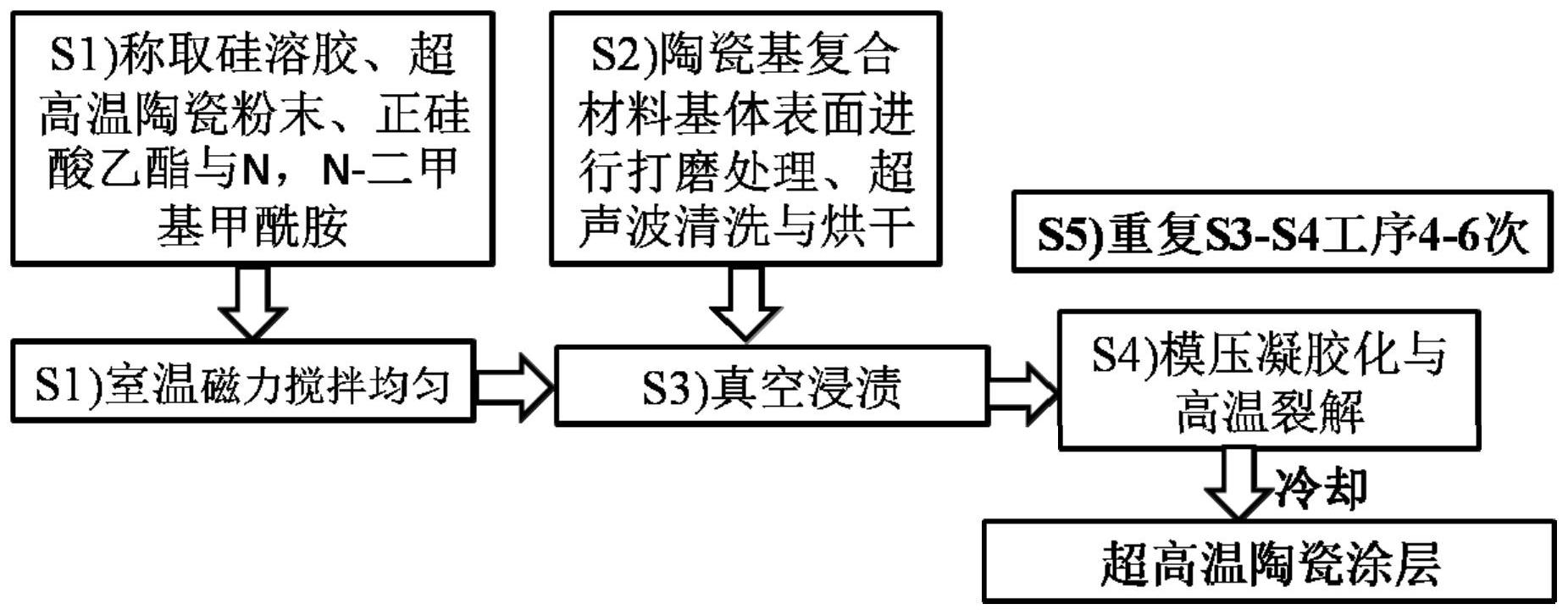
技术摘要:
本发明涂层材料技术领域,提供了一种陶瓷基复合材料用耐高温涂层的制备方法,它以正硅酸乙酯和N,N‑二甲基甲酰胺分别作为抗凝胶剂和分散剂,采用浸渍‑模压低温凝胶化‑高温裂解工艺在陶瓷基复合材料表面得到涂层。本发明制备周期短、成本低,模压低温凝胶化‑高温裂 全部
背景技术:
近年来,航空航天事业的飞速发展,使人类探索外太空的美好梦想正在一步一步 成为现实。在支撑航空航天技术发展的诸多科学技术中,材料体系是重要基础。世界各工业 发达国家都集中精力寻找能替代已不能适应新要求的金属及金属合金材料。 陶瓷材料以其突出的耐高温性能受到材料工作者的青睐,但作为结构材料实用化 却存在着脆性大的致命问题,包括断裂韧性低、断裂应变小、抗冷热交变和冲击载荷性能差 的固有缺点。 陶瓷基复合材料(Ceramic Matrix Composites,CMCs)就是在这一背景下出现的 以连续纤维作为增强体、以陶瓷作为基体的一种近年发展较快的高比强度、高比模量、耐高 温、抗烧蚀的新兴材料体系。 碳纤维增强陶瓷基复合材料是航空航天用高温结构材料的技术制高点之一,可反 映先进航空航天器的设计和制造能力。因此,大力发展碳纤维增强陶瓷基复合材料技术对 于提高我国航空航天技术水平具有重要意义。 碳纤维增强陶瓷基复合材料具有种种优异性能,但在高于400℃氧化气氛中碳纤 维会快速氧化,导致复合材料性能下降甚至失效,大大限制了其在高温氧化性条件下的应 用。因此,提高陶瓷基复合材料的抗氧化耐烧蚀性能对于推进其在航空航天领域的应用,具 有重大的现实意义。 陶瓷基复合材料的抗氧化技术主要有界面抗氧化技术、基体改性技术以及表面涂 层技术三种,界面抗氧化的成本高、工艺难度较大,对界面材料具有一定的要求;基体改性 虽然可以解决材料抗氧化性能低的问题,但引入的物质会导致其力学性能的降低;表面涂 层技术比较简单且不会降低材料的机械性能。因此,表面涂层法是碳材料抗氧化最常用、也 是最有效的方法之一。
技术实现要素:
本发明的目的是提供一种陶瓷基复合材料用耐高温涂层的制备方法,以在陶瓷基 复合材料表面通过低温和快速工艺制备超高温陶瓷涂层,使陶瓷基复合材料克服耐高温抗 氧化性能差等缺点。 本发明的技术方案是,一种陶瓷基复合材料用耐高温涂层的制备方法,包括以下 步骤: S1:向硅溶胶中加入添加剂,混合,然后加入陶瓷粉末,在室温下磁力搅拌,形成含 陶瓷粉末的硅溶胶悬浮液; S2:用SiC砂纸对陶瓷基复合材料基体表面进行打磨处理,然后再用去离子水或有 4 CN 111718208 A 说 明 书 2/7 页 机物(无水乙醇)进行超声波清洗然后置于烘箱中烘干待用; S3:在真空条件下将经过步骤S2处理后的陶瓷基复合材料浸渍在S1得到的硅溶胶 悬浮液中进行真空整体浸渍; S4:将经过S3的陶瓷基复合材料取出,室温下晾干,然后在真空条件下或者惰性气 体环境下依次对所述陶瓷基复合材料进行模压凝胶化、裂解、冷却至室温; S5:重复上述S3到S4的过程若干次,得到耐高温陶瓷涂层; 其中上述耐高温陶瓷涂层是指陶瓷涂层耐1500℃高温氧化;步骤S4中的模压凝胶 化的温度为100~200℃,步骤S4中的裂解的温度为800~1000℃;所得耐高温陶瓷涂层与基 体具有≥10MPa的结合力;在1500℃氧化1h后的材料的强度保留率≥60%。 