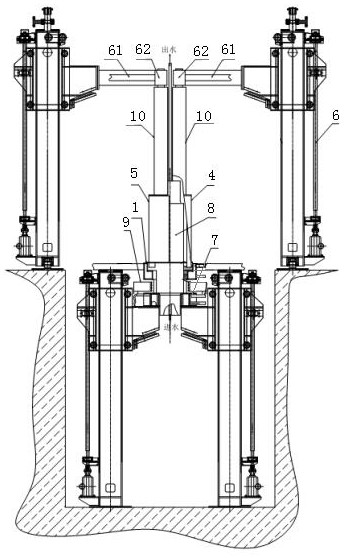
技术摘要:
一种抽锭式电渣重熔法制备双金属覆合轧辊的装置及方法,所述的装置包括一体式结晶器、变压器电源、短网和自耗电极;一体式结晶器内从上至下设有渣料区、熔炼区和结晶区;所述自耗电极包括自耗电极正极和自耗电极负极;所述变压器电源、短网、自耗电极正极、渣料区、自 全部
背景技术:
我国的钢产品在全世界占有量50%以上,而大多钢厂离不开热轧辊,其每年消耗也 非常惊人,年消耗量达50万吨以上,产值达一百多亿。而复合高速钢轧辊以优异的耐磨性和 使用寿命越来越受到国内大型钢企的青睐。由于高速钢合金量达15%以上,离心工艺通常采 用三层复合方式,技术难度大,制造废品率高,国内具备生产能力的轧辊厂寥寥,同时结合 层缺陷等一些质量问题也经常导致轧辊使用过程的提前报废,造成客户损失。 目前国内90%的热轧采用离心浇铸的方式覆合,但这种方式容易产生合金偏析,外 层与芯部冶金结合存在铸造缺陷,且厚度不均匀,组织粗大。国外如日本采用CPC (Continuous Pouring Process for Cladding的缩写,意思是连续浇铸外层成型法)技术 生产的热轧辊,目前已成熟应用,售价高出同材质轧辊的1/3。该工艺是将需要复合的外层 金属液体浇入到在其中心安装有芯棒材料的水冷结晶器内,芯棒材料通过在其上部安装的 感应加热器进行预热,从而实现两种材料的复合,并实现两种材料之间的界面达到冶金结 合,通过抽锭设备,将复合好的轧辊不断地从水冷结晶器中抽出,使生产连续进行,直接复 合轧辊浇注完成。CPC生产技术相较于离心浇铸在组织上基本解决了偏析等问题,但该技术 价格贵,成本高,生产周期长,且由于是连续浇注,还是存在氧化夹渣及组织粗大等问题,所 以影响了轧辊的上机寿命。 CN108372286B公开了一种电渣重熔法制备双金属复合轧辊的装置及方法,其装置 包括T型结晶器的上部结晶器和下部水冷结晶器;上部结晶器为导电结晶器,与下部水冷结 晶器绝缘隔断,下部水冷结晶器装配液位检测仪;重熔复合变压器电源通过短网导线与上 部结晶器连接;方法为:化渣结束后,断开化渣供电回路;浇渣时,当结晶器内渣池的液面没 过导电石墨块下沿时,轧辊辊芯预热供电回路导通并对辊芯进行预热;预热结束,关闭此回 路并降低自耗电极至其端部插入渣池以导通电极熔化与双金属复合供电回路,随之进行双 金属的熔炼复合。 上述专利文献的方法虽然公开了电渣重熔法制备双金属复合轧辊的方法,但采用 的设备却存在以下缺陷:(1)在结晶器方面,其上部为导电结晶器、下部为冷却结晶器组成 的T型结晶器,且上、下结晶器通过绝缘阻隔,一方面会导致结构大大复杂化,且渣温不易控 制;(2)在电路短网和电极方面,电路短网为:变压器→短网→自耗电极→导电结晶器→短 网→变压器;电极采用整体圆套或者数根圆电极,先通过自耗电极为正极,引锭板为负极进 行预热,而后又改自耗电极为正极,导电结晶器为负极。这样的电路中,假如在导电结晶器 有冷却的情况下,就容易因导电结晶器壁出现渣皮而阻断电流,使熔炼过程不稳定,假如导 电结晶器没有冷却的情况下,则很容易因为渣温较高而导致导电结晶器损坏;(3)在结晶器 放置方面,其结晶器直接置于引锭板上,且必须采用石棉绳或镁砂进行绝缘密封,当电极与 4 CN 111590054 A 说 明 书 2/5 页 结晶器壁间的距离过小或电极过偏时,容易引起分流打弧,损坏结晶器,严重情况下,还会 因结晶器被击穿后漏水而发生爆炸事故;(4)轧辊辊芯不能自身进行水温调节,进而无法精 确控制双金属覆合层的厚度。
技术实现要素:
本发明的目的是克服现有技术的上述不足而提供一种结构简单,使用寿命长,冶 炼电流稳定的抽锭式电渣重熔法制备双金属覆合轧辊的装置及方法。 本发明的技术方案是: 本发明之一种抽锭式电渣重熔法制备双金属覆合轧辊的装置,包括一体式结晶器、变 压器电源、短网和自耗电极;一体式结晶器内从上至下设有渣料区、熔炼区和结晶区;所述 自耗电极包括自耗电极正极和自耗电极负极;所述变压器电源、短网、自耗电极正极、渣料 区、自耗电极负极、短网和变压器电源构成供电回路。 进一步,所述自耗电极正极和自耗电极负极均为半圆环电极;正极的半圆环电极 与假电极焊接成一体固定于电渣炉的其中一横梁支臂上,负极的半圆环电极与假电极焊接 成一体固定于电渣炉的另一横梁支臂上。 