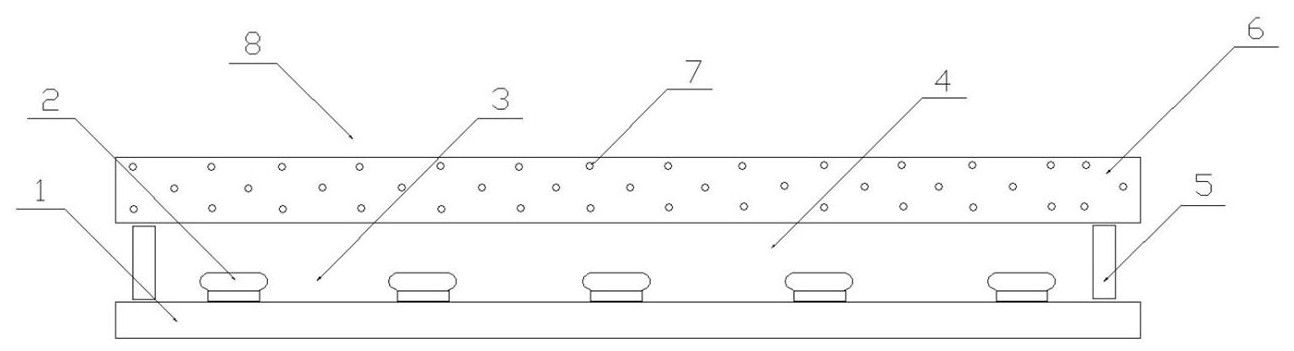
技术摘要:
本发明公开一种拼装式MiniLED量子点微晶发光面板,包括电路基板,所述电路基板上焊接有MiniLED芯片,所述焊接好MiniLED芯片的电路基板上覆盖有保护胶体材料和扩散材料;所述电路基板上设有多个连接端子,多个电路基板通过连接端子可拼装地连接;所述电路基板上附着有量 全部
背景技术:
背光模组的液晶显示器相比现有技术具有较高的色彩饱和度,尤其是其色彩饱和 度为相对于NTSC的标准的90%以上。 但目前将量子点制作在膜片上的工艺尚未成熟,大面积的量子点膜片制备良率不 高,或者由于设备限制根本无法进行大面积的量子点膜片的制备。因此,大尺寸的背光模组 若需要采用量子点膜片,则需要进行特殊的结构设计。 另外,传统背光方式的缺点:1、不管是直下式或侧入式的,亮度损失严重,效率低, 功耗大;2、扩散不均匀,容易造成显示屏幕的亮度不均;3、组装工序多,良率不高,费工费 时;4、达到要求的效果,要用多层功能膜,材料成本高。
技术实现要素:
针对上述问题,本发明提出了一种拼装式MiniLED量子点微晶发光面板及其制备 方法,使得能够获得具有较高色彩饱和度的液晶面板。 本发明提出了一种拼装式MiniLED量子点微晶发光面板,包括电路基板,所述电路 基板上焊接有MiniLED芯片,所述电路基板上焊接了MiniLED芯片的一端覆盖有保护胶体 层,所述保护胶体层内设有扩散材料;所述电路基板上设有多个连接端子,多个电路基板通 过连接端子可拼装地连接成标准拼装单元;所述保护胶体层上附着有量子点微晶层,所述 量子点微晶层为固化量子点微晶的保护胶体层或固化量子点微晶的塑料膜。 所述量子点微晶层里的量子点微晶的粒径为0.1-50μm。 所述量子点微晶为绿色量子点微晶和/或红色量子点微晶。 所述保护胶体层内加的扩散材料为有机扩散材料,所述有机扩散材料包括苯乙烯 型或丙烯酸树脂。 所述电路基板为柔性电路板。 一种拼装式MiniLED量子点微晶发光面板的制备方法,包括如下步骤: 1)在电路基板上焊接MiniLED芯片,在焊接有MiniLED芯片的电路基板上覆盖保护胶体 层,所述保护胶体层内设有扩散材料; 2)将多个电路基板通过连接端子拼装连接做成标准拼装单元; 3)将量子点微晶和胶体混合,得到量子点微晶胶液; 4)将量子点微晶胶液用覆膜的方式或印刷或喷涂的方式,覆盖在拼装好的标准拼装单 元的保护胶体层上得到量子点微晶层,所述量子点微晶层的厚度为50~400μm; 5)所