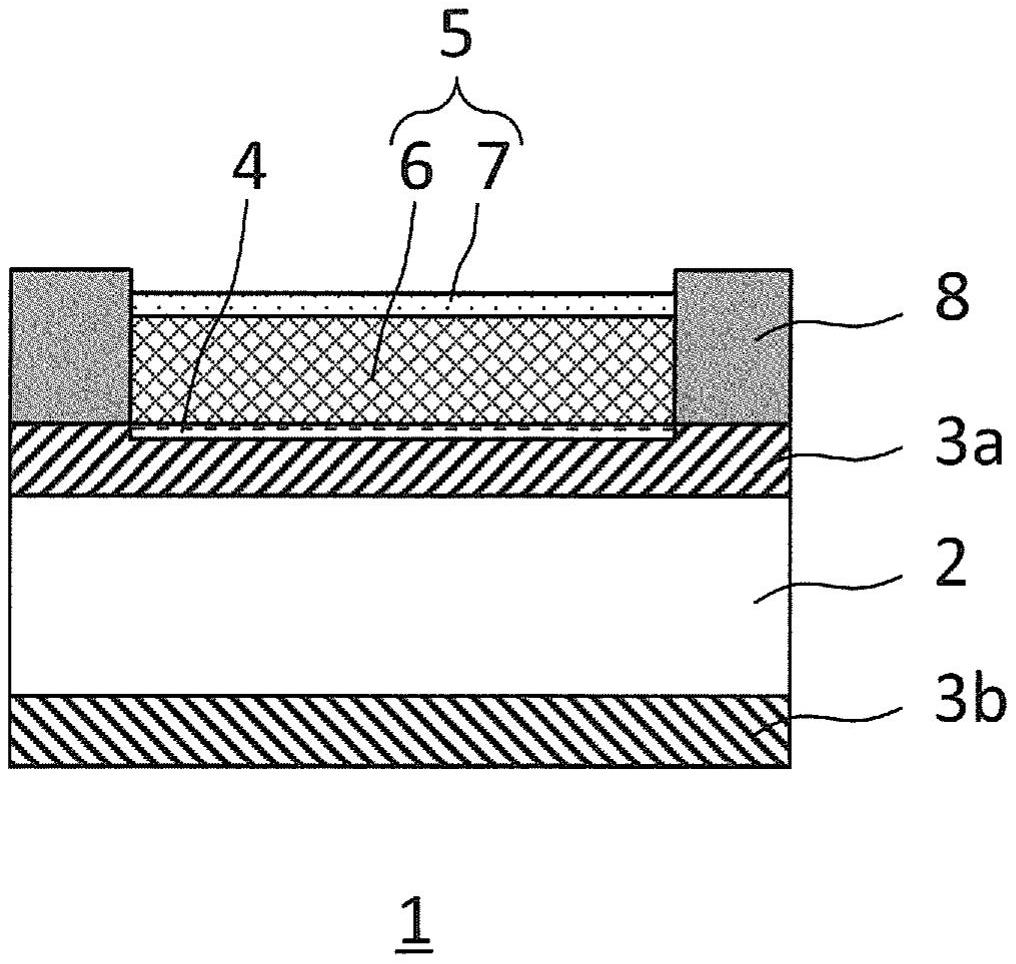
技术摘要:
半导体元件,其为在具有表侧电极及背侧电极的表背导通型基板的至少单侧的电极上依次形成有第一电极及非电解镀层的半导体元件,上述第一电极含有比形成上述电极的金属贵的元素,上述电极形成有上述第一电极,上述第一电极的面积比形成有上述第一电极的所述电极的面积小 全部
背景技术:
目前为止,在将表背导通型的半导体元件安装于模块的情况下,将半导体元件的 背侧电极焊接于基板等,将半导体元件的表侧电极进行引线接合。但是,近年来,从制造时 间缩短及材料费用削减的观点考虑,使用将金属电极直接焊接于半导体元件的表侧电极的 安装方法增多。就半导体元件的表侧电极而言,一般由铝或铝合金形成,因此为了进行焊 接,需要在半导体元件的表侧电极上形成数μm的厚度的镍膜、金膜等。 但是,在使用如蒸镀或溅射的真空成膜法来形成镍膜等的情况下,通常只得到1.0 μm左右的厚度。另外,如果要想使镍膜厚膜化,则制造成本上升。因此,作为以低成本、可高 速且厚膜化的成膜方法,镀敷技术受到关注。 作为镀敷技术,有在由铝或铝合金形成的电极(以下有时简写为“Al电极”)的表面 能够选择性地形成镀层的非电解镀敷法。作为非电解镀敷法,一般利用钯催化法及锌酸盐 法。就钯催化法而言,是在Al电极的表面使钯作为催化剂核而析出,形成非电解镀层。另外, 就锌酸盐法而言,是在Al电极的表面使锌与Al进行置换而由此使其作为催化剂核来析出, 形成非电解镀层。就用于该方法的锌酸盐液而言,由于价格便宜,因此在不断地被广泛采 用。 例如,在专利文献1中,提出半导体元件的制造方法,其包含:在半导体基板上的Al 电极的侧面形成由聚酰亚胺制成的保护膜,在没有形成保护膜的Al电极的表面,通过非电 解镀敷法,选择性地形成包含镍镀层和在其上层叠的金镀层的非电解镀层。 现有技术文献 专利文献 专利文献1:日本特开2005-51084号公报
技术实现要素:
发明要解决的课题 由于在保护膜与非电解镀层之间没有形成化学键合,因此在其间存在间隙。如果 该间隙大、非电解镀敷处理的时间长、或者进行高温处理,则有时药液从该间隙侵入而腐蚀 Al电极。如果发生Al电极的腐蚀,则Al电极与接合用的非电解镀层之间的附着力降低,在焊 接或引线接合时有时非电解镀层鼓起、剥离。 用于解决课题的手段 本发明为了解决上述的课题而完成,目的在于提供在焊接或引线接合时非电解镀 层不鼓起且不剥离的、接合可靠性高的表背导通型的半导体元件及其制造方法。 3 CN 111742395 A 说 明 书 2/14 页 本发明人为了解决上述这样的课题深入研究,结果发现:在表侧电极或背侧电极 上,形成含有比形成该电极的金属贵的元素且面积比该电极小的第一电极,在该第一电极 上形成非电解镀层,由此能够防止电极的损伤引起的电极与非电解镀层之间的附着力的降 低,完成了本发明。 即,本发明为半导体元件,是在具有表侧电极及背侧电极的表背导通型基板的至 少单侧的电极上依次形成有第一电极和非电解镀层的半导体元件,上述第一电极含有比形 成上述电极的金属贵的元素,所述电极形成有上述第一电极,上述第一电极的面积比形成 有上述第一电极的上述电极的面积小。 另外,本发明为半导体元件的制造方法,其包含:在表背导通型基板的单侧形成表 侧电极的工序;在上述表侧电极上的一部分使用非电解镀敷法使比形成上述表侧电极的金 属贵的元素析出而形成第一电极的工序;和在上述第一电极上使用非电解镀敷法将上述第 一电极作为催化剂来形成非电解镀层的工序。 发明的效果 根据本发明,能够提供在焊接或引线接合时非电解镀层不鼓起且不剥离的、接合 可靠性高的表背导通型的半导体元件及其制造方法。 附图说明 图1为根据实施方式1的半导体元件的截面示意图。 图2为根据实施方式1的半导体元件的平面示意图。 图3为根据实施方式1的另一半导体元件的截面示意图。 图4为根据实施方式2的半导体元件的截面示意图。 图5为根据实施方式2的另一半导体元件的截面示意图。 图6为根据实施方式3的半导体元件的截面示意图。 图7为根据实施方式3的另一半导体元件的截面示意图。