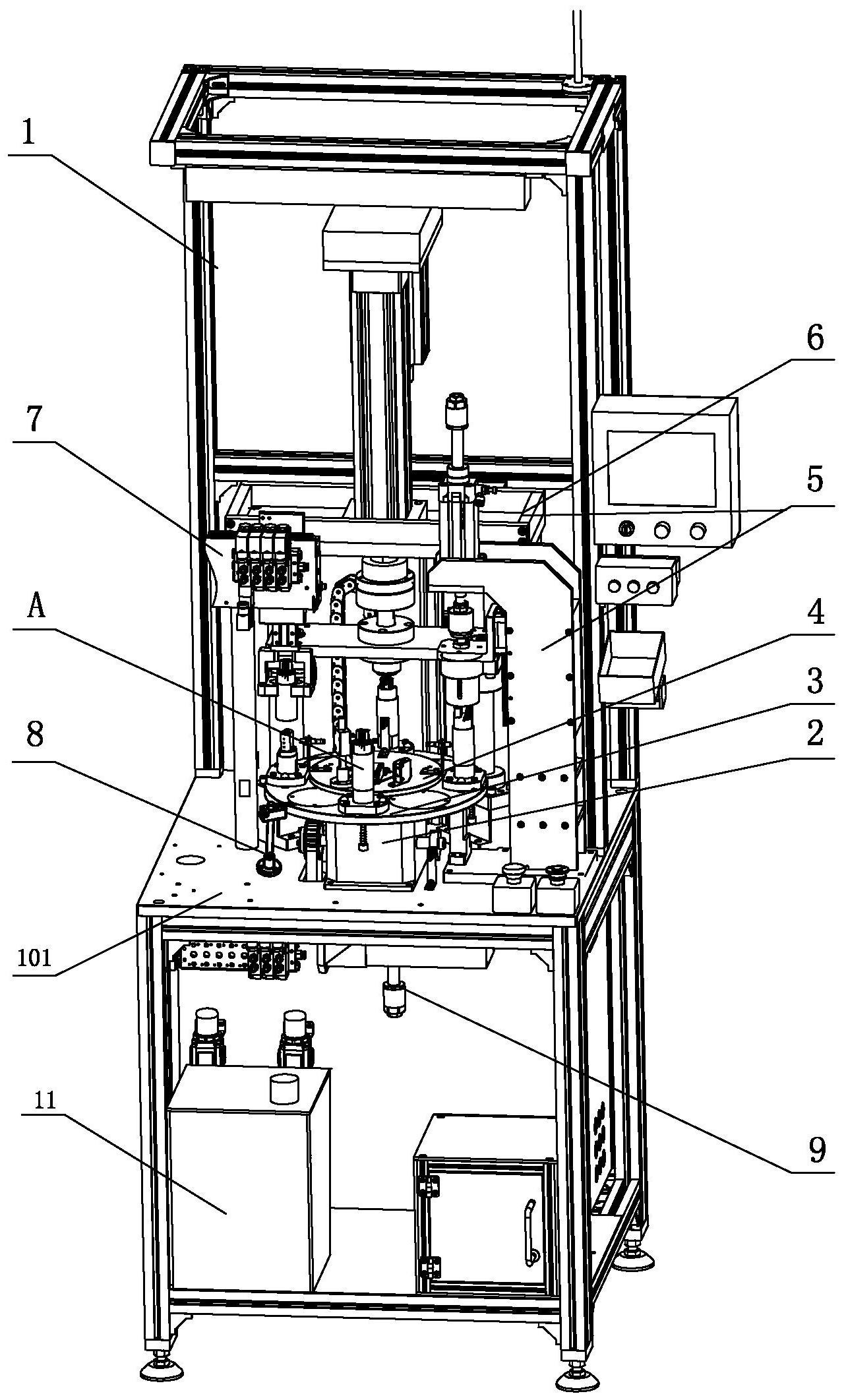
技术摘要:
一种燃油泵磁系统出油座组合件装配装置,包括分序装置、工位转换装置、监测和吸附装置、预压装置、压紧装置、传送装置和顶出装置,分序装置用于推动转盘,将放置于转盘放料组件上的工件按工艺要求进行分步转换;工位转换装置用于工件的定位,监测和吸附装置用于对工件 全部
背景技术:
汽车发动机供油系统的燃油泵磁系统出油座组合件,是指汽车发动机供油系统的 电动燃油泵的磁系统零部件与出油座A1合装后形成的组合件,其中燃油泵的磁系统零部件 包括:极壳A2、撑片A3、磁钢ⅠA4和磁钢ⅡA5,传统的装配工艺流程为:(1)手工将出油座A1与 极壳A2放入工装上,用气动装置将其压紧;(2)手工往压装好的出油座与极壳组件内预装磁 钢ⅠA4和磁钢ⅡA5;(3)手工将预装好磁钢的极壳组件放置于工装上,在两个磁钢之间放入 撑片A3,用气动装置将撑片压入极壳的固定位置完成装配;传统工艺存在的不足之处主要 是: 1.装配工序多、工效低,劳动强度大; 2.装配过程全靠手工,装配质量无法控控制,装配精度难以保证。
技术实现要素:
本发明的目的在于:提供一种燃油泵磁系统出油座组合件装配装置及装配方法, 以克服已有技术所存在的上述不足。 为解决以上技术问题,本发明采取的技术方案是: 一种燃油泵磁系统出油座组合件装配装置,包括机架以及安装在机架上的分序装置、 工位转换装置、监测和吸附装置、预压装置、压紧装置、传送装置、顶出装置和控制系统;所 述分序装置安装于机架的中心部位,包括分序器和减速器,所述分序器通过分序器安装板 安装在机架平台的上部,减速器通过减速器安装板安装在机架平台的下部;分序器的内部 变速齿轮组通过同步轮和同步带与减速器的动力组件传动连接; 所述工位转换装置及监测和吸附装置安装于分序器顶部,所述工位转换装置包括一个 水平布置的圆形工位盘和四个结构相同的放料组件,所述工位盘通过其中心的安装孔Ⅰ安 装在分序器顶部的法兰盘上,四个放料组件均布在工位盘接近圆周的环面上,所述一种燃 油泵磁系统出油座组合件装配装置以工位盘为中心,对应四个放料组件依次布置四个装配 工位:其前侧的放料组件位于第一工位,右侧的放料组件位于第二工位,后侧的放料组件位 于第三工位,左侧的放料组件位于第四工位,工作时分序器带动工位盘逆时针转动,每转动 90度工位转换一次,使装配在第一工位、第二工位和第三工位的工件依次进入下一工位,在 第四工位已完成装配的工件被取出后回到第一工位继续装配下一工件; 所述监测和吸附装置包括一个水平布置的固定圆盘、以及安装在固定圆盘上的光电开 关、真空吸阀、激光传感器和三个结构相同的接近开关;所述固定圆盘通过其中心的安装孔 Ⅱ安装在分序器顶部位于法兰盘中心的圆柱轴上,所述固定圆盘的直径小于工位盘的直 7 CN 111590320 A 说 明 书 2/12 页 