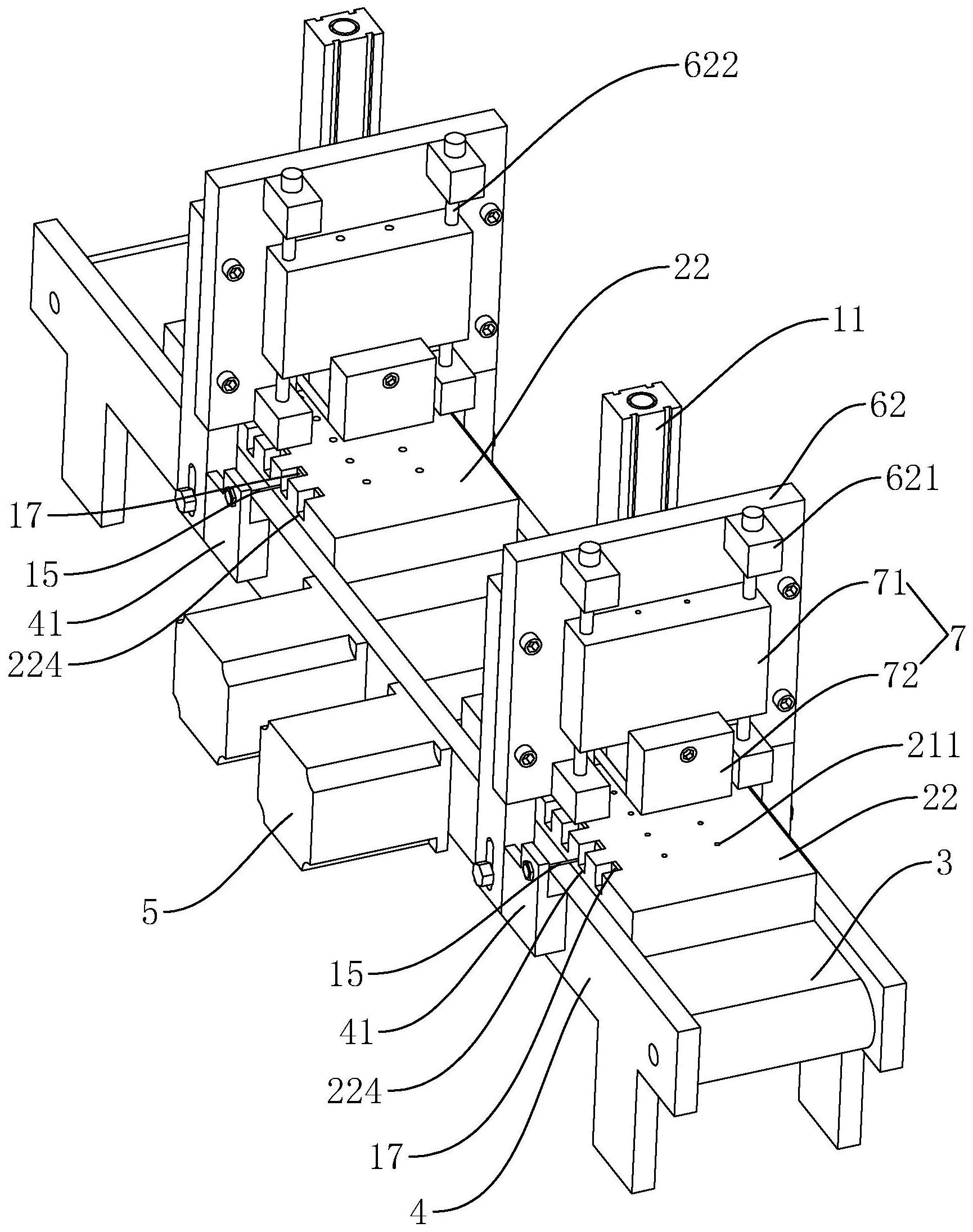
技术摘要:
本发明涉及一种用于直流插头管件生产的排料系统,包括机台、用于承接音叉管及拼针的接料模板、用于传输接料模板的传输组件和用于将音叉管及拼针按指定形态传输到接料模板上的排布组件,传输组件和排布组件设置在机台上,接料模板上开设有多个供音叉管和拼针通过的模孔 全部
背景技术:
如图1和图2所示,目前直流插头在生产过程中需在将音叉管18和拼针19放置在注 塑模具20上并进行注塑,从而使音叉管18和拼针19之间形成绝缘的塑料层,形成直流插头 生产过程中的配件管件,操作者后续再对该管件进行接线等加工即可完成直流插头的生 产。 如图1和图3所示,目前为了一次性实现多个配件管件的注塑加工,操作者常通过 一套音叉管18和拼针19自动排料装置来实现对音叉管18和拼针19的批量排布上料,现有的 自动排量装置包括机台1、传送带3、接料模板2和振动盘9,传送带3、振动盘9设置在机台上, 机台1设置有两个,两个机台1上均设置有一个振动盘9和一个传送带3,两个振动盘9分别对 音叉管18和拼针19进行传输,两个振动盘9上分别连接有用于将音叉管18和拼针19传输到 接料模板2上的输料管91,接料模板2在传送带3的传输下平稳移动。 如图1和图3所示,接料模板2上间隔开设有多个供音叉管18和拼针19落下的模孔 21,模孔21与用于注塑的注塑模具20(见图2)上的供拼针19和音叉管18设置的流道孔对准 设置,需要将音叉管18和拼针19装设在接料模板2上时,操作者将接料模板2先放在与用于 传输音叉管18的振动盘9位于同一机台1上的传送带3上,在传送带3的传输下接料模板2移 动至用于传输音叉管18的输料管91下方,当传输音叉管18的输料管91对准接料模板2上的 一模孔21时,在重力作用下音叉管18落到模孔21中,模孔21中的音叉管18挡住输料管91中 的音叉管18,随着传送带3的继续运输,接料模板2顶面挡住输料管91底部,直到输料管91底 部再对准另一模孔21后,音叉管18在振动盘9的传输作用下再落到模孔21中; 当接料模板2上各个模孔21内均装设有音叉管18后,操作者将该接料模板2移动至与用 于传输拼针19的振动盘9位于同一机台1上的传送带3上,接料模板1从用于传输音叉管18的 输料管91下方经过后,接料模板2被传输至用于传输拼针19的输料管91底部,与音叉管18传 输到模孔21中的过程类似,当接料模板2传输至模孔21中的音叉管18中空处对准用于传输 拼针19的输料管91时,在振动盘9的传输作用下拼针19落入模孔21中的音叉管18的中空处 中部,落入模孔21中的拼针19挡住输料管91中的拼针19继续落下,随着传送带3的继续运 输,直到输料管91底部再对准另一模孔21后,拼针19在重力作用下再落到模孔21中; 待一个接料模板2上的模孔21均装有音叉管18和拼针19后,操作者将接料模板2从传送 带3上取下并倒扣在用于对直流插头配件管件进行注塑加工的注塑模具20上,使原先位于 模孔21中的音叉管18和拼针19落在注塑模具20上的流道孔中,操作者即可启动注塑机以对 直流插头的配件管件进行注塑加工。 