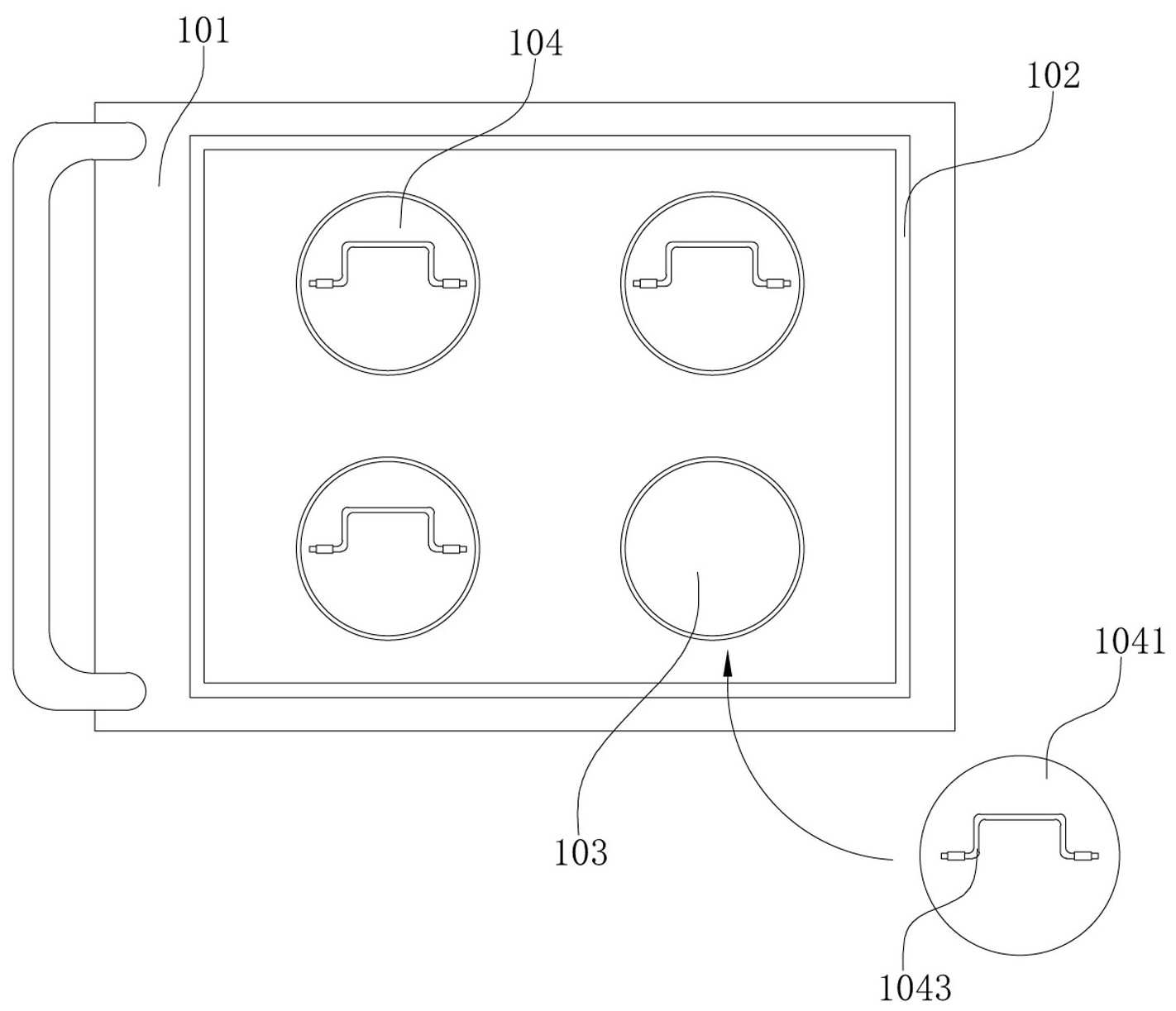
技术摘要:
本发明属于熔融纺丝技术领域。一种聚合物纤维纺丝组件拆分系统,用于实现纺丝组件拆分,具体包括保温台车、压力机、施力扳手、顶出装置、夹持器、内芯分解装置和分离刀,保温台车用于纺丝组件的存储和保温;压力机用于对纺丝组件的导流板施压,压力机的压力头与导流板 全部
背景技术:
熔融纺丝,是以聚合物熔体为原料,采用熔融纺丝机进行纺丝的一种成型方法。 熔体纺丝时,本体聚合物在熔化后被送入纺丝部位,经纺丝泵定量送入纺丝组件, 过滤后,由喷丝板的毛细孔中挤出。液态丝条通过冷却介质时逐渐固化,而后由下方的卷绕 装置高速拉伸成丝,该丝为初生纤维,初生纤维经过后加工成为纤维。为不使丝条冷却过速 难于成丝,有时采用等温熔体纺丝,即在喷丝板外加一个等温室(称纺丝甬道)。卷绕装置的 拉伸速度很高,可达1500~3000 m/min,视材料种类及流变性质而定。熔体纺丝的拉伸比很 大,产率很高,且可在较大的范围内调节。涤纶(聚酯纤维)、锦纶和聚丙烯纤维均是按熔体 纺丝成型的。 聚合物纤维纺丝组件决定着纺丝品种、质量和物性等指标。为了保证机台上组件 的纺丝质量,下机台的组件要经过煅烧、分解、盐浴、超声波清洗、全自动检测等多个工序的 处理,通常将下机组件直接装炉进行整体煅烧,采用此种煅烧方式,发现喷丝板砂盒微孔内 仍存有大量碳化物残渣、杂质或毛刺、堵孔、半堵孔等现象,需再次进行烧却,同时喷丝板随 着使用次数的增加,微孔内杂质逐渐变多、孔径逐渐变小,装机后飘丝、堵孔、板面漏胶,影 响可纺性。基于以上原因,本项目对现有纺丝组件烧却工艺进行优化,改善组件的处理效 果。
技术实现要素:
本发明目的是针对上述存在的问题和不足,提供一种聚合物纤维纺丝组件拆分系 统及拆分方法,其结构设计合理,能够大大提高拆分效率,并对拆分后的各部件进行烧却, 提高了清理效率,降低了作业难度,使得各个工序有序进行。 为实现上述目的,所采取的技术方案是: 一种聚合物纤维纺丝组件拆分系统,用于实现纺丝组件拆分,具体包括: 保温台车,其用于纺丝组件的存储和保温; 压力机,其用于对纺丝组件的导流板施压,所述压力机的压力头与导流板对应贴合; 施力扳手,所述施力扳手包括作业端和施力臂,所述作业端与锁紧螺母匹配; 顶出装置,其用于将纺丝组件中的组件内芯脱离顶出壳体; 夹持器,其用于纺丝组件的夹持移送; 内芯分解装置,其用于将砂盒上的铝环挤压变形;以及 分离刀,用于部件分离和残余物料的清理。 