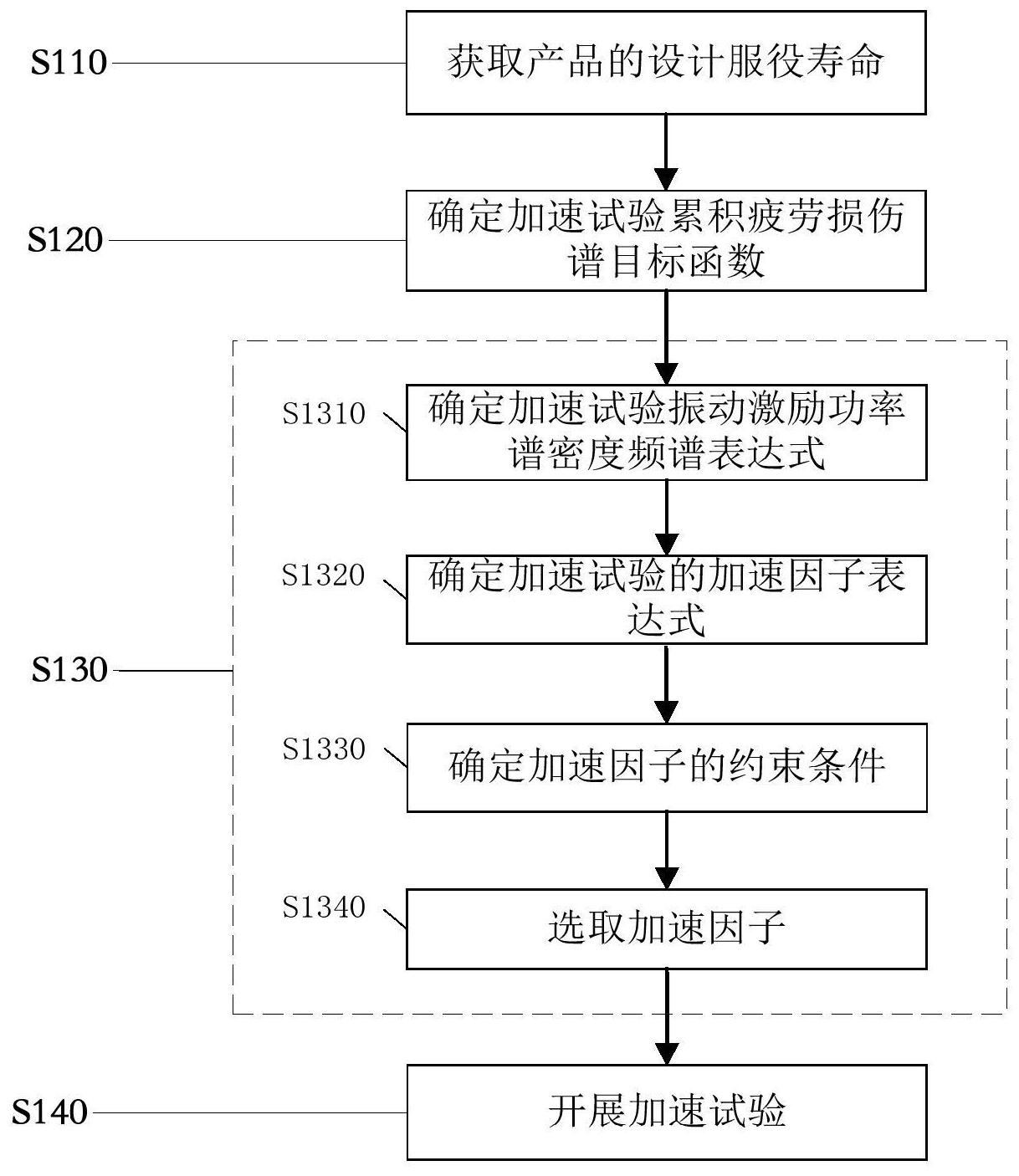
技术摘要:
本发明提供了一种随机振动疲劳的加速试验方法及系统,该方法包括:根据获取的待试验产品的设计服役寿命和实测的振动激励功率谱密度频谱,基于疲劳损伤谱理论确定所述待试验产品的累积疲劳损伤谱目标函数式,进而依据加速试验前后疲劳损伤等效原理,获取加速试验加速因 全部
背景技术:
基于设备的故障和失效统计数据可以得知:设备产品的振动与冲击因素引起的故 障和失效占比颇高,成为影响设备产品性能和可靠性的关键因素之一,在产品设计、开发过 程中对产品振动环境适应能力和可靠性进行分析与评估成为不可或缺的环节,但基于实际 环境振动载荷来模拟整个寿命周期的手段不易实现,需通过开展振动疲劳加速试验来模拟 整个寿命周期的振动激励过程,基于合理的成本对产品潜在的故障与失效风险进行快速、 准确地评估,为产品改进与优化设计提供指导。 目前产品振动疲劳加速试验的技术主要采用基于Miner线性累积损伤疲劳理论, 通过提高振动幅值,缩短试验时间,实现等效加速试验或通过采集结构危险位置的应变谱, 通过雨流计数方法得到损伤时间历程曲线,然后基于损伤历程曲线对应变谱进行编辑处 理,进而借助重构技术生成用于加速试验的载荷谱。但上述现有技术仅能实现对具有单种 输入振动工况的产品进行加速试验,无法实现对多种输入工况产品的试验,不具通用性;同 时试验资源损耗过高,无法适用于大规模的产品加速试验。
技术实现要素:
为解决上述问题,本发明提供了一种随机振动疲劳的加速试验方法,在一个实施 例中,所述方法包括: 步骤S1、根据待试验产品的设计技术要求获取所述待试验产品的设计服役寿命 Ts; 步骤S2、利用所述待试验产品的Ts和实测的振动激励功率谱密度频谱G(f)获取所 述待试验产品的累积疲劳损伤谱目标函数式; 步骤S3、根据所述累积疲劳损伤目标函数式基于加速试验前后疲劳损伤等效原 理,确定待试验产品的加速试验开展时间Tt的约束条件和加速试验加速因子α; 步骤S4、根据确定的所述Tt的约束条件和所述α对所述待试验产品开展加速试验, 获取所述待试验产品的加速试验结果; 其中,所述待试验产品包括具有多种振动工况的产品。 