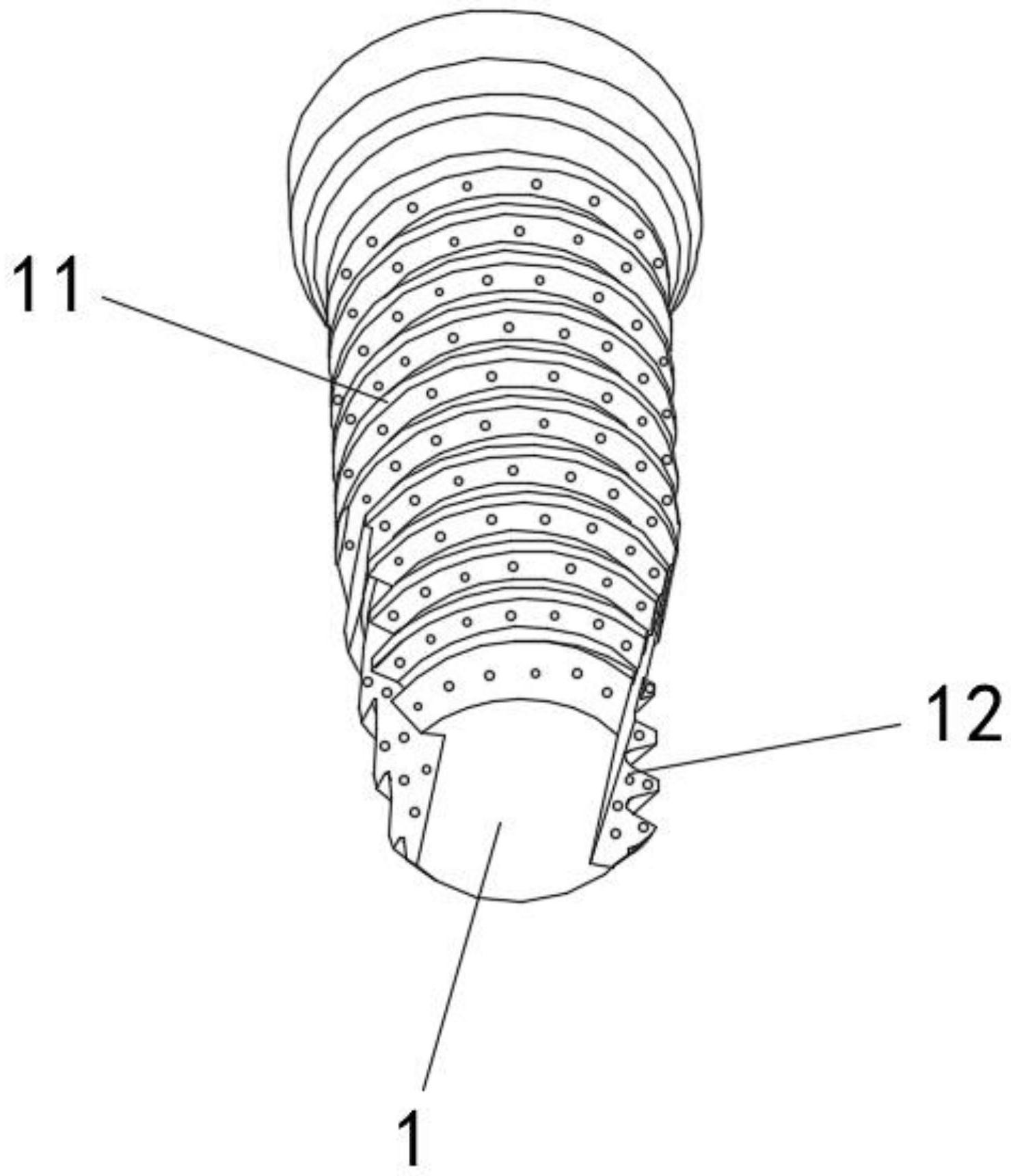
技术摘要:
本发明公开了一种陶瓷种植体的制备方法,采用的造粒粉A和造粒粉B的主要成分均为3mol%钇稳定氧化锆粉,区别为在作为表面材料的造粒粉B中添加了颗粒状造孔剂,所以造粒粉A和造粒粉B的结合性好,通过分层加料后,可同步成型,烧结制得的种植体既能保持氧化锆良好的力学性 全部
背景技术:
缺牙修复目前主要有三种方法,即活动假牙、烤齿牙和种植牙。活动假牙简单、便 宜,但舒适度、美观度和咀嚼效果都非常差。烤齿牙是较好的修复方式,但缺少一颗牙就要 把两边的健康牙磨掉,且没有牙根刺激作用,牙槽会慢慢萎缩。种植牙是目前兼美观和功能 性最好的牙列缺损修复的方式之一。 随着生活水平和审美要求的不断提高,种植义齿修复已成为口腔修复的重要组成 部分。原有钛种植体由于伪影、色泽、种植体周围炎等问题,氧化锆种植体成为种植体发展 的趋势。氧化锆作为种植体牙根材料具有良好的生物相容性和物理性能,经过合理的外科 手术将植体植入颌骨,可以形成种植体与骨组织在分子水平上的结合,在生理性质咬合力 的作用下,有活化的细胞在起作用,动态矿化,改进植体的稳定性。这种结合是生理性的,利 用的是口腔组织的再生和愈合能力,具体来说,种植体植入颌骨后,会依靠分化中的骨细胞 向种植体表面迁移、黏附、增殖和分化,并对种植体表面进行改造。随后向成骨细胞分化,成 骨细胞分泌大量基质和生长因子并继而发生钙化,参与骨的重建。这就要求氧化锆种植体 既骨有良好的稳定性,合适的硬度和弹性模量、较高的力学性能和韧性,同时表面需有良好 的孔隙。 为了提高种植体表面粗糙度,其表面改性处理有多种类型,包括喷涂、喷砂、酸蚀 和激光刻蚀等,但这些表面改性处理方法仍存在许多不足。当种植体植入到口腔中后,在力 学环境和生物液体侵蚀的共同作用下,涂层容易脱落、溶解,造成材料的生物活性降低、使 用寿命缩短。此外,由于种植体的硬度较高,采用喷砂、酸蚀和激光刻蚀的方法不仅成孔难 度较大,对种植体的孔隙控制性也较差,口腔组织与种植体的结合性较低。
技术实现要素:
本发明的目的在于提供一种陶瓷种植体的制备方法,采用不同原料组分,分层加 料,同步成型,烧结制得的种植体既能保持氧化锆良好的力学性能,又能保证种植体牙根部 表面具有人体牙根相近的孔隙,克服了喷涂、喷丸处理工艺制备的种植体表面与主体结合 不牢固及喷砂工艺制备的种植体对孔隙控制性差的缺点。 