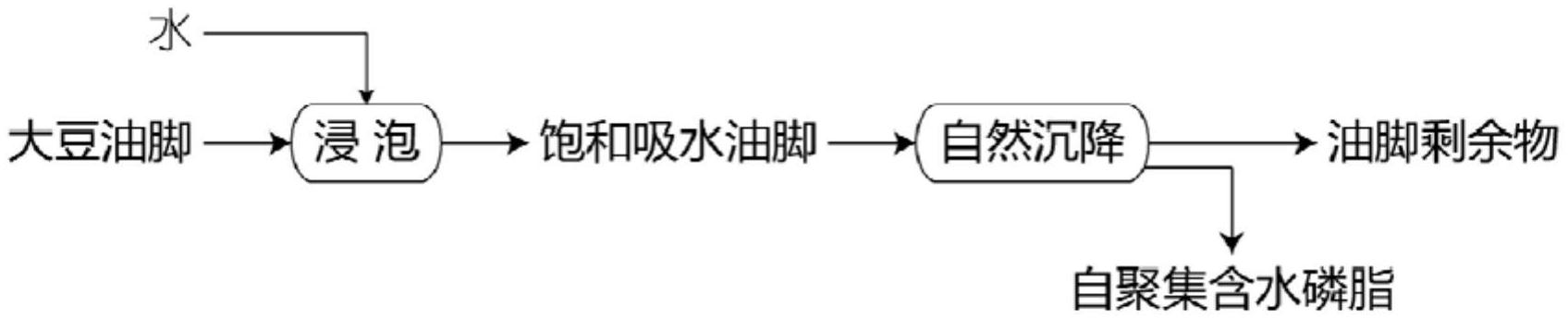
技术摘要:
本发明属于磷脂加工技术领域,具体涉及一种从大豆油脚中分离自聚集含水磷脂的方法。所述方法包括如下步骤:取大豆油脚在水中浸泡,得到饱和吸水油脚,自然沉降,即得;所述大豆油脚与水的质量比为1:1‑3.5。本发明解决了现有方法制备的含水磷脂的丙酮不溶物含量不高、 全部
背景技术:
磷脂加工的原料是大豆油脚,简称油脚,是油脂加工领域的大豆油脂精炼过程中 水化脱胶工艺的副产物,也称为水化油脚,其主要成分是磷脂30-45g/100g、大豆油20-30g/ 100g和水分30-50g/100g,微量成分是金属离子,如钙、镁和铁等,以磷脂金属盐的形式存 在,如铁离子含量,以丙酮不溶物计通常为50-100mg/kg,个别情况高达150mg/kg以上。 工业化的磷脂加工方法主要有两种,一是水化法制备浓缩磷脂,即从大豆毛油中 水化提取大豆油脚后,直接干燥脱水得到浓缩磷脂,因其具有流动性也称为流体磷脂,其干 基丙酮不溶物含量为60-65g/100g;二是溶剂法制备粉末磷脂,即以大豆油脚或者浓缩磷脂 为原料,用丙酮萃取除去油脂,得到粉末磷脂,其干基丙酮不溶物含量为95-98g/100g。目前 市场上主流产品是浓缩磷脂,粉末磷脂在市场中占比不足5%。 虽然大豆油脚绝大多数被加工成浓缩磷脂,但浓缩磷脂有很大缺陷。例如文献《大 豆浓缩磷脂生产工艺》(胡兴中.大豆浓缩磷脂生产工艺[J].中国油脂,2007,32(9):20-21) 和《浓缩磷脂制取工艺与实践》(胡庆涛等.浓缩磷脂制取工艺与实践[J].中国油脂,2002, 27(1):39-40)介绍了以水化油脚为原料进行脱水、氧化漂白生产浓缩磷脂的方法。该工艺 的缺点是浓缩磷脂的丙酮不溶物含量太低(60-65g/100g)、需要化学漂白,市场价格仅为 0.4万元/吨,与粉末磷脂4万元/吨的售价有较大差距。 中国专利CN103665029A公开了一种制备大豆粉末磷脂的方法,该方法采用丙酮作 为溶剂萃取水化油脚,分离出丙酮不溶物,再低温真空干燥丙酮不溶物脱除溶剂,得到粉末 磷脂。该方法的缺点是使用丙酮溶剂,生产成本高,并且存在环境污染和溶剂残留的食品安 全隐患,难以普遍推广,因此不能促进油脂加工领域从浓缩磷脂向粉末磷脂转化的产品结 构升级,也不能改善油脂精炼损耗高的现状。 目前水化法制备磷脂的研究存在诸多缺陷,比如中国专利CN107325125A公开了一 种大豆油脚制备水合磷脂的方法及其制得的水合磷脂(以下简称水合磷脂),该方法包括如 下操作步骤:取大豆油脚加入软化水混合均匀后,静置进行层析;层析结束后控制温度为 85-95℃,进行离心分离得到水合磷脂,其丙酮不溶物能够达到90-92%。该专利存在如下缺 陷: (1)水合磷脂的干基丙酮不溶物含量低:该专利是均质水化方法,即油脚与水要混 合均匀,混合均匀时不可避免地发生乳化,如果乳化严重,磷脂与油脂就很难再分离。为了 避免严重乳化,该专利采取了两个措施,第一、严格控制加水量,加水量是油脚重量的0.25- 0.74倍;第二,加入氢氧化钠或者硫酸,用作破乳剂。上述措施带来的问题是大豆油脚中的 主要成分磷脂、油脂和磷脂金属盐没有得到有效分离,水合磷脂的干基丙酮不溶物含量最 高仅达到92%,与溶剂法丙酮不溶物95-98%相比,尚有一定的差距; 3 CN 111548365 A 说 明 书 2/10 页 (2)水合磷脂未能彻底干燥,缺乏工业用途:该水合磷脂通过浓缩脱水、添加防腐 剂、巴氏杀菌和包装得到了一种含水量为22.5-41.2%的含水磷脂产品,但是这种含水磷脂 产品不符合国家标准《GB28401食品添加剂磷脂》关于水分不得超过2%的规定,不能销售; 如果按照现有的制备粉末磷脂的方法进行干燥,则时间太长、产能太低,没有工业化生产的 可行性,既不能销售也不能进一步加工导致其缺乏工业用途。 