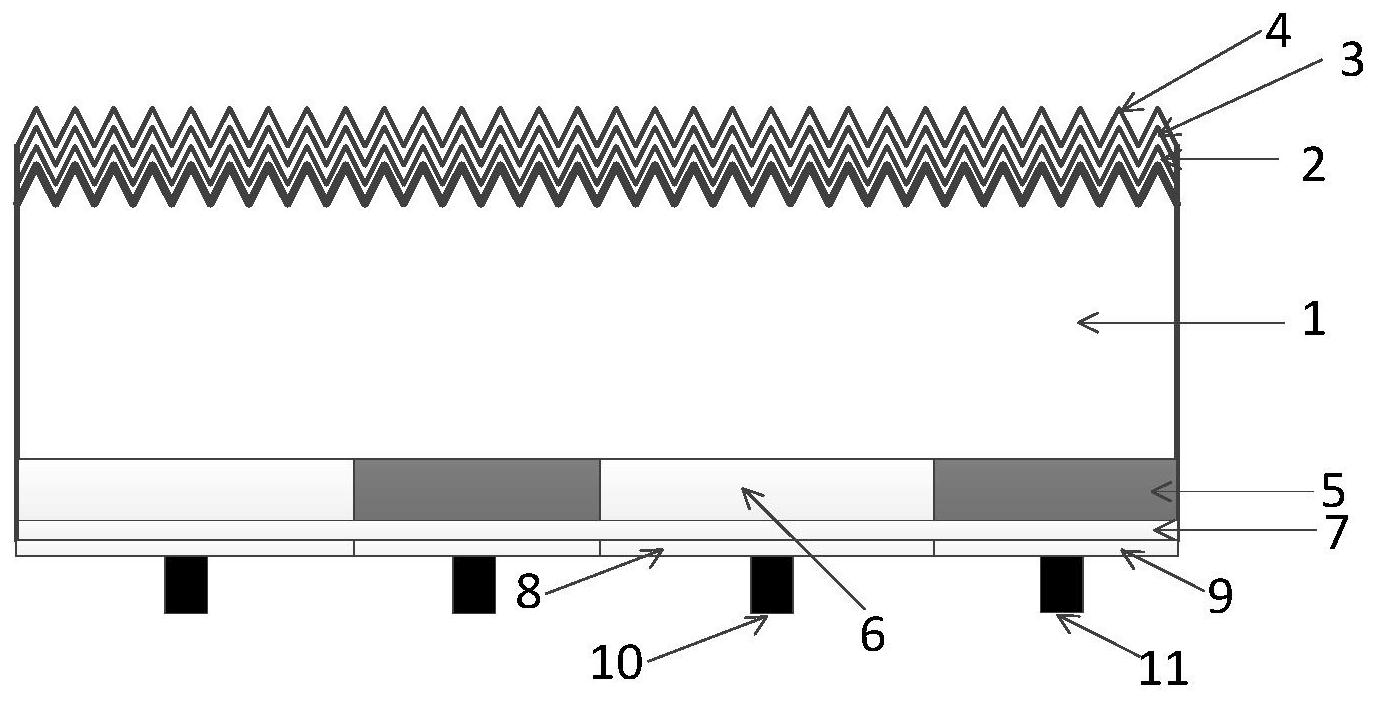
技术摘要:
本专利提供了一种叉指型背接触太阳电池结构及其制造方法,包括N型单晶硅片为基体,所述单晶硅片前表面设置有硼掺杂层,所述单晶硅片前表面硼掺杂层上设置有AL2O3钝化层,在所述单晶硅片前表面AL2O3钝化层上设置有SiNx减反射层;所述单晶硅片背表面场为磷掺杂层,所述单 全部
背景技术:
太阳能是一种清洁的可再生的能源,取之不尽,用之不竭。开发和利用太阳能,对 环境的污染小,能为人类提供充足的能量,亦不会影响自然界的生态平衡,相对于其他新能 源如风能、地热能、生物能和潮汐能等,太阳能以可利用率高、资源分布广泛和使用安全可 靠等诸多优点,成为最具有发展前景的能源之一。 目前硅太阳电池是发展最成熟的,也占据市场的主导地位。现今单晶硅太阳电池 因材料纯度较高,晶体缺陷密度低,可用于高效太阳能电池的研究和试制,能获得较高的转 换效率,技术也最为成熟,而且也取得了很好的应用,N型IBC(Interdigitated Back Contact)太阳电池以n型单晶硅为衬底,p-n结和金属电极全部以叉指形状置于电池背面, 正面没有电极遮光,并且通过表面制绒和增加减反射层来提高电池对光的吸收,获得了非 常高的短路电流和光电转换效率。 对于背接触太阳电池,由于P 和N 掺杂区域均放置在电池背面,当前表面采用前 表面场钝化(FSF)时,这种结构对电池背面P区和N区的尺寸比例要求较高,P区应适当宽一 点,而N区应尽可能的窄,N区越窄,工艺难度越大。并且对于不同类型的掺杂层,其表面的钝 化方式也不同。 因此,本发明的主要目的在于解决电池背表面场宽度较窄导致的工艺难度增加以 及电池背面复合较大等问题。
技术实现要素:
本发明提供了一种叉指型背接触太阳电池结构及其制造方法,解决了降低工艺难 度,并且对于不同类型的掺杂层,根据钝化材料所带电荷的正负性对电池背面进行钝化可 改善背面的钝化性能,提高电池效率。 一种叉指型背接触太阳电池结构,包括N型单晶硅片为基体,所述单晶硅片前表面 设置有硼掺杂层,所述单晶硅片前表面硼掺杂层上设置有AL2O3钝化层,在所述单晶硅片前 表面AL2O3钝化层上设置有SiNx减反射层;所述单晶硅片背表面场为磷掺杂层,所述单晶硅 片背面发射极为硼掺杂层,所述单晶硅片背表面设置有SiO2钝化层,所述单晶硅片背面发 射极表面设置有AL2O3钝化层,所述单晶硅片背面场表面设置有SiNx钝化层,所述单晶硅片 背面发射极连接有负电级,所述单晶硅片背面场连接有正电极。 优选的,所述N型单晶硅片基体的电阻率为1-10Ω·cm。 优选的,所述单晶硅片前表面硼掺杂层的方阻为80-160Ω·cm,结深为0.1-0.5μ m。 优选的,所述单晶硅片前表面AL2O3钝化层膜厚为1-10nm。 优选的,所述单晶硅片前表面SiNx减反射层膜厚为40-80nm,折射率为1.8-2.5。 4 CN 111613688 A 说 明 书 2/4 页 优选的,所述单晶硅片背表面场磷掺杂层的方阻为80-160Ω·cm,结深为0.1-0.5 μm。 优选的,所述单晶硅片背表面SiO2钝化层厚度为1-5nm。 