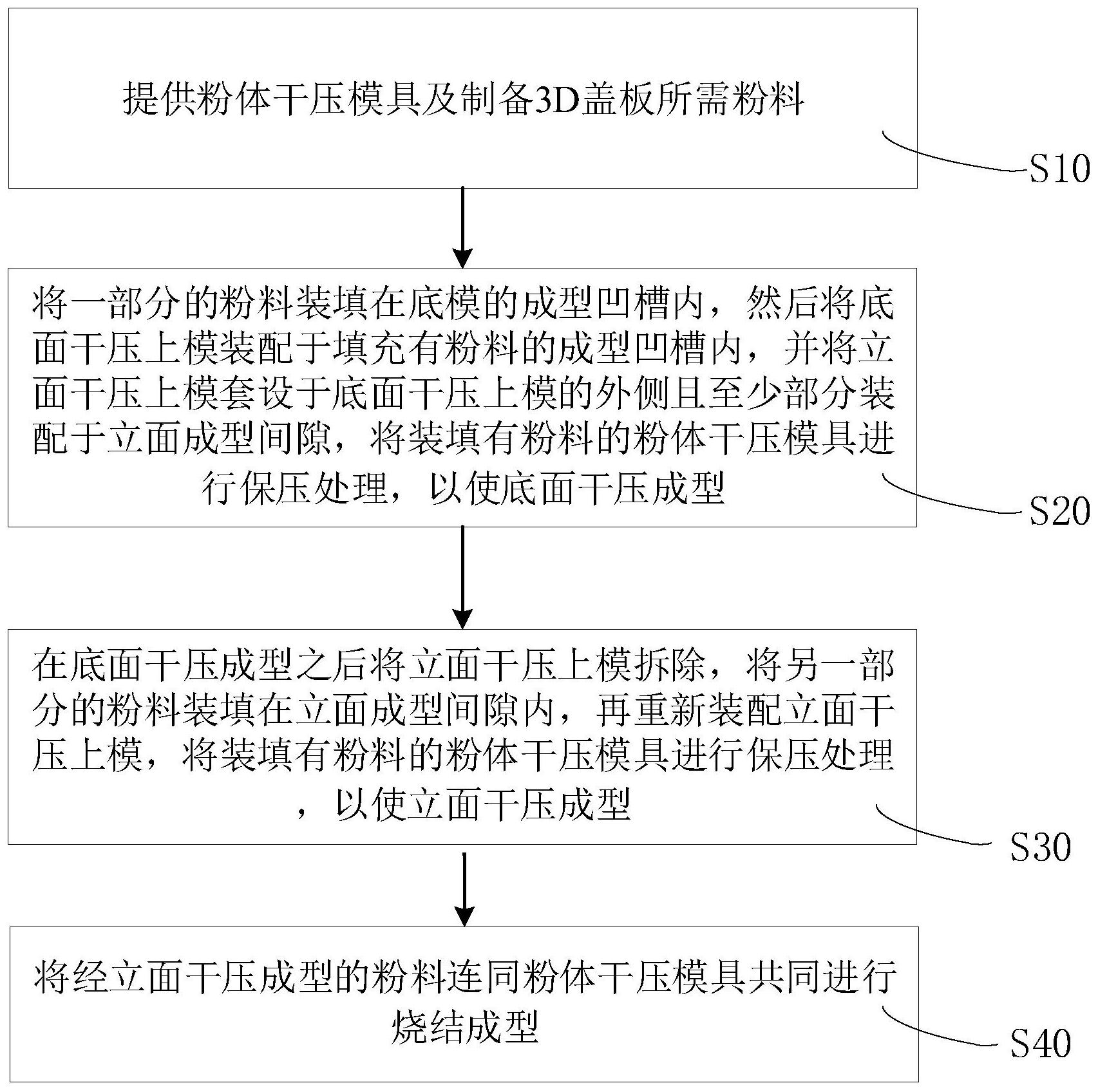
技术摘要:
本发明涉及一种3D盖板的制备方法,包括如下步骤:提供粉体干压模具及制备3D盖板所需粉料;将一部分的粉料装填在底模的成型凹槽内,然后将底面干压上模装配于填充有粉料的成型凹槽内,并将立面干压上模套设于底面干压上模的外侧且至少部分装配于立面成型间隙,将装填有 全部
背景技术:
随着5G时代的到来,3C产业盖板迎来一次变革。传统的金属手机盖板对5G信号屏 蔽严重,且无法进行无线充电,面临淘汰。塑料手机盖板握持感不足,不够高端。众多手机厂 商逐渐开始使用玻璃、陶瓷或微晶玻璃材质的3D盖板。 3D玻璃盖板的触感优秀,装饰简单,兼具美观与实用的优点,是手机盖板发展的主 流趋势。传统将玻璃等材质由2D、2.5D变为3D结构的主流做法为热弯,即加热使玻璃软化, 然后利用模具对玻璃加压,形成特定的3D形状。但此方法对3D玻璃生产的局限性高,难以生 产弯折幅度大,立面高度深的3D玻璃盖板。 陶瓷材质的3D盖板,握持感出众且硬度高,经久耐用。然而由于陶瓷硬度高,且无 法使用类似玻璃热弯的工艺,所以无法生产3D形状的陶瓷盖板。目前市面上主流的陶瓷盖 板为2D、2.5D,缺乏科技感、不够美观,难以引起消费者的购买欲望。 微晶玻璃又叫玻璃陶瓷,是以玻璃为基质,陶瓷为增强体的复合材料。微晶玻璃由 于存在微小晶粒在玻璃基质中,故而具有陶瓷的高硬度,又具有玻璃的韧性,是一种力学性 能出众的无机非金属材料。微晶玻璃由于其出众的力学性能引起了各方关注。但目前微晶 玻璃材质的3D盖板的制备面临诸多困难,玻璃热弯工艺对微晶玻璃适用性不高,难以生产 弯折幅度大、立面高度深的3D微晶玻璃盖板。
技术实现要素:
基于此,有必要提供一种适用范围广、能够适用于玻璃、陶瓷或微晶玻璃材质的3D 盖板生产的制备方法。 一种3D盖板的制备方法,包括如下步骤: 提供粉体干压模具及制备3D盖板所需粉料;其中所述粉体干压模具包括底模及上 模组件,所述底模设有成型凹槽;所述上模组件包括底面干压上模及立面干压上模;所述底 面干压上模能够与所述成型凹槽相配合,所述底面干压上模的外径小于所述成型凹槽的内 径以使所述底面干压上模与所述成型凹槽配合时形成立面成型间隙;所述立面干压上模能 够套设于所述底面干压上模的外侧且至少部分装配于所述立面成型间隙; 将一部分的粉料装填在所述底模的成型凹槽内,然后将所述底面干压上模装配于 