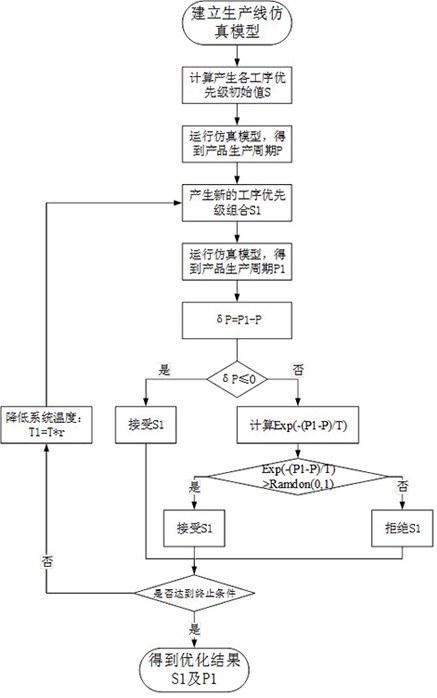
技术摘要:
本发明提供了一种装配生产线仿真模型优化方法,属于生产线仿真模型优化领域,对装配生产线仿真模型中的每一个工序都赋予了一个执行优先级,建立并确定了执行优先级与资源分配时的获取顺序间关系;并且确定工序执行优先级组合与产品生产周期间存在关联,不同工序的执行 全部
背景技术:
由于现代制造生产线已经变得极为复杂,生产线效能受到产品生产流程、生产线 布局、人力资源配置、设备效能、设备故障率、物流系统效能及供应链系统效能等多方面因 素影响,单一算法已经很难对生产线系统做出有效评估。在这样的背景下,出现了离散事件 仿真理论和相应仿真软件。通过离散事件仿真软件可以对生产线系统进行建模和仿真,将 生产线系统的相关要素纳入到模型中,对这些要素的运行规律进行提炼和抽象,并用数学 分布或编程语言体现出来。对建立的生产线系统模型进行仿真运行,可以分析得到系统生 产时间、各元素的繁忙程度、生产瓶颈等信息,同时可以分析生产线元素如人员数量变动对 生产线效能的影响,给出生产线调整的建议。 目前在采用流水线进行产品装配的领域,装配关系通常为串行执行,上一道工序 执行完毕后才能执行下一道工序,产品在不同工位间流动,产品工艺路径固定,产品装配过 程中对各项资源的需求明确,能够按照产品实际装配过程建立装配生产线仿真模型。 但是对于一类复杂产品装配生产线,如航空器、航天器装配生产线等,每一个装配 单元进行小部分工作,同一时间可能有多个装配单元工作,这意味着产品无法在装配单元 中流动,因为在同一时间模型中存在多个装配单元请求同一产品,这在装配生产线仿真模 型构建时是无法实现的。由于装配生产线仿真模型中的装配单元网络通常很大,装配单元 的数量可能达到几百上千个,而这些装配单元在空间上有很大的重叠,因此无法按照装配 单元的实际物理位置进行建模,因此无法使用传统装配生产线仿真建模手段实现这类复杂 产品的装配生产线仿真模型构建。 因此有研究人员提出了一种新的装配生产线仿真模型,该装配生产线仿真模型包 括逻辑仿真层和物理仿真层,其中逻辑仿真层包括装配生产线仿真单元模型以及装配生产 线仿真单元模型之间的依赖关系,物理仿真层包括装配站位、消耗性资源和循环使用资源, 并提出了构建装配生产线仿真模型的具体步骤。 该模型将装配生产线仿真模型分为物理仿真层及逻辑仿真层两部分,能够表达产 品在真实空间中的位置移动以及产品在每个站位上装配工序的运行状态;能够对复杂产品 如航空器、航天器,产品不移动或仅在几个固定站位间移动,同一时间有多个装配单元工作 的装配生产线进行装配生产线仿真模型构建;能够体现循环使用资源及消耗性资源对装配 生产线运行状态的影响;能够体现不同工序间依赖关系对装配生产线运行状态的影响。能 够体现空间限制对于装配生产线运行状态的影响。 该装配生产线仿真模型由物理仿真层和逻辑仿真层组成。 物理仿真层能够表达产品在真实空间中的物理位置、装配过程中发生的移动以及 产品本身的变化。 物理仿真层由若干个站位、循环使用资源、消耗性资源构成。 4 CN 111552241 A 说 明 书 2/10 页 站位表示产品装配过程中的某个阶段,在该阶段,产品的物理位置相对固定,在该 位置完成一些装配、测试、调试或检验工作。产品的装配过程可以划分为若干个站位,上一 个站位的工作结束后,产品移动到下一个站位。 站位内的工作可以划分为若干个工序,所有工序完成后表明该站位工作结束,产 品可移动到下一站位。 产品在站位间依次移动,没有跨越站位的情况。 循环使用资源包括产品在装配过程中可以循环重复使用的资源,包括设备、工装、 人员等。 特别地,将操作空间作为一种循环使用资源,将产品上可供进行装配操作的空间 划分为若干个单元,每个单元能够容纳一定的人员或设备进行装配操作,每个单元被定义 为一种循环使用资源。 在产品装配过程中,循环使用资源可以被周期性申请和释放。 消耗性资源包括产品在装配过程中需要使用的零件、成品、标准件和耗材等。 消耗性资源可以在产品装配过程中被申请。 逻辑仿真层能够表达每个站位中各工序间依赖关系、工序执行顺序、工序对循环 使用资源的申请和释放、工序对消耗性资源的申请,工序开始执行、等待、执行完毕的状态 判定。 