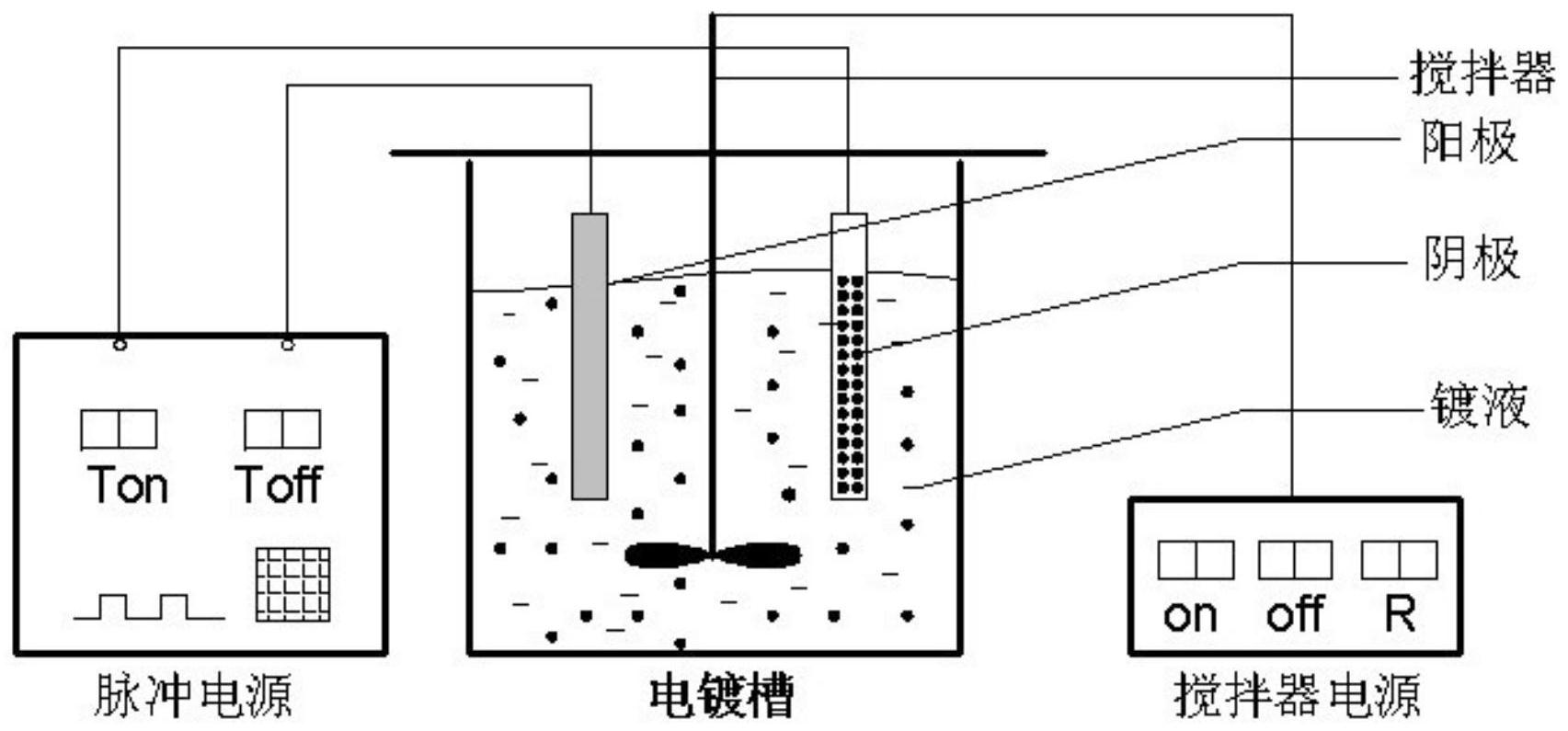
技术摘要:
本发明提供了一种铝合金表面脉冲电沉积Ni‑SiC复合镀层的方法,其中电镀液包括:柠檬酸钠、乙二胺四乙酸二钠、硫酸镍、氯化镍、硼酸、碳化硅颗粒和表面活性剂硬脂酸钠;其中所述电镀液pH为5‑6;所述电沉积过程中进行机械搅拌;所述电沉积的电流密度为15‑22A/dm2。本 全部
背景技术:
近几年来,随着我国工业技术的迅速发展,为了进一步提高零部件的生产效率和 降低生产成本,工业领域对材料的性能提出了更高,更苛刻的要求。例如,高强度、硬度、耐 摩擦磨损性能和抗腐蚀能力等,同时在最大的提高零件性能的同时,最少的排放对环境有 害的污染物。在条件较为恶劣的工矿领域,为了对铝合金设备实施更好的保护,会在铝合金 产品的表面制备一层保护膜,来提升其表面硬度、耐磨性能和耐蚀性能,进而来对铝合金产 品进行更好的保护。 目前,为了提高铝合金产品的表面硬度、耐磨性能、耐蚀性能及其它机械性能,通 常会对铝合金表面进行电镀处理,现有的电镀工艺有:Ni-SiC复合电镀、镀铬等。铬金属镀 层表现出众多优越性能,如高耐蚀性能、耐磨性能和硬度等,以及在高温下低氧化速率和较 好的强度保持性,解决了铝合金在使用程中出现的磨损问题,提高了其使用寿命。但在电镀 铬过程中产生的气体和废液会对人体和环境产生巨大的危害,因此需要寻找一种绿色健康 的新工艺来代替镀铬。 Ni-SiC复合镀是使用电沉积或化学镀的方法使金属Ni与SiC颗粒共同沉积而获得 复合材料的工艺过程。其作为一项比较新的材料表面处理技术,已成为提高材料表面耐磨、 硬度、耐腐蚀等性能的重要方法。相对于镀铬工艺而言,Ni-SiC复合镀符合国家清洁生产的 理念,其工艺过程避免了对人体和环境的污染物,降低了电镀的成本,同时Ni-SiC复合镀层 在硬度、耐磨、耐蚀等主要性能上相当或优于铬金属镀层。 目前,有许多文献和专利介绍了铝合金表面沉积Ni-SiC复合镀层的制备方法及其 使用的电镀液;专利CN109797413《Ni-P-SiC复合镀层电镀液及铝合金基体的电镀方法》中 使用氨基磺酸盐型镀液,在镀液pH值为1.5,通过直流电源提供3.5A/dm2的电流进行电镀, 而在《耐磨Ni-SiC复合镀层的研制及应用》中提出了在氨基磺酸盐型镀液体系下,当电流小 于2A/dm2时很难保证镀层中碳化硅的含量。 中国专利CN105506526《铝合金表面Ni-SiC复合镀层的制备方法及其电镀液》中采 用恒直流电源,通过空气搅拌的方式进行电镀,其使用的电镀液酸性较强,前处理采用了二 次浸锌来提高镀层与铝合金基体的结合力。 