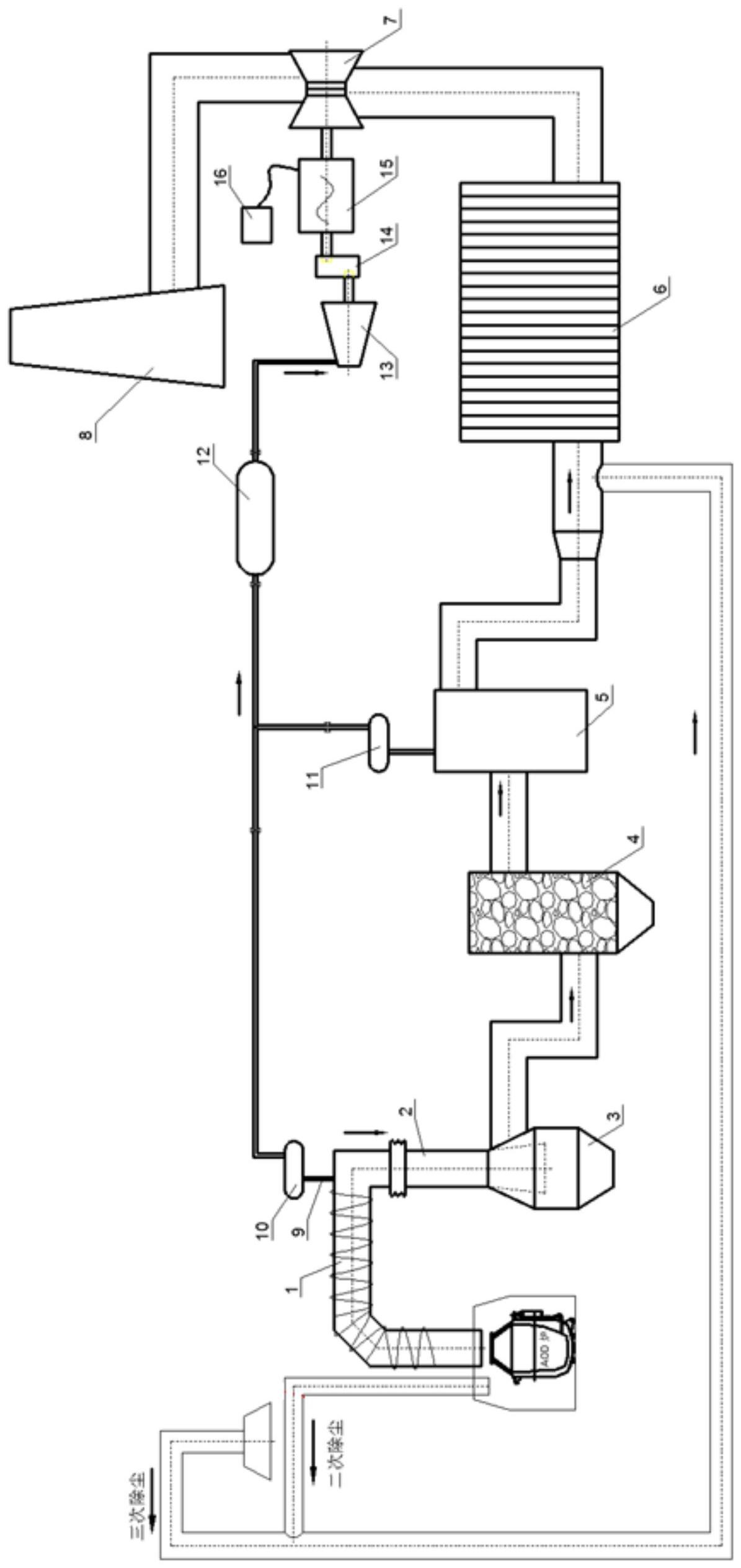
技术摘要:
本发明公开了一种AOD炉烟气余热高效回收系统,设置烟气余热回收管路及蒸汽余热回收管路,AOD炉产生的高温烟气与汽化烟道发生热交换产生高温饱和蒸汽和降温烟气;降温烟气通过烟气余热回收管路进行余热回收,高温饱和蒸汽通过蒸汽余热回收管路进行余热回收;在所述的烟 全部
背景技术:
AOD炉是一种冶炼不锈钢的工艺装置,其生产过程与转炉相近,均为间断性。由于 冶炼工艺需要,AOD炉的脱碳速度较转炉慢很多,导致其冶炼周期较长(120t AOD炉冶炼周 期100min,转炉为30min),产生的烟气温度、成分较转炉变化均较大。AOD炉的烟气温度在炉 口部位高达1600℃,但随着冶炼时间延长,脱碳速度逐渐减小,炉口烟气温度将降至100℃。 因此,AOD炉烟气的余热“品质”较转炉煤气的显热要差很多。目前有些企业对AOD炉的烟气 余热进行了部分回收,少数企业仍象征性的回收了少量余热。如何减少该烟气余热回收工 艺中的能耗损失、提高余热回收率对于企业节能减排意义较大。 现有回收工艺首先将AOD炉的高温含尘烟气负压通过汽化烟道,温度降至~850 ℃,同时产生~2.5MPa的饱和蒸汽(一次高压饱和蒸汽),降温后的烟气接着进入余热锅炉, 烟气温度将降至~200℃,再次产生~2.5MPa的饱和蒸汽(二次高压饱和蒸汽);烟气从锅炉 排出后进入脉冲布袋进行过滤净化,随后进入引风机,烟气压力变为正压,最终通过烟囱排 入大气;整个冶炼过程产生的一次、二次高压饱和蒸汽各自对应1个汽包,从2个汽包引出的 高压饱和汽进入蓄热器,蓄热器将间断的一次、二次高压饱和汽转化为连续的低压饱和汽 (~1.2MPa);低压饱和汽将作为主蒸汽进入汽轮机带动发电机发电,最终实现AOD炉高温烟 气的余热发电。 现有回收工艺首先将烟气显热转为饱和蒸汽的热焓再转为电能,该电能通过线缆 输送到指定变电所,经过二次分配后再送至用电设施。在该工艺中,从余热回收到电能的二 次利用,涉及多次电能的输送和转换的损耗,回收效率较低。 高温含尘烟气通过汽化烟道后直接进入锅炉,对锅炉换热管的寿命有较大影响。 为了延长换热管寿命,对烟气流速有了较大限制,不得已将锅炉体积设计的较大。但由于流 速过低后,烟尘将附着在换热管表面,影响了换热效果,最终降低了烟气余热回收率。同时 需考虑内部除灰设施,最终导致一次投资增加且实际使用效果并不理想。 由于AOD炉烟气参数变化剧烈,当烟气量大、温度高时,将产生大量饱和汽,当烟气 量少、温度低时,将不产生蒸汽,已有工艺依靠蓄热器来熨平间蒸汽的波峰与波谷,产生连 续主蒸汽。但由于AOD炉生产工艺复杂,烟气瞬息变化,很难通过热力计算得到蓄热器的合 适选型,实际生产中蓄热器往往过小,导致产汽波峰时大量蒸汽被放散;同时烟气温度的往 复变化降低了锅炉换热管的寿命,也不利于提高余热回收率。
