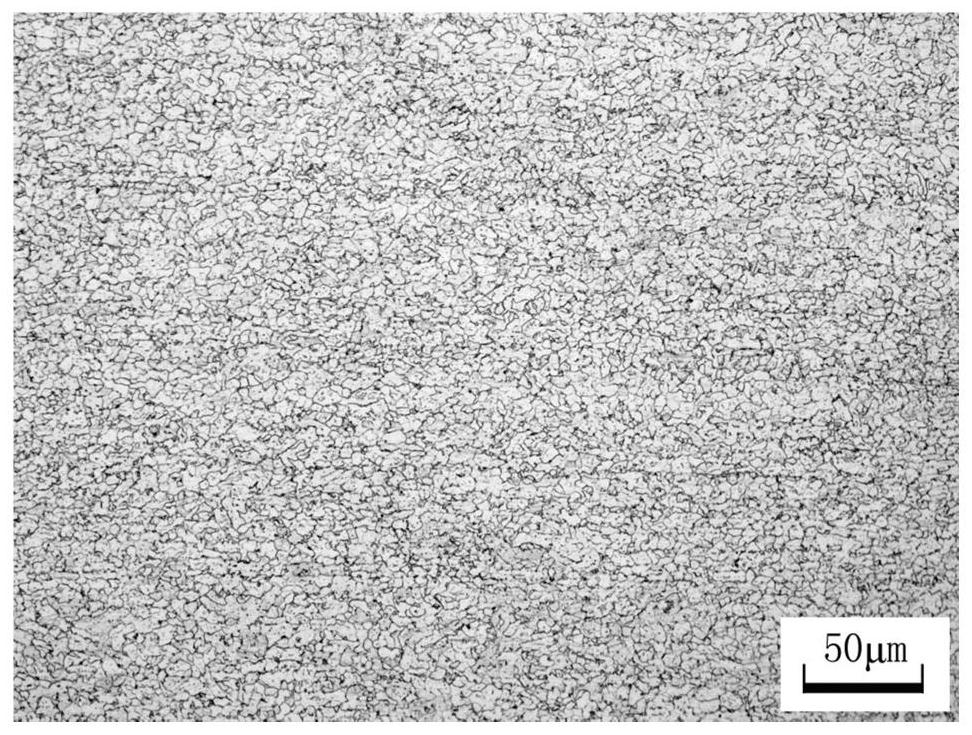
技术摘要:
本发明公开了一种车轮用1500MPa级热成形钢板及其生产方法,属于热轧钢技术领域。该热成形钢板包括如下质量百分比含量的各化学组分:C:0.20~0.25,Si:0.10~0.30,Mn:1.00~1.40,P≤0.010,S≤0.004,Ti:0.020~0.040,Cr:0.10~0.30,B:0.0030~0.0040,其余为Fe及不 全部
背景技术:
当前的汽车行业,降低燃料消耗、减少CO2和废气排放已成为社会的需求,作为材 料生产厂的钢铁业为了适应这种发展趋势,已开发出许多种类的超高强度钢板来帮助减轻 汽车重量,适应汽车工业的新要求。 热成形技术在汽车领域具有广阔的应用前景。采用热成形工艺制造商用车车轮, 在车轮行业属于技术创新。车轮行业传统选材为低合金钢或者双相钢,采用热成形钢车轮 强度可以从600MPa大幅提升至1500MPa。另外车轮作为承载件,高强化对汽车轻量化减重的 效果更为显著。 中国发明专利申请(申请公布号:CN106811689A,申请公布日:2017-06-09)公开了 一种抗拉强度≥2000MPa热成形钢的制备方法。其化学成分以质量百分比计为:C:0.3~ 0.5%,Si:1.2~1.7%,Mn:1.4~2.0%,Al:0.01~0.07%,Cr≤1.5%,P≤0.008%,S≤ 0.005%,B:0.001~0.01%,Ti:0.05~0.1%,Nb:0.01~0.08%,其余为Fe和不可避免的杂 质元素,采用冶炼、热轧、冷轧、罩式退火得到热成形钢,本发明钢制备流程简单,奥氏体化 淬火后,屈服强度Rp0.2=1000~1200MPa,抗拉强度Rm≥2000MPa,延伸率A50=8~9%,采 用罩式退火工艺,将热成形前的基料强度降至屈服强度424~588MPa,抗拉强度616~ 760MPa,延伸率A50提高至17.3~20.4%,大大降低了热成形前进行形状裁剪和切削加工过 程中由于强度太高造成的开卷困难,开卷断带,剪切落料脆裂,边部应力过高,损坏剪切加 工刀刃等问题。 中国发明专利申请(申请公布号:CN107641759A,申请公布日:2018-01-30)公开了 一种基于CSP流程生产薄规格热成形钢的方法。本发明设计的薄规格热成形钢的化学成分 及重量百分比为:C:0.20~0.25%,Si:0.15~0.30%,Mn:1.15~1.5%,Cr:0.20~0.40%, Ti:0.015~0.05%,Nb:0.018~0.03%,B:0.002~0.005%,Als:0.015~0.05%,P≤ 0.015%,S≤0.004%,N≤0.005%,其余为Fe及不可避免的杂质。采用的CSP生产方法包括 步骤:炼钢、连铸、均热、除鳞、精轧、层流冷却及卷取、平整、热冲压成形。得到的薄规格热成 形钢具有较好的抗拉强度和塑性,而且轧制过程稳定性高,产品表面质量优良,满足汽车行 业“以热代冷”的市场需求。 