进一步,还包括轧辊辊芯,所述轧辊辊芯的中心位置开设有中心孔,所述中心孔的 上部和下部分别连接进/出水管。 进一步,还包括底水箱,所述轧辊辊芯设于底水箱的面板的中心孔中。 进一步,所述一体式结晶器为一体式T型结晶器,一体式结晶器的底部直接与底水 箱的面板螺纹连接。 进一步,所述一体式结晶器的外侧且位于结晶区位置处设有能够移动的感应加热 及保温装置。 本发明之一种抽锭式电渣重熔法制备双金属覆合轧辊的方法,包括以下步骤: S1:将轧辊辊芯与一体式结晶器保持轴线重合,并接好轧辊辊芯中心孔处的进/出水 管,保证中心孔内有冷却液体通过; S2:对进入一体式结晶器之前的渣料进行化渣,并对轧辊辊芯进行预热; S3:预热完毕后,将化渣后的渣液倒入一体式结晶器内,通电进行渣液起弧; S4:轧辊辊芯在高温渣液和轧辊辊芯中心孔冷却的双重作用下,出现一定厚度的表层 熔融,自耗电极不断熔化产生的金属液滴逐渐与轧辊辊芯熔融状态的金属覆合在一起,并 在一体式结晶器的冷却作用下凝固成一定厚度的覆合工作层; S5:随着双金属覆合过程的进行,启动抽锭系统进行抽锭,并通过调节轧辊辊芯中心孔 内的水温,控制轧辊辊芯表层的熔化厚度; S6:随着抽锭的进行,待具有覆合工作层的轧辊辊芯长度增加到预设长度后,对其进行 感应加热保温; S7:当轧辊辊芯覆合工作层达到所需目标长度后,停止抽锭;抬升自耗电极脱离渣池, 断电,完成轧辊辊芯覆合工作层的双金属熔覆操作。 进一步,S1~S3具体包括以下步骤: 将留有中心孔的轧辊辊芯固定在底水箱的中心孔内,使得轧辊辊芯与一体式结晶器保 持轴线重合,并将一体式结晶器安装于底水箱上,接好轧辊辊芯的中心孔处的进/出水管; 5 CN 111590054 A 说 明 书 3/5 页 将自耗电极分别装至电渣炉的各横梁支臂的夹头上并夹紧; 按计算的渣料重量,称取烘烤的渣料待用; 选取适量的石墨化渣包放至化渣机特定平台上,接通化渣机电源,起弧后不断加入渣 料进行化渣;同时,对轧辊辊芯进行感应预热; 预热完毕后,在一体式结晶器与轧辊辊芯之间安装导渣模,化渣完毕后,将化渣后的液 渣通过导渣模倒入一体式结晶器中,取走导渣模后,通电进行渣液起弧。 进一步,S5中,控制轧辊辊芯表层的熔化厚度为5~10mm。 进一步,所述轧辊辊芯采用低合金钢进行锻造或铸造而成;所述自耗电极采用离 心浇铸方式将高速钢预制成圆筒体,再将圆筒体一分为二,形成自耗电极的正极和负极。 本发明的有益效果: (1)采用一体式结晶器,结构简单,渣温易于控制,熔速快,省电; (2)供电回路不存在因渣皮绝缘的影响导致冶炼电流不稳定现象,一体式结晶器在水 冷作用下,也不会导致高温渣液对一体式结晶器内壁的损坏; (3)自耗电极采用两个半圆筒组合,其中一个半圆电极充当正极,另一个半圆电极充当 负极,这样可以降低对轧辊辊芯的温度影响; (4)将结晶器直接置于底水箱的面板上,不必采用任何绝缘措施,工装简单容易控制, 且避免了分流引起的打弧现象以及可能造成的安全事故; (5)在轧辊辊芯的中心留孔,采用可调试水冷却装置,通过调节水温,能够精确控制双 金属覆合层厚度; (6)高速钢制成自耗电极进行熔融,使得钢水在渣池中获得二次过滤净化,轧辊辊芯的 工作层,经高速钢套电渣熔覆而成,因此外层钢水洁净度更高; (7)结合层无气孔、疏松、夹渣等铸造缺陷,高速钢外层凝固结晶的冷却温度场及其稳 定性远优于离心铸造工艺,铸态晶粒均匀、细小,经过锻造后这一优势得到进一步巩固和强 化;结合层质量和轧辊辊芯强度,大大降低了轧辊制造中热处理工序的断裂风险,使轧辊可 以采取更剧烈的加热与冷却工艺制度,并由此缩短工艺周期,同时也使高速钢材料获得了 更充分的组织转变和更优异的轧辊使用性能。 附图说明 图1是本发明实施例的结构示意图; 图2是图1所示实施例一体式结晶器的结构放大示意图。 附图标识说明:1.一体式结晶器;2.变压器电源;3.短网;4.自耗电极正极;5.自耗 电极负极;6.升降机构;7.底水箱;8.轧辊辊芯;9.移动式感应线圈;10.假电极;11.渣料区; 12.熔炼区;13.结晶区;61.横梁支臂;62.夹头;71.面板;81.中心孔;82.出水管;83.进水 管。