径,从而使监测和吸附装置位于工位转换装置的四个放料组件的内圈内;所述真空吸阀和 三个接近开关均布安装在固定圆盘接近圆周的环面上,其位置分别与四个工位的放料组件 对应,其中:真空吸阀与第一工位的放料组件对应,其真空吸阀活塞正对第一工位的放料组 件,三个接近开关的位置分别与第二工位、第三工位和第四工位的放料组件对应并正对该 工位的放料组件,所述光电开关和激光传感器安装在真空吸阀的两侧并正对第一工位的放 料组件;所述激光传感器用于监测第一个工位极壳的装配状态,所述光电开关用于监测第 一个工位出油座及撑片和磁钢的装配状态,三个接近开关分别用于监测监控第二工位、第 三工位和第四工位工件的压装状态; 位于第二工位的预压装置通过底座安装在分序装置右侧的机架平台上,包括动力组件 和预压头组件,预压头组件位于该工位的放料组件的上部,且预压头组件的中心与放料组 件的中心处在同一中心线上; 位于第三工位的压紧装置安装在分序装置正后方的机架平台上,包括动力组件和压头 组件,压头组件位于该工位的放料组件的上部,且压头组件的中心与放料组件的中心处在 同一中心线上; 位于第三工位的顶出装置安装于分序装置正后方的机架平台下部,包括动力组件和撑 片推头,撑片推头伸出机架平台上面正对该工位的放料组件下部的撑片推杆; 所述传送装置安装于压紧装置左侧的机架平台上,包括动力组件和取件夹头,所述动 力组件和取件夹头通过滑轨组件安装在位于放料组件上部的机架上,取件时,取件夹头的 中心与放料组件的中心处在同一中心线上; 所述分序装置、预压装置、压紧装置、传送装置和顶出装置的动力组件以及监测和吸附 装置的真空吸阀、激光传感器、接近开关和光电开关分别与控制系统的气路单元或电路单 元连接; 所述工位转换装置用于对压装工件的支撑定位,所述分序装置用于为工位转换装置的 分步转换提供转动力,并按装配顺序将工位转换装置从第一工位依次分步转换到第二工 位、第三工位和第四工位,所述监测和吸附装置用于工件初装的定位以及工件在各工位装 配状态的监测, 所述预压装置用于对初装工件进行校正预压,所述压紧装置用于对经过预压装置校正 预压的工件进行最后装配压紧,所述顶出装置用于推动放料组件底部的撑片推杆,使工件 内的撑片脱离放料组件、从而使工件与放料组件脱离便于取出,所述传送装置用于将压装 完成的工件从第四工位的放料组件取出传送到另一工序充磁,所述控制系统用于接收监测 和吸附装置反馈的信息,并通过气路和电路的控制实现各装置动力组件工作状态的控制。 