技术实现要素:
针对现有技术中的缺陷和不足,本发明给出了一种AOD炉烟气余热高效回收系统, 避免现有回收工艺过程中电能输送和转化的损耗,提高余热回收率; 为达到上述目的,本发明采取的技术方案包括: 4 CN 111595166 A 说 明 书 2/8 页 一种AOD炉烟气余热高效回收系统,设置烟气余热回收管路及蒸汽余热回收管路; AOD炉产生的高温烟气与汽化烟道发生热交换产生高温饱和蒸汽和降温烟气;降 温烟气通过烟气余热回收管路进行余热回收,高温饱和蒸汽通过蒸汽余热回收管路进行余 热回收; 在所述的烟气余热回收管路上至少依次接设除尘装置和蓄热装置; 所述的除尘装置设置除尘炉体,在所述除尘炉体的顶部半嵌入设置缓冲排烟腔, 在所述除尘炉体中部外连通围设供氧管路;所述的缓冲排烟腔的外径沿远离除尘炉体顶部 渐大; 所述的蓄热装置至少设置蓄热炉体,在所述的蓄热炉体内至少沿轴向依次叠设多 个蓄热段;蓄热段中设置蓄热砖,蓄热砖为沿轴向设置通孔的块体;高温烟气由蓄热炉体顶 部输入,经多个蓄热段蓄热后由蓄热炉体底部排出;低温烟气由蓄热炉体底部输入,经多个 蓄热段蓄热后由蓄热炉体顶部排出。 可选的,所述的缓冲排烟腔设置腔管,与腔管连通设置缓冲排烟管;缓冲排烟管为 外径渐大的管体结构;所述缓冲排烟管的高度为炉体高度的1/3~3/4倍;所述的缓冲排烟 管的外径范围为1.5~2.5m;所述缓冲排烟腔嵌入炉体中的深度为1~2m。 可选的,所述的缓冲排烟腔与除尘炉体形成环形间隙,环形间隙的体积为80~ 90m3。 可选的,所述的供氧管路包括供氧主管和多个供氧支管;供氧支管沿周向连通围 设在除尘炉体外;所述的除尘炉体沿轴向依次设置进烟段、缓冲燃烧段和沉降排灰段;所述 的缓冲排烟腔沿进烟段和缓冲燃烧段嵌设;所述的供氧管路围设在缓冲燃烧段外; 所述的进烟段为锥形腔体结构,在所述进烟段连通设置进烟管;与所述缓冲排烟 腔顶部连通设置排烟管,排烟管上设置CO检测器; 所述的沉降排灰段为锥形腔体结构,在沉降排灰段底部设置排灰阀门;在沉降排 灰段侧壁设置检修口。 可选的,所述的多个蓄热段至少包括第一蓄热段、第二蓄热段和第三蓄热段;按蓄 热温度高低分,第一蓄热段、第二蓄热段和第三蓄热段的蓄热温度或蓄热系数依次降低;所 述的蓄热砖为横截面是多边形的带孔块体,孔径为20~25mm,孔数为7~9个。 