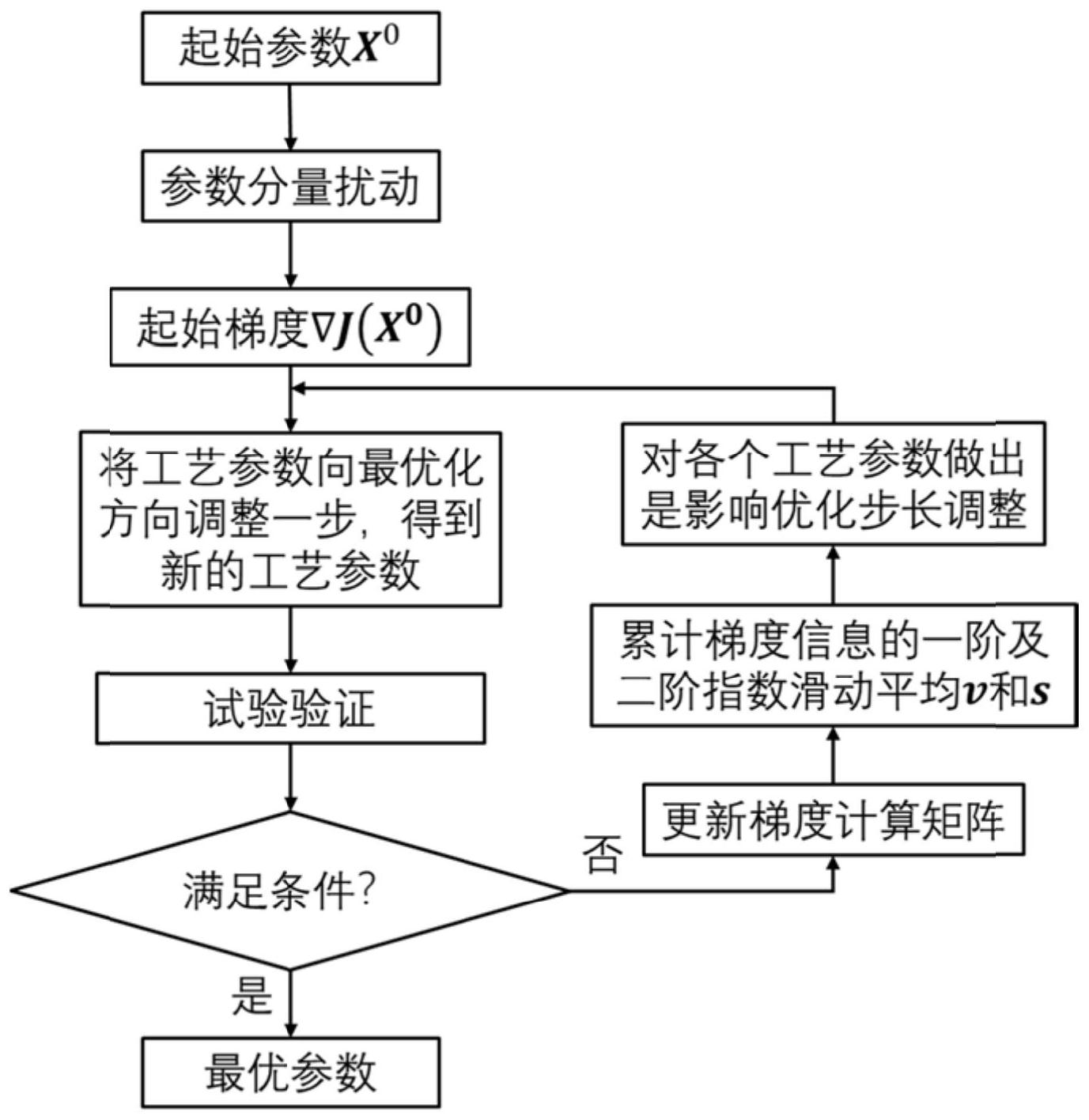
技术摘要:
本发明公开了一种注射成形工艺参数无模型优化方法,解决现有优化方法存在的所需试验次数多,对不同参数为进行适应性调整的问题。本方法无需对产品质量指标与工艺参数之间建立代理模型,通过在线迭代的方法使得工艺参数向最优解附近收敛。本发明通过迭代梯度估计方法, 全部
背景技术:
注射成形是典型的批处理过程,目前注射成形的材料可以包括:塑料、橡胶、磁性 粉末、金属等。以塑料注射成形为例,每个批处理过程包括三个阶段:填充阶段,保压阶段, 冷却和塑化阶段。在填充阶段,注塑机将熔体推入模具的模腔中,通过速度/压力(V/P)切换 点后将切换到保压阶段,维持一定的保压压力以补偿收缩。随后料筒中的螺杆退回并反转, 将新的塑料颗粒进行加热并塑化,同时模具中的塑料熔体经过一定时间冷却固定成形,直 到产品可以从模具中顶出。 模具设计,零件设计,原材料和工艺参数是影响注塑产品的最主要因素。确定模具 和零件的设计以及原材料的类型后,工艺参数是影响产品质量,生产率和能耗的最重要因 素。因此,确定最优的工艺参数意义重大。但是,由于成形过程中涉及的参数数量众多,不同 参数之间存在耦合,并且优化目标和参数之间存在时变和非线性的关系,这项工作仍然是 一个挑战。 试错法等传统方法在很大程度上取决于技术人员的个人经验,通过反复试凑调节 工艺参数。这种优化方法耗费时间且需要多次试验,无法再满足工业的效率要求。随着数值 分析的发展,许多研究人员将不同的数学模型用于参数优化方法,这些方法可以分为两类: 基于模型的优化(model-based optimization ,MBO)和无模型优化(model-free optimization,MFO)。 MBO方法首先需要采集若干组工艺参数及其对应的优化目标值,通过这些数据建 立优化目标与参数的代理模型。建立代理模型的方法包括人工神经网络(ANN),支持向量机 (SVM)等等。由于注塑成形过程的复杂性,建立足够精度的代理模型通常需要大量的试验数 据进行回归拟合,因此增加了优化成本;除此之外,优化目标与工艺参数之间的关系通常会 随材料、产品结构等因素变化,因此,MBO方法建立的代理模型只适用于特定种类的材料及 结构,无法直接推广到其他产品中,而是需要重新进行建立代理模型的过程,从而降低了优 化效率。 与MBO方法相比,MFO方法不需要事先建立代理模型,而是在每一步得到的优化目 标值作为反馈,判断当前的优化方向,逐渐迭代到最优的工艺参数。MFO方法的关键在于寻 找准确的优化方向以及如何分配每个参数的优化步长。MFO方法可以分为两类:基于梯度的 方法和不基于梯度的方法。不基于梯度的方法根据随机搜索找到更接近优化目标的参数, 从而确定优化方向,如Nelder–Mead方法,进化算法等等。这种方法的优点在于无需额外的 试验次数来进行梯度的估计,但是优化过程存在一定的随机性,且收敛速度与基于梯度的 方法相比更低。