优选的,所述单晶硅片背面发射极表面AL2O3钝化层膜厚为1-10nm。 优选的,所述单晶硅片背面场表面SiNx钝化层膜厚为40-80nm。 优选的,所述负电级宽度为300-1600μm。 优选的,所述正电极宽度为100-700μm。 一种叉指型背接触太阳电池的制造方法, S1、选择N型单晶硅片作为基体,并进行双面制绒处理; S2、对N型单晶硅片进行双面硼扩散; S3、在N型单晶硅片双面沉积AL2O3薄膜; S4、对N型单晶硅片背表面N型BSF区域进行开槽; S5、对N型单晶硅片进行单面磷扩散形成N型单晶硅片背表面场; S6、在N型单晶硅片正反面沉积氮化硅膜; S7、对硅片进行丝网印刷银浆和铝浆形成正负电极; S8、进行烧结,最终得到IBC电池。 优选的,S1中所述N型单晶硅片基体的厚度为140-180μm,电阻率为1-10Ω·cm。 优选的,S2使用低压高温扩散炉对所述N型单晶硅片进行双面硼扩散,扩散温度为 800-1100℃,扩散时间为10-50分钟,扩散后P 掺杂层的方块电阻为80-160Ω·cm,结深为 0.1-0.5μm。 优选的,S3使用ALD设备在所述N型单晶硅片双面沉积AL2O3薄膜,薄膜厚度为1- 10nm。 优选的,S4使用激光开槽设备对所述N型单晶硅片背表面N型BSF区域进行开槽。 优选的,S5使用掩膜工艺在激光开槽区域使用低压高温扩散炉对所述N型单晶硅 片进行单面磷扩散形成背表面场,扩散温度为800-1100℃,扩散时间为10-50分钟,扩散后N 掺杂层的方块电阻为80-160Ω·cm,结深为0.1-0.5μm。 优选的,S6使用PECVD设备在硅片正反面沉积氮化硅膜,膜厚为40-80nm,折射率为 1.8-2.5。 优选的,S8为放入烧结炉进行烧结,烧结温度为700-1000℃。 本发明与现有技术相比存在以下优点和积极效果: 1、电池前表面采用FFE浮动结结构在有效降低表面载流子复合的同时可提供背表 面场的宽度比例,降低工艺难度。 2、针对不同类型的表面掺杂,选择不同的钝化材料进行表面钝化可有效降低电池 正反面少子复合率。 具体通过在电池前表面采用硼掺杂形成浮动(FFE)结构,这种结构可为光生少子 提供横向传输路径,降低前表面少子复合率;该结构对电池背表面场所占的尺寸比例要求 较低,可使得背表面场所占比例接近50%;同时,由于电池正面为P型掺杂,采用三氧化二铝 (Al2O3)和二氧化硅做表面钝化可有效提升钝化性能,电池背面P区表面同样采用二氧化硅 (SiO2)和三氧化二铝(Al2O3)做钝化,N区则采用二氧化硅(SiO2)和氮化硅(SiNx)做钝化, 5 CN 111613688 A 说 明 书 3/4 页 以这种钝化方式可有效降低电池正反面的少子复合率,进而提升电池转换效率。 附图说明 图1为叉指型背接触太阳电池示意图。 其中:N型单晶硅基体1;前表面P 掺杂层2;前表面三氧化二铝(Al2O3)钝化层3;氮 化硅减反射层4;N 掺杂层5;P 掺杂层6;二氧化硅层7;背表面三氧化二铝(Al2O3)钝化层8; 背表面氮化硅(SiNx)钝化层9;正电极10;负电极11。