上述中的现有技术方案存在以下缺陷:用于注塑加工成直流插头配件管件的拼针 直径远小于音叉管直径,当落入模孔中的拼针在运输过程中发生偏移而离开模孔中的音叉 5 CN 111590814 A 说 明 书 2/12 页 管中空处中部时,易导致输料管中再落下一枚拼针,进而导致一个模孔中有不止一个拼针, 操作者在将接料模板上的音叉管和拼针导入到用于注塑的注塑模具上时还需手工将多余 的拼针从接料模板上取下,增加了操作者的工作量。
技术实现要素:
针对现有技术存在的不足,本发明的目的之一是提供一种用于直流插头管件生产 的排料系统,可确保接料模板上的每个模孔中均只存在一个音叉管和一个拼针,操作者不 需在进行注塑加工之前对模板上多余的拼针手动取下,具有可减少操作者工作量的优点。 本发明的目的之二是提供一种排料工艺,具有可减少操作者工作量的优点。 本发明的上述发明目的之一是通过以下技术方案得以实现的: 一种用于直流插头管件生产的排料系统,包括机台、用于承接音叉管及拼针的接料模 板、用于传输接料模板的传输组件和用于将音叉管及拼针按指定形态传输到接料模板上的 排布组件,所述传输组件和排布组件设置在机台上,所述接料模板上开设有多个供音叉管 和拼针通过的模孔,所述排布组件上连接有不少于两个分别用于容纳传输组件传输的音叉 管和拼针的连通件,所述连通件上开设有用于供音叉管或拼针嵌入的第一通孔,所述连通 件上滑动连接有用于挡住第一通孔的挡板,所述挡板上开设有供音叉管或拼针通过的第二 通孔,所述第一弹性件两端分别与挡板和连通件连接,所述连通件上设置有用于驱动挡板 滑动至第一通孔与第二通孔连通以使一根音叉管或拼针通过的驱动组件,所述挡板上设置 有在驱动挡板在滑动完成后复位至重新挡住第一通孔的第一弹性件,所述传输组件上设置 有检测模块,所述检测模块电连接有处理器,所述驱动组件与处理器电连接,所述检测模块 用于检测接料模板的移动位置并输出检测信号,所述处理器用于接收检测信号并在模孔与 第一通孔对准时输出运行触发信号,所述驱动组件用于接收运行触发信号并输出运行信 号。 通过采用上述技术方案,系统运行时,音叉管、拼针分别在排布组件的传输下有序 传输到连通件上,挡板挡住了第一通孔,音叉管、拼针滞留在第一通孔中,在传输组件的传 输下接料模板先移动至承接有音叉管的连通件处,接料模板上的一组模孔与第一通孔对准 时,处理器输出运行触发信号,驱动组件启动并带动挡板移动,第一弹性件弹性压缩形变, 容纳有音叉管的第一通孔与第二通孔相通,音叉管通过第一通孔、第二通孔传输到模孔中, 挡板滑动完成后在第一弹性件的弹力作用下挡板复位并重新挡住第一通孔,在传输组件的 传输下接料模板继续传输并当下一组模孔对准第一通孔时处理器再次输出运行触发信号, 随着传输组件的运行接料模板上的模孔均装设有音叉管; 接料模板随传输组件的传输移动至承接有拼针的连通件处,当接料模板上装有音叉管 的一组模孔对准内设有拼针的第一通孔时,处理器输出运行触发信号,驱动组件启动并带 动挡板移动,第一弹性件弹性形变,容纳有拼针的第一通孔与第二通孔相通,拼针通过第一 通孔、第二通孔传输到已装设有模孔中,挡板滑动完成后在第一弹性件的弹力作用下挡板 复位并重新挡住第一通孔,在传输组件的传输下接料模板继续传输并当下一组模孔对准第 一通孔时处理器再次输出运行触发信号,随着传输组件的运行接料模板上的模孔均装设有 音叉管及拼针。 