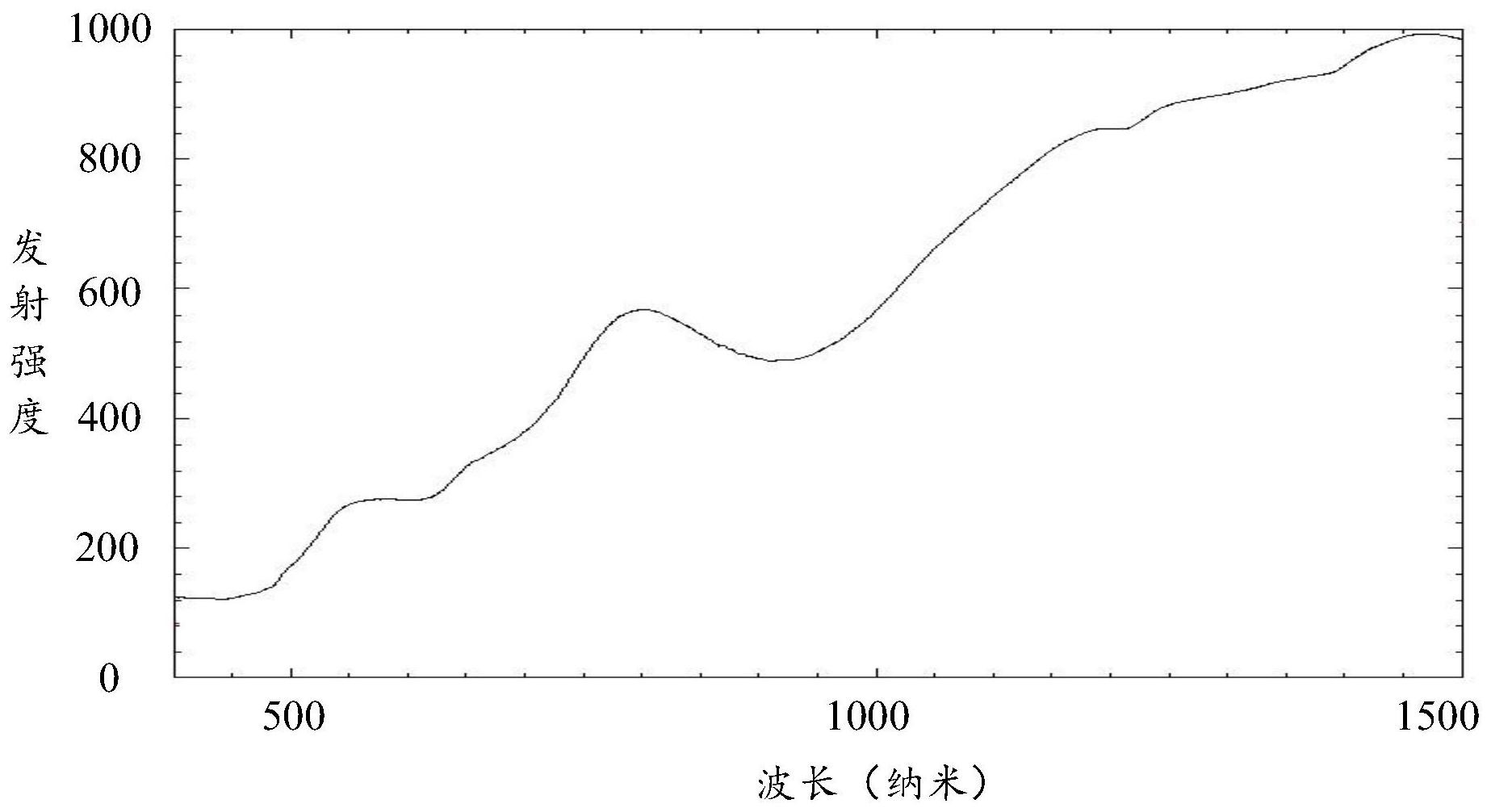
技术摘要:
本发明提供了磁性材料、磁性材料的制备方法和油墨。磁性材料包括:MpRqFexOy化合物;其中,M元素包括Y元素、Eu元素、Tm元素、Lu元素、Yb元素、Ho元素、Nd元素、Sm元素、Gd元素、Ga元素、Mn元素、Ni元素和Co元素中的至少之一或其组合,R元素包括Er元素、Ce元素、Bi元素 全部
背景技术:
磁性材料和针对磁性材料的磁化性能测试在防伪领域具有广泛的应用前景。 在利用磁性材料及其磁性特征进行防伪的相关技术中,主要以检测磁性材料的剩 磁指标作为主要的测试和防伪鉴别手段。其中,在磁化状态下,磁性防伪材料的剩磁越高, 则越有利于信号的检测,但剩磁越高,却越不利于防伪的隐蔽。 目前,相关技术中缺少一种能够既便于检测,由具有较高隐蔽性能的磁性防伪材 料。
技术实现要素:
本发明旨在解决上述技术问题的至少之一。 为此,本发明的第一目的在于提供一种磁性材料。 本发明的第二目的在于提供一种磁性材料的制备方法。 本发明的第三目的在于提供一种油墨。 为实现本发明的第一目的,本发明的实施例提供了一种磁性材料,包括:MpRqFexOy 化合物;其中,M元素包括Y元素、Eu元素、Tm元素、Lu元素、Yb元素、Ho元素、Nd元素、Sm元素、 Gd元素、Ga元素、Mn元素、Ni元素和Co元素元素中的至少之一或其组合,R元素包括Er元素、 Ce元素、Bi元素、Zn元素、Cr元素、Ca元素、Al元素、B元素和V元素中的至少之一或其组合。 本实施例可提供一种磁化率较高并且剩磁较低的磁性材料,利用该材料磁化率较 高的属性,可将应用于防伪鉴别。比如,采用本发明实施例的磁性材料印制钞票、证件、卡 件、有价证券等物品的防伪标识。由于本实施例的磁性材料的磁化率较高且剩磁较低,因此 其在防伪验证时易于检测,并具有较好的防伪隐蔽性,从而有效地提高产品的防伪鉴别层 次,增加产品被仿冒的难度。本发明实施例的磁性材料能够实现上述作用的原因在于,在 MpRqFexOy化合物中,R元素以掺杂的形式进入到M元素的氧化物的晶格内,从而改变晶体内 原子之间的磁矩,并使材料整个磁畴的磁矩发生变化,由此使得本实施例的磁性材料得到 了预期的磁性。因此,本实施例的磁性材料磁化率较高,剩磁较低,并且对红外光具有较高 反射率的磁性材料,其既便于检测,由具有较高隐蔽性能的磁性防伪材料。 另外,本发明上述实施例提供的技术方案还可以具有如下附加技术特征: 上述技术方案中,R元素的摩尔百分数q小于或等于O元素的摩尔百分数y的3%。 