另一种水化法提取磷脂的现有技术,如文献《液晶态分离提纯大豆磷脂的研究》 (李子明等.液晶态分离提纯大豆磷脂的研究[J].中国粮油学报,2007,22(1):31-32),以下 简称液晶态磷脂。该文献方法存在以下技术缺陷:(1)液晶态磷脂的干基丙酮不溶物含量较 低:采用均质水化方法,加水量是0.67倍油脚,得到的液晶态磷脂的干基丙酮不溶物含量仅 为86.05%,这与水合磷脂的缺陷相同;(2)缺乏工业用途:液晶态磷脂的干燥问题与水合磷 脂相同,虽然液晶态磷脂用间歇式真空干燥方式得到了粉末磷脂,但是干燥时间太长,磷脂 产品的色泽较深(棕色),无法应用于工业化生产。 中国专利CN102517148A公开了一种磷脂两步脱色方法,采用过氧化氢漂白和硅胶 吸附的两步脱色方法,该方法的缺点是:(1)化学漂白脱色,使磷脂产生氧化副产物、破坏磷 脂的天然性,同时存在食品安全风险,不符合“绿色”发展的大趋势;(2)硅胶吸附脱色的效 果很差,失效的硅胶成为废渣,不利于环保;(3)漂白破坏了磷脂中有益的抗氧化成分,使磷 脂的抗氧化性、营养价值降低,缩短了磷脂的保质期。 在磷脂加工领域,从产品的角度看粉末磷脂替代浓缩磷脂是未来的方向,从方法 的角度看水化法替代溶剂法是未来的方向,虽然目前已有一些水化法的研究,但是水化法 制备得到的磷脂的纯度仍不够高、色泽改善仍未脱离化学漂白的方法、水化法的脱水效率 仍未达到工业化的水平、工艺技术在完整性和连续化方面尚有不足。 因此,开发一种从大豆油脚中分离自聚集含水磷脂的方法,以解决上述技术问题 是非常必要的。
技术实现要素:
本发明的第一个目的在于提供一种从大豆油脚中分离自聚集含水磷脂的方法。本 发明用以解决现有方法制备的含水磷脂的丙酮不溶物含量不高、以及行业长期依赖溶剂法 制备粉末磷脂的缺陷,用以解决水化法粉末磷脂无法实现工业化生产的技术难题。本发明 制备的自聚集含水磷脂的用途是制备水化法粉末磷脂,丙酮不溶物含量高达92.5-95.5g/ 100g,色泽为自然黄色,不漂白、无溶剂,可以取代溶剂法粉末磷脂,避免溶剂法粉末磷脂带 来的环境污染和食品安全隐患,并且水化法粉末磷脂的生产成本远低于溶剂法。所述从大 豆油脚中分离自聚集含水磷脂的方法,在磷脂加工领域和相关研究中均未见报道。 本发明的第二个目的在于提供了上述方法制备得到的自聚集含水磷脂在制备粉 末磷脂中的应用。 本发明是通过以下技术方案予以实现的: 一种从大豆油脚中分离自聚集含水磷脂的方法,包括如下步骤: 将大豆油脚在水中浸泡,得到饱和吸水油脚,自然沉降,即得;所述大豆油脚与水 的质量比为1:1-3.5。 所述自聚集含水磷脂是指大豆油脚中的磷脂与水自发结合、自发聚集形成的聚集 4 CN 111548365 A 说 明 书 3/10 页 体。 所述的浸泡,是指大豆油脚在水中是分散相,而水是连续相,构成了一种浸泡体 系。 所述浸泡的结果,是得到饱和吸水油脚。在浸泡结束时,饱和吸水油脚中的磷脂吸 水量达到饱和,即磷脂含水量达到70-80g/100g。 优选地,所述大豆油脚与水的质量比为1:1-3.5。 当水少于油脚重量的1.0倍时,大豆油脚无法在水中实现有效浸泡,进而影响磷脂 与水的结合。当水多于油脚质量的3.5倍时,虽然有利于大豆油脚的浸泡,但增加了水的成 本、能源消耗和增加了设备的体积。 