填充有粉料的所述成型凹槽内,并将所述立面干压上模套设于所述底面干压上模的外侧且 至少部分装配于所述立面成型间隙,将装填有粉料的粉体干压模具进行保压处理,以使底 面干压成型; 在所述底面干压成型之后将所述立面干压上模拆除,将另一部分的粉料装填在所 述立面成型间隙内,再重新装配所述立面干压上模,将装填有粉料的粉体干压模具进行保 压处理,以使立面干压成型; 4 CN 111605044 A 说 明 书 2/9 页 将经所述立面干压成型的粉料连同所述粉体干压模具共同进行烧结成型。 上述3D盖板的制备方法,采用特定的粉体干压模具及新型粉体干压工艺对粉料进 行底面干压成型和立面干压成型以使底面和立面的粉料均被压制紧实,然后连同粉体干压 模具共同进行烧结成型,可避免烧结存在大量孔隙的问题,进而制得具有立面结构的3D盖 板。 此外,上述3D盖板的制备方法适用范围广,可以适用于但不限于陶瓷材质、玻璃材 质、微晶玻璃材质的3D盖板的生产制备,不仅无需等静压处理即可将立面粉料颗粒压实,而 且克服了传统的玻璃热弯工艺难以生产弯折幅度大、立面高度深的3D盖板的问题,甚至可 以生产“中框 后盖”一体化的3D玻璃盖板、3D陶瓷盖板、3D微晶玻璃盖板。 在其中一些实施例中,所述底面干压成型中的保压处理的条件为:于(50~200) MPa/cm2的压力下保压5min~30min;和/或 所述立面干压成型中的保压处理的条件为:于(50~200)MPa/cm2的压力下保压 5min~30min。 在其中一些实施例中,在粉料装填至所述成型凹槽内或所述立面成型间隙内之 后,且在进行保压处理之前,还包括步骤: 将装填有粉料的粉体干压模具进行震荡,以使所述粉体干压模具内的粉料均匀分 布。 在其中一些实施例中,提供制备3D盖板所需粉料的步骤包括如下步骤:按照制备 3D盖板所需原料称取各组分,粉碎混合,得到所述粉料;和/或 在所述烧结成型的步骤之后还包括步骤:拆除所述粉体干压模具并取出成型产 品,及进行切割、开孔槽及抛光处理。 在其中一些实施例中,所述3D盖板为玻璃材质,所述烧结成型的条件为于550℃~ 1200℃烧结2h~12h;或 所述3D盖板为陶瓷材质,所述烧结成型的条件为于550℃~1500℃烧结2h~12h; 或 所述3D盖板为微晶玻璃材质,所述烧结成型的条件为:加热至900℃~1050℃熔 融,降温100℃~500℃,继续烧结晶化2h~12h。 