其进一步的技术方案是:所述分序器外侧设有与内部变速齿轮组传动连接的同步 轮Ⅰ,所述减速器外侧设有与内部动力组件传动连接的同步轮Ⅱ,所述同步轮Ⅱ与同步轮Ⅰ 位于同一侧并通过同步带传动连接;所述分序器顶面设有固定安装的圆柱轴,分序器顶面 的法兰盘套装在圆柱轴外周并与内部变速齿轮组传动连接,所述法兰盘包括定位圆柱Ⅰ和 限位面Ⅰ,所述工位转换装置的工位盘通过其安装孔Ⅰ安装于法兰盘的限位面Ⅰ上、并以定位 圆柱Ⅰ为定位,用螺栓固紧,所述圆柱轴包括定位圆柱Ⅱ和限位面Ⅱ,所述监测和吸附装置 的固定圆盘通过其安装孔Ⅱ安装在圆柱轴的限位面Ⅱ上、并以定位圆柱Ⅱ为轴心定位,用 螺栓固紧; 8 CN 111590320 A 说 明 书 3/12 页 分序装置工作时,动力组件之伺服电机通过同步轮Ⅱ和同步带带动同步轮Ⅰ和分序器 内部变速齿轮组转动,从而带动安装在法兰盘上的工位转换装置绕圆柱轴逆时针分步转 动。 更进一步:所述放料组件结构相同,包括基座,基座上部为一带台阶的、与出油座 内腔对应的圆柱状结构,包括自下而上的、由大变小的大圆柱、中间圆台和小圆柱,从而构 成用于燃油泵磁系统零部件和出油座的支撑和定位的工作面,其中:大圆柱与中间圆台交 接的圆台面为极壳限位面,小圆柱顶面为出油座限位面,小圆柱两侧构成支撑定位磁钢的 磁钢定位面,小圆柱与中间圆台交接的圆台面左侧设有磁钢限位块,中间圆台右侧设有一 竖向切面,该切面与大圆柱交接处形成一空腔,空腔内装有一撑片定位块,撑片定位块外侧 构成撑片限位面,撑片限位面与大圆柱面内侧之间的空隙构成撑片放置间隙; 所述大圆柱、中间圆台和小圆柱的中心设有通气孔,大圆柱左侧开有与通气孔相通的 吸阀接口,小圆柱两侧的磁钢定位面上对应各开有吸气小孔,装配工作开始时位于第一工 位的真空吸阀活塞与大圆柱的吸阀接口相接,通过真空吸阀抽吸使通气孔内形成负压从而 将放置在磁钢定位面上的磁钢Ⅰ和磁钢Ⅱ吸紧;所述基座下部连接压装支撑块,压装支撑块 开有与上部撑片放置间隙相通的孔道,所述孔道内安装撑片推杆和复位弹簧。 进一步:所述预压装置还包括支撑立臂、滑轨组件和浮动接头Ⅰ,所述支撑立臂通 过底座安装在机架平台上,所述滑轨组件包括安装板、滑轨和滑槽,所述安装板为“L”形结 构,其水平面为安装面,其竖立面的背面设有滑槽,安装板通过滑槽与支撑臂内侧面的滑轨 滑动连接,滑轨下端设有用于调节滑轨组件行程的限位销;预压装置动力组件之标准气缸 安装在支撑立臂的横臂上部,预压装置的预压头组件和浮动接头Ⅰ安装在横臂下部,浮动接 头Ⅰ上端与标准气缸的活塞连接,浮动接头Ⅰ下端连接安装板的安装面,预压头组件连接在 安装面的底面; 所述预压头组件包括导正头、预压头、弹簧和弹簧顶板,所述预压头组件下部的底座上 安装有预压支撑块,预压支撑块的中心与预压头组件的中心处在同一中心线上,工位转换 时所述预压支撑块的顶面与工位盘的底面滑动接触并将工位盘支撑;所述标准气缸包括调 速阀和气路连接口,标准气缸工作时,其活塞推动浮动接头以及安装在安装板Ⅱ上的预压 头组件沿滑轨下压或升起;滑轨组件的运动保证了预压头组件向下垂直运动的平稳性能, 导正头将有可能偏移的出油座导正,预压头下压将出油座预压到位,限位销用于限制预压 的行程。 