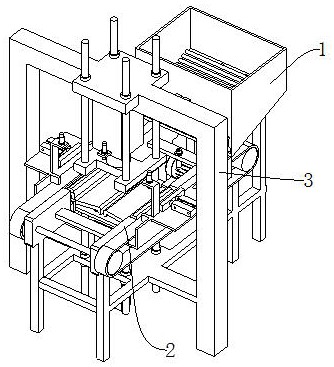
技术摘要:
本发明涉及金属件加工领域,具体是涉及一种长条形金属板材连续折弯机,包括下料机构、输送机构和折弯机构,输送机构的输入端设有下料机构,沿输送机构的输送路径上设有折弯机构,折弯机构包括第一折弯机构和第二折弯机构,第二折弯机构包括第二折弯驱动气缸、折弯支撑 全部
背景技术:
易弯折金属及合金弯折后广泛应用于各个领域,其中在机器散热装置和暖气片散 热装置方面,板材的折弯部位为直角时,具有良好的散热性能。折弯机是一种能够对金属板 材进行折弯的机器,现有的折弯机在使用的过程中,将需要折弯的金属板材放置在工作台 上,由折弯上模向下、与折弯下模共同作用进行折弯工作。但是折弯机进行弯折时操作比较 繁琐,对金属板材没有任何缓冲结构,容易损坏到板材,同时机器使用不便,且折弯机的结 构比较复杂,成本较高。
技术实现要素:
本发明所要解决的技术问题是提供一种长条形金属板材连续折弯机,该技术方案 解决了现有折弯机对金属板材没有任何缓冲结构,容易损坏板材的问题,该连续折弯机折 弯支撑板上的折弯缓冲板、缓冲弹簧在折弯过程中起到了对折弯支撑板以及金属板材的缓 冲作用,与第二折弯机构相配合,将金属板材折弯成U型。 为解决上述技术问题,本发明提供以下技术方案: 提供一种长条形金属板材连续折弯机,包括下料机构、输送机构和折弯机构,所述输送 机构的输入端设有所述下料机构,沿输送机构的输送路径上设有所述折弯机构,折弯机构 设置在下料机构侧部,折弯机构包括第一折弯机构和第二折弯机构,所述第一折弯机构设 置在所述第二折弯机构的顶部,第二折弯机构包括第二折弯驱动气缸、折弯支撑板、折弯缓 冲板和缓冲弹簧,所述第二折弯驱动气缸的输出端传动连接有所述折弯支撑板,折弯支撑 板上对称铰接有两块所述折弯缓冲板,每个折弯缓冲板与折弯支撑板之间均设有缓冲弹 簧,缓冲弹簧的一端与折弯缓冲板连接,缓冲弹簧的另一端与折弯支撑板连接。 作为长条形金属板材连续折弯机的一种优选方案,所述下料机构包括储料箱、出 料口、挡料驱动气缸、挡料板和下料传感器,所述输送机构的输入端处设有所述储料箱,储 料箱上设有出料口,储料箱的侧部设有所述挡料驱动气缸,挡料驱动气缸的输出端传动连 接有用于遮挡或者开启出料口的挡料板,储料箱的侧部设有所述下料传感器。 作为长条形金属板材连续折弯机的一种优选方案,所述储料箱内转动连接有若干 下料引导辊。 作为长条形金属板材连续折弯机的一种优选方案,储料箱的外壁上设有振动电 机。 作为长条形金属板材连续折弯机的一种优选方案,所述第一折弯机构包括第一折 弯驱动气缸和折弯压杆,输送机构的侧部设有龙门架,龙门架上悬挂有所述第一折弯驱动 气缸,第一折弯驱动气缸的输出端传动连接有所述折弯压杆,折弯压杆设置为工字型,第一 折弯驱动气缸的底部设有所述第二折弯机构。 3 CN 111589908 A 说 明 书 2/4 页 作为长条形金属板材连续折弯机的一种优选方案,输送机构上对称设有两个定位 驱动气缸,每个所述定位驱动气缸的输出端均传动连接有一个所述定位推板。 作为长条形金属板材连续折弯机的一种优选方案,每个定位驱动气缸的侧部设有 均设有一个折弯传感器,第一折弯驱动气缸的侧部设有出料传感器。 作为长条形金属板材连续折弯机的一种优选方案,龙门架上设有至少一根第一导 向杆,第一导向杆与龙门架滑动连接,且龙门架的一端与折弯压杆连接,第二折弯驱动气缸 的侧部设有至少一根第二导向杆,第二导向杆的一端与折弯支撑板连接。 本发明与现有技术相比具有的有益效果是: 下料机构内放置的金属板材会从储料箱的出料口处滑落下料,在输送机构的输送下, 进入折弯机构上的折弯工位位置,当有折弯传感器检测到金属板材通过时,定位驱动气缸 会开始工作,驱动定位推板从金属板材的两侧对其进行矫正和夹紧定位,折弯机构的第一 折弯机构和第二折弯机构开始工作,第二折弯驱动气缸工作时,驱动折弯支撑板向上升起, 折弯支撑板上的折弯缓冲板、缓冲弹簧在折弯过程中起到了对折弯支撑板以及金属板材的 缓冲作用,第一折弯驱动气缸工作时,会驱动折弯压杆向下降,与第二折弯机构相配合,将 金属板材折弯成U型。 该连续折弯机通过将金属板材存放在储料箱内,金属板材在重力作用、下料引导 辊和振动电机下滑落出出料口并落入输送机构上,并在输送机构的输送下,进入折弯机构 上的折弯工位位置,折弯机构的第一折弯机构和第二折弯机构开始工将金属板材折弯成U 型,提高生产效率和生产质量,方便快捷。 附图说明 图1为本发明的结构示意图一; 图2为本发明的结构示意图二; 图3为本发明的俯视图; 图4为本发明的结构示意图三; 图5为图4中A处的放大示意图; 图6为本发明的结构示意图四; 图7为本发明的结构示意图五。 图中标号为: 1-下料机构;1a-储料箱;1b-出料口;1c-下料引导辊;1d-振动电机;1e-挡料驱动气缸; 1f-挡料板;1g-下料传感器; 2-输送机构; 3-折弯机构;3a-龙门架;3b-第一折弯驱动气缸;3c-折弯压杆;3d-第一导向杆;3e-第 二折弯驱动气缸;3f-折弯支撑板;3g-折弯缓冲板;3h-缓冲弹簧;3i-折弯传感器;3j-出料 传感器;3k-定位驱动气缸;3l-定位推板;3m-第二导向杆。