而基于梯度的方法一般需要额外的试验以拟合梯度,如同时摄动随机近似 (SPSA)方法,但得益于梯度提供的明确的优化方向,基于梯度的方法由较快的收敛速度,能 4 CN 111611715 A 说 明 书 2/11 页 够以更少的实验成本得到最优的工艺参数。目前的MFO方法仍然存在不足之处:优化方向的 确定一般需要额外的试验以拟合梯度,提高了优化成本;参数调整过程中对每个参数的调 整步长通常是相等的,没有充分考虑对不同参数的适应性。基于以上考虑,有必要提出一种 无模型自适应的优化方法,以提高工艺参数优化的效率。
技术实现要素:
本发明目的在于解决现有注射成形工艺参数优化方法仍然存在的不足之处,提供 一种更加快速、低成本、自适应的工艺参数优化方法。 本发明采用迭代梯度估计方法计算当前点的梯度方向,作为参数调整方向,并且 采用自适应矩估计算法实现每个参数步长的自适应调整,以解决现有优化方法试验次数 多、对不同参数适应性低等问题,最终以少量试验次数实现工艺参数的快速优化。 为实现上述目的,本发明采用的技术方案如下: 一种注射成形工艺参数无模型优化方法,包括: (1)针对待优化的注射成形工艺,确定待优化的质量指标Q和该质量指标的质量指 标目标值Qtarget; (2)确定n个待优化工艺参数,确定待优化工艺参数的初始值,并进行预处理,得到 初始的参数样本; (3)对当前参数样本中的每个参数分别进行扰动,得到n组经过扰动操作后的参数 样本,最终获得包含当前参数样本在内的n 1组参数样本及对应的n 1个质量指标值Q1; (4)利用获取得到的n 1个质量指标值Q1,求取当前参数样本处的梯度值; (5)根据得到的梯度值,更新当前参数样本,利用更新后的参数样本,求取其对应 的质量指标值Q2,将质量指标值Q2与质量指标的质量指标目标值Qtarget进行比较: 若满足设定要求,输出最优工艺参数; 否则,利用更新后的参数样本以及质量指标值Q2替换步骤(3)中的n 1组参数样本 中优化目标值最差的一组参数样本以及质量指标值Q1,返回步骤(4)。 步骤(1)中,确定优化的质量指标Q(如产品重量、翘曲等)、质量指标目标值Qtarget 和优化目标误差容差δ;选择要优化的参数X=(x T1,x2,…,xn) 及其可行范围,如以下公式所 示: s.t.Li≤xi≤Ui,i=1,2,...,n X=(x1,x2,...,x )Tn J(X)表示当前质量指标值与目标值(即Qtarget)间的差异。其中质量指标Q(X),可以 视为关于工艺参数X的隐函数,X由n个参数x1,x2,…,xn组成,如保压压力、熔体温度等,Li和 Ui表示参数xi的上下界。 由于不同参数存在数量级上的差异,如熔体温度和注射时间之间相差两个数量 级,通常需要在参数优化过程中对各个参数按照下式进行归一化,进行归一化能够保证各 个参数能够以相同的幅度变化。作为优选,步骤(2)中,预处理过程如下: 5 CN 111611715 A 说 明 书 3/11 页 其中:X为某一个工艺参数,Xnorm为X预处理后的参数;L为该工艺参数对应的最小 值,U为工艺参数对应的最大值。 本发明中,所述质量指标值Q1、质量指标值Q2可以通过仿真或者实验得到。 