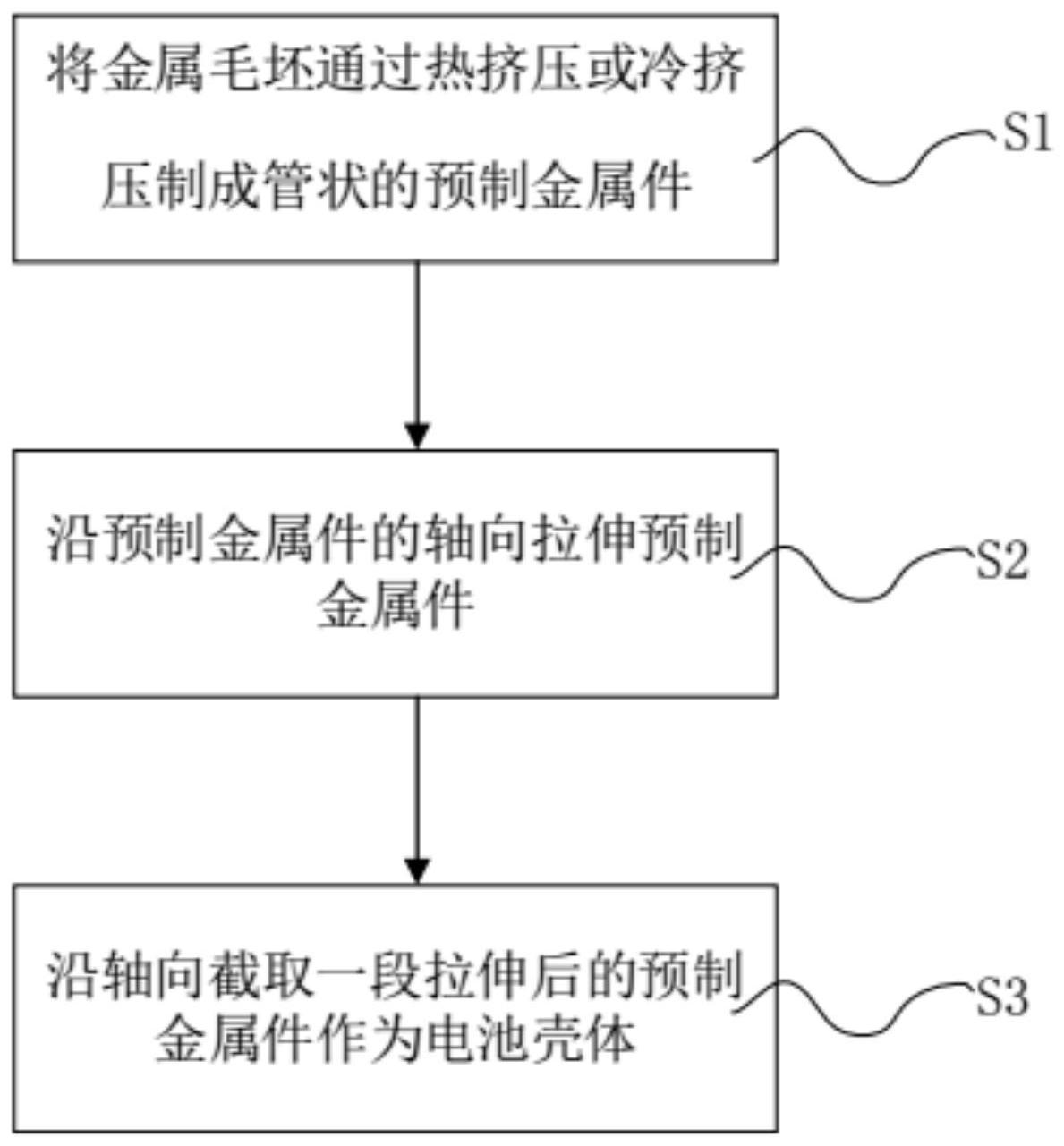
技术摘要:
本发明涉及动力电池技术领域,公开了一种电池壳体的制造方法、电池壳体和单体电池。电池壳体的制造方法包括以下步骤:S1、将金属毛坯通过热挤压或冷挤压制成管状的预制金属件;S2、沿预制金属件的轴向拉伸预制金属件;S3、沿轴向截取一段拉伸后的预制金属件作为电池壳 全部
背景技术:
单体电池的电池壳体上一般设有用于安装电芯的开口,在电池壳体的开口处焊接 盖板组成单体电池。目前,电池壳体大多是薄壁金属板折弯成型后焊接或直接多次冲压成 电池壳体,由于电池壳体的壁厚较薄,电池壳体的制造难度和成本随壳体的长度或深度加 长而成倍增加,且制造效率低下。而且多次冲压易造成金属薄板局部材料缺失,同时搭边废 料也较多,降低了材料利用率,降低了合格率,导致成本增加;金属材料的韧性也限制了冲 压深度,限制了电池壳体的尺寸,从而限制了单体电池的容量,也很难生产出适配于薄片电 池的电池壳体;而且焊接薄壁金属板,易造成焊缝处的开裂,增大了单体电池电解液的漏液 风险。故通过上述方法不易制造出壁厚较薄的且长度或深度较长电池壳体,导致电池壳体 的制造工序增多,难度大,成本高,也降低了单体电池或单体电池组成的电池模组的散热效 率,降低了安全性。 综上,亟需一种电池壳体的制造方法、电池壳体和单体电池用来解决如上提到的 问题。
技术实现要素:
本发明的目的在于提供一种电池壳体的制造方法,提高了电池壳体的合格率和制 造效率,降低了制造壁厚较薄且尺寸较长或较深电池壳体的生产难度,也突破了对于电池 壳体的容量的限制。 为达此目的,本发明采用以下技术方案: 一种电池壳体的制造方法,包括以下步骤: S1、将金属毛坯通过热挤压或冷挤压制成管状的预制金属件; S2、沿所述预制金属件的轴向拉伸所述预制金属件; S3、沿轴向截取一段拉伸后的所述预制金属件作为电池壳体。 优选地,所述步骤S1中,当所述金属毛坯通过热挤压制成管状的所述预制金属件 时,具体包括:加热所述金属毛坯,挤压加热后的所述金属毛坯制成管状的所述预制金属 件。 优选地,所述步骤S1中,当所述金属毛坯通过冷挤压制成管状的所述预制金属件 时,具体包括:冷挤压所述金属毛坯制成管坯,割除所述管坯的多余部分制成管状的所述预 制金属件。 优选地,所述步骤S2具体包括,当拉伸所述预制金属件至其壁厚为预设值时,则停 止拉伸所述预制金属件。 优选地,所述壁厚的所述预设值不小于0.2mm。 3 CN 111740041 A 说 明 书 2/6 页 优选地,所述步骤S3中,在拉伸后的所述预制金属件上截取的长度为 300- 1000mm。 优选地,在步骤S3之后,还包括:S4、清洗并烘干所述电池壳体。 本发明的目的在于提供一种电池壳体,提高了电池壳体的合格率和制造效率,降 低了制造成本,降低了制造壁厚较薄且尺寸较长或较深电池壳体的生产难度,突破了对于 电池壳体的容量的限制,利于生产大容量电池壳体,也使电池壳体更适配于薄片电池。 