所述保温台车包括: 台车本体; 4 CN 111604351 A 说 明 书 2/8 页 保温箱体,其设置在所述台车本体上; 保温腔,所述保温箱体上设置有多个保温腔,所述保温腔与所述保温箱体之间填充有 保温层; 保温盖,各所述保温腔的顶部均对应设置有保温盖;以及 抓提手,其设置在所述保温箱体的侧部。 所述抓提手包括第一臂杆和第二臂杆,所述第一臂杆和所述第二臂杆均呈L型,在 所述第一臂杆和所述第二臂杆的第一端部均设置有抓钩,所述第二臂杆的第二端部设置有 连接竖杆,连接竖杆与所述第一臂杆的中部铰接; 所述保温腔包括保温底撑板和金属网侧壁;所述保温盖包括盖体、设置在所述盖体下 部的隔热块和设置在所述盖体上部的把手,所述隔热块为锥台结构。 所述保温箱体内还设置有加热腔,各所述保温腔的周边均盘绕有加热流道,所述 加热流道与所述加热腔连通,在所述加热腔内设置有加热器;还包括温控单元,所述温控单 元检测保温腔内的温度并控制所述加热器工作。 所述夹持器包括: 第一夹持板; 第二夹持板,所述第一夹持板和所述第二夹持板均呈圆弧形,所述第一夹持板和所述 第二夹持板的第一端部通过铰接轴铰接;以及 夹持臂,所述第一夹持板和所述第二夹持板的第二端部均设置有夹持臂。 所述铰接轴上设置有扭簧,所述第一夹持板和第二夹持板上均设置有扭力孔,所 述扭簧的两个作业部分别与所述第一夹持板和所述第二夹持板的扭力孔对应设置; 所述夹持臂包括臂杆和设置在臂杆端部的握持部,所述第一夹持板和第二夹持板均为 弹性板。 所述防滑部包括设置在所述第一夹持板和第二夹持板中部的耐热防滑板、和/或 设置在所述耐热防滑板两侧的筋板,所述筋板上设置有多道防滑齿,所述耐热防滑板的外 端面较所述筋板的外端面高,所述耐热防滑板和所述筋板均与所述第一夹持板和第二夹持 板通过螺栓连接固定。 所述内芯分解装置包括: 定位座,其固定设置在工作台上,所述定位座上设置有圆弧形的定位槽,所述定位槽的 上部设置有上限位凸台;以及 切刀,其铰接设置在工作台上,所述切刀包括变形刀头和驱动柄,所述变形刀头与所述 定位座的定位槽上部对应设置。 还包括卡旋扳手,所述卡旋扳手包括盘体和设置在所述盘体上的两个旋转臂,所 述盘体下部设置有与所述锁紧螺母匹配的卡旋块;所述分离刀包括分离刀柄和分离刀片, 通过所述分离刀片插入相邻两贴合部件的缝隙,并将两部件分离;所述顶出装置包括定位 套筒、设置在定位套筒底部的升降顶杆和驱动所述升降顶杆的驱动动力推杆。 