步骤(3)中,对每个参数分别进行扰动,扰动大小和方向没有严格限制,扰动后共 得到n 1组工艺参数及其对应的质量目标值,进而得到其对应的优化目标值J: 其中,J(X0)、J(X1)、J(Xn)分别为X0、X1、Xn对应的质量目标值与质量指标目标值之 间的差值(即对应质量目标值与质量指标目标值之间的差的绝对值); 步骤(4)中,根据J(X)在X0处的泰勒展开: 写作矩阵形式: 进一步可由下式求得当前参数样本X0处的梯度值: 其中: 为由当前参数样 本针对第i个参数扰动后得到的参数样本,其中δi为扰动量;J(Xi)为Xi对应的质量指标值Q (Xi)与质量指标目标值Qtarget的差值;i=1,2,3...n。 由公式计算得到的梯度的反方向,即 为参数的优化方向,由下式产生下 6 CN 111611715 A 说 明 书 4/11 页 一迭代点,得到的新的工艺参数将会更接近设定的目标值。即步骤(5)中,更新当前参数样 本的方法如下: 其中α0为参数调整的步长;X0为当前参数样本; 为更新后的当前参数样 本; 为梯度值。得到更新的参数 后,需要进行去归一化(如公式(2)),使参 数回到物理参数值(Xdenorm),以方便技术人员进行实验操作得到 处的目标值 Xdenorm=Xnorm×(U-L) L 上述物理转换仅在求解质量指标值或目标值时进行,在后续的更新过程中,始终 采用经过预处理的参数数据,以保持处理过成的统一性。当然,如果采用仿真方法求解质量 指标值或目标值时,可以通过编程直接采用得到的 进行判断等。 步骤(5)中,判断质量指标值Q2是否满足要求,若|Q2-Qtarget|<δ,则所得优化目标 已满足终止条件,优化进程停止, 为最优参数,进行物理转化后,可以输出实际的 最优参数信息;反之则不满足终止条件,则更新步骤(3)中的参数样本后,返回到步骤(4), 进行下一次的优化计算。 在上述更新步骤(3)中参数样本后,更新梯度计算矩阵。使用新得到的点 代替原梯度计算矩阵中目标值最差的点,同时成为当前的参数 样本(假设为(X0,J(X0)),不失一般性),由J(X)在X0处的泰勒展开,得到更新之后的梯度计 算矩阵为: 在获得梯度信息之后,现有的优化方法通常采用梯度下降算法来将更新参数。在 这种情况下,将步长α0设置为常数,并且参数变化量 仅取决于当前单点 的梯度,而忽略了历史梯度信息的积累,而历史梯度信息的积累可以为接下来的优化方向 及步长提供有用的建议,从而在之后的优化步骤中能够更加适应地调整步长α0。因此,本发 明步骤(5)中,利用自适应矩估计方法,基于历史梯度信息的积累,实现对当前参数样本的 更新。 进一步讲,首次更新时,可以给定步长α0数值,在后续的更新过程中,可以采用自 适应矩估计方法,经过适应性调整之后各个参数的优化步长为: 7 CN 111611715 A 说 明 书 5/11 页 其中,X0为当前参数样本, 为更新后的当前参数样本;η为预先设定的步长 系数;δ为修正系数; 为历史梯度的一阶指数滑动平均的修正,由历史梯度的一阶指数滑 动平均和历史梯度信息计算得到; 为历史梯度的二阶指数滑动平均的修正,由历史梯度 的二阶指数滑动平均和历史梯度信息计算得到。 