本实施例的磁性材料为具有石榴石结构的铁氧体。石榴石结构由氧离子堆积而 成,其晶体结构为四面体、八面体或十二面体。在石榴石铁氧体内,通过适当地掺杂,可以增 加材料中分子的磁矩,然而,过多的掺杂离子则会削弱磁性离子的交换作用。因此,本实施 例通过原料配比的控制,对化合物MpRqFexOy中各元素的含量,尤其是掺杂剂R元素的含量进 4 CN 111584177 A 说 明 书 2/10 页 行了控制,以保证磁性材料具有优异的磁防伪性能。 上述任一技术方案中,Fe元素的摩尔百分数x为2至5之间的任一整数;和/或O元素 的摩尔百分数为3至24之间的任一整数。 本实施例对原料中Fe元素和O元素的摩尔比例进行控制,以进一步保证磁性材料 具有优异的磁防伪性能。 上述任一技术方案中,磁性材料在0-300Oe范围内的最大质量磁化率大于或等于 0.4厘米3/克,最大质量磁化率为磁化强度与外加磁场强度的最大比值与质量相除之商; 和/或 和/或磁性材料在680纳米至2000纳米波长范围内的平均近红外光反射率大于或 等于50%;和/或磁性材料在800纳米波长的近红外光反射率大于或等于60%。 本实施例的磁性材料具有较高的近红外光反射率。利用此属性,可进一步增强本 发明实施例的磁性材料的防伪效果。本实施例的磁性材料具有较高的近红外光反射率的原 因在于,磁性材料一般都由具有活跃外围电子的元素构成,当波长为680纳米至2000纳米的 近红外光照射磁材料时,波长为680纳米至2000纳米的近红外光可以提供使得磁性材料中 电子由低能级向高能级的跃迁运动所需的能量,从而使得近红外光被磁材料吸收。正因为 如此,多数磁材料在680纳米至2000纳米的波长区域内多表现为红外反射率不高的属性。本 实施例提供的磁性材料通过非磁性离子的掺杂使材料中磁性离子电子排布发生变化,从而 使材料兼具有磁性的同时,亦可避免对红外光的强烈吸收,并避免因红外光辐照而出现的 电子跃迁的现象。因此,本实施例的磁性材料对680纳米至2000纳米的波长区域内的红外光 具有较高的反射率。尤其,本发明实施例提供的磁性材料在800nm处的反射率高于50%。 为实现本发明的第二目的,本发明提供了一种磁性材料的制备方法,适于制备如 本发明任一实施例的磁性材料,制备方法包括:步骤S100,将M元素的盐溶液、R元素的盐溶 液和Fe元素的盐溶液混合均匀,获得混合液;步骤S200,对通过步骤S100获得的混合液进行 喷雾造粒,获得微球;步骤S300,对通过步骤S200获得的微球进行预烧结,获得预烧结体;步 骤S400,对通过步骤S300获得的预烧结体进行研磨,获得预烧结粉体;步骤S500,对通过步 骤S400获得的预烧结粉体进行二次烧结,获得磁性材料。 