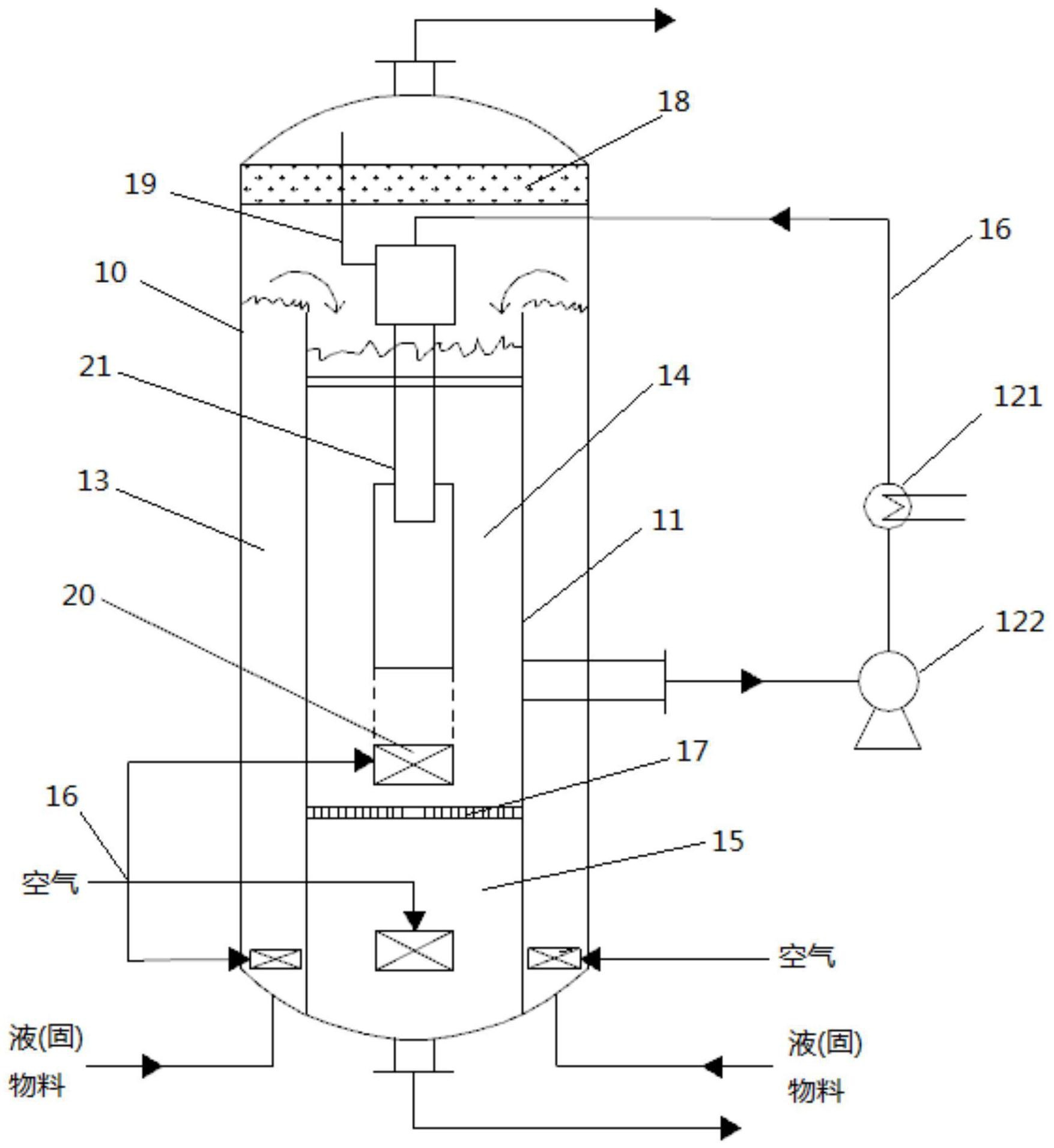
技术摘要:
本发明提供了一种PX生产PTA的内置微界面机组智能强化反应系统及工艺,该系统包括:反应器、设置在所述反应器内部的微界面机组以及智能控制模块;其中,所述反应器包括外壳、同心设置在所述外壳内部的内筒以及部分设置在所述外壳外部的循环换热装置,所述内筒的底端封闭 全部
背景技术:
PX(对二甲苯)生产TA(对苯二甲酸)的氧化反应过程非常复杂,主要包括4个步骤, 即对二甲苯(PX)→对甲基苯甲醛(TALD)→对甲基苯甲酸(p-TA) →对羧基苯甲醛(4-CBA) →对苯二甲酸(TA),此反应过程中的4个氧化反应是串联反应,其一般以醋酸为溶剂,以醋 酸钴、醋酸锰和氢溴酸(或四溴甲烷) 为催化剂。 目前,现有的PTA生产技术中,氧化反应过程中的4个主要步骤均在同一个反应器 内进行,尽管上述4个步骤的反应速率常数相差十几倍,但是却采用混合反应工艺,没有针 对不同反应给予不同条件,反应溶剂醋酸在高温高压下被大量浪费,同时不能及时地取出 产品TA,因此能耗高、醋酸消耗量大、反应效率低。
技术实现要素:
鉴于此,本发明提出了一种PX生产PTA的内置微界面机组智能强化反应系统及工 艺,旨在解决现有的PX生产PTA过程中反应溶剂醋酸在高温高压下被大量浪费,同时不能及 时地取出产品TA的问题。 一个方面,本发明提出了一种PX生产PTA的内置微界面机组智能强化反应系统,包 括:反应器、设置在所述反应器内部的微界面机组以及智能控制模块;其中, 所述反应器包括外壳、同心设置在所述外壳内部的内筒以及部分设置在所述外壳 外部的循环换热装置,所述内筒的底端封闭的连接在所述外壳的内底面上、顶端开放,所述 外壳与所述内筒之间的区域为第一反应区,所述内筒内部自上向下依次为第二反应区和第 三反应区,所述循环换热装置分别与所述内筒和所述微界面机组相连; 所述微界面机组包括第一微界面发生器和第二微界面发生器,所述第一微界面发 生器分别设置在所述第一反应区、第二反应区和第三反应区的底部、用以将作为反应原料 的空气破碎为直径大于等于1μm、小于1mm的微气泡,所述第二微界面发生器设置在所述第 二反应区的上端、并与设置在第二反应区底部的第一微界面发生器相对、用以在所述循环 换热装置输送的所述第二反应区内部反应液的动力作用下将汇集在所述反应器顶部的未 被反应的空气卷吸进其内部破碎为所述微气泡; 所述智能控制模块设置在所述反应器上,其包括PLC控制器、传感器和云处理器, 所述传感器将采集的电信号传输给云处理器,所述云处理器根据传感器传回的反应参数在 云数据库进行筛选对比,筛选出最佳控制参数后对PLC控制器发出相对应的命令。 进一步地,上述PX生产PTA的内置微界面机组智能强化反应系统中,所述PLC控制 器包括: 所述第一PLC控制器,用以控制所述第一反应区的反应温度和反应压力; 4 CN 111574345 A 说 明 书 2/7 页 所述第二PLC控制器,用以控制所述第二反应区的反应温度和反应压力;; 所述第三PLC控制器,用以控制所述微界面机组的发生器工作。 