在逻辑仿真层中将物理仿真层里的站位映射为一系列具有一定相互依赖关系的 工序的集合。 工序间依赖关系如下: 1、除第一个工序外,每个工序都有一个或多个前置工序,只有当一个工序的所有 前置工序都已执行时,该工序才具备执行条件; 2、每个工序都有0个或多个后置工序,后置工序可由其他工序的前置工序计算得 到。 一个工序开始执行前要进行执行条件判定,执行条件判定包括以下方面: 1、该工序的所有前置工序都已执行完毕; 2、该工序申请所需的循环使用资源,所需的循环使用资源必须处于可用状态,且 未被其他工序占用; 3、该工序申请所需的消耗性资源,所需的消耗性资源必须处于可用状态,且数量 足够。 如果工序开始执行前执行条件不满足,则该工序处于等待状态。 工序执行条件全部满足后,工序开始执行,一定时间后,工序执行完毕,通知后置 工序可以开始执行,并释放占用的循环使用资源。 一个站位的所有工序执行完毕后,该站位的工作完成,产品移动到下一站位,所有 站位工作完成后,产品装配过程完成。 利用上述模型能够对产品生产周期及生产线产能进行评估,但如何调节仿真模型 以提升生产线产能,仍缺乏有效优化方法。 目前针对生产线产能优化问题,仍采用经验法或实验验证法,如根据生产线实际 运行情况、模型仿真情况,调节某些生产线参数如生产线人员配置数量、工艺流程、设备数 5 CN 111552241 A 说 明 书 3/10 页 量等,再观察仿真结果或数据分析结果,相应再调节参数,直至达到期望结果,调节过程十 分繁琐,特别是工艺流程的优化调整,经验型及主观性强,难以获得最优解。
技术实现要素:
本发明的目的在于:提供了一种装配生产线仿真模型优化方法,对装配生产线仿 真模型中的每一个工序都赋予了一个执行优先级,建立并确定了执行优先级与资源分配时 的获取顺序间关系;并且确定工序执行优先级组合与产品生产周期间存在关联,不同工序 的执行优先级组合对应不同的产品生产周期,通过寻找最优的工序的执行优先级组合,能 够找到最短的产品生产周期;给出具体的工序的执行优先级组合迭代优化方法,通过该方 法能够找到最优的执行优先级组合。 本发明采用的技术方案如下: 一种装配生产线仿真模型优化方法,对装配生产线仿真模型中的每一个工序均赋 予一个执行优先级,用数字代表,该优先级代表该工序在与其他工序同时申请相同资源时 的分配顺序,进行仿真时,优先级高的工序应当优先获得资源; 寻找一个各工序优先级数字的组合S,在S情况下,仿真模型运行得到的产品生产 周期最短,则寻找最优解的具体步骤如下: 步骤1:按照当前优先级数字组合S,运行仿真模型,得到产品生产周期P和初始系 统温度Tmax; 步骤2:产生一个新的优先级数字组合S1,产生方式为将从原有优先级数字组合随 机选取两个工序,交换这两个工序的优先级数字,运行仿真模型,得到产品生产周期P1; 步骤3:如果P1<P,则接受新的数字组合S1,如果P1≥P,则以一定概率接受S1,概 率计算方法为将Exp(-(P1-P)/T)的值V与一个0到1间的随机数比较,如V大于该随机数,则 接受S1,并降低温度T,下降后温度T1=T*r; 步骤4:重复步骤2、3,直至满足预设定的产品生产周期阈值或温度下限Tmin; 其中,r表示下降率,根据需求设置,用于控制降温的快慢;Tmax表示系统的初始温 度,系统的初始温度应处于一个高温的状态;Tmin表示系统的终止温度,若系统温度达到 Tmin,则停止搜索。 在本方案中,首先在步骤1中会手动设置或自动生成一个系统初始温度Tmax,本方 案中的温度T以及系统初始温度Tmax、系统终止温度Tmin设置为限制本方案的迭代次数,其 中Tmax、Tmin和每次迭代的下降率r是根据需求预设的,一般设Tmax为1,在无法找到满足预 设定的产品生产周期阈值的方案时,用变换后的温度T1与Tmin进行对比,若T1小于等于 Tmin,则已经进行了足够多次数的迭代重复寻找优先级数字组合S,还无法找到满足预设定 的产品生产周期阈值的,则直接停止迭代重复寻找;当然,在T1>Tmin,但是此时找到的新的 优先级数字组合S1对应的产品生产周期P1满足预设定的产品生产周期阈值的,以此时的优 先级数字组合S1为最终确定的优先级数字组合S。 