优选地,所述步骤S2中的所述待试验产品的累积疲劳损伤谱目标函数式如下: 式中,∑FDS(f)为所述待试验产品的累积疲劳损伤谱,FDSi(f)为所述待试验产品 第i种振动工况对应的疲劳损伤谱,x为所述待试验产品具有的振动工况个数,K为单自由度 5 CN 111597673 A 说 明 书 2/11 页 系统刚度,Q为动态放大因子,Ts,i为待试验产品第i种振动工况对应的设计服役寿命,f为随 机振动激励频率,Gi(f)为待试验产品第i种振动工况的振动激励功率谱密度频谱,m和C为 材料疲劳特性参数,,Γ函数定义为 进一步地,所述步骤S3包括: 步骤S3-1、根据所述待试验产品的累积疲劳损伤目标函数式确定待试验产品加速 试验振动激励功率谱密度频谱Gt(f)的表达式; 步骤S3-2、根据所述Gt(f)的表达式,利用待试验产品实测振动激励下的疲劳损伤 谱与加速试验振动激励下疲劳损伤谱一致的原理确定待试验产品加速因子α的表达式; 步骤S3-3、根据所述α的表达式和所述待试验产品的累积疲劳损伤谱目标函数式 确定待试验产品的试验开展时间的约束条件和α的约束条件; 步骤S3-4、利用所述α的约束条件确定待试验产品α的值。 进一步地,所述步骤S3-1中的所述加速试验振动激励功率谱密度频谱Gt(f)的表 达式如下: 式中,∑FDS(f)为所述待试验产品的累积疲劳损伤谱,f为随机振动激励频率,K为 单自由度系统刚度,Q为动态放大因子,m和C为材料疲劳特性参数,Tt为加速试验开展时间, Γ函数定义为 进一步地,所述步骤S3-2中的所述待试验产品加速因子α的表达式如下: 式中,As为待试验产品实测振动激励下的加速度均方根值;At为加速试验振动激励 下的加速度均方根值,Gs(f)为待试验产品实测振动激励下的振动激励功率谱密度频谱。 进一步地,所述步骤S3-3包括: 根据加速试验振动循环次数Nt大于高低周疲劳转折点循环次数Np的原则确定所述 Tt的第一约束条件为下式: T ≥N /f t p 根据所述Tt的第一约束条件确定所述α的第一约束条件为下式: 根据随机振动载荷作用下结构应力响应近似服从高斯分布的原则确定所述α的第 二约束条件为下式: 根据所述α的第二约束条件确定所述Tt的第二约束条件为下式: 6 CN 111597673 A 说 明 书 3/11 页 根据所述α的第一约束条件和第二约束条件可得α的极限约束条件如下: 根据所述Tt的第一约束条件和第二约束条件确定Tt的极限约束条件如下: 上式中,αmax为待试验产品的加速因子最大值,σs为待试验产品的材料屈服强度, σ1s为待试验产品的疲劳破坏危险区域实测振动激励下的1σ应力值,Np为高低周疲劳转折点 循环次数,Ttmin为待试验产品的加速试验开展时间最大值,f 为振动激励频率的平均值。 