可选的,在所述多个蓄热段下还设置烟气导流段;烟气导流段由多个空心板块组 成; 在所述烟气导流段下还设置耐材支撑段,耐材支撑段通过多个均匀分布的支柱进 行支撑;与蓄热炉体外连通所述耐材支撑段设置第三绝热管道和第四绝热管道;第三绝热 管道上设置第三阀门,第四绝热管道上设置第四阀门。 可选的,在所述的多个蓄热段前的蓄热炉体上还设置烟气分流段,烟气分流段为 圆柱形空腔结构;与蓄热炉体外连通所述烟气分流段设置第一绝热管道和第二绝热管道; 第一绝热管道上设置第一阀门,第二绝热管道上设置第二阀门;在所述烟气分流段前的蓄 热炉体上还设置烟气缓冲段,所述烟气缓冲段为锥形收口结构。 可选的,所述的烟气余热回收管路包括依次连通的绝热烟道、除尘装置、蓄热炉、 余热锅炉、布袋除尘器、引风机和烟囱。 可选的,所述的蒸汽余热回收管路包括依次连通的蒸汽管道、第一汽包、蒸汽蓄热 5 CN 111595166 A 说 明 书 3/8 页 器、汽轮机、离合器和发电机;所述的发电机为烟气余热回收管路的烟气排出供电。 可选的,蒸汽余热回收管路产生的蒸汽转换为电能,所述的电能为烟气余热回收 管路的烟气排出供电。 本发明的技术方案通过降低进入锅炉烟气的含尘量,同时避免烟气温度往复变化 对锅炉换热管的影响,延长锅炉寿命,提高换热效率,最终提升整个工艺的余热回收率。 附图说明 附图是用来提供对本公开的进一步理解,并且构成说明书的一部分,与下面的具 体实施方式一起用于解释本公开,但并不构成对本公开的限制。在附图中: 图1为本发明的AOD炉烟气余热高效回收系统结构示意图; 图2是本发明的除尘装置结构示意图; 图3为本发明的蓄热装置结构图; 图4为图3中蓄热砖结构示意图; 图中各标号表示为:1-汽化烟道、2-绝热烟道、3-除尘装置、4-蓄热装置、5-余热锅 炉、6-布袋除尘器、7-引风机、8-烟囱、9-蒸汽管道、10-第一汽包、11-第二汽包、12-蒸汽蓄 热器、13-汽轮机、14-离合器、15-发电机、16-变频器; 31-缓冲排烟腔、311-缓冲排烟管、32-除尘炉体、321-进烟段、322-缓冲燃烧段、 323-沉降排渣段、3231-检修口、33-供氧主管、331-供氧支管、34-进烟管、35-排烟管、351- CO检测器;3a-供氧主管阀门、3b-供氧支管阀门、3c-排灰阀门。 41-烟气缓冲段、42-烟气分流段、43-第一蓄热段、44-第二蓄热段、45-第三蓄热 段、46-烟气导流段、47-耐材支撑段、471-支柱;4a-第一阀门、4b-第二阀门、4c-第三阀门、 4d-第四阀门、4e-第一绝热管道、4f-第二绝热管道、4g-第三绝热管道、4h-第四绝热管道。