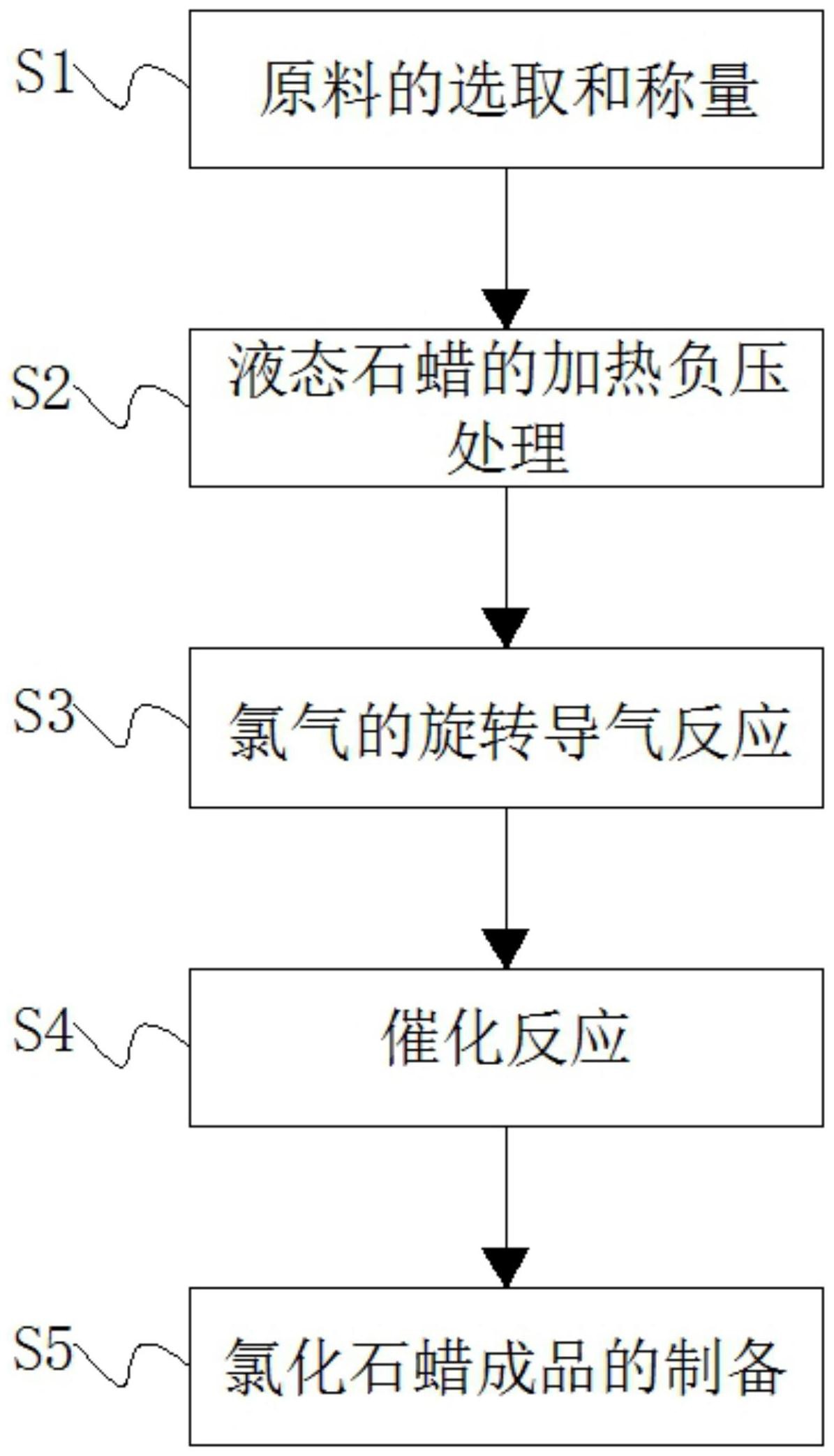
技术摘要:
本发明公开了一种可提高原料资源利用率的氯化石蜡生产工艺,具体包括以下步骤:S1、原料的选取和称量,S2、液态石蜡的加热负压处理,S3、氯气的旋转导气反应,S4、催化反应,S5、氯化石蜡成品的制备,本发明涉及石蜡生产技术领域。该可提高原料资源利用率的氯化石蜡生 全部
背景技术:
氯化石蜡是石蜡烃的氯化衍生物,具有低挥发性、阻燃、电绝缘性良好、价廉等优 点,可用作阻燃剂和聚氯乙烯辅助增塑剂,广泛用于生产电缆料、地板料、软管、人造革、橡 胶等制品,以及应用于聚氨酯防水涂料、聚氨酯塑胶跑道,润滑油,等的添加剂,适用于各类 产品阻燃之用,广泛应用在塑料、橡胶、纤维等工业领域作增塑剂,织物和包装材料的表面 处理剂,粘接材料和涂料的改良剂,高压润滑和金属切削加工的抗磨剂,防霉剂、防水剂,油 墨添加剂。 传统的固体氯化石蜡生产工艺分为悬浮法与溶剂法两种,但悬浮法存在的不足之 处是产品含水难于除尽,溶解性及热稳定性较溶剂法逊色,溶剂法通常进行二级间断氯化 反应,将溶融的石蜡在95-105℃下预氯化至含氯量40%左右.再加入0.5-6倍量的CCl4溶 剂,压力常压至6kgf/cm2,温度70-120℃,反应时间12-30小时,氯化物料水洗至pH6.5-7再 用碱中和pH7-7 .5,即可通过直接蒸气精制,汽提出来的CCl4经冷凝分离干燥后供循环使 用,脱溶剂后的物料经冷却、研磨、干燥、过筛最终取得成品。 目前的氯化石蜡在生产过程中,原料资源利用率较低,氯气与石蜡反应较慢,且反 应不充分,从而导致反应结束后仍然有较多的氯气残留在反应釜中为反应,若直接排除会 污染环境,因此需要花费大量的生产成本对残余氯气进行回收处理,不能实现通过对氯化 石蜡的生产方法进行改进,来使氯气与石蜡进行充分反应,降低氯气的残余量,无法达到通 过负压条件下进行反应,来提高原料资源的利用率的目的,从而给生产人员的氯化石蜡生 产带来极大的不便。
技术实现要素:
(一)解决的技术问题 针对现有技术的不足,本发明提供了一种可提高原料资源利用率的氯化石蜡生产 工艺,解决了现有的原料资源利用率较低,氯气与石蜡反应较慢,且反应不充分,从而导致 反应结束后仍然有较多的氯气残留在反应釜中为反应,若直接排除会污染环境,因此需要 花费大量的生产成本对残余氯气进行回收处理,不能实现通过对氯化石蜡的生产方法进行 改进,来使氯气与石蜡进行充分反应,降低氯气的残余量,无法达到通过负压条件下进行反 应,来提高原料资源的利用率目的的问题。 (二)技术方案 为实现以上目的,本发明通过以下技术方案予以实现:一种可提高原料资源利用 率的氯化石蜡生产工艺,具体包括以下步骤: S1、原料的选取和称量:首先通过称量设备分别量取所需重量的液态石蜡、高活性 3 CN 111592913 A 说 明 书 2/5 页 催化剂、稳定剂和氯化亚砜溶剂和PH调节剂,并将量取的各组分通过存储罐进行保存,备 用; S2、液态石蜡的加热负压处理:将步骤S1量取的液态石蜡倒入反应釜中,首先启动 加热设备,将反应釜加热至60-80℃,保持温度10-15min,同时启动反应釜内部的搅拌设备, 带动搅拌叶片旋转对液态石蜡进行缓慢搅拌,搅拌完成后,盖好反应釜顶盖,并进行很好的 密封处理,然后启动抽气泵,将反应釜内液态石蜡顶部的空气抽出,使反应釜内呈负压状 态: S3、氯气的旋转导气反应:将外部储备有氯气的储气罐通过导气管连接反应釜顶 部的搅拌导气设备的进气管,然后启动气泵将储气罐中的氯气通过泵入反应釜中,此时启 动搅拌导气设备,使搅拌头进行旋转,从而实现将氯气旋转的通入液态石蜡中,使氯气与石 蜡进行充分接触反应; S4、催化反应:将步骤S1量取的高活性催化剂通过反应釜上安装的滴加设备加入 到步骤S3的反应釜中,此时启动搅拌设备以300-400r/min的转速搅拌10-15min,使氯气和 石蜡进行充分反应; S5、氯化石蜡成品的制备:将步骤S1量取的氯化亚砜溶剂以转速为500-600r/min 搅拌1-2h,然后回流5-7h后,常压回收过量的氯化亚砜,之后将步骤S1量取的PH调节剂加入 到反应釜中,搅拌30-40min进行PH的调节,然后再加入稳定剂,再次搅拌20-30min,最后洗 涤减压脱水至含水量小于2%,出料为成品。 优选的,所述步骤S3中搅拌导气设备包括中空旋转轴、搅拌头和进气管,中空旋转 轴的顶端进气管的一端通过管道连接件进行固定连接,并且使进气管与中空旋转轴内的导 气孔连通,而中空旋转轴的底端贯穿反应釜顶盖延伸至反应釜的釜底,并且与搅拌头固定 连接,搅拌头也为中空,其外表面开设有到排气孔。 