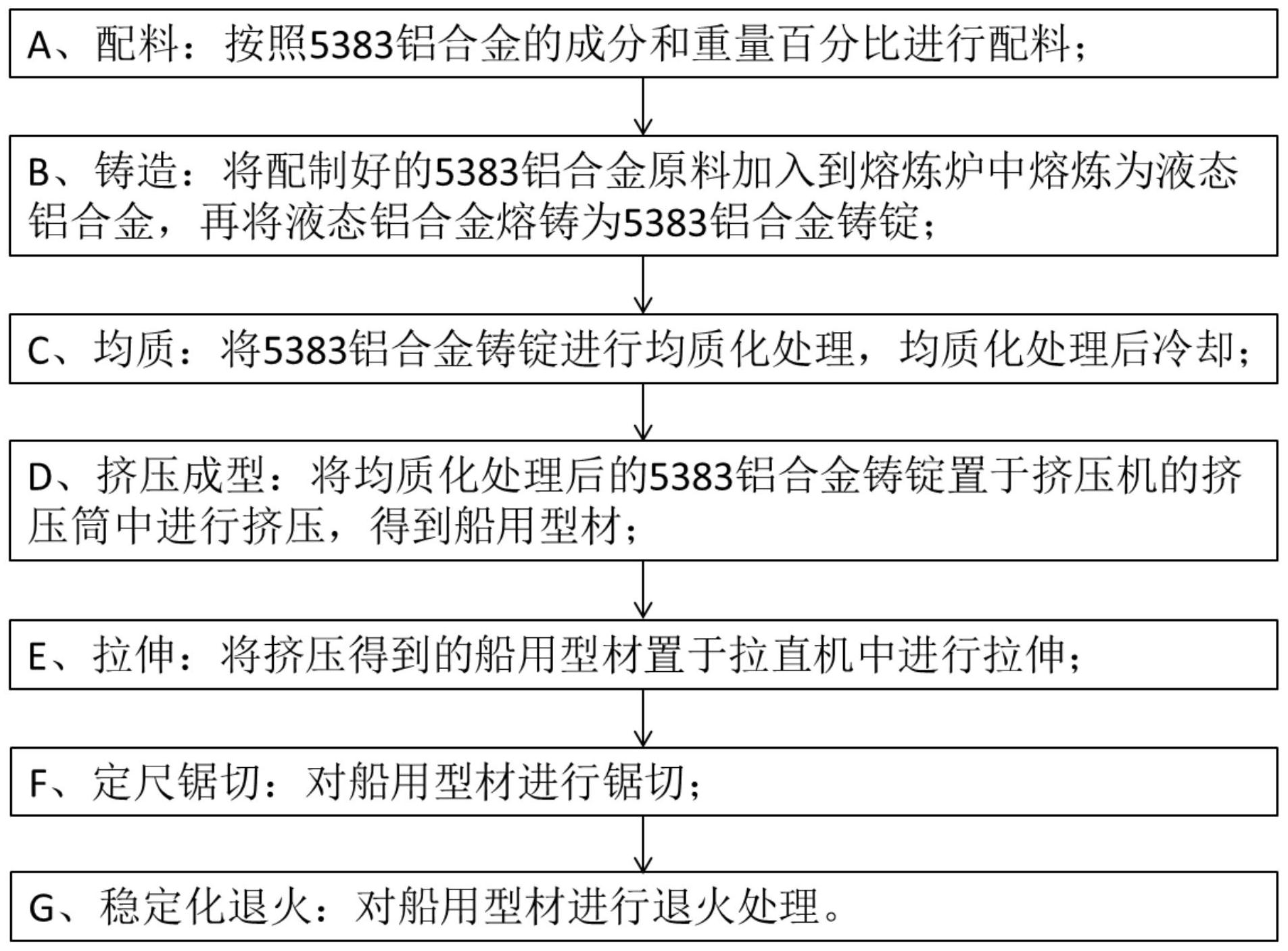
技术摘要:
本发明公开了一种高强度耐腐蚀的5383铝合金及船用型材制备工艺,5383铝合金具有结构强度高、耐腐蚀能力和可加工成型性能好的优点,兼顾了力学性能、抗腐蚀性能和生产成本;并且,制备工艺简单,生产出来的型材不仅尺寸可控,不良率低,使型材具有更高的尺寸精度,而且 全部
背景技术:
铝合金船舶具有便捷性、安全舒适、耐腐蚀、抗冲击等多种优势,是促进我国船舶 工业结构调整转型升级、加快我国世界造船强国建设步伐的必然要求,对维护国家海洋权 益、加快海洋开发、保障战略运输安全、促进国民经济持续增长具有重要意义。但对于船舶 用铝合金轻量化而言,强度、抗腐蚀性、可焊接性等性能缺一不可,当前行业内主要选用 5083合金或者6082合金。由于6082属于可热处理强化合金,这种合金在焊后其焊接区强度 会出现剧烈衰减(焊缝仅为母材的60%左右),且6XXX系合金的抗腐蚀能力低于5XXX系合 金,长期浸泡在海水中可能出现晶间腐蚀,因此主要适用于船体上部结构如甲板等部件中, 应用范围及尺度极为有限。而5083合金属于不可热处理强化合金,焊后强度与母材相比无 明显的衰减(一般可达到母材强度的90%以上),且在海水中具备优异的腐蚀抗力,一般应 用在船舶的外壳、龙骨等重要的结构件上,作为当前铝合金船舶结构件中最主要应用的材 料。5083合金材料主要的强化方式为加工硬化,即通过对材料施加大量的变形量,通过室温 下冷塑性变形这种“冷作硬化”引入大量的高密度位错,造成材料的“加工硬化”来对材料进 行强化处理,其主要生产制备方式为板材压延加工的方式,对均匀化处理后的铸锭通过多 道次的中间退火、热轧、冷轧等工序制备获得,生产工序极其复杂。而对于挤压成型而言,材 料只需通过模具挤出即可一次成型,通过拉伸矫直消除材料中应力即可获得最终的成品, 生产工序简单。 同时,对于5XXX系合金而言,一方面随着Mg含量的增加,材料的强度越来越高,用 于结构件上轻量化减重效果越明显,另一方面,当Mg含量超过3.5%(wt.%)时,随着Mg含量 的增加,晶界处易连续析出β相(Mg5Al8),这种β相与铝基体之间存在明显的电位差,会造成 材料的抗腐蚀能力大幅下降,这种影响尤其是在最终的冷加工变形工序,随着冷加工变形 量的增加,位错在晶界处会“塞积”,材料中引入的大量位错结构会促使Mg朝着晶界迁移,更 利于这种β相沿晶界析出,对材料的腐蚀抗力造成恶劣影响,因此在高镁含量的5XXX系合金 中,必须严格控制其冷加工变形量。同时在挤压过程中,尺寸精度主要依靠模具设计的来保 证,模具的模孔设计准则主要是根据材料的热胀冷缩原理以及后续的拉伸加工变形量等参 数对尺寸的影响,若通过采用传统的5083合金挤出挤压毛坯后,后续对挤压毛坯加强塑性 变形获得成品的方式,对于断面较为复杂的产品尺寸精度无法保证,工艺几乎无法实现。 因此开发一种强度较高、抗腐蚀能力强、工艺简便、断面适用性强的船用高强铝型 材材料及工艺成为当务之急。故应运而生了一种5383铝合金,其结构强度较5083铝合金得 到较大幅度提高,耐腐蚀能力与5083铝合金持平或更优,可加工成型性能与5083铝合金相 当。