在一个实施例中,在所述步骤S1之后,还包括修正所述设计服役寿命Ts的步骤: 根据长寿命产品的服役寿命内振动循环次数等于恒幅疲劳极限点循环次数的原 则修正待试验产品的Ts,如下式: Tsr=min{Nl/f ,Ts} 式中,Tsr为待试验产品修正后的设计服役寿命,Nl为待试验产品的恒幅疲劳极限 点循环次数,f 为振动激励频率的平均值。 在一个实施例中,在所述步骤S3之后,还包括利用所述步骤S3中确定的α的值对待 试验产品进行振动疲劳仿真分析的步骤: 通过仿真计算待试验产品实测振动激励下的疲劳损伤值和加速振动试验激励下 的疲劳损伤值; 若计算得到的两者的值不一致,则重新选取待试验产品α的值,直至满足实测振动 激励下的疲劳损伤值与加速振动试验激励下的疲劳损伤值一致。 在一个实施例中,所述方法还包括: 分别获取待试验产品疲劳破坏危险区域在实测振动激励预试验和加速振动激励 预试验中的频响特性曲线,并根据获取的所述频响特性曲线修正非线性频响区间的加速试 验振动激励功率谱密度频谱。 另外,根据本发明其他方面,还提供了一种随机振动疲劳的加速试验系统,所述系 统执行上述的一个或多个实施例中所述的方法。 与最接近的现有技术相比,本发明还具有如下有益效果: 本发明提供的一种随机振动疲劳的加速试验方法,通过根据待试验产品的设计服 役寿命和振动激励功率谱密度频谱确定待试验产品的累积疲劳损伤谱目标函数,计算获取 待试验产品开展加速试验的时间和加速因子的约束条件,进而确定加速因子合理取值并开 展加速试验获取待试验产品的加速试验结果。本发明的技术方案在有效实现多工况待试验 产品的等效加速试验的前提下,有效提升了产品加速试验结果的可靠性,同时控制了产品 加速试验过程的成本,有助于产品进行性能优化和产品所属技术领域的稳定发展。 7 CN 111597673 A 说 明 书 4/11 页 附图说明 附图用来提供对本发明的进一步理解,并且构成说明书的一部分,于本发明的实 施例共同用于解释本发明,并不构成对本发明的限制。在附图中: 图1是本发明实施例一提供的随机振动疲劳的加速试验方法的流程示意图; 图2是本发明实施例二提供的随机振动疲劳的加速试验方法的材料S-N曲线示意 图 图3是本发明实施例二提供的随机振动疲劳的加速试验方法的流程示意图; 图4是本发明实施例三提供的随机振动疲劳的加速试验方法的流程示意图; 图5是本发明实施例四提供的随机振动疲劳的加速试验方法的流程示意图; 图6是本发明实施例提供的随机振动疲劳的加速试验系统的结构示意图。