优选的,所述步骤S1中称取2.5-3.8L的液态石蜡、8-15mL的高活性催化剂、3-5mL 的稳定剂和1-3mL的氯化亚砜溶剂和1-3mL的PH调节剂。 优选的,所述步骤S2中抽气泵的是选用RA0250D型号的离心泵。 优选的,所述步骤S3中通入氯气的体积为15-25mL。 优选的,所述步骤S1中高活性催化剂为过氧化铝、过氧化氢或过氧酸钠中的一种 或多种的组合。 (三)有益效果 本发明提供了一种可提高原料资源利用率的氯化石蜡生产工艺。与现有技术相比 具备以下有益效果:该可提高原料资源利用率的氯化石蜡生产工艺,具体包括以下步骤: S1、原料的选取和称量:首先通过称量设备分别量取所需重量的液态石蜡、高活性催化剂、 稳定剂和氯化亚砜溶剂和PH调节剂,并将量取的各组分通过存储罐进行保存,备用,S2、液 态石蜡的加热负压处理:将步骤S1量取的液态石蜡倒入反应釜中,首先启动加热设备,将反 应釜加热至60-80℃,保持温度10-15min,S3、氯气的旋转导气反应:将外部储备有氯气的储 气罐通过导气管连接反应釜顶部的搅拌导气设备的进气管,然后启动气泵将储气罐中的氯 气通过泵入反应釜中,S4、催化反应:将步骤S1量取的高活性催化剂通过反应釜上安装的滴 加设备加入到步骤S3的反应釜中,此时启动搅拌设备以300-400r/min的转速搅拌10- 15min,使氯气和石蜡进行充分反应,S5、氯化石蜡成品的制备:将步骤S1量取的氯化亚砜溶 4 CN 111592913 A 说 明 书 3/5 页 剂以转速为500-600r/min搅拌1-2h,然后回流5-7h后,常压回收过量的氯化亚砜,之后将步 骤S1量取的PH调节剂加入到反应釜中,搅拌30-40min进行PH的调节,然后再加入稳定剂,再 次搅拌20-30min,最后洗涤减压脱水至含水量小于2%,出料为成品,可实现通过对氯化石 蜡的生产方法进行改进,来使氯气与石蜡进行充分反应,降低氯气的残余量,很好的达到了 通过负压条件下进行反应,来提高原料资源的利用率的目的,很好的加快了氯气与石蜡的 反应速度,使反应更加充分,避免了反应结束后仍然有较多的氯气残留在反应釜中为反应, 无需花费大量的生产成本对残余氯气进行回收处理,从而大大方便了给生产人员的氯化石 蜡生产。 附图说明 图1为本发明的流程图。