有客户提出,船用龙骨材料选取5383合金,需达到屈服强度≥190MPa、抗拉强度≥ 310MPa、延伸率≥13%,更理想地,达到屈服强度≥220MPa、抗拉强度≥310MPa、延伸率≥ 3 CN 111549264 A 说 明 书 2/8 页 10%,在腐蚀抗力方面,需要在30℃下的硝酸溶液环境中进行24h的接触腐蚀测试,测试后 单位面积的重量损失需低于25mg/cm2,即存在较低的晶间腐蚀倾向,更理想地,试验后需低 于15mg/cm2,无任何晶间腐蚀倾向,达到高强高腐蚀抗力的船用铝合金材料应用要求。 根据资料报道,5383合金属于高Mg含量的5XXX系合金,大多数企业为了提升5383 合金的强化能力和腐蚀抗力等性能指标,主要是通过添加Sc、Er等稀土元素实现,但稀土元 素的价格昂贵,导致成本高昂。而有的企业为了降低成本,其研发的5383铝合金在合金成分 和配比上实际仍是5083铝合金,实质是对5083铝合金加大变形量获得的5383铝合金,其初 始挤出后强度比较低,因而为了达到高强船用铝合金骨架型材的力学性能标准,必须要在 拉伸矫直时对材料很大的冷加工量,不仅工序极为复杂,导致尺寸精度不易控制,不良率极 高,同时材料的腐蚀抗力下降,无法满足船用材料的实际应用需求。 解决以上问题成为当务之急。
技术实现要素:
为解决以上的技术问题,本发明提供了一种高强度耐腐蚀的5383铝合金及船用型 材制备工艺。 其技术方案如下: 一种高强度耐腐蚀的5383铝合金,其要点在于,铝合金的成分和重量百分比为:Si ≤0.16%、Fe≤0.22%、Cu≤0.12%、Mn:0.75~0.95%、Mg:4.3~4.8%、Cr≤0.1%、Zn≤ 0.37%、Ti≤0.05%、Zr:0.05~0.15%、单个杂质≤0.05%,合计≤0.15%,余量为Al。 以上具有较高镁含量的5383合金,在不添加昂贵的稀土元素如钪、铒等的前提下, 通过加入工业上常用的锰和锆元素,通过合理的工艺设计,有效抑制材料在热加工过程中 的回复及再结晶,挤出后强度高,同时却在成本上远低于稀土元素;因此,本发明的5383铝 合金具有结构强度高、耐腐蚀能力和可加工成型性能好的优点,兼顾了力学性能、抗腐蚀性 能和生产成本,实现综合性能的进一步提高。 作为优选,铝合金的成分和重量百分比为:Si≤0.15%、Fe≤0.2%、Cu≤0.12%、 Mn:0.8~0.95%、Mg:4.4~4.8%、Cr≤0.1%、Zn≤0.35%、Ti≤0.05%、Zr:0.07~0.15%、 单个杂质≤0.05%,合计≤0.15%,余量为Al。以上5383铝合金,具有更高的结构强度、耐腐 蚀能力和可加工成型性能。 一种船用型材制备工艺,其特征在于,按照以下步骤进行: A、配料:按照权利要求1或2中所述的5383铝合金的成分和重量百分比进行配料; B、铸造:将配制好的5383铝合金原料加入到熔炼炉中熔炼为液态铝合金,再将液 态铝合金熔铸为5383铝合金铸锭; C、均质:将5383铝合金铸锭进行均质化处理,均质化处理后冷却; D、挤压成型:将均质化处理后的5383铝合金铸锭置于挤压机的挤压筒中进行挤 压,得到船用型材; E、拉伸:将挤压得到的船用型材置于拉直机中进行拉伸; F、定尺锯切:对船用型材进行锯切; G、稳定化退火:对船用型材进行退火处理。 