进一步地,上述PX生产PTA的内置微界面机组智能强化反应系统中,所述传感器包 括: 多个温度传感器,其分别设置在所述第一反应区、所述第二反应区、所述第三反应 区以及循环换热装置中,用以实时监测系统温度; 多个压力传感器,其分别设置在所述反应器中,用以实时监测系统压力。 进一步地,上述PX生产PTA的内置微界面机组智能强化反应系统中,所述第一反应 区为进行对二甲苯转化为对甲基苯甲醛、对甲基苯甲醛转化为对甲基苯甲酸的反应区,所 述第二反应区为所述对甲基苯甲酸转化为对羧基苯甲醛的反应区,所述第三反应区为所述 对羧基苯甲醛转化为对苯二甲酸的反应区。 进一步地,上述PX生产PTA的内置微界面机组智能强化反应系统中,所述内筒的高 度为所述外壳高度的4/5。 进一步地,上述PX生产PTA的内置微界面机组智能强化反应系统中,所述第一反应 区的体积占所述反应器内总反应体积的45%所述第二反应区的体积占所述反应器内总反 应体积的53.5%,所述第三反应区的体积占所述反应器内总反应体积的1.5%。 进一步地,上述PX生产PTA的内置微界面机组智能强化反应系统中,所述第一微界 面发生器为气动式,所述第二微界面发生器为液动式。 另一方面,本发明还提出了一种PX生产PTA的内置微界面机组智能强化反应工艺, 其特征在于,包括如下步骤: 将对二甲苯、醋酸和催化剂的混合物通过反应器下端进入反应器外壳与内筒间的 第一反应区内,同时将空气通进设置在所述第一反应区底部的通过第三 PLC控制器控制的 微界面发生器内,使其破碎为直径大于等于1μm、小于1mm 的微气泡,与液相物料形成乳化 液,通过第一PLC控制器实时控制反应温度和反应压力,并在所述催化剂作用下将对二甲苯 转化为对甲基苯甲醛、同时将对甲基苯甲醛转化为对甲基苯甲酸,其中未反应完的所述空 气离开液面上升到所述反应器的上方,并通过设置在所述第一反应区的温度传感器实时监 测其内部反应温度; 随着第一反应区内上述反应的不断进行反应混合液从所述第一反应区溢流至所 述内筒中,通过第二PLC控制器控制反应温度和反应压力,同时通过设置在所述内筒上部的 第二反应区底部的第一微界面发生器向该区域通入破碎成所述微气泡的空气,并在所述催 化剂的作用下与混合液中的所述对甲基苯甲酸反应生成对羧基苯甲醛,并通过设置在所述 第二反应区的温度传感器实时监测其内部反应温度,其中未反应完的空气离开液面上升到 所述反应器的上方,并在循环换热装置的动力作用下通过设置在所述第二反应区上部的第 二微界面发生器的卷吸作用下,通过导气管被送入到该区域底部继续参与所述对羧基苯甲 醛的生成反应,经过多次循环之后,在压力推送下,尾气从所述反应器顶部出口进入到尾气 处理单元中; 所述第二反应区内反应生成的所述对羧基苯甲醛穿过防浪格栅进入到该区下方 的第三反应区中,与设置在该区底部的第一微界面发生器通入的所述微气泡在所述催化剂 的作用下发生氧化反应生成对苯二甲酸,并与未反应完的反应混合物通过所述反应器下方 5 CN 111574345 A 说 明 书 3/7 页 出口排出,进入后续分离精制工段,反应过程中通过设置在所述反应器内部的多个压力传 感器实时监测系统的反应压力。 