中国发明专利申请(申请公布号:CN 108359895 A,申请公布日:2018-08-03)公开 了一种抗拉强度950MPa级别的热成形钢及其热轧工艺,所述热成形钢化学成分组成及其质 量百分含量为:C:0.06~0.10%,Si:0.3~0.6%,Mn:1.0~2.0%,S≤0.004%,P≤0.02%, Nb:0.01~0.06%,Ti:0.01~0.06%,B:0.0008~0.0020%,其余为Fe及不可避免的杂质; 所述热轧工艺包括加热、粗轧、精轧、层流冷却和卷取工序。本发明生产的热成形钢产品经 热成形工艺处理后,微观组织由多边形铁素体和马氏体组成,屈服强度≥700MPa,抗拉强度 3 CN 111575602 A 说 明 书 2/7 页 ≥950MPa,断后伸长率≥10%,可用于对塑性、强度和焊接性能要求较高的汽车用钢领域。 中国发明专利申请(申请公布号:CN 109136759A,申请公布日:2019-01-04)公开 了轮辋用1300MPa级热成形钢及制备方法,其化学成分按重量百分比包括:0.19~0.24%的 C、0.10~0.30%的Si、1.00~1.40%的Mn、P≤0.010%、S≤0.004%、0.020~0.040%的Ti、 0.0030~0.0040%的B,余量为Fe及不可避免的杂质。采用热轧 罩式退火处理工艺,可以降 低钢板强度,提升延伸率,从而使钢材具有良好的成形性能和焊接性能,其热轧钢板的抗拉 强度≤520MPa、屈服强度≤400MPa、延伸率≥30%,热成形钢经过常规的热成形工艺处理 后,抗拉强度≥1300MPa、屈服强度≥1000MPa、延伸率≥10%。 中国发明专利申请(申请公布号:CN 109136759A,申请公布日:2019-01-04)公开 了轮辐用厚规格1300MPa级热成形钢及制备方法,化学成分按重量百分比包括:0.20~ 0.24%的C、0.20~0.30%的Si、1.10~1.50%的Mn、P≤0.010%、S≤0.004%、0.020~ 0.040%的Ti、0.0030~0.0040%的B,余量为Fe及不可避免的杂质,且钢的厚度为3.0~ 10.0mm。本发明的化学成分以及热轧工艺,获得晶粒尺寸细小的铁素体 珠光体组织,综合 力学性能良好的热成形钢板材,板材的抗拉强度≤650MPa、屈服强度≤540MPa、延伸率≥ 27%,热成形钢经过常规的热成形工艺处理后,抗拉强度≥1300MPa、屈服强度≥1000MPa、 延伸率≥10%。 其中,上述专利1公布的是一种冷轧热成形钢,专利2公布的是一种利用CSP流程生 产的薄规格热轧热成形钢,他们都是生产薄规格的产品,主要为1.0~3.0mm,用作汽车的安 全件,如A柱、B柱等,制成的零件通常采用点焊的方式衔接,不适用于厚规格的车轮零件。本 发明是针对车轮零件,车轮零件需要预先冷成形,对冷加工成形性要求较高,专利1公布的 热成形钢热成形前的强度为屈服强度424~588MPa,抗拉强度616~760MPa,延伸率17.3~ 20.4%,专利2没有对热轧钢板的成形性能做出要求,都不能满足车轮零件冷加工要求。专 利3公布的热成形钢成形后抗拉强度只有950MPa,满足不了更高强度1500MPa的需求,也没 有对热轧钢板的成形性能做出要求。专利4和专利5分别为1300MPa级热轧热成形轮辋和轮 辐用钢,其中专利4采用罩式退火处理,会导致钢板表面脱碳,脱碳层深度≥30μm,导致材料 的疲劳性能不能满足要求,而专利5没有采用罩退处理,但是对热轧工艺没有控制,使得热 轧钢板的强度较高,不利于对钢板的冷加工。