为了更好的实施本方案,进一步地,所述初始优先级的确定方式包括但不限于以 下三种方式: 方式1:计算每个工序的前置工序数量和后置工序数量之和,记为N,并按N的数字 大小降序,给每个工序赋优先级初值;N越大的工序,优先级越高,N最大的工序优先级数字 6 CN 111552241 A 说 明 书 4/10 页 为1,之后优先级数字依次递增; 方式2:计算每个工序的执行时间,记为T,并按T的数字大小降序,给每个工序赋优 先级初值;T越大的工序,优先级越高,T最大的工序优先级数字为1,之后优先级数字依次递 增; 方式3:记M=α*N β*T,其中α和β为权重,并按M的数字大小降序,给每个工序赋优 先级初值;M越大的工序,优先级越高,M最大的工序优先级数字为1,之后优先级数字依次递 增。 为了更好的实施本方案,进一步地,所述执行优先级用自然数代表。 为了更好的实施本方案,进一步地,所述装配生产线仿真模型由物理仿真层和逻 辑仿真层组成,其中物理仿真层表达产品在真实空间中的物理位置、装配过程中发生的移 动以及产品本身的变化;物理仿真层由若干个站位、循环使用资源、消耗性资源构成; 逻辑仿真层表达每个站位中各工序间依赖关系、工序执行顺序、工序对循环使用 资源的申请和释放、工序对消耗性资源的申请,逻辑仿真层表达还表达工序开始执行、等 待、执行完毕的状态判定。 为了更好的实施本方案,进一步地,所述站位表示产品装配过程中的某个阶段,在 该阶段,产品的物理位置相对固定,在该位置完成一些装配、测试、调试和或检验工作; 产品的装配过程可以划分为若干个站位,上一个站位的工作结束后,产品移动到 下一个站位; 站位内的工作可以划分为若干个工序,所有工序完成后表明该站位工作结束,产 品可移动到下一站位。产品在站位间依次移动,没有跨越站位的情况。 为了更好的实施本方案,进一步地,循环使用资源包括产品在装配过程中可以循 环重复使用的资源,在产品装配过程中,循环使用资源可以被周期性申请和释放。 为了更好的实施本方案,进一步地,将操作空间作为一种循环使用资源,将产品上 可供进行装配操作的空间划分为若干个单元,每个单元能够容纳一定的人员或设备进行装 配操作,每个单元被定义为一种循环使用资源。 为了更好的实施本方案,进一步地,在逻辑仿真层中将物理仿真层里的站位映射 为一系列具有一定相互依赖关系的工序的集合。 为了更好的实施本方案,进一步地,所述工序间的依赖关系主要包括: 依赖关系1:除第一个工序外,每个工序都有一个或多个前置工序,只有当一个工 序的所有前置工序都已执行时,该工序才具备执行条件; 依赖关系2:每个工序都有0个或多个后置工序,后置工序可由其他工序的前置工 序计算得到。 为了更好的实施本方案,进一步地,一个工序开始执行前要进行执行条件判定,所 述执行条件主要包括以下条件: 执行条件1:该工序的所有前置工序都已执行完毕; 执行条件2:该工序申请所需的循环使用资源,所需的循环使用资源必须处于可用 状态,且未被其他工序占用; 执行条件3:该工序申请所需的消耗性资源,所需的消耗性资源必须处于可用状 态,且数量足够。 7 CN 111552241 A 说 明 书 5/10 页 综上所述,由于采用了上述技术方案,本发明的有益效果是: 1.本发明所述的一种装配生产线仿真模型优化方法,提供了一种装配生产线仿真 模型优化方法,对装配生产线仿真模型中的每一个工序都赋予了一个执行优先级,建立并 确定了执行优先级与资源分配时的获取顺序间关系; 2.本发明所述的一种装配生产线仿真模型优化方法,确定了工序执行优先级组合 与产品生产周期间存在关联,不同工序的执行优先级组合对应不同的产品生产周期,通过 寻找最优的工序的执行优先级组合,能够找到最短的产品生产周期; 3.本发明所述的一种装配生产线仿真模型优化方法,给出具体的工序的执行优先 级组合迭代优化方法,通过该方法能够找到最优的执行优先级组合。 附图说明 为了更清楚地说明本技术方案,下面将对实施例中所需要使用的附图作简单地介 绍,应当理解,对于本领域普通技术人员来讲,在不付出创造性劳动的前提下,还可以根据 这些附图获得其他相关的附图,其中: 图1是本发明的原理流程框图。