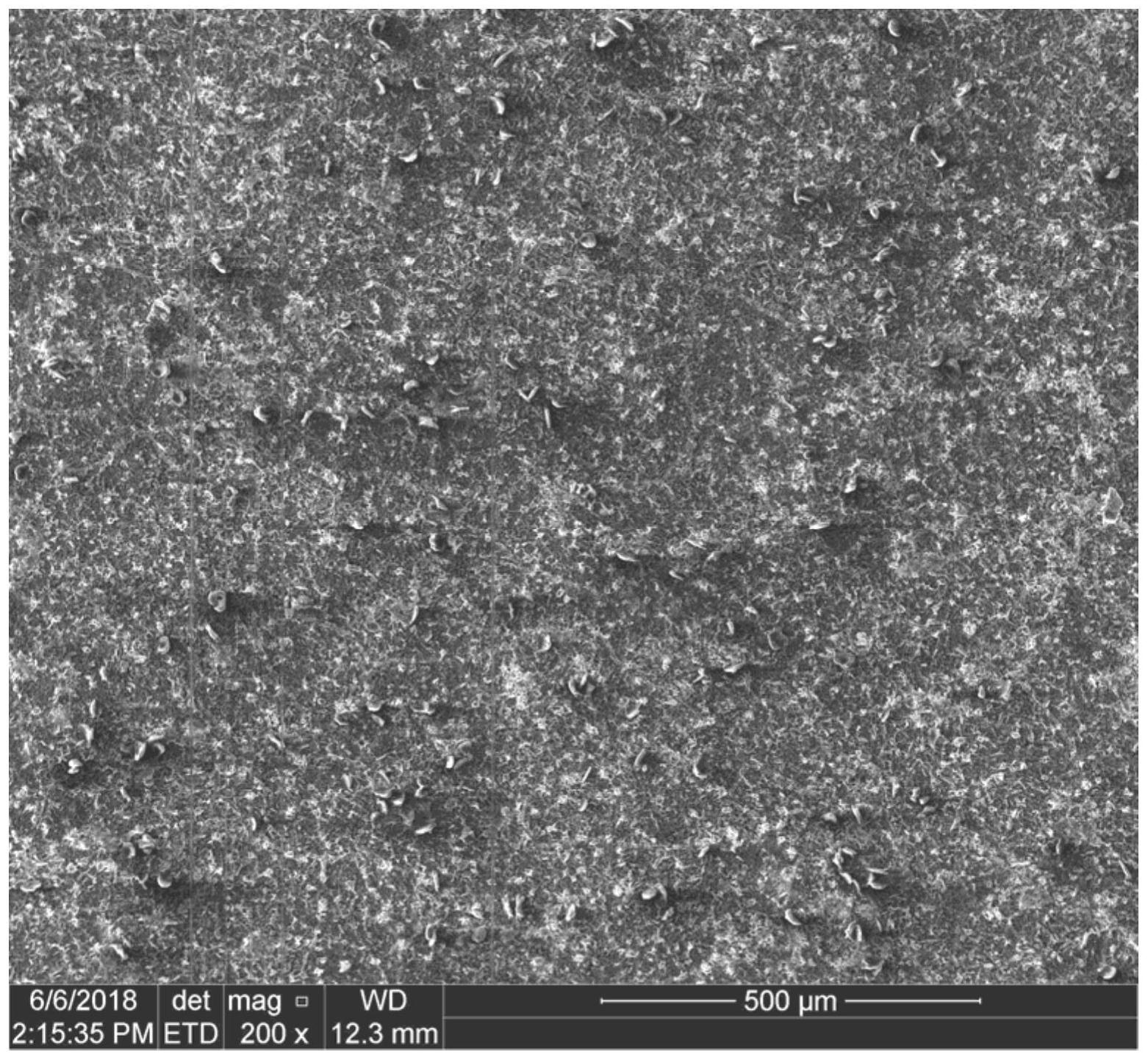
技术摘要:
本发明公开了一种具有优异涂装性能的热成形零部件用的镀铝钢板及其制造方法及热成形零部件,所述制造方法如下:冷轧带钢经清洗→连续退火→热浸镀→镀层厚度控制→合金化→冷却→涂油;热浸镀使用的镀液包括以下重量百分比的成分:Si:3.0~6.0%,Sn、Cu、Mo三者中的 全部
背景技术:
近年以来,节能减排法律法规的严格对车身轻量化提出了较高的要求。为实现车 身轻量化的同时保持安全性能,高强度零部件被大量应用于汽车车身制造。冷成形超高强 钢由于冲压过程中的回弹效应,在车身超高强零部件中的应用受到局限。热成形技术由于 零件尺寸精度高、无回弹效应、强度级别高而得到广泛应用普及。 在热冲压成形过程中,无涂层板的使用在加热过程中需要保护气氛防止钢板表面 的氧化,但在热冲压过程中,零部件表面仍会发生部分氧化需要后续进行喷丸处理,才能进 行焊装、涂装等后道工序。这大大增加了热成形零部件的成本,同时产生了环保压力。在装 车后,热成形零部件通常作用B柱等安全件,这些零件处于在车身空腔位置,容易发生电泳 不良的风险,在整车服役过程中,车身处于暴露于腐蚀环境中,零件容易产生锈蚀继而存在 引发安全问题的风险。因此,涂层热成形钢被不断开发出来以应对上述问题。其中Al-Si镀 层目前使用较广。 然而Al-Si镀层在热成形过程中与空气接触形成硅氧化物薄膜覆盖于表面,这层 氧化物不能被磷酸溶解而导致磷化膜无法生成。因此Al-Si镀层热成形钢零部件在装车涂 装时,不能形成质量好的磷化膜用来保证电泳漆层的粘附性和耐蚀性。在另外一方面,铝硅 镀层在热成形之后镀层间会形成大量裂纹,在电泳过程中,电泳漆渗入微裂纹区,在裂纹区 周围形成油漆较薄的区域,在宏观上造成油漆表面凹凸不平的外观,这些区域在腐蚀环境 中容易产生锈点。
技术实现要素:
为解决上述技术问题,本发明提供的一种具有优异涂装性能的热成形零部件用的 镀铝钢板及其制造方法,此种钢板在应用于制造热成形零部件,消除了因为微裂纹形成而 造成的凹凸不平的油漆外观,提升油漆之后的耐蚀性。 本发明还提供了一种热成形零部件,采用所述的镀铝钢板经热成形工艺制备得 到,其经磷化处理后,再经电泳涂装处理,得到的漆膜的外观平滑、附着力及耐腐蚀性良好。 