进一步:所述压紧装置之动力组件安装在支撑架组件上部,压紧装置之压头组件 通过内支撑组件安装在支撑架组件内,所述支撑架组件为一门字形支架,包括加强横板和 支撑在加强横板两端的左支柱和右支柱,压紧装置动力组件的电动气缸安装在加强横板上 部的正中央,压头组件安装在加强横板的下部并与电动气缸连接,所述内支撑组件安装在 支撑架组件的“门框”内,位于支撑架组件的左右支柱之间,内支撑组件是一个小门字形支 架,包括水平滑板以及支撑在水平滑板两端的左导柱、左基座、右导柱和右基座,左、右导柱 分别通过左、右基座固定在机架平台上,水平滑板两端通过导孔与左、右导柱滑动配合,所 述压头组件安装在水平滑板正中间,所述压头组件包括电缸连接头、浮动接头Ⅱ、连接头、 出油座压头和压力传感器,所述电缸连接头上端与电动气缸连接,下端与压力传感器连接, 浮动接头Ⅱ上端与压力传感器连接,下端与固定在水平滑板上的连接头连接,出油座压头 9 CN 111590320 A 说 明 书 4/12 页 连接在水平滑板下部,其中心与进入该工位的放料组件的中心处在同一垂直线上; 所述压力传感器与控制系统的电路单元连接,用于监测电动气缸压力输出的状况,电 动气缸工作时带动电缸连接头、压力传感器、浮动接头Ⅱ、连接头和水平滑板沿左、右导柱 上下滑动,从而带动出油座压头压下或升起。 进一步:所述传送装置的动力组件包括双轴气缸、手指气缸和无杆气缸,所述取件 夹头包括左夹头和右夹头,所述双轴气缸安装在气缸安装板后部,其下端通过安装块连接 手指气缸,手指气缸的左、右活塞分别连接左夹头和右夹头,所述无杆气缸安装在气缸安装 板前部并与安装在机架上的滑轨滑动连接,无杆气缸前部安装电磁阀组件,所述电磁阀组 件包括电磁阀Ⅰ、电磁阀Ⅱ和电磁阀Ⅲ,分别用于控制无杆气缸、双轴气缸和手指气缸的工 作状态;无杆气缸工作时带动气缸安装板以及安装在气缸安装板上的双轴气缸、手指气缸 沿滑轨左右滑动,双轴气缸工作时推动手指气缸下行或上升,手指气缸工作时带动左、右夹 头张开或夹紧。 进一步:所述的顶出装置包括撑片推头、气缸板和动力组件,所述顶出装置通过气 缸板安装在对应于第四工位的机架平台底部,其撑片推头伸出机架平台上面并与位于该工 位的放料组件下部的撑片推杆相对,所述动力组件为可调气缸,可调气缸工作时,其撑片推 头推动放料组件的撑片推杆上升从而将该工位的电动燃油泵电磁系统组件内的撑片脱离 放料组件,以便手指气缸将组件夹起传递到下一工序。 进一步:所述工位转换装置位于工位盘下部的机架平台上与第三工位对应的位置 安装有用于支撑工位盘平稳转动的压装支撑块,压装支撑块的中心与工位转换装置上部的 压紧装置之压头组件的中心处在同一垂直线上,工位转换时该压装支撑块顶面与工位盘底 面滑动接触,并支撑工位盘使其在工件压装过程中始终保持水平状态,从而保证产品的装 置质量。 