由于用于传输音叉管和拼针的第一通孔并非同一条第一通孔,故两组第一通孔可 6 CN 111590814 A 说 明 书 3/12 页 设置为仅可供单个拼针和仅可供单个音叉管移入的第一通孔,而用于供拼针和音叉管通过 的第二通孔亦可开设成仅可供单个拼针或仅可供单个音叉管穿过的大小,每次当第一通孔 对准模孔时,处理器输出运行触发信号进而使驱动组件驱动挡板做一次滑动,且在每次滑 动结束后第一弹性件驱动挡板复位至初始位置,即随着每一次第一通孔与模孔的对准均可 使一个音叉管或拼针移入,在使一个音叉管或拼针进入模孔后挡板即会在第一弹性件的弹 力作用下反向滑动至挡住第一通孔,确保接料模板上的每个模孔中均只存在一个音叉管和 一个拼针,操作者不需在进行注塑加工之前对模板上多余的拼针手动取下,减少操作者工 作量。 本发明在一较佳示例中可以进一步配置为:所述传输组件包括传送带和第一连接 架,所述第一连接架设置在机台上,所述传送带设置在第一连接架上,所述第一连接架上安 装有第二连接架,所述连通件与第二连接架沿靠近和远离传送带的方向滑动连接,所述挡 板滑动方向与连通件滑动方向交错,所述连通件与传送带之间存在供接料模板通过的间 隔,所述驱动组件包括驱动连通件往复滑动的驱动件和在随着连通件的滑动带动挡板滑动 的楔形凸起,所述驱动件用于接收运行触发信号并输出运行信号,所述楔形凸起设置在第 二连接架上。 通过采用上述技术方案,初始状态下连通件与传送带、传送带上的接料模板之间 均存在间隙,方便操作者查看接料模板上的拼针和音叉管装设情况,当操作者发现部分已 与第一通孔对准过一次的模孔内缺少音叉管或拼针时操作者可检查排布组件是否出现故 障,进而确保直流插头管件的正常生产加工。 当第一通孔对准一组模孔时,驱动件启动带动连通件朝靠近接料模板的方向滑 动,随着连通件的滑动楔形凸起推动挡板滑动,当连通件抵在接料模板上时第一通孔与第 二通孔对准且相通,音叉管或拼针即可在排布组件的传输下从第一通孔移至模孔内,当一 个音叉管或一个拼针落入模孔后,驱动件驱动连通件反向移动,楔形凸起解除对挡板的推 动,在第一弹性件的弹力作用下挡板反向滑动从而挡住第一通孔,避免更多的音叉管或拼 针从第一通孔中落下; 当连通件抵在接料模板上时第一通孔和第二通孔完全对准、连通,音叉管、拼针方移入 模孔,此时音叉管、拼针需移动的距离最短,音叉管、拼针在移入模孔时的晃动减少,且避免 了音叉管、拼针在移入模孔时从连通件和接料模板之间的间隙中掉出,确保了音叉管准确 落入模孔中,确保了拼针可准确落入模孔中音叉管的中空处。 