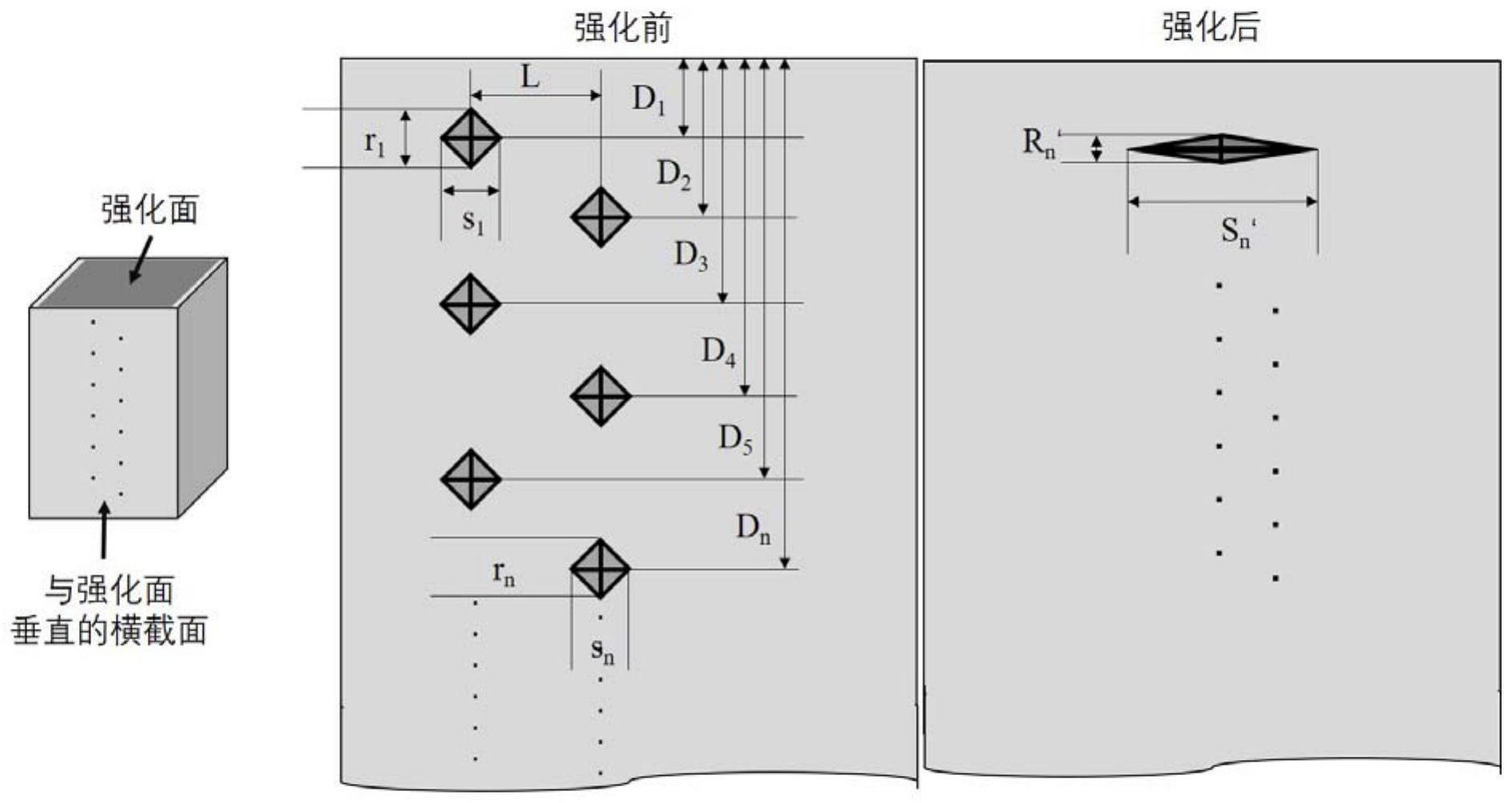
技术摘要:
本发明属于零件表面处理技术,涉及一种表面强化层塑性变形量和深度的评估方法;本发明利用显微硬度计在试块的横截面预制凹坑整列,当对待强化表面进行表面强化后,近表层发生压缩,凹坑也相应地发生塑性变形,通过计算凹坑的变形程度获得该深度处的塑性变形量。并设定 全部
背景技术:
表面强化是基于塑性形变强化理论,通过在金属表面引入塑性变形,形成组织强 化层和残余压应力层,从而提高金属的疲劳性能、耐磨损和抗应力腐蚀性能。目前的主要表 面强化技术包括喷丸、激光冲击、孔挤压、超声冲击、滚压、双相流。通过硬质介质或高压冲 击波等作用于金属表面,在材料表层增殖位错,产生应变硬化,形成高幅值的残余压应力。 在工程应用中,批产前工艺参数需进行筛选、优化和固化,需要对强化效果进行评 估,其中,表面组织变形层是影响强化效果的重要因素。表面强化会在金属表面层形成一定 深度的压缩区,组织内部形成高密度的位错,因而不同深度处的塑性变形量和塑性变形层 深度可作为表面强化效果的判别依据之一。而在批产的工艺质量检查中,采用随炉试片进 行监控,分析试片的表层塑性变形量和塑性变形层深度,也是评估工艺稳定性的重要手段。 目前,评估表面强化层塑性变形量和深度的主要实验方法是通过金相观察方法, 通过扫描电镜、金相显微镜或EBSD等手段分析不同深度处的晶粒或相的变形程度,并由此 方法确定变形层的深度。但是,由于金属内部晶粒尺寸存在一定的差异性,该方法在分析变 形程度的误差较大;另外,由于强化层的变形程度随深度逐渐递减,和未变形的基体无明显 的界面层,因此,在判定变形层深度时,误差也较大。
技术实现要素:
本发明的目的是:提出了一种表面强化层塑性变形量和深度的评估方法,可解决 表面强化层塑性变形量和深度难以评估的难题,为表面强化效果提供了一种随炉试片检验 手段,满足表面强化批产前工艺参数固化和批产中工艺质量检查的需求。 