采用以上方法,工艺简单,生产出来的型材不仅尺寸可控,不良率低,使型材具有 4 CN 111549264 A 说 明 书 3/8 页 更高的尺寸精度,而且屈服强度能够达到220MPa以上,相对于现有的5383铝合金型材提升 了10%以上,大幅提高了型材的强度,同时生产效率高,材料的抗腐蚀能力强,获得了一种 高强耐腐蚀的船用高强铝合金挤压型材。 作为优选,步骤C中,所述均质化处理采用双级均热,第一级均热温度为400~420 ℃,保温时间10h,第二级均热温度为505~515℃,保温时间18h。采用以上方法,能够保证 Mn、Zr等元素以细小的第二相形式充分弥散的析出,进一步提升后续得到的船用型材的力 学性能。 作为优选,步骤C中,第二级均热保温完成后采用风冷冷却。采用以上方法,能够保 证均质化处理效果,同时降低冷却时的冷却应力,获得具有较好直线度的圆铸锭,确保后续 挤压过程不因铸棒弯曲造成产品气泡等表面缺陷。 作为优选,步骤D中,将5383铝合金铸锭挤压为船用型材的挤压比为10~60,以得 到高强度型材。 作为优选,步骤D中,型材的出口温度控制在560℃以下。采用以上方法,能够避免 局部熔化而发生在拉应力作用下裂纹被放大(拉裂)的情况。 作为优选,步骤E中,拉伸率为0.5~4%。采用以上方法,冷加工拉伸率较低,使型 材尺寸更可控。 作为优选,步骤B中,将液态铝合金采用半连续水冷铸造方式熔铸为呈圆棒形结构 的5383铝合金铸锭。采用以上方法,冷却速度快,Mn、Zr等合金元素能在铸造过程中充分固 溶到铝合金基体中,不会在冷却过程中因冷却速度过慢发生析出长大,形成了Mn、Zr元素充 分固溶的过饱和固溶体,为后续步骤C中均匀化热处理过程中均匀、弥散地析出含Mn、Zr等 第二相粒子创造充分条件。 作为优选,步骤G中,在150~200℃的温度范围内对船用型材进行1~4小时的稳定 化退火。采用以上方法,能够大幅提升型材的抗腐蚀能力。 与现有技术相比,本发明的有益效果: 采用以上技术方案的一种高强度耐腐蚀的5383铝合金及船用型材制备工艺,5383 铝合金在不添加昂贵的稀土元素如钪、铒等的前提下,通过加入工业上常用的锰和锆元素, 通过合理的工艺设计,有效抑制材料在热加工过程中的回复及再结晶,挤出后强度高,同时 却在成本上远低于稀土元素;因此,本发明的5383铝合金具有结构强度高、耐腐蚀能力和可 加工成型性能好的优点,兼顾了力学性能、抗腐蚀性能和生产成本;并且,制备工艺简单,生 产出来的型材不仅尺寸可控,不良率低,使型材具有更高的尺寸精度,而且屈服强度能够达 到220MPa以上,相对于现有的5383铝合金型材提升了10%以上,大幅提高了型材的强度,同 时生产效率高,材料的抗腐蚀能力强,获得了一种高强耐腐蚀的船用高强铝合金挤压型材。 附图说明 图1为船用型材制备工艺的流程图; 图2为出口温度在560℃以上时,型材出现拉裂的示意图; 图3为实施例1(挤压比60)制得的船用型材; 图4为实施例6(挤压比10)制得的船用型材; 图5为表2的柱状图。 5 CN 111549264 A 说 明 书 4/8 页