在其中一些实施例中,所述底面干压上模的厚度大于所述成型凹槽的深度;所述 立面干压上模能够套设于所述底面干压上模的外侧且部分装配于所述立面成型间隙;所述 上模组件还包括上模外框,所述上模外框能够套设于所述立面干压上模凸出于所述底模的 外侧区域且与所述底模相贴合; 所述底面干压成型的步骤中,在所述保压处理的步骤之前还包括如下步骤:将所 述上模外框套设于所述立面干压上模凸出于所述底模的外侧区域且与所述底模相贴合。 在其中一些实施例中,所述底模、所述底面干压上模、所述立面干压上模及所述上 模外框的材质各自独立地选自金属、石墨及陶瓷材料中的一种。 在其中一些实施例中,所述底模包括底模基体及凸台,所述底模基体包括边缘部 及被所述边缘部围绕的中心部,所述凸台设于所述中心部上,所述成型凹槽设于所述凸台 上; 所述上模外框能够与所述底模的所述凸台及所述边缘部相贴合。 5 CN 111605044 A 说 明 书 3/9 页 在其中一些实施例中,所述上模外框具有外框基体,所述外框基体设有用于与所 述底面干压上模配合的第一中心孔,所述外框基体的一表面围绕所述第一中心孔设有凹陷 部,所述凹陷部用于与所述底模的凸台相贴合,所述外框基体的边沿用于与所述边缘部相 贴合。 在其中一些实施例中,所述立面干压上模具有用于与所述底面干压上模配合的第 二中心孔; 所述立面干压上模沿所述第二中心孔的轴向包括第一端和第二端,所述第一端用 于装配于所述立面成型间隙且所述第二端凸出于所述底模;在自所述第一端至所述第二端 的方向上,所述第一端的壁厚保持不变,所述第二端的壁厚逐渐增大。 在其中一些实施例中,所述成型凹槽的底壁与侧壁呈倒角设置,所述底面干压上 模的与所述成型凹槽配合的端部的底壁与侧壁也呈倒角设置。 在其中一些实施例中,所述倒角的角度为75°~90°。 附图说明 图1为本发明一实施方式的3D盖板的制备方法的流程图; 图2为本发明一实施例的粉体干压模具的一状态的结构示意图; 图3为图2所示的粉体干压模具的又一状态的剖面结构示意图; 图4为图3所示的粉体干压模具的俯视图; 图5为图3所示的粉体干压模具的仰视图; 图6为图2所示的粉体干压模具的底模的结构示意图; 图7为图6所示的底模的剖面结构示意图; 图8为图2所示的粉体干压模具的上模外框的结构示意图; 图9为图8所示的上模外框的剖面结构示意图; 图10为图2所示的粉体干压模具的立面干压上模的结构示意图; 图11为图10所示的立面干压上模的剖面结构示意图; 图12为图10所示的立面干压上模的侧视图。