本发明通过将含陶瓷粉末的硅溶胶悬浮液以浸渍方式在处理过的陶瓷基复合材 料表面包覆、浸渍,然后依次经模压凝胶化、裂解处理,利用硅溶胶实现凝胶化,通过调整凝 胶化温度,使凝胶化程度完全从而提高陶瓷产率,得到超高温陶瓷涂层,涂层与基体表面结 合力强,耐高温性能优异。 进一步的,上述步骤S1中,陶瓷粉末为锆的氧化物、碳化物与硼化物中的一种或多 种组合,粉末的粒度大小为100目-200目,所述硅溶胶和陶瓷粉末的质量比为(1:1)~(1: 5)。 陶瓷粉末比例太高导致溶液较浓,不利于浸渍,太少导致溶液较稀,材料的浸渍周 期加长,不利于生产。 进一步的,上述步骤S1中,添加剂包括正硅酸乙酯和N,N-二甲基甲酰胺;所述硅溶 胶、正硅酸乙酯与N,N-二甲基甲酰的质量比为(1:0.1:0.1)~(1:0.2:0.2);所述搅拌的速 率为800~1500rpm,时间为1~2h。 正硅酸乙酯与N,N-二甲基甲酰胺分别作为抗凝胶剂和分散剂,可在室温下实现硅 溶胶的抗凝胶化,同时可以保持陶瓷粉末分散均匀。 进一步的,上述步骤S3中,所述真空整体浸渍的温度为常温,时间为4~8h,压力为 负压0.1MPa;所述步骤S4中的真空条件为负压0.1MPa。 负压下进行浸渍以促进硅溶胶悬浮液有效地浸渍进入复合材料表面。优选地,所 述真空整体浸渍的时间为6h。控制真空整体浸渍的时间以控制涂层的增重率。 进一步的,上述步骤S4中,所述模压凝胶化采用具有以下结构的模压工具操作,模 压工具包括外形尺寸匹配的上模板和下模板;下模板为中央有凹槽的板,上模板为中央有 凸起的板,所述凹槽与凸起在上模板与下模板贴合时位置相互匹配、外周尺寸相同且所述 凸起的高度小于所述凹槽的深度,以置放待压缩的预制件;上模板和下模板边缘各设置有 位置对应的连接孔,上模板和下模板利用螺栓经连接孔实现连接、压紧。 进一步的,上述上模板和下模板的材质为不锈钢,上模板和下模板的厚度各为 20mm;所述螺栓的材质为耐高温不锈钢。 本发明的模压工具简单、压力易控制:将预制件(表面浸渍有含陶瓷粉末的硅溶胶 悬浮液的陶瓷基复合材料板)放置于下模板上的凹槽内,盖合上模板,将螺栓穿过上模板和 下模板边缘上的连接孔,固定并压紧,并通过螺栓控制压紧力。可以看出,通过对模压工具 的固定位置及通孔设计,采用螺栓螺杆固定模压工具与预制件,并产生一定的压力;并通过 凹槽与凸起嵌合时形成的空隙高度设计控制预制件厚度。 5 CN 111718208 A 说 明 书 3/7 页 进一步的,上述步骤S4中,所述模压凝胶化的温度控制方法为:以10℃/min的升温 速率从室温升温至100~200℃,并在100~200℃下保温0.5~2h,优选升温至150℃保温1h; 所述裂解的温度控制方法为:以10℃/min的升温速率从室温升温至800~1000℃,优选900 ℃,并在最终温度下保温0.5~2h。 