进一步:所述工位盘接近圆周的圆环面上均布设有四个指示牌Ⅰ,所述指示牌位于 每两个放料组件之间,工位盘的外侧设有指示装置,指示装置通过安装座安装在机架平台 上,其导杆支撑的指示牌Ⅱ与工位盘上的指示牌Ⅰ处于同一平面,并且指示牌Ⅱ的指针Ⅱ与 工位盘其中的一个指示牌Ⅰ的指针Ⅰ相对,工位转换时,则指示牌Ⅱ的指针Ⅱ与工位盘的下 一个指示牌Ⅰ的指针Ⅰ相对。 其另一技术方案是:一种燃油泵磁系统零部件与出油座的装配方法,该方法是用上述 的一种燃油泵磁系统出油座组合件装配装置,组装燃油泵电磁系统零部件与出油座的方 法,包括下述步骤: S1.观察指示牌Ⅱ的指针Ⅱ是否与工位盘其中的一个指示牌Ⅰ的指针Ⅰ相对,以确认工 位盘处于正确位置,然后启动装配装置; S2.人工初装 S21.按下控制键,监测和吸附装置位于第一工位的真空吸阀启动,其真空吸阀活塞伸 出与第一工位放料组件的吸阀接口对接; S22.将撑片放置于放料组件的撑片放置间隙中; S23.将磁钢Ⅰ和磁钢Ⅱ分别放置于小圆柱两侧的磁钢定位面上,真空吸阀将磁钢定位 面上的磁钢Ⅰ和磁钢Ⅱ吸紧; S24.将极壳套进中间圆台并限位于极壳限位面; 10 CN 111590320 A 说 明 书 5/12 页 S25.将出油座扣在极壳上端并限位于小圆柱的出油座限位面,位于第一工位的光电开 关及激光传感器分别监测到出油座和燃油泵磁系统零部件放置到位,控制面板上对应的绿 灯亮起,人工装配完成,真空吸阀活塞退出第一工位放料组件的吸阀接口; S26.分序装置启动,带动工位转换装置逆时针旋转90度,使在第一工位放料组件上已 初装好的工件转至第二工位进入预压工序; S3.预压装配 S31.预压装置的标准气缸工作,推动预压头组件下压,对已初装好的燃油泵磁系统零 部件和出油座进行导正预压; S32.监测和吸附装置与第二工位对应的接近开关监测到工件预压到位,控制面板上对 应的绿灯亮起; S33.分序装置启动,带动工位转换装置逆时针旋转90度,使在第二工位放料组件上已 预压到位的工件转至第三工位进入压紧工序; S4.压紧装配 S41.压紧装置上的电动气缸工作,向下推动压头组件对已预压导正的工件压紧; S42.顶出装置的顶出气缸工作,撑片推头向上运动推动放料组件的撑片推杆,将撑片 推出放料组件的撑片放置间隙,使压装好的工件松动; S43.监测和吸附装置与第三工位对应的接近开关监测到工件已压装完成,并且撑片已 推出放料组件的撑片放置间隙,控制面板上对应的绿灯亮起; S44.分序装置启动,带动工位转换装置逆时针旋转90度,使第三工位的放料组件和工 件转至第四工位准备取出工件; S5.取出工件 S51.监测和吸附装置与第四工位对应的接近开关监测到工件全部压装完成,传送装置 的电磁阀Ⅱ和电磁阀Ⅲ启动,气路导通,双轴气缸和手指气缸工作,在双轴气缸下滑的同 时,手指气缸张开左右夹头将压装好的工件夹出放料组件,无杆气缸工作通过滑轨将工件 送入另一道工序充磁; S6.在进行步骤S25工件转入第二工位的同时,第四工位空置的放料组件转入第一工位 的位置,并依次重复步骤S2~S5的操作,如此循环直至全部工件装配完成。 