本发明在一较佳示例中可以进一步配置为:所述第一连接架上设置有用于驱动传 送带转动的电机,所述电机与处理器电连接,所述处理器还用于输出延时停止信号,所述电 机用于接收延时停止信号并在指定延时时间内输出停止信号。 通过采用上述技术方案,当驱动件接收运行触发信号时电机接收延时停止信号, 故连通件滑动时电机停止运行,从而使传送带和传输带上的接料模板停止移动,在连通件 滑动及音叉管、拼针移入模孔的过程中接料模板的静止提高了音叉管、拼针移入模孔的准 确性,避免了连通件滑动及音叉管、拼针移入模孔的过程中由于接料模板的移动而导致音 叉管、拼针移动位置出现偏差,避免音叉管、拼针及接料模板因音叉管、拼针因移动位置偏 差而斜插在接料模板上导致音叉管、拼针或接料模板的受损。 本发明在一较佳示例中可以进一步配置为:所述第一连接架上设置有用于驱动传 7 CN 111590814 A 说 明 书 4/12 页 送带转动的电机,所述电机与处理器电连接,所述处理器还用于输出延时停止信号,所述电 机用于接收延时停止信号并在指定延时时间内输出停止信号。 通过采用上述技术方案,每个连通件对应一个传送带设置,两个连通件分别进行 音叉管的上料和拼针的上料,当一个接料模板上的模孔均装设有音叉管后,该接料模板传 输至另一传送带上,随后操作者可在已空置的传送带上放置另一接料模板,从而提高音叉 管和拼针装满接料模板的速度,且由于各传送带均有独立的电机驱动运行,当一连通件上 的第一通孔对准模孔时,该连通件对准的传送带单独停止运行,待拼针落入音叉管的中空 处后该传送带再次运行,而再次器件其他传送带均不受该传送带停止运行的干涉,进而确 保每个传输带上的接料模板均可独立正常进行音叉管或拼针的装设。 本发明在一较佳示例中可以进一步配置为:所述驱动件包括气缸,所述气缸设置 在第二连接架上,所述气缸的活塞杆上设置有滑块,所述滑块与连通件固定,所述第二连接 架上开设有滑槽,所述滑块与滑槽沿靠近、远离传输带的方向滑动连接。 通过采用上述技术方案,气缸通常连接有电磁阀,当电磁阀接收到运行触发信号 时,气缸运行一次,气缸的活塞杆伸出带动滑块滑动,当滑块滑动至滑槽尽头时气缸活塞杆 停止伸出,此时挡板在楔形凸起的推动下滑动至第一通孔与第二通孔对准且相通,随后气 缸的活塞杆回缩,带动滑块反向滑动至初始位置;滑槽为滑块的滑动和连通件的滑动设定 了轨迹,避免了在气缸运行过程中因连通件重心与滑块重心不同而导致连通件、滑块的摆 动,避免摆动导致气缸活塞杆受损,同时滑槽为滑块的滑动限定的滑动距离,操作者不需通 过程序控制来设定气缸活塞杆的伸出长度,操作方便。 本发明在一较佳示例中可以进一步配置为:所述挡板上转动连接有用于与第二连 接架设有楔形凸起的一面及楔形凸起抵接的滚动体。 通过采用上述技术方案,连通件滑动带动挡板同步移动,滚动体与第二连接架抵 接并转动,通过滚动摩擦力小于滑动摩擦力的原理使连通件、挡板移动更加流畅,同时滚动 体与楔形凸起抵接推动挡板滑动时滚动体保持转动,提高了挡板滑动的流畅程度。 