一种聚合物纤维纺丝组件拆分方法,利用上述的聚合物纤维纺丝组件拆分系统进 行纺丝组件的拆分,其特征在于,具体包括以下步骤: 保温:将纺丝组件从纺丝机上拆卸下来,并放入保温台车内进行保温; 施压:将保温台车中的纺丝组件提送至压力机上,通过压力机对导流压盖施压后,再对 5 CN 111604351 A 说 明 书 3/8 页 锁紧螺母施力,使得锁紧螺母松动; 顶出:将锁紧螺母松动后的纺丝组件提送至顶出装置,卸下锁紧螺母,并将组件内芯顶 出壳体; 初步分离:将组件内芯已送至分解工作台上,将导流板、喷丝板和砂盒进行分离,并对 喷丝板和导流板上的残余物料进行清理; 砂盒分离:将砂盒内的铝环进行挤压变形,并取出铝环,清除砂盒内的金刚砂、粘网和 残余物料; 将分离后的各部件运送至烧却现场,摆放入烧却栏,等待烧却清理。 采用上述技术方案,所取得的有益效果是: 本申请保温台车通过设置保温腔和保温盖,能够避免拆卸后的纺丝组件的温度降低导 致拆分困难的问题,使得后续的拆分工作能够顺利进行;在作业过程中,通过配套的抓提 手,能够方便的进行纺丝组件的抓取,操作便捷。通过加热腔的结构设计,能够避免因为长 时间的放置导致的纺丝组件温度降低的问题,便于根据周期长短进行温度的调整和控制, 使得其各个工序之间的更为协调。抓提手的结构简单,抓取可靠稳定,能够在狭小的保温腔 内进行操作,且与纺丝组件的结构相匹配,从而保障了抓取和移动过程中安全,避免坠落导 致的安全隐患。本申请的保温盖保温性能更好,与保温腔的匹配定位使得其密封性好,且便 于进行操作。 本申请的夹持器便于进行纺丝组件的夹持和移动,夹持效果好,夹持稳定,避免纺 丝组件坠落造成的安全隐患,大大提高了整个拆分过程的便捷性和效率。 本申请的第一夹持板和第二夹持板的结构设计,能够保障夹持板与纺丝组件具有 足够的夹持力和摩擦力,从而避免纺丝组件的滑落,其夹持臂的结构设计,能够便于操作, 握持更方便,更便于施力,在提拉、推送等过程中,操作效率高,降低劳动强度;扭簧的结构 设计,能够使得第一夹持板和第二夹持板具有一定的夹持力,在夹持过程中,扭簧提供一定 的作用力,从而便于实现定位、初步夹持、施力夹持、夹持移动的过程的转变。 本申请内芯分解装置结构设计合理,能够快速实现定位,并对铝环进行挤压变形, 提高拆分效率,降低操作难度。过对定位座的结构设计,一方面能够保障其稳定支撑;另一 方面上限位凸台的设计,能够使得切刀有效的定位和导向,避免切刀与铝环接触不稳定,提 高在施力过程中的稳定性。 本申请整个系统额设置,能够使得各个工序间的协调和转换更为方便,使得纺丝 组件得到高效的拆分,并进行拆分状态下的烧却,降低了作业难度,提高了作业效率,保障 了烧却清理的质量。 附图说明 为了更清楚地说明本发明实施例的技术方案,下文中将对本发明实施例的附图进 行简单介绍。