其进一步技术方案是:在进行步骤S25、S32或S43时,如控制面板上对应的绿灯不 亮而报警,则需要对该步骤的装配重新进行直至装配到位。 由于采取以上技术方案,本发明之一种燃油泵磁系统出油座组合件装配装置及装 配方法具有如下有益效果: 1.由于具有以下技术特征,因而生产效率高; (1)设有分序装置、工位转换装置、预压装置、压紧装置、顶出装置和传送装置,除了第 一工位需要人工初装以外,预压、压紧和取出工件均由装置自动完成,整个装配由原来的三 个工人、三道工序完成的工作,改变为只需一个工人操作,一次装夹即可完成产品的装配, 不仅提高了生产效率,而且减轻了工人的劳动强度; (2)本装配装置的分序、预压、压紧、顶出所采用的动力装置采用减速电机,气缸等,均 可方便的与外部气路电路单元和单元连接,易于控制,易于实现装配自动化,提高功效; 2.由于具有以下技术特征,因而装配质量好、精度高; 11 CN 111590320 A 说 明 书 6/12 页 (1)装配装置设有监测和吸附装置、既可方便人工初装时磁钢的定位(对所有放料组件 处于第一道工位的位置时,放料组件的背面始终对应着监测装置的真空吸阀的活塞运动方 向,装置启动后真空吸阀活塞与放料组件的吸阀接口对接,并利用真空负压的工作原理,保 证使两个磁钢零件始终吸附在磁钢定位件的两侧),又可监控工件装配是否完整,位置是否 正确,以及预压和压紧是否合格; (2)装配装置设有指示装置,可通过目测直观的判断工位转换是否到位; (3)机架平台上设有压装支撑块、预压装置下部设有预压支撑块,可保证工位转换和压 装时,工位盘保持平稳的水平状态,保证装配质量; (4)预压装置的预压头组件设有浮动接头Ⅰ、导正头、预压头和弹簧,预压头组件通过滑 轨组件连接,滑轨组件52的运动保证了预压头组件向下垂直运动的平稳性能,导正头将有 可能偏移的出油座A1导正,预压头下压将出油座A1预压到位,限位销524可限制预压的行 程,从而有效保证预压的精确; (5)压紧装置的压头组件设有浮动接头Ⅱ,压紧装置的压头组件通过内支撑组件的水 平滑板连接,水平滑板与左右导柱滑动连接,用可以导正出油座压头。 下面结合附图和实施例对本发明之一种燃油泵磁系统出油座组合件装配装置及 装配方法 的技术特征做进一步的说明。 附图说明 图1为本发明之燃油泵磁系统部件与出油座合装件的装配装置结构示意图(立体 效果); 图2为分序装置结构示意图(立体效果); 图3为工位转换装置结构示意图(立体效果); 图4为监测和吸附装置结构示意图(立体效果); 图5为分序装置、工位转换装置、监测和吸附装置以及顶出装置组合装配结构示意图 (立体效果); 图6为预压装置结构示意图(立体效果); 图7为预压头组件结构示意图; 图8为压紧装置结构示意图(立体效果); 图9为传送装置结构示意图(立体效果); 图10为指示装置结构示意图(立体效果); 