第m次更新时,对应的历史梯度的一阶指数滑动平均的修正为 历史梯度的 二阶指数滑动平均的修正为 分别由下式求得: 其中:m为更新次数;vm-1为第m次更新时的历史梯度的一阶指数滑动平均;vsm-1为 第m次更新时的历史梯度的二阶指数滑动平均;v0=0;s0=0; 为第m-1次更新后 得到的梯度值;⊙ 表示矩阵对应元素相乘;β1为一阶指数衰减率系数;β2为二阶指数衰减率 系数。β1为0.85~0.95;β2为0.99~0.999。 具体讲,计算历史梯度的一阶指数滑动平均: v0=0 β1为一阶指数衰减率系数,通常设置为0.9。计算一阶指数滑动平均主要起到加速 优化过程的作用。例如之前的若干个优化步骤中某一参数分量的梯度均为正值,则一阶指 数滑动平均v会记录并积累这种趋势,并在之后的优化步中增大此参数的步长,从而起到加 速的作用。一阶指数滑动平均v的作用类似于物理中动量的概念,因此也被称为动量算法。 计算历史梯度的二阶指数滑动平均: s0=0 8 CN 111611715 A 说 明 书 6/11 页 β2为二阶指数衰减率系数,通常设置为0.999;⊙ 表示矩阵对应元素相乘。考虑到 优化目标仅对一部分参数敏感,而对其他参数的变化不敏感。对于多个参数的优化问题,需 要针对不同参数设置不同的优化步长,从而与其对优化目标的影响程度相适应。二阶指数 滑动平均s通过积累梯度的平方来评估每个参数的影响,并提高优化方法的适应性。如果目 标函数在某些维度上的梯度的平方始终很小,则在这些维度上的下降步长会增大以加速收 敛;反之,对于一些上下波动较大的参数则会减小其优化步长,以减少波动。 指数滑动平均误差修正。由于v和s的初始值一般设为0,会导致指数滑动平均出现 误差,根据下式修正这种由初始值引起的误差。其中m表示当前为第m优化步。 最终得到工艺参数更新公式为: 其中η为预先设定的步长系数,δ为一个很小的正数(如10-8)以避免分母为0。 本发明的方法可以用于采用各种注射成形材料(包括但不限于塑料、橡胶、磁性粉 末、金属等)的注射成形工艺的优化。 本发明提出的注射成形工艺参数优化方法的有益效果在于: 1、本发明提供了一种无模型的优化方法,无需建立代理模型,采用迭代梯度估计 方法计算当前点的梯度方向,大大减少了建模所需的大量试验次数,且易于推广到其他工 艺过程。 2、结合自适应矩估计算法,实现了注射成形工艺参数的快速、自适应优化,解决了 以往工艺参数优化方法收敛速度慢、未针对不同参数进行适应性调整的问题,大大减少了 优化成本,在具体实施过程中具有很强的可操作性。 3、除此之外,注射成形时一种典型的批次过程,本发明所提出的优化方法也可在 其他批次过程(如铸造)工艺参数优化进行推广。 附图说明 图1为本发明的注射成形工艺参数无模型自适应优化方法的流程图; 图2为实施例的优化过程中实验序号与产品重量的变化趋势图; 图3为本发明的方法与没有采用自适应性步长调整的优化方法结果对比图。