其中,附图仅仅用于展示本发明的一些实施例,而非将本发明的全部实施例限 制于此。 图1为纺丝组件的结构示意图。 图2为根据本发明实施例的纺丝组件拆分系统的保温台车的结构示意图之一。 图3为根据本发明实施例的纺丝组件拆分系统的保温台车的结构示意图之二。 6 CN 111604351 A 说 明 书 4/8 页 图4为根据本发明实施例的纺丝组件拆分系统的保温台车的结构示意图之三。 图5为根据本发明实施例的抓提手的结构示意图。 图6为根据本发明实施例的纺丝组件拆分系统的夹持器的结构示意图。 图7为根据本发明实施例的第一夹持板和第二夹持板的连接结构示意图。 图8为根据本发明实施例的第一夹持板或第二夹持板的正视结构示意图。 图9为根据本发明实施例的第一夹持板或第二夹持板的侧视结构示意图。 图10为根据本发明实施例的夹持臂结构示意图。 图11为根据本发明实施例的内芯分解装置的结构示意图。 图12为根据本发明实施例的定位座的结构示意图。 图13为根据本发明实施例的切刀与定位单元的结构示意图。 图14为根据本发明实施例的定位座和定位单元的俯视结构示意图。 图15为根据本发明实施例的切刀的结构示意图。 图16为根据本发明实施例的施力扳手的结构示意图。 图17为根据本发明实施例的分离刀的结构示意图。 图18为根据本发明实施例的顶出装置的结构示意图。 图19为根据本发明实施例的卡旋扳手的结构示意图。 图中序号: 101为台车本体、102为保温箱体、103为保温腔、104为保温盖、1041为盖体、1042为隔热 块、1043为把手、105为抓提手、1051为第一臂杆、1052为第二臂杆、1053为抓钩、1054为连接 竖杆、106为保温层、107为加热腔、108为加热流道、109 为加热器; 201为第一夹持板、202第二夹持板、203为夹持臂、204为铰接轴、205为扭簧、206为扭力 孔、207为臂杆、208为握持部、209为耐热防滑板、210为筋板、211为防滑齿、212为螺栓; 301为定位座、302为切刀、303为工作台、304为耐磨板、305为定位槽、306为变形刀头、 307为驱动柄、308为定位套、309为切刀铰轴、310为轴承、311为支撑台肩、312为螺母、313为 下底板、314为上限位凸台; 401为作业端、402为施力臂、403为分离刀柄、404为分离刀片、405为盘体、406为卡旋 块、407为旋转臂; 501为定位套筒、502为升降顶杆、503为驱动动力推杆; 601为壳体、602为锁紧螺母、603为导流板、604为砂盒、605为分流块、606为喷丝板、607 为铝环、608为导流压盖。