本实施例的磁性材料的制备方法适于制备如本发明任一实施例的磁性材料,其具 有本发明任一实施例的磁性材料的全部有益效果,在此不再赘述。 上述技术方案中,在步骤S100中,M元素的盐溶液包括M元素的硝酸盐溶液、M元素 的硫酸盐溶液、M元素的盐酸盐溶液中的至少之一或其组合;和/或在步骤S100中,R元素的 盐溶液包括R元素的硝酸盐溶液、R元素的硫酸盐溶液、R元素的盐酸盐溶液中的至少之一或 其组合;和/或在步骤S100中,Fe元素的盐溶液包括Fe元素的硝酸盐溶液、Fe元素的硫酸盐 溶液、Fe元素的盐酸盐溶液中的至少之一或其组合。 采用上述盐溶液可获得溶解程度好且均质和均一性能好的混合液。 上述任一技术方案中,在步骤S300中,预烧结的烧结温度为700摄氏度至900摄氏 度,预烧结的烧结时间为1小时至5小时。 本实施例对预烧结的烧结温度和烧结时间进行控制,以保证磁性材料的理化性能 和磁性能。 上述任一技术方案中,在步骤S400中,研磨的研磨时间为4小时至8小时。 5 CN 111584177 A 说 明 书 3/10 页 本实施例对研磨的研磨时间进行控制,以保证磁性材料的粒度分布均匀,性能均 一稳定。 上述任一技术方案中,在步骤S500中,二次烧结的烧结温度为900摄氏度至1400摄 氏度,二次烧结的烧结时间为5小时至8小时。 本实施例对二次烧结的烧结温度和烧结时间进行控制,以保证磁性材料中R元素 以掺杂的形式充分占据M元素的氧化物的晶格,从而改变晶体内原子之间的磁矩,并使材料 整个磁畴的磁矩发生变化,由此使得本发明实施例的防伪材料得到了预期的磁性。 为实现本发明的第三目的,本发明的实施例提供了一种油墨,包括以下组分:如本 发明任一实施例的磁性材料,15至40质量份;颜料,15至25质量份;连结料,70至80质量份; 植物油,3至6质量份;溶剂,2至4质量份;助剂,1至3质量份;干燥剂,0.3至1质量份。 本实施例的油墨包括如本发明任一实施例的磁性材料,其具有本发明任一实施例 的磁性材料的全部有益效果,在此不再赘述。 本发明的附加方面和优点将在下面的描述部分中变得明显,或通过本发明的实践 了解到。 附图说明 本发明的上述和/或附加的方面和优点从结合下面附图对实施例的描述中将变得 明显和容易理解,其中: 图1为本发明一个实施例的磁性材料的反射图谱; 图2为本发明一个实施例的磁性材料的制备方法的步骤流程图。