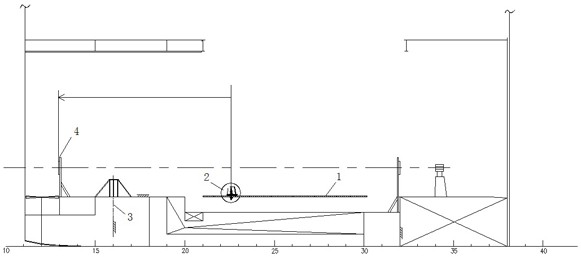
技术摘要:
本发明涉及一种建造工序前移逆向推进精度提高的工艺工法,属于船舶建造技术领域。它为了改变目前的传统造船法,改变了现有的船体误差累计对后期轮机工作的影响,将建造过程中的工序前移,参与到船体合拢过程中,并同时严格过程控制和跟踪,确保轮机安装工作的顺利和安 全部
背景技术:
现有技术下,随着建造材料、设备和人力资源等成本不断上升,如再依据传统造船 法,利润率将不断被压缩。目前国内造船法,均是依照“中国造船质量标准”中的8.1.2.2 的 要求“轴系找中前,机舱前壁往后、主甲板或强力连续甲板以下的全部船体结构和基座应装 焊、矫正结束,艉轴管按交验合格的船体中心线装焊完工,艉轴管、冷却水舱以及双层底舱 室密性试验结束”在机舱总组分段完成后,进行轴系找中的;在船体即成型的基层上进行轮 机设备,特别是拉线照光定位艉管的。 基于目前的船舶建造质量标准比较低:从板拼装在分段胎架上定位(船体标准是 标准小于5mm,极限是15mm)分段合拢的偏差和扭曲(船体标准是标准小于10mm,极限是 20mm)。 造船前程中的累计误差,往往需要轮机的轴系,舾装的舵系来补救,主要有如下情 况: 1.轮机在船体机舱成型的框架内,从艉柱后端点向前找中,艉管环氧厚度余量来借(补 救)。 2.轮机主机机械顶部支撑板船体侧加强板对筋偏离问题。 3.下舵承座和舵销承座镗孔,现有的方案是购买的铸钢件余量直径20mm,来补救, 遇到船体扭曲较大的,一边镗了15mm,对称的另一边只有5mm的情况时有发生。 4.如艉柱分段101和机舱总组(201&211PS&221PS)合拢扭曲,艉管环氧局部厚,艉 管环氧存在客观的厚薄不均匀性。 5. 中组102PCS 在合拢到机舱总段中,其合拢口的坡口收缩,焊接过程重心稳性 等船体问题,均有引起实际舵系偏离理论中线的可能。 6.有些船配有高效舵,高效舵的舵套筒需要提前在分段阶段焊接到位,一旦焊接 成型后,就不好动了。总组后,船体的合拢精度不好的话,(即粗拉线时,发现轴舵系的相交 度不达标时)舵系是不能再镗孔来补救的,此时可以调整的空间特别很小,即仅艉管的环氧 厚度余量来补救。 造船阶段过程中,很多时候做的不是选择题,有时左边是对,右边也是对。形象点 说:误差有累计、有叠加、也有相互抵消的,故很多时候,单独一个部门很难准确把握准确方 向,那么轮机人员提前参与进去,及时修正和减少船体建造误差累计叠加对后期轮机工作 的影响,这个很有必要性;小的方面减少轴舵系船体铸钢件上的镗孔余量、确保主机顶部支 撑船体筋板不再被割了再焊接;大的方面,船体实际线型流程,没有折角,提高船舶推进效 率;同时定向航行时,自动舵减少工作修正。 因此,为改变现状,研究一种改进造船法,从而缩短建造周期、提高精度,进一步提 3 CN 111591409 A 说 明 书 2/4 页 高利润的时效是迫在眉睫的。
技术实现要素:
本发明的目的是为了解决上述背景问题中提出的问题,提供一种建造工序前移逆 向推进精度提高的工艺工法,它是通过逆向反推:以结果为导向、以轮机为主线、调整和控 制船体合拢精度。 本发明的目的是这样实现的:一种建造工序前移逆向推进精度提高的工艺工法, 包括以下步骤: 准备工作:参与船体分段下料和合拢过程控制,相辅相成; 步骤一:从下料开始,责任部门自检、精控做二级检验并记录; 步骤二:结构组件拼板,板上画线,一级检验,二级检验; 步骤三: 焊接试验室参与并研究,逐步提高分段成型后的数据,精控协助; 步骤四:主机所在基座所在分段为201分段,201分段的主尺度报告中,在主机凹坑内前 后做分段中心线标记,分2级检验记录 步骤五:201分段搭载场地,相关责任方依据搭载场地的所定的船中线,校核并调整分 