优选地,所述浸泡的温度为60-95℃。 在0℃到100℃的水中,磷脂与水都可以发生结合,温度越高结合的效率越高。因 此,提高水温,可以缩短浸泡时间。但是在沸水中,不利于自聚集含水磷脂的稳定,并且水的 沸腾蒸发也浪费能源。因此所述浸泡的温度优选为60-95℃。当温度在60℃以上时属于杀菌 温度,可以防止浸泡期间油脚发生变质,而小于95℃可防止水发生沸腾。 优选地,所述浸泡的时间为1-3h。 所述浸泡时间,是指得到饱和吸水油脚所需的时间,此时油脚中的磷脂吸水量达 到饱和。浸泡时间,从大豆油脚呈颗粒状在水中静置浸泡开始,到大豆油脚中开始出现棕色 自聚集含水磷脂为止。浸泡中的大豆油脚为黄色,而出现的自聚集含水磷脂是棕色,因此可 以目测判断浸泡是否达到结束时间。 优选地,所述自然沉降的时间为3-8h。 所述自然沉降的结果,是得到自聚集含水磷脂。在自然沉降结束时,从饱和吸水油 脚得到自聚集含水磷脂和油脚剩余物两种组份。 优选地,所述浸泡为静置浸泡。 浸泡期间,不宜有搅拌操作,以防止出现乳化现象。 优选地,在所述浸泡之前,所述大豆油脚以搅拌的方式在水中打散成为颗粒状。 优选地,所述大豆油脚颗粒的粒径≤5mm。 更优选地,所述大豆油脚颗粒的粒径为0.3-3mm。 大豆油脚粒径越小,油脚与水的接触面积越大,越有利于提高大豆油脚中磷脂与 水的传质与传热效率。但是,大豆油脚粒径太小,存在大豆油脚与水被混合均匀、出现均质 化的风险,破坏了浸泡体系。 优选地,所述方法还包括在所述浸泡体系中添加电解质。 更优选地,所述电解质在水中的质量分数为0.01-0.3%。 适量的电解质有利于大豆油脚中磷脂与水的结合,电解质过多时会抑制磷脂与水 的结合,太少或者不添加电解质,则自聚集含水磷脂的含水量偏高,造成脱水时的能源浪 费。 更优选地,所述电解质包括酸、碱和盐中的至少一种。 更优选地,所述电解质为DL-苹果酸钠、L-苹果酸、DL-苹果酸、冰乙酸、柠檬酸、柠 檬酸钾、柠檬酸钠、柠檬酸一钠、葡萄糖酸钠、乳酸、乳酸钾、乳酸钠、碳酸钾、碳酸钠、碳酸氢 钾、碳酸氢钠、硫酸钠、氯化钾、氢氧化钾、氢氧化钠、盐酸、磷酸和氯化钠中的至少一种。 5 CN 111548365 A 说 明 书 4/10 页 所述自聚集含水磷脂的主要成分是磷脂、油脂和水,含水量为70-80g/100g;以干 基计,丙酮不溶物含量为92.5-95.5g/100g;感官指标为棕色半透明流体。 本发明还涉及上述方法制备得到的自聚集含水磷脂在制备粉末磷脂中的应用。 优选地,采用所述自聚集含水磷脂制备粉末磷脂,包括如下步骤: (1)制备浓缩含水磷脂:将所述自聚集含水磷脂在真空条件下在90-110℃使含水 量浓缩到25-65g/100g,得到浓缩含水磷脂,其干基丙酮不溶物含量为92.5-95.5g/100g,感 官指标为棕色半透明流体。 (2)制备含水磷脂弹性体:将所述浓缩含水磷脂以10-100cm/min的速度推送到搅 拌器中,搅拌转数为800-1200rpm,搅拌时间为5-30s,得到连续输出的含水磷脂弹性体,其 含水量、丙酮不溶物含量与浓缩含水磷脂相同,但感官指标变化为黄色不透明半固体。 所述含水磷脂弹性体,是指该含水磷脂是一种胶体化学范畴的弹性体,其流变学 性质为储能模量G′比损耗模量G″大5-10倍,表现出较强的固体特征(弹性),而液体特征(粘 性)变得较弱,属于弹性体。 (3)制备固体磷脂:将所述连续输出的含水磷脂弹性体通过孔径为2-6mm的进料 口,送入常压或者真空连续干燥机中,在120-160℃干燥6-20min,得到连续输出的条状固体 磷脂,其含水量为3-10g/100g,干基丙酮不溶物含量为92.5-95.5g/100g,感官指标为黄色 条状固体。 (4)制备粉末磷脂:将所述条状固体磷脂粉碎、过筛,在60℃真空干燥30-60min,得 到粉末磷脂,其含水量为≤2g/100g,干基丙酮不溶物含量为92.5-95.5g/100g,感官指标为 黄色粉末,产品执行国家标准《GB28401食品添加剂磷脂》。 步骤(4)所述粉末磷脂的含水量,等同于国家标准《GB28401食品添加剂磷脂》所述 的干燥减量。 所述真空为0.01-0.004MPa。 本发明的有益效果是: 第一、本发明的方法,使自聚集含水磷脂含水量达到了70-80g/100g,磷脂吸水量 达到了饱和:磷脂吸水量达到饱和时,磷脂亲油性降低到最小,即自聚集含水磷脂的油脂含 量最小,且磷脂的纯度最高。从实验数据来看,本申请的自聚集含水磷脂为饱和吸水磷脂, 干基丙酮不溶物含量高达92.5-95.5g/100g,而不饱和吸水磷脂的干基丙酮不溶物含量要 低得多,例如大豆油脚的干基丙酮不溶物含量为60-65g/100g(磷脂含水量为30-50g/ 100g),再如文献公开的液晶态磷脂的干基丙酮不溶物含量为86.05g/100g(磷脂含水量为 64g/100g)。 第二、本发明制备的自聚集含水磷脂,在所有的水化法中,干基丙酮不溶物含量是 最高的:本发明制备的自聚集含水磷脂的干基丙酮不溶物含量为92.5-95.5g/100g,专利公 开的水合磷脂为90-92g/100g,文献报道的液晶态磷脂为86.05g/100g。 第三、本发明是磷脂丙酮不溶物含量与溶剂法最相近的水化法:本发明制备的自 聚集含水磷脂的干基丙酮不溶物含量为92.5-95.5g/100g,接近甚至达到了溶剂法粉末磷 脂95-98g/100g的水平。从行业发展的角度看,水化法最终要替代溶剂法成为主流方法,以 消除有机溶剂造成的环境污染、溶剂残留造成的食品安全隐患和降低生产成本,本发明是 最适合替代溶剂法的水化法。 6 CN 111548365 A 说 明 书 5/10 页 第四、本发明的制备方法,包括自聚集含水磷脂制备方法及其制备水化法粉末磷 脂的应用,具有完整的工艺技术,在品质、保质期、生产成本、环保和食品安全方面都具有很 大优势,适合工业化生产。 本发明优化了水的用量、浸泡体系的分散相油脚颗粒粒径、温度和时间等工艺参 数,使自聚集含水磷脂的含水量达到饱和,使其干基丙酮不溶物含量达到水化法的最高值。 附图说明 图1为大豆油脚浸泡并自然沉降得到自聚集含水磷脂的工艺流程图。 图2为大豆油脚浸泡并自然沉降得到自聚集含水磷脂的工艺示意图。其中: (a)为大豆油脚在水中的示意图; (b)为大豆油脚颗粒是分散相、水是连续相的浸泡体系示意图; (c)为饱和吸水油脚开始出现自然沉降的自聚集含水磷脂的示意图; (d)为饱和吸水油脚经自然沉降得到自聚集含水磷脂的示意图。 图3为自聚集含水磷脂制备固体磷脂的工艺流程图。 图4为浓缩含水磷脂制备固体磷脂的工艺示意图。 图5为应用例1自聚集含水磷脂制备得到的含水磷脂弹性体的储能模量G′与损耗 模量G″的流变学特征图。 图6为应用例2自聚集含水磷脂制备得到的含水磷脂弹性体的储能模量G′与损耗 模量G″的流变学特征图。 其中:(1)是连续相水;(2)是大豆油脚;(3)是分散相大豆油脚颗粒;(4)是饱和吸 水油脚;(5)是自聚集含水磷脂;(6)是油脚剩余物;(7)是浓缩含水磷脂;(8)是含水磷脂弹 性体;(9)是固体磷脂。A是浸泡罐;B是调速齿轮泵;C是管道搅拌器;D是连续式干燥机。