本发明在一较佳示例中可以进一步配置为:所述机台上设置有第三连接架,所述 第三连接架与第一连接架之间沿传送带传输方向存在间隔,所述第三连接架上设置有用于 承接完成音叉管和拼针设置后的接料模板的承接台,所述承接台与第三连接架沿传送带传 输方向滑动连接,所述承接台上设置有限制承接台滑动的限位件。 通过采用上述技术方案,完成音叉管和拼针设置后的接料模板在传送带的串熟悉 啊移动到承接台上,操作者即可从承接台上将接料模板取下并将承接模板上的音叉管和拼 针转移至注塑模具上,位于承接台上的接料模板在脱离传送带后停止移动,避免了由于操 作者操作的延迟而导致装有音叉管和拼针的接料模板从传送带上掉落。 本发明在一较佳示例中可以进一步配置为:所述接料模板侧部开设有多个凹陷, 所述凹陷沿传送带传输方向间隔设置,所述模孔在接料模板上沿传送带传输方向间隔设置 有多排,所述凹陷设置数量与模孔设置排数相等,各所述凹陷沿传送带传输方向的间距等 于各排所述模孔沿传送带传输方向的间距,所述检测模块实体设置在第一连接架上,所述 检测模块实体的检测端随接料模板的移动而检测到接料模板的凹陷处时输出检测信号。 通过采用上述技术方案,检测模块实体的检测端对准凹陷时处理器输出运行触发 信号,带动气缸运行一次,使每个第一通孔中有一个音叉管或拼针进入该第一通孔对准的 8 CN 111590814 A 说 明 书 5/12 页 模孔,且即使更换了不同规格的接料模板导致接料模板的模孔数量不同,操作者不需更改 处理器内的程序设置亦可正常对该不同规格的接料模板进行音叉管和拼针的上料,操作方 便。 本发明在一较佳示例中可以进一步配置为:所述接料模板包括主模部和滑动部, 所述滑动部滑动连接在主模部上,所述模孔包括第三通孔和第四通孔,所述第三通孔开设 在主模部上并穿透主模部,所述第四通孔开设在滑动部上并穿透滑动部,所述主模部上设 置有用于使滑动部持续挡住第三通孔的第二弹性件,所述第二弹性件两端分别与滑动部和 主模部连接。 通过采用上述技术方案,当检测模块检测到凹陷时第三通孔对准第一通孔,则当 接料模板上装设满音叉管和拼针后音叉管和拼针均位于第三通孔内,操作者再将接料模板 移动至注塑模具上并滑动滑动部,使第四通孔对准注塑磨具上的流道孔,随后操作者滑动 滑动部,使滑动部解除对第三通孔的阻挡并滑动至第三通孔对准第四通孔,第三通孔和第 四通孔连通,在重力作用下音叉管和拼针落入注塑模具上的流道孔中,操作者不需将接料 模板倒扣在注塑模具上即可将音叉管和拼针装入注塑模具,避免在接料模板倒扣的过程中 部分音叉管或拼针掉落。 本发明的上述发明目的之二是通过以下技术方案得以实现的: 一种用于直流插头管件生产的排料工艺,其采用了上述任意一项所述的用于直流插头 管件生产的排料系统,包括如下步骤: S1、排布组件将音叉管和拼针传输至第一通孔中,挡板挡住传输至第一通孔中的音叉 管和拼针; S2、在传送带的传输下接料模板移动至装有音叉管的连通件处,检测模块检测接料模 板的移动并输出检测信号,处理器接收检测信号并判断供音叉管通过的第一通孔是否对准 模孔; S3、当供音叉管通过的第一通孔对准一排模孔时处理器输出运行触发信号,驱动件启 