段中心线与合拢线在同一个纵向截面上; 步骤六:相关责任方依据主机船体基座凹坑的标记点,架设艏标杆,并做标记,分2级检 验记录; 步骤七:依据艏标杆确定第一个主机地脚螺栓孔的位置,并开孔; 步骤八:依据主机安装图的主机地脚螺栓孔位置,开主机地脚螺栓孔和主机回油口的 位置; 步骤九:以第一地脚螺栓为基准,向201分段后方Fr13肋位处架设辅助标杆; 步骤十:搭载211PS,212PS到201分段上,确保分段211PS,212PS的中心线和合拢线在同 一个纵向截面上; 步骤十一:合拢101分段到总组分段上:先分段中心线和合拢线在同一个纵向截面上, 同时保证艉铸钢件到辅助光靶的距离; 步骤十二:利用已确定的基准定位组合艉管的位置; 步骤十三:提前进主机,定位艉管的基准转移到辅助基准Fr13处; 步骤十四:打开曲轴的前后盖,由前向后,穿过曲轴中心向后照光定位艉管。 所述步骤十、步骤十一均是用可调的分段的支撑架精确调节。 所述可调的分段的支撑架是液压油缸式。 所述步骤十二中,艉管后端面距离第一个地脚螺栓的距离主机第一颗螺栓的距离 艉13416~13424mm。 所述步骤十三中,艉管后法兰面距离辅助光靶L5=5857±1 mm。 所述步骤十四中,曲轴中心设置有通孔。 相比于现有技术,本发明一种建造工序前移逆向推进精度提高的工艺工法具有以 下优点: 1、满足轴系和舵系的相交度要求; 2、相对传统造船法减少舵系铸钢件镗孔的余量; 4 CN 111591409 A 说 明 书 3/4 页 3、降低艉管环氧厚度局部太薄的风险; 4、减少主机机械顶部支撑的对筋“补救措施”; 5、中间轴承可以提前焊接; 6、主机可以在粗拉线后吊入机舱; 7、提前结束机舱结构顶板的临时大开口,减少对船体弹性变形和塑性变形的影响; 8、取消主甲板的临时盖板; 9、上建和烟囱可以提前搭载,最终缩短整个建造周期。 传统的所谓“船舶建造工序前移探究”主要精力在即成的船体结构上,提高预舾装 率来展开,形象点说,还是围绕“船老大”,展开如何减少船坞/船台阶段的周转率、提高分 段、总段的预舾装率以及扩大分段总组率,减少后期舾装作业对油漆破坏、污染程度,诸如 PSPC等涂层保护的研究工作;本发明所述的工艺工法,继续向前推进研究,积极参与到与轮 机密切相关的机舱分段的下料和合拢过程控制,与船体相辅相成,最终在满足船体要求的 同时,也满足轮机的安装要求,缩短后期“镗、削、借、补的余量”工作量。 本发明改变目前的传统造船法,改变现有的船体误差累计对后期轮机工作的影 响,工序前移参与到船体合拢过程中、严格过程控制和跟踪,确保轮机安装工作的顺利和安 全操作性,最终目的是缩短船舶建造周期,保证利润最大化。 附图说明 图1为本发明的轴系舵系拉线照光图。 图2为本发明轴系舵系拉线照光图的侧视图。 图3为本发明中的主机底座第一只螺栓孔中心的具体结构图。 图4为本发明中的主船体合拢结束后拉线照光图。 图5为本发明中的船体侧视面分段划分左半视图。 图6为本发明中的船体侧视面分段划分右半视图。 图7为本发明中船体的双层底分段划分左半视图。 图8为本发明中的船体上甲板分段划分右半视图。 图9为本发明中船体的一号平台处的分段划分图。 图10为本发明中船体的二号平台处的分段划分图。 图11为本发明中船体的基准FR39处的分段划分图。 图12为本发明中船体的基准FR10处的分段划分图。 图13为本发明中船体的船艉处的分段划分图。 其中:1、主机座面板;2、主机底座第一只螺栓孔中心;3、中间轴承中心线;4、光靶 B;5、主机飞轮法兰端面;6、光靶A;7、光靶C;8、光靶D;9、光靶E;10、艉柱件;11、舵系中心线; 12、中间轴承中心线;13、一号平台;14、二号平台;15、上甲板。