图11为顶出装置结构示意图(立体效果); 图12~图13为放料组件结构示意图: 图12为立体效果图,图13为图12之A-A剖视图; 图14为工件装在放料组件上的结构示意图(立体效果); 图15为装配好的燃油泵电磁系统零部件与出油座合装件结构示意图(剖视); 图16为带分序监测凸轮和接近开关Ⅰ的分序装置结构示意图(立体效果); 图中: A—燃油泵电磁系统出油座组合件,A1—出油座,A2—极壳,A3—撑片,A4—磁钢Ⅰ,A5— 12 CN 111590320 A 说 明 书 7/12 页 磁钢Ⅱ;1—机架,101—机架平台; 2—分序装置,21—分序器,211—分序器安装板,212—同步轮Ⅰ,214—法兰盘,214-1— 定位圆柱Ⅰ,214-2—限位面Ⅰ,215—圆柱轴,215-1—定位圆柱Ⅱ,215-2—限位面Ⅱ,22—同 步带,23—减速器,231—减速器安装板,232—同步轮Ⅱ; 3—工位转换装置,31—工位盘,311—安装孔Ⅰ,32—指示牌Ⅰ,321—指针Ⅰ,33—放料组 件,331—基座,332—大圆柱,332-1—极壳限位面,332-2—大圆柱面,332-3—吸阀接口, 333—中间圆台,334—磁钢限位块,335—小圆柱,335-1—出油座限位面,335-2—磁钢定位 面,335-3—吸气小孔,336—撑片定位块,336-1—撑片限位面,336-2—撑片放置间隙, 337—压装支撑块,338—复位弹簧,339—撑片推杆; 4—监测和吸附装置,41—固定圆盘,411—安装孔Ⅱ,42—光电开关,43—真空吸阀, 431—真空吸阀活塞,44—激光传感器,45—接近开关; 5—预压装置,51—支撑立臂,511—横臂,52—滑轨组件,521—限位销,522—滑槽, 523—安装板,524—滑轨,53—标准气缸,531—调速阀,532—气路连接口,54—浮动接头Ⅰ, 55—预压头组件,551—导正头,552—预压头,553—弹簧,554—弹簧顶板,56—底座,57— 预压支撑块; 6—压紧装置,61—支撑架组件,611—加强横板,612—左立柱,613—右立柱,62—压头 组件,621—电缸连接头,622—浮动接头Ⅱ,623—连接头,624—出油座压头,625—压力传 感器,63—内支撑组件,631—水平滑板,632—左导柱,633—右导柱,634—左基座,635—右 基座,64—电动气缸; 7—传送装置,71—左夹头,72—右夹头,73—手指气缸,74—安装块,75—双轴气缸, 76—气缸安装板,77—电磁阀组件,771—电磁阀Ⅰ,772—电磁阀Ⅱ,773—电磁阀Ⅲ,78—无 杆气缸,79—滑轨; 8—指示装置,81—安装座,82—导杆,83—指示牌Ⅱ,831—指针Ⅱ; 9—顶出装置,91—撑片推头,92—气缸板,93—可调气缸,94—气缸推杆; 10—压装支撑块,11—控制系统; 图16中:213—分序监测凸轮,24—接近开关Ⅰ。