动,连通件向靠近接料模板的方向移动; S4、楔形凸起推动挡板滑动,第一通孔和第二通孔相通,一音叉管从第一通孔传输至模 孔中; S5、第一弹性件的弹力作用下挡板移动至重新挡住第一通孔,接料模板传送至容纳有 音叉管的第一通孔对准下一模孔时,上述步骤S3-S4重复,多次重复使接料模板上所有模孔 中均嵌入有音叉管; S6、在传送带的传输下容纳有音叉管的接料模板移动至容纳有拼针的连通件处,检测 模块检测接料模板的移动并输出检测信号,处理器接收检测信号并判断供拼针通过的第一 通孔是否对准模孔; S7、当供拼针通过的第一通孔对准一排模孔时处理器输出运行触发信号,驱动件启动, 连通件向靠近接料模板的方向移动; S8、楔形凸起推动挡板滑动,第一通孔和第二通孔相通,一拼针从第一通孔移至位于模 孔中的一音叉管的中空处; S9、传送带-3-再启动且在第一弹性件的弹力作用下挡板移动至重新挡住第一通孔,接 料模板传送至容纳有拼针的第一通孔对准下一模孔时,上述步骤S7-S8再次重复,如此重复 9 CN 111590814 A 说 明 书 6/12 页 使接料模板上所有模孔中均嵌入有一个音叉管和一个拼针。 通过采用上述技术方案,通过检测模块的检测和处理器的控制,每次第一通孔对 准模孔时驱动组件自动运行以驱动连通件移动以及挡板的以滑动,以使每一个模孔中均装 设有一个音叉管和一个拼针,在使一个音叉管或拼针进入模孔后挡板即会在第一弹性件的 弹力作用下反向滑动至挡住第一通孔,确保接料模板上的每个模孔中均只存在一个音叉管 和一个拼针,操作者不需在进行注塑加工之前对模板上多余的拼针手动取下,减少操作者 工作量。 综上所述,本发明包括以下至少一种有益技术效果: 1.每次当第一通孔对准模孔时,处理器输出运行触发信号进而使驱动组件驱动挡板做 一次滑动,且在每次滑动结束后第一弹性件驱动挡板复位至初始位置,即随着每一次第一 通孔与模孔的对准均可使一个音叉管或拼针移入,在使一个音叉管或拼针进入模孔后挡板 即会在第一弹性件的弹力作用下反向滑动至挡住第一通孔,确保接料模板上的每个模孔中 均只存在一个音叉管和一个拼针,操作者不需在进行注塑加工之前对模板上多余的拼针手 动取下,减少操作者工作量; 2.当连通件抵在接料模板上时第一通孔和第二通孔完全对准、连通,音叉管、拼针方移 入模孔,此时音叉管、拼针需移动的距离最短,音叉管、拼针在移入模孔时的晃动减少,且避 免了音叉管、拼针在移入模孔时从连通件和接料模板之间的间隙中掉出,确保了音叉管准 确落入模孔中,确保了拼针可准确落入模孔中音叉管的中空处; 3.连通件滑动时电机停止运行,从而使传送带和传输带上的接料模板停止移动,在连 通件滑动及音叉管、拼针移入模孔的过程中接料模板的静止提高了音叉管、拼针移入模孔 的准确性,避免了连通件滑动及音叉管、拼针移入模孔的过程中由于接料模板的移动而导 致音叉管、拼针移动位置出现偏差,避免音叉管、拼针及接料模板因音叉管、拼针因移动位 置偏差而斜插在接料模板上导致音叉管、拼针或接料模板的受损。 附图说明 图1是