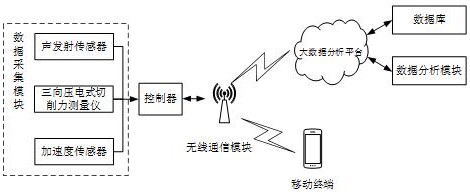
技术摘要:
本发明涉及断刀检测的技术领域,具体公开用于CNC断刀预测的系统,包括用于采集刀具数据信息的数据采集模块、用于指令控制的控制器、用于数据传输的无线通信模块、用于数据存储、分析与预测的大数据分析平台以及用于信息查看的移动终端。以及提出了一种基于改进粒子群优 全部
背景技术:
刀具毁损状态的智能识别作为制造过程技术的一部分,现已逐渐被人们重视。一 个运行可靠的刀具磨损状态监测系统可以通过及时、准确地反映刀具磨损状态信息来指导 机床完成自动换刀,实现不间断生产过程,稳定工件的加工质量。 传统的数控加工刀具状态监测方法普遍采用单一传感器监测方法,通过采集并处 理与切削过程相关的信号,如电流信号、切削信号、振动信号、切削声信号或电机功率等,间 接获得反映刀具磨损状态的某些信息,此方法获取的信息存在类型单一、信息量有限、抗干 扰能力较低等缺陷。 传统的断刀检测设备体积较大且价格昂贵,只能实时监测一台机床的工作状态, 无法实现一台设备实时监测多台设备的运行,给企业的生产带来了不便,增加了监测设备 支出。 传统的 刀具状态预测方法普遍采 用单一 B P神经网络算法 ,申请号为 201811122597.1的专利公开了一种“基于改进的BP神经网络的刀具磨损预测方法”,此种技 术方案采用的BP神经网络算法存在的问题是:学习效率比较低,收敛速度慢,虽然提出了采 用多种函数来改善模型的权重和阈值,但是网络训练过程中的参数仍需要通过大量试验得 到的经验函数来设定。 针对BP神经网络存在陷入局部最小和收敛速度慢的问题、粒子群优化算法容易早 熟以及算法后期易在全局最优解附近产生震荡现象,本发明采用基于改进粒子群优化BP神 经网络的CNC断刀预测方法,创新之处在于利用权重线性递减的粒子群优化算法,让惯性权 重从最大值减小到最小值,这种改进后的粒子群算法增加了粒子的寻优效果,大大提高了 算法收敛速度、精度和稳定性。本发明采用的改进算法对断刀状态的预测有显著的效果,处 理速度快、预测准确性高。 由此可见,采用基于改进粒子群优化BP神经网络的算法是实现对刀具状态预测的有效 方法。
技术实现要素:
针对现有技术存在的问题,本发明提供一种用于CNC断刀预测的系统及方法。 本发明采用以下技术方案实现。 一种用于CNC断刀预测的系统,其特征在于:所述CNC断刀预测系统包含数据采集 模块、控制器、无线通信模块、大数据分析平台、移动终端;所述数据采集模块包括声发射传 感器、测力仪、加速度传感器,分别用于采集数控机床运行时刀具产生的声发射信号、切削 力信号以及加速度信号;所述控制器用于接收大数据分析平台的控制指令,并将采集的数 据信息通过无线通信模块传输至大数据分析平台;所述无线通信模块用于实现控制器与大 4 CN 111597860 A 说 明 书 2/7 页 数据分析平台之间的数据交互,其实现形式包括蓝牙、WiFi、以及ZigBee;所述大数据分析 平台包括数据库和数据分析模块,分别用于数据存储以及利用CNC断刀预测方法对数据进 行分析和处理;所述移动终端为智能手机或者平板电脑,能够实现与大数据分析平台的信 息交互,实时查看刀具的状态信息;所述数据采集模块与控制器的输入端相连,控制器的信 号端通过无线通信模块与大数据分析平台和移动终端相连。 进一步地,所述大数据分析平台是建立在服务器集群上,为大数据分析平台提供 硬件支撑,所述数据库和数据分析模块是在服务器集群上分别部署基于Hadoop、Hbase存储 系统及上层的计算架构。其具体实现包括: 1,数据采集模块获取的信号,经由控制器,以物联网通信协议等数据格式,送达集群部 署的大数据平台的服务器。 2,大数据平台的接收端口,以Java技术为核心构建的高并发高可用的响应接口,将数 据快速存入Kafka消息中间件构建的消息通道当中,以便数据的分发处理。 3,从消息通道中,不断获取信号数据,存入Hadoop集群当中,从而行程历史数据。