技术实现要素:
为解决上述技术问题,本发明公开了一种车轮用1500MPa级热成形钢板及其生产 方法。本发明提出了车轮用厚规格的热成形钢,并提出了控制措施,保证钢板在冷加工良好 成形性能,通过热成形后达到1500MPa的高强度,并且车轮零件具有良好的疲劳性能。。 为实现上述目的,本发明公开了一种车轮用1500MPa级热成形钢板,其特征在于, 它包括如下质量百分比含量的各化学组分:C:0 .20~0.25,Si:0 .10~0.30,Mn:1 .00~ 1.40,P≤0.010,S≤0.004,Ti:0.020~0.040,Cr:0.10~0.30,B:0.0030~0.0040,其余为 Fe及不可避免的杂质,且所述热成形钢板厚度为2.0~12.0mm。 进一步地,所述B元素的含量为0.0030~0.0035%。 进一步地,所述Ti元素的含量为0.020~0.025%。 进一步地,所述Cr元素的含量为0.14~0.25%。 4 CN 111575602 A 说 明 书 3/7 页 进一步地,所述热成形钢板采用热轧工艺制得,且热轧后的钢板表面脱碳层深度 ≤30μm。 进一步地,所述热成形钢板采用热轧工艺制得,且热轧后的钢板表面脱碳层深度 为20~30μm。 进一步地,所述热成形钢板制成的车轮置于车轮台架上进行疲劳寿命测试,其疲 劳寿命大于100万次。 为更好的实现本发明技术目的,本发明还公开了一种上述车轮用1500MPa级热成 形钢板的制备方法,其特征在于,它包括冶炼、精炼、连铸、加热、粗轧、精轧、层流冷却、卷取 及热成形处理工艺,其中,所述层流冷却包括对轧制后钢卷立即进行前段快冷,冷却至715 ~740℃进行卷取,冷却速率≥100℃/s。 进一步地,所述加热温度控制在1250~1290℃,加热时间≥150min。 进一步地,所述冷却速率为115~125℃/s。 进一步地,所述粗轧结束温度为1050~1060℃,控制精轧终轧温度为850~865℃; 且粗轧除鳞不少于五道次,精轧前除鳞集管开启数不少于二根。 有益效果: 1、本发明采用合理的化学成分,并根据各化学成分对应设置各热轧工艺,获得热 轧板的晶粒尺寸细小的铁素体 珠光体组织,晶粒度等级≥10级;尤其是热轧钢板表面脱碳 层深度≤30μm,较好的保证了热成形板的力学性能。 2、本发明设计的热成形钢板不仅在厚度上能同时保证轮辐和轮辋使用,同时在使 用性能上抗拉强度≥1500MPa、屈服强度≥1000MPa、延伸率≥8%,将其置于车轮台架上进 行疲劳寿命测试,其疲劳寿命大于100万次,可满足汽车车轮钢高强度轻量化要求。 附图说明 图1为本发明实施例热成形钢板热成形处理前的金相组织图; 图2为本发明实施例热成形钢板热成形处理后的金相组织图。