进一步地,上述PX生产PTA的内置微界面机组智能强化反应工艺中,所述第一反应 区的体积占所述反应器内总反应体积的45%,所述第二反应区的体积占所述反应器内总反 应体积的53.5%,所述第三反应区的体积占所述反应器内总反应体积的1.5%。 进一步地,上述PX生产PTA的内置微界面机组智能强化反应工艺中,所述第一微界 面发生器为气动式,所述第二微界面发生器为液动式。 与现有技术相比,本发明的有益效果在于,本发明提供的PX生产PTA的内置微界面 机组智能强化反应系统及工艺,考虑到PX生产PTA的四步反应的速率差异,采用分段式的反 应理念,将反应器内部设置为三个不同的反应区,各反应区不同的反应步骤,实现了在同一 反应器内针对不同反应阶段给予不同条件,尤其是解决了醋酸溶剂不能承受高温氧化条件 的矛盾,并且利用水作为 p-TA氧化反应的溶剂,有效地解决了现有的PX生产PTA过程中反 应溶剂醋酸在高温高压下被大量浪费,同时不能及时地取出产品TA的问题,进而大大地降 低了能耗、节省了醋酸溶剂、提升了反应效率。 尤其是,本发明的PX生产PTA的内置微界面机组智能强化反应系统及工艺,通过在 反应器内部的各个反应区内设置微界面发生器,在各反应器内部对空气进行破碎,使其破 碎为直径大于等于1μm、小于1mm的微气泡,与液相物料形成乳化液,有效地增大了空气与液 相物料之间的传质面积,减小液膜厚度,降低传质阻力,进而有效地降低了能耗、提升了反 应效率。 进一步的,本发明的PX生产PTA的内置微界面机组智能强化反应系统及工艺,通过 设置循环换热装置,在反应进行的过程中有效控制了反应过程中的温度,同时确保了反应 器内部各反应物料之间混合的均匀度,确保了各反应物能够充分的参与反应,进而极大地 提升了反应物的利用率,同时防止了因局部温度不均引发副反应的发生,在一定程度上提 升了产物的质量。 附图说明 通过阅读下文优选实施方式的详细描述,各种其他的优点和益处对于本领域普通 技术人员将变得清楚明了。附图仅用于示出优选实施方式的目的,而并不认为是对本发明 的限制。而且在整个附图中,用相同的参考符号表示相同的部件。在附图中: 图1为本发明实施例提供的PX生产PTA的内置微界面机组智能强化反应系统的结 构示意图。 图中:10为外壳、11为内筒、13为第一反应区、14为第二反应区、15 为第三反应区、 16为管道、17为防浪格栅、18为除沫网、19为导气管、20 第一微界面发生器、21为第二微界 面发生器、121为换热器、122为压力泵122。