海量 的历史数据可以用在日常数据统计分析,也可以用于预测模型的自我学习。 4,从消息通道,利用流式计算框架,结合相关检测模型,快速地进行实时数据的运算。 一种用于CNC断刀预测的方法,其特征在于,所述方法包括如下步骤: S1,使用数据采集模块采集数控机床运行的原始信号数据,建立包含断刀故障状态和 非断刀正常状态数据库; S2,对采集的原始信号数据进行归一化处理,按比例划分为训练集和测试集; S3,建立基于BP神经网络的数控机床断刀预测模型; S4,利用改进粒子群优化BP神经网络,进行模型训练,输出优化后的BP神经网络的最佳 权值和阈值; S5,将测试集中的样本数据作为输入,通过步骤S4优化后的BP神经网络来进行数控机 床断刀预测。 所述步骤S2中的归一化处理方法采用离差标准化处理方法,是对原始信号数据的 线性变换,使结果落到[0,1]区间,转换函数如下: 其中, 是归一化后的数据, 为原始信号数据,max为原始信号数据的最大值,min为 原始信号数据的最小值。 所述步骤S3中的数控机床断刀预测模型采用三层BP神经网络模型;所述模型的输 入层中,输入节点数为3个,为声发射信号、加速度和切削力;所述模型的隐含层节点数为7 个;所述模型的输出层中,输出节点数为2个,为断刀故障状态和非断刀正常状态。 所述采集数控机床运行的原始信号数据,其过程是利用离散分布采样不断采集其 声发射、加速度以及切削力的信号数据得到其时序数据。 所述步骤S4利用改进粒子群优化BP神经网络的具体步骤为: S41,使用将BP神经网络的权值和阈值定义为粒子群搜索空间中的一个粒子,并进行粒 子群参数的初始化; 5 CN 111597860 A 说 明 书 3/7 页 S42,根据粒子个体最优位置和群体的全局最优位置计算适应度函数,其适应度函数 为: 其中, 为粒子数,为输入样本数, 为网络的实际输出, 为样本输出; S43,更新微粒的速度和位置,微粒的速度和位置表达式为: 其中, 、 为加速常数, 是微粒空间维数, 为惯性权重, 、 为0到1之间均匀分 布的随机数, 是每个微粒所经过的个体最佳位置; 是群体所发现的最佳位置; S44,计算位置更新后每个微粒的适应度,将每个微粒的适应度与以前经历过的最好位 置所对应的适应度比较,如果较好,则将其当前的位置作为该微粒的最好位置; S45,将每一个微粒的适应度与全体微粒所经历过的最好位置比较,如果好,更新全体 微粒的最好位置; S46,检查终止条件,如果没有达到预设条件,则返回步骤S43;如果满足预设条件,则停 止迭代,输出最优解。 所述步骤S43中惯性权重的计算采用线性变化的权重,计算公式为: 其中, 、 分别表示的最大值和最小值,表示当前迭代步数, 表示最大 迭代步数; 所述步骤S46中的终止条件为达到最大迭代次数或者达到了足够好的适应值。 本发明的有益效果是: (1)本发明将传感器、无线通信网络以及大数据三种技术相融合,由无线通信网络完成 传感器采集数据的传输,大数据分析平台完成数据的分析与预测,摆脱了对工业现场检测 仪器设备的依赖,极大的降低了生产成本; (2)本发明采集数控机床运行的原始信号数据,包含声发射信号、加速度信号以及切削 力信号,数据全面可靠,保证了算法的训练质量; (3)本发明将粒子群优化算法的寻优特性应用在BP神经网络权值和阈值的优化问题 上,不仅可以优化了神经网络的结构,也可以提高神经网络效率; (4)针对BP神经网络存在陷入局部最小和收敛速度慢的问题、粒子群优化算法容易早 熟以及算法后期易在全局最优解附近产生震荡现象,本发明采用权重线性递减的粒子群优 化算法,让惯性权重从最大值减小到最小值,这种改进后的粒子群算法大大提高了粒子的 寻优效果。 6 CN 111597860 A 说 明 书 4/7 页 附图说明 图1是一种用于CNC断刀预测的系统的结构示意图; 图2是一种用于CNC断刀预测的系统的大数据分析平台结构示意图; 图3是一种用于CNC断刀预测的方法的总体流程图; 图4是改进粒子群优化算法应用于BP网络时适应度曲线的变化图。