该工序下利用模具的重力与螺栓连接在实现凝胶化的同时控制产品厚度,无需采 用压机实现压力凝胶化,实现材料的快速制备。 凝胶化初胚在高温裂解生成超高温陶瓷涂层。 进一步的,上述步骤S5中,所述步骤S3到S4的过程重复4~6次,以保证浸渍完全。 进一步的,上述步骤S1中的磁力搅拌的速率为800~1500rpm,时间为1~2h。 充分搅拌以获得均匀的硅溶胶悬浮液 进一步的,上述步骤S2中,超声波清洗时间为20-40分钟;所述烘箱设置的温度为 70-90℃。 本发明提供的陶瓷基复合材料用涂层的一致性较好,涂层与基体具有较强的结合 力(≥10MPa),涂层具有较好致密性和完整性。1500℃氧化1h后的材料的强度保留率≥ 60%,具有较好的抗氧化性能。 与现有技术相比,本发明的有益效果有: 1、本发明的制备方法采用浸渍-模压交联-高温裂解工艺制备得到涂层,其中模压 交联是使硅溶胶悬浮液在低温下发生凝胶化;高温裂解实现硅溶胶的无机化。通过模压凝 胶化-高温裂解工艺实现硅溶胶的凝胶化与无机化,同时在无机化过程中无小分子挥发性 气体跑出,使产品的质量保持稳定。 2、本发明方法通过在原料中添加正硅酸乙酯与N,N-二甲基甲酰胺分别为抗凝胶 剂与分散剂,有效的阻止陶瓷粉末的加入造成的硅溶胶发生凝胶,分散剂使得陶瓷粉末在 硅溶胶中有效的分散,形成悬浮液。 3、本发明方法使用可控制压力的模压工具,通过模具设计控制预制件的厚度并提 供预定的压力,提高硅溶胶的陶瓷产率。 4、本发明方法使用的模压凝胶化和裂解的温度均在1000℃以下,既能保证陶瓷基 复合材料的性能不受影响,还能降低制备成本,所得陶瓷基复合材料用涂层的一致性较好, 涂层与基体具有较强的结合力(≥10MPa),涂层具有较好致密性和完整性。1500℃氧化1h后 的材料的强度保留率≥60%,具有较好的抗氧化性能。 本发明采用溶胶-凝胶工艺,将超高温陶瓷粉末添加到硅溶胶中,通过加入抗凝胶 剂与分散剂,将陶瓷粉末均匀分散在硅溶胶中,通过浸渍-模压交联-高温裂解工艺在陶瓷 基复合材料表面制备涂层,涂层与基体具有较强的结合力,涂层具有较好致密性和完整性。 附图说明 为了更清楚地说明本发明实施例或现有技术中的技术方案,下面将对实施例或现 有技术描述中所需要使用的附图作简单地介绍,显而易见地,下面描述中的附图仅仅是本 发明的一些实施例,对于本领域普通技术人员来讲,在不付出创造性劳动的前提下,还可以 根据这些附图示出的结构获得其他的附图。 图1为本发明实施例提供的陶瓷基复合材料用耐高温涂层的制备方法的流程示意 6 CN 111718208 A 说 明 书 4/7 页 图; 图2为本发明实施例使用的模压工具结构示意图,其中(a)为上模板相对于下模板 打开的状态;(b)为上模板与下模板相互盖合并压紧(中间有预制件时处于压紧状态)的状 态。