本发明采取的技术方案为: 一种具有优异涂装性能的热成形零部件用的镀铝钢板的制造方法,包括以下步 骤: (1)将冷轧带钢清洗后进行连续退火,得到基板; (2)基板在镀液中进行热浸镀,所述镀液包括以下重量百分比的成分:Si:3.0~ 6.0%,Sn、Cu、Mo三者中的任意一种或多种的总含量为0.5~2.5%,剩余部分为Al和不可避 3 CN 111575622 A 说 明 书 2/6 页 免的杂质; (3)将热浸镀后的冷轧带钢入合金化炉进行合金化; (4)冷却; (5)涂油。 进一步地,步骤(1)中,所述冷轧带钢的制备工艺为:铁水预处理→转炉冶炼→合 金微调→精炼→连铸→热轧→酸洗冷轧。 步骤(2)中,基板入镀液温度620~680℃,热浸镀镀液温度600~660℃,浸镀时间2 ~6s。热浸镀温度过低或时间过短,基体镀层之间的扩散层未充分形成导致漏镀风险增加。 热浸镀温度过高或时间过长造成能耗较高及生产效率的降低。 步骤(2)中,所述热浸镀在连续热浸镀产线上进行,连续热浸镀产线配有合金化 炉;热浸镀时使用气刀吹扫控制镀层厚度控制。 步骤(3)中,基板以400~500℃温度进入合金化炉,合金化炉温度为550~700℃, 合金化时间3~20s。合金化温度过低或时间过短,对热成形后的涂装性能提升作用降低;合 金化温度过高,镀层表面质量下降;合金化时间过长则导致生产效率的降低。 步骤(3)中,合金化后镀层的厚度为6~20μm。 步骤(3)中,合金化炉使用还原性气氛或惰性气氛进行保护。所述还原性气氛优选 为N2和H2的混合气;所述惰性气氛为N2。 本发明还提供了一种具有优异涂装性能的热成形零部件用的镀铝钢板,采用上述 的制造方法制备得到。 进一步地,所述镀铝钢板包括基板和镀层,所述基板包括以下重量百分比的化学 成分:C:0.20~0.30%、Si:0.10~0.35%、Mn:0.9~1.60%、P:≤0.05%、S:≤0.05%、Al: ≤0.10%、Cr:0.10~0.80%、Mo:≤0.05%、B:0.0004~0.01%、N:≤0.01%、Ti Nb V:0.08 ~0.10%,余量为Fe和不可避免的杂质。 本发明还提供了一种热成形零部件,将所述的镀铝钢板经热成形工艺制备得到。 进一步地,所述热成形工艺为:加热温度860~940℃,加热时间2.0~5.0min,热成 形温度680~720℃,保压时间6~9s,热冲压后冷却速率为35~60s,出模温度≤200℃。 