本发明的技术方案是: 一种表面强化层塑性变形量和深度的评估方法,采用随炉试块,利用显微硬度计 在与待强化面相垂直的横截面上预制n个凹坑,通过分析强化前后n个凹坑的变形程度来评 估不同深度处的塑性变形量,并设定变形量阈值,评估强化层的深度。其特征在于: (1)所述凹坑上表面的两条对角线长度分别为r和s,其中长度为r的对角线与待强 化面垂直,凹坑中心距待强化面的距离分别为D1、D2、D3、D4、D5、……、Dn; (2)将横截面进行遮蔽处理,将随炉试块放入强化处理设备内,对待强化面进行表 面强化处理,强化后去除遮蔽物; (3)采用扫描电子显微镜观察横截面上凹坑,分别获得不同深度处的凹坑的两条 对角线长度Rn和Sn,并通过如下公式计算凹坑变形量ε(Dn): ε(Dn)=[(1-Rn/rn) (1-sn/Sn)]/2×100% 该变形量即为表面强化层在深度Dn处的塑性变形量; 3 CN 111593174 A 说 明 书 2/3 页 (4)当某一深度Dn处的凹坑的变形量ε(Dn)≤10%且上一个凹坑的ε(Dn-1)>10%时, 则认为强化层深度D=(Dn Dn-1)/2。 所述凹坑的形状为方形或长方形。 所述凹坑交错排列。 所述凹坑中心距待强化面的距离为Dn。 所述表面强化处理为喷丸、激光冲击、孔挤压、超声冲击、滚压、双相流中的一种。 所述随炉试块表面强化前,先将随炉试块待强化面相垂直的横截面进行抛光。 所述凹坑最小间距不小于凹坑尺寸的2倍。 所述观察横截面上凹坑采用光学电镜观察。 本发明的优点是: 其一,本方法通过对比表面强化前后的凹坑尺寸变化量,计算塑性变形量,相比传 统的金相法,测试精度和准确度更高。 其二,本方法采用随炉试块的方式进行评估,简单方便,不会伤及真实零件,工程 应用价值较高。 第三,本方法可以通过调节凹坑到待强化表面的距离和交错排列,可以获得近表 面大范围深度内的塑性变形量,准确高效。 附图说明 图1为随炉试块凹坑设置及强化前后示意图 图2为喷丸强化后凹坑对角线长度Rn随深度Dn的变化规律图 图3为喷丸强化后凹坑对角线长度Sn随深度Dn的变化规律图 图4为喷丸强化后凹坑变形量ε(Dn)随深度Dn的变化规律图