为达此目的,本发明采用以下技术方案: 一种电池壳体,所述电池壳体为采用如上所述的电池壳体的制造方法制造而成。 本发明的目的在于提供一种单体电池,提高了电池壳体的合格率和制造效率,降 低了制造成本,降低了制造壁厚较薄且尺寸较长或较深电池壳体的生产难度,保证了电池 的散热效率,提高了安全性,也突破了对于单体电池的容量的限制,利于生产大容量电池, 也便于生产薄片电池。 为达此目的,本发明采用以下技术方案: 一种单体电池,包括盖板、电芯和如上所述的电池壳体,两个所述盖板分别封堵于 所述电池壳体的两端开口处,所述电芯置于所述电池壳体和所述盖板围成的腔体内并连接 于所述盖板上的极柱。 优选地,两个所述盖板上的所述极柱分别为正极极柱和负极极柱,所述正极极柱 焊接于所述电芯的正极极耳,所述负极极柱焊接于所述电芯的负极极耳。 本发明的有益效果: 本发明提供的电池壳体的制造方法,通过热挤压或冷挤压的方式,获得管状的预 制金属件,减少了废料的产生,降低了生产难度和成本,提高了制造效率,有效降低了材料 缺失和焊缝处开裂的风险,提高了电池壳体的合格率。在热挤压或冷挤压后,对预制金属件 进行再次拉伸,进一步减小了电池壳体的壁厚,降低了制造出尺寸较长或较深且壁厚较薄 的电池壳体的难度,提高了合格率,而且提高了采用本方法制成的电池壳体的电池模组的 比能量,也提高了采用本方法制成的电池壳体的电池模组的散热效率,符合单体电池的散 热需求,提升了安全性。相较于传统的多次拉伸成型的制作方法,采用先热挤压或冷挤压再 拉伸的顺序,进一步降低了产生材料缺失和焊缝处开裂的风险,提高了电池壳体的合格率 及原材料的利用率,也缩短了生产时间,进一步降低了成本。直接在管状的预制金属件上直 接截取电池外壳,能够根据电池容量的需求截取所需要长度的电池外壳,使电池满足各种 空间需要,提高了空间利用率,突破了对于单体电池的容量的限制,利于生产尺寸较大的大 容量电池壳体,也便于生产与薄片电池更适配的电池壳体。 本发明提供的电池壳体,采用上述电池壳体的制造方法制造而成,两端开口的电 池壳体,降低了制造壁厚较薄且尺寸较长或较深电池壳体的生产难度,提高了电池壳体的 合格率和制造效率,降低了制造成本,突破了对于电池壳体的容量的限制,利于生产大容量 电池,也使电池壳体更适配于薄片电池。 本发明提供的单体电池,使用上述电池壳体,提高了电池壳体的合格率和制造效 率,降低了制造成本,降低了制造壁厚较薄且尺寸较长或较深电池壳体的生产难度,保证了 电池的散热效率,提高了安全性,降低了由单体电池组成的电池模组内部温控系统或冷板 的需求,进一步降低了成本,也突破了对于单体电池的容量的限制,利于生产大容量电池, 4 CN 111740041 A 说 明 书 3/6 页 也便于生产薄片电池。 附图说明 图1是本发明实施例提供的电池壳体的制造方法的主要步骤流程图; 图2是本发明实施例提供的电池壳体的制造方法的详细步骤流程图; 图3是本发明实施例提供的单体电池的结构示意图; 图4是本发明实施例提供的电池模组的结构示意图。 图中: 10、单体电池; 1、电池壳体; 2、盖板;21、极柱。