本发明提供的技术方案中,使用包括以下重量百分比的成分:Si:3.0~6.0%,Sn、 Cu、Mo的总含量为0.5~2.5%,剩余部分为Al和不可避免的杂质的镀液进行热浸镀,这样镀 液成分中的Si可在钢板表面形成Fe-Al-Si抑制层,可以有效阻碍脆性相Fe2Al5形成,提高镀 层粘附性。镀液成分中的Sn、Cu、Mo具有抑制热成形后镀层中微裂纹形成的作用,减小了电 泳涂装过程中的电泳漆液渗入微裂纹的几率;同时Sn、Cu、Mo在热成形过程中抑制硅氧化膜 的形成,促进热成形后磷化反应的进行。在Si含量低于3%时,Fe-Al合金层变厚,镀层粘附 性降低,Si含量大于6%时,影响镀层表面质量,根据以上情况,本发明镀液中添加Si含量控 制为3~6%;Sn、Cu、Mo的总含量低于0.5%,它们所发挥的抑制热成形后镀层中微裂纹形成 及抑制硅氧化膜的形成的效果不明显,而大于2.5%引起镀层表面质量的下降和镀液成本 的增加,因此本发明中需将三者的总含量控制在0.5~2.5%。 本发明在热浸镀产线上进行合金化处理,同时在合金化处理的过程中使用保护气 氛保护。这样做的益处在于:由于钢板是以热态进入合金化炉,可以在几秒内达到热成形过 程中1~3min才能达到的镀层合金化效果,同时在此过程中钢板被保护性气氛包围,镀层不 4 CN 111575622 A 说 明 书 3/6 页 发生氧化,因此总的暴露于空气中的时间减少,Si的氧化膜形成减少,热成形后钢板可磷化 性增强,磷化膜可覆盖部分镀层表面裂纹,提升电泳涂装之后的附着力、耐蚀性。 本发明通过对镀液成分、热浸镀工艺的控制获得了一种镀铝钢板,使用此种钢板 制造热成形零部件可消除传统铝硅钢板在电泳之后形成的凹凸不平的外观,提升了电泳涂 装之后附着力、耐蚀性。且使用本发明的钢板可以降低热成形过程中的加热时间或加热温 度。 附图说明 图1为实施例5中的镀铝钢板热成形后镀层磷化后的表面形貌; 图2为实施例5中的镀铝钢板热成形后镀层磷化后的放大的表面形貌(a)及图中A 点(b)和B点(b)处对应的成分; 图3为对比例中的镀铝钢板热成形后镀层磷化后的表面形貌(a)及放大的表面形 貌(b); 图4为实施例5(a)及对比例(b)中的热成形试样电泳涂漆后的外观。