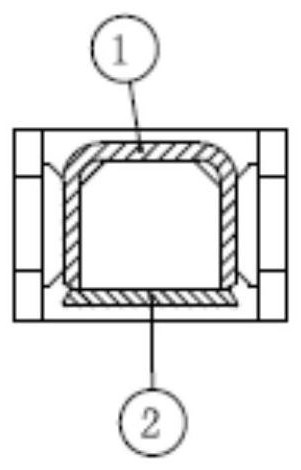
技术摘要:
本发明公开了一种多功能破拆机器人工作装置用上动臂及其加工方法,上动臂的箱体结构包括U型板和底板,U型板的开口向下,其两条侧边末端与底板焊接形成上动臂的箱体结构,上动臂的箱体结构两端焊接挡板,U型板的侧边表面焊接加强板,加强板的外侧表面焊接叉板,且叉板同 全部
背景技术:
现有多功能破拆机器人工作装置的上动臂,它的结构采用顶板、底板、左右侧板、 加强板焊接而成的封闭箱体结构,在极限工况时,这种结构的焊缝较多,导致加工精度下 降,容易出现应力集中,使侧板应力分布不均匀,造成侧板开裂,使上动臂的寿命降低。 如图2~5所示,为现有的破拆机器人工作装置上动臂,从上动臂结构上来看,其由 右侧板1'、顶板2'、原始底板3'、原始挡板4'、原始叉板5'、第一加强板6'、第二加强板7'和 左侧板8'组成。
技术实现要素:
本发明旨在提供一种多功能破拆机器人工作装置用上动臂及其加工方法,改变现 有上动臂结构中侧板因应力分布不均匀导致的开裂现象,提高上动臂的加工精度、强度和 刚性,延长上动臂的使用寿命。 本发明的技术方案如下: 多功能破拆机器人工作装置用上动臂,上动臂侧面连接有油缸铰点支撑板,上动 臂为箱体结构,箱体结构包括U型板和底板,所述U型板的开口向下,其两条侧边末端与底板 焊接。 优选的,U型板的开口方向指向油缸铰点支撑板与油缸连接的一侧,且底板的宽度 大于U型板的开口宽度,使得U型板与底板的焊接位置位于底板的端面上。 进一步,多功能破拆机器人工作装置用上动臂还包括挡板,所述挡板位于上动臂 长度方向的两端,且与U型板和底板焊接。 优选的,所述挡板的面积大于U型板和底板形成的箱体截面面积,且在挡板与U型 板和底板连接处轮廓线外侧形成一个环形余量区域。 进一步,多功能破拆机器人工作装置用上动臂还包括加强板,所述加强板位于上 动臂的侧表面,且与U型板的侧边表面焊接。 优选的,所述加强板的一端与挡板焊接。 优选的,所述加强板在U型板侧边表面的垂直投影位于U型板侧边表面的轮廓范围 内。 进一步,多功能破拆机器人工作装置用上动臂还包括叉板,所述叉板焊接在加强 板的侧表面,且叉板同时与挡板焊接。 优选的,所述叉板上且位于叉板与加强板连接区域内开有焊接用通孔。 优选的,所述叉板与加强板连接区域在加强板侧表面的垂直投影位于加强板侧表 面的轮廓范围内。 本发明中,多功能破拆机器人工作装置用上动臂的加工方法包括U型板、底板、挡 3 CN 111576922 A 说 明 书 2/3 页 板、叉板和加强板的焊接,且按照以下顺序进行, 步骤一,焊接U型板和底板形成上动臂的箱体结构; 步骤二,在步骤一箱体结构长度方向的两端焊接挡板,挡板同时与U型板和底板焊 接; 步骤三,在U型板的两条侧边表面焊接加强板; 步骤四,焊接叉板,且叉板同时与挡板、加强板焊接。 本发明的关键点在于解决了上动臂因应力集中造成侧板应力分布不均匀,使侧板 易出现开裂的现象。相比于现有的上动臂,U型板的加入减少了焊缝数量,改变了焊缝的空 间分布,加上其结构本身的对称性更好,导致箱体结构应力分布更均匀,刚性更好。同时,叉 板的焊接位置发生了改变,接触面积更大更均匀,整体强度提高。此外,挡板、U型板、底板、 加强板和叉板的两两连接,结构整体性得到提高,箱体厚度得到增加。按照本发明的焊接顺 序得到的上动臂结构,其变形较小,精度较高,从而改善了上动臂受力时的应力分布状况。 本发明的上动臂结构加工简单,变形相应减小,保证了上动臂的加工精度,强度和刚性增 强,其寿命有所提高。 与现有技术相比,本发明提供了一种多功能破拆机器人工作装置用上动臂及其加 工方法,本发明的上动臂外形结构易焊接成型,加工工艺简单,应力集中减小,不会因应力 集中而造成上动臂侧板开裂。焊后变形小,其强度和刚性得到加强。 附图说明 图1为上动臂安装位置示意图; 图2为现有上动臂结构焊接示意图; 图3为图2的纵截面示意图; 图4为图2的横截面示意图; 图5为图2左端局部正视图; 图6为本发明的上动臂结构示意图; 图7为图6的纵截面示意图; 图8为图6的横截面示意图; 图9为图6左端局部正视图; 图10为本发明上动臂中U型板和底板的截面示意图; 图中,1.U型板;2.底板;3.挡板;4.叉板;5.加强板;1'.右侧板;2'.顶板;3'.原始 底板;4'.原始挡板;5'.原始叉板;6'.第一加强板;7'.第二加强板;8'.左侧板。