在电镀领域中,生产和试验过程中很少使用过低的阴极电流密度。随着阴极电流 密度的增大,阴极的极化作用也随之增大,镀层结晶也随之变得细致紧密,而在文献报道的 电镀过程中电流密度上限一般维持在5-10A/dm2范围内;对于使用不同类型的镀液来说,阴 极上的电流密度不能过大,不能超过允许的上限值,否者会严重影响镀层的质量。在文章 《高频脉冲电沉积Ni-SiC纳米复合镀层的制备及性能研究》中,实验中电源施加的频率范围 为20~140kHz,而使用的电流密度上限为5A/dm2,当电流密度为5A/dm2时镀层已开始严重起 3 CN 111607816 A 说 明 书 2/5 页 泡、不能成型。 因此,为了降低了电镀成本,避免电镀过程中出现的Ni-SiC复合镀层组织粗大,颗 粒分布不均匀和镀层与基体结合力不强等问题,急需一种新型的电沉积Ni-SiC复合镀层的 方法。
技术实现要素:
为解决现有技术的缺点和不足之处,本发明的目的在于提供一种铝合金表面脉冲 电沉积Ni-SiC复合镀层的方法。该方法通过确定铝合金的前处理工艺、Ni-SiC复合电镀的 镀液配方和参数等条件,使用脉冲电沉积技术,在镀液酸性较弱的体系中,使用机械搅拌, 施加高的电流密度在铝合金表面沉积一层SiC含量高、分布均匀,与基体结合力好的Ni-SiC 复合镀层及技术对加快实际工业生产效率和降低成本具有重要意义。 本发明的目的通过下述技术方案实现: 一种铝合金表面脉冲电沉积Ni-SiC复合镀层的方法,其中所用电镀液包括: 其中所述电镀液pH为5-6; 所述电沉积过程中进行机械搅拌; 所述电沉积的电流密度为15-22A/dm2。 在电镀液配制完成后,可使用搅拌器对其进行机械搅拌,时间优选为3-5h,搅拌速 率为150r/min,使碳化硅颗粒均匀的分布在镀液中。 优选的,所述脉冲的频率为800~1200Hz,占空比为0.6~0.8。 优选的,所述机械搅拌速率为120-200r/min。 优选的,所述脉冲电沉积温度为40-50℃,时间为30-60min。 优选的,其中SiC的粒径为60nm-25μm。 在电镀过程中电流密度的大小是决定电镀效率的决定性因素,在以往的电镀过程 中,由于使用不同的镀液,电镀过程中电流密度上限一般维持在5~10A/dm2范围内,效率 低,生产速度慢,间接的提高了生产成本。而在使用本发明配制的镀液进行电镀时,当电流 密度维持在15~22A/dm2之间时,镀液未因电流密度大而出现分解现象,在铝合金样品表面 制备的镀层成形性好。 