数据采集步骤:通过设置在充气管路上的质量流量计和压力传感器以及电磁阀的 关断,分别采集预充装n次中的mn、Pn数据值(其中n≥2); 数值计算步骤:根据预先设定充装阈值压力P阈值,基于采集到的mn、Pn数据值,计算 得出极限充装量mmax值,并设定安全充装量m阈值; 正式充装步骤:基于安全充装量m阈值,控制充装到压力容器的气体充装量。 由于采用了上述技术方案,能够通过n次预充装计算得到压力容器的极限充装量, 解决了气体在充装过程中,无法得知压力容器能容纳的极限气体质量的问题,同时依据设 定的充装最大压力和安全充装量阈值能够提高气体在充装过程中的安全性。 进一步的,所述限压式气体充装方法还包括 充装监控步骤:通过设置在充气管路上的质量流量计和压力传感器,分别采集气 体实时充装的m充、P充值,将m充值与m阈值比较,当m充≥m阈时,关闭电磁阀停止气体充装。 由于采用了上述技术方案,对整个充装过程进行实时监测,当充装量或充装压力 任一达到阈值时,即停止充装,能够有效降低因错误充装带来的安全隐患,不会出现过量充 装和超压充装的现象。 进一步的,根据采集到的Pn值和温度变化系数值,得到每次预充后压力容器内气 体的温度Tn值,再依据n次预充装得到的mn、Pn、Tn值,结合得到压力容器的初始充装质量m0, 5 CN 111720728 A 说 明 书 3/5 页 在得到初始充装质量m0的基础上,计算压力容器的体积V,根据设定的充装最大压力P阈、压 力容器体积V和压力容器初始充装质量 m0得到极限充装量mmax,按照所述设定安全充装量 m阀小于等于极限充装量mmax值。 由于采用了上述技术方案,在充装气体时,可以根据n次预充装时采集的充装质量 和压力,即可计算出初始充装质量m0和压力容器的实际体积V,使得根据初始充装质量m0得 到的最大充装量mmax更为精准。在实际应用中,能确保即便压力容器在充装气体前,内部留 有一定质量的气体,也不会出现过量充装和超压充装的现象,同时也能保证在不知道压力 容器体积的情况下,也可以安全得进行气体充装。 进一步的,所述n为2,所述数据采集步骤采集第1次预充装的充装质量 m1和压力 P1、第2次预充装的充装质量m2和压力P2;所述压力容器的初始充装质量m0依据下述式(1)计 算得出, m0=P1T2m2/(P2T1-P1T2)-m1 (1) 在式(1)中,“P1”是第1次预充装工序后通过压力传感器采集的压力容器内气体压 力,“T1”是第1次预充装工序后计算的压力容器内气体温度,“m1”是第1次预充装工序后通过 质量流量计采集的充装质量,“P2”是第2次预充装工序后通过压力传感器采集的压力容器 内气体压力,“T2”是第2次预充装工序后计算的压力容器内气体温度,“m2”是第2次预充装工 序后通过质量流量计采集的充装质量;(其中T1和T2通过质量流量计测得温度进行温度补偿 的方式计算得到。) 所述压力容器的体积V依据下述式(2)计算得出, V=Z(m0 m1 m2)RT2/P2M (2) 在式(2)中,“Z”为天然气偏差系数,是一个固定值,“R”为通用气体常数,“M”为物 质的摩尔质量。 由于采用了上述技术方案,在充装气体时,采集两次预充装时的充装质量和压力, 即可计算出初始充装质量m0和压力容器的实际体积V,工序简单,操作效率高。 综上所述,由于采用了上述技术方案,本发明的有益效果是: 1、本发明方法,解决了充装压缩气体时,容易产生因过量充装和超压充装带来安 全风险的问题,提高了充装过程的安全性。 2、本发明方法,通过n次预充装采集的数值计算出充装量阈值(其中n ≥2),工序 简单,操作效率高。 3、本发明方法,适用于各种压力容器在不同压强下的充装,应用范围更广,应用场 景更为多样化。 4、本发明方法,可以为在充装气体前,内部留有一定质量气体的压力容器进行气 体充装。 5、本发明方法,能够在充装时实时监测压力容器的充装量和压力容器内气体的压 强和温度,进一步提高气体充装时的安全性。 附图说明 图1是运用本发明的一个实施例所涉及的装置结构图; 图2是本发明的系统结构图; 6 CN 111720728 A 说 明 书 4/5 页 图3是本发明的气体充装过程流程图。