为实现上述目的,本发明采用以下技术方案: 一种陶瓷种植体的制备方法,包括以下步骤: S1、配料:将3mol%钇稳定氧化锆粉经过造粒机制成粒径为0.06-0.15mm的造粒粉 A;按重量比将3mol%钇稳定氧化锆粉60-80份、造孔剂20-40份混合均匀,再经过造粒机制 成粒径为0.06-0.15mm的造粒粉B; S2、成型:采用双层加料方法同时将造粒粉A和造粒粉B分别填充到成型模具的中 间层和四周的表面层中,表面层的厚度为总厚度的20%-25%,经干压或冷等静压成型后得 3 CN 111548153 A 说 明 书 2/5 页 到毛坯,成型后的毛坯经去毛刺、调尺寸的修坯加工后得到素坯; S3、烧结:将常温的素坯放入烧结炉中,素坯经过分段升温后,在1500-1530℃的温 度条件下保温40-90min,得到坯体,并将坯体加工至所需尺寸; S4、酸洗:将烧结好的坯体先用去离子水清洗,再用15%盐酸浸泡3-5h,然后20% NaHCO3溶液浸泡1~2h,最后用去离子水清洗; S5、杀菌:将清洗好的坯体烘干、杀菌,最终制得陶瓷种植体。 优选地,步骤S2中的双层加料方法具体为:采用具有同心加料口的双层加料漏斗, 先将双层加料漏斗伸入成型模具底部,再将造粒粉A和造粒粉B分别从双层加料漏斗的中间 加料口和外层加料口填充到成型模具内时,并逐渐将双层加料漏斗上提,当造粒粉A和造粒 粉B填充到成型模具90~95%高度时,继续填充造粒粉B,停止填充造粒粉A,直至将成型模 具填满。 优选地,所述颗粒状造孔剂为400~2000目的壳类活性炭、500~2000目的木质类 活性炭、325~2000目的煤质活性炭或3~50μm的有机高分子造孔剂中的一种或其多种的混 合物。 优选地,所述壳类活性炭为花生壳或椰子壳活性炭;所述木质类活性炭为木材或 竹材活性炭:所述有机高分子造孔剂为PPA、PMMA、PS中的一种或其两种以上的混合物。 优选地,所述种植体外侧壁上设置有外螺纹;所述种植体下端两侧分别设置有止 转口,通过口腔细胞增生到止转口内限制外螺纹回转。 优选地,步骤S2中干压压力为6.0~8.0MPa,保压时间为10~30s。 优选地,所述所述步骤S2中冷等静压压力为50~120MPa,保压时间为300~600s。 优选地,步骤S3中素坯的具体烧结方法为:将常温的素坯放入烧结炉中,经60min 将温度升至320℃后,保温120min;保温结束后,经160min将温度继续升至800℃后,保温 150min;保温结束后,经300min将温度继续升至1200℃后,保温40min;保温结束后,经 300min将温度继续升至1500℃后,保温40-90min;保温结束后,经400min将温度降至700℃ 后,再自然冷却至室温得到坯体。 采用上述技术方案后,本发明与