在现有的镀液中使用了硬脂酸钠作为表面活性剂。硬脂酸根离子的羟基氧原子上 存在孤对电子,而Ni原子外围电子排布为3d84s2,d轨道有两个空位,易接受电子,因此孤对 电子可进入空余的d轨道形成配位共价键而使硬脂酸离子化学吸附在Ni-SiC镀层表面,并 4 CN 111607816 A 说 明 书 3/5 页 通过膜外长链烷烃基交织成具有物理隔绝性和斥水性的网状结构。同时,硬脂酸根离子可 在硅烷膜的空隙处与镀层Ni或硅烷分子中的硅醇基发生反应,从而使硅烷膜更致密、更均 匀。Ni-SiC镀层表面复合膜的疏水和隔绝腐蚀介质的能力更强,因而能给予镀层更好的耐 蚀性。 本发明使用的是脉冲复合电沉积技术来制备Ni-SiC复合镀层,在使用其它直流电 镀时,由于金属离子趋近阴极不断被沉积,因而不可避免地造成析氢和浓差极化,导致镀层 不均匀致密。而由于脉冲复合电沉积技术是利用电流或电压脉冲的张驰,增加阴极的活化 极化和降低阴极的浓差极化,从而达到提高沉积层的纯度、密度、均匀度,并降低镀层空隙 率的目的。同时,脉冲复合电沉积技术操作简单,成本低廉,电镀效率高。 本发明中,在脉冲复合电沉积技术制备Ni-SiC复合镀层的电镀过程中,相较于其 它直流电源在低pH条件下的电镀技术,电镀前进行二次浸锌等前处理,在低酸性条件下的 镀液中,通过控制镀液中柠檬酸钠、乙二胺四乙酸二钠的含量、脉冲电源的频率和占空比参 数来提高镀层与基体的结合力。 本发明适当增加硫酸镍和氯化镍的浓度,同时降低镀液中碳化硅的浓度,能以较 高的电镀速率获得细化致密复合镀层。 本发明中,通过控制硼酸量的加入进而调节镀液的pH值。 本发明在电镀过程中采用机械搅拌,搅拌速率优选为120-200r/min,使碳化硅纳 米颗粒在镀液中均匀分散,避免团簇现象的产生,使镀层更加致密均匀。 本发明提供的铝合金表面脉冲电沉积Ni-SiC复合镀层的方法能够在铝合金表面 制备出一层孔隙率小、结合能力强、碳化硅颗粒含量高且分布均匀的Ni-SiC复合镀层。其具 有较高的显微硬度及良好的耐磨性能和耐蚀性能。 附图说明 图1是本发明实施例的实验装置示意图。 图2是本发明实施例制备的Ni-SiC纳米复合镀层的微观表面形貌图。 图3是本发明实施例制备的Ni-SiC微米复合镀层的微观表面形貌图。 图4是本发明实施例制备的Ni-SiC微纳米复合镀层的显微硬度柱状图。 图5是本发明实施例制备的Ni-SiC微纳米复合镀层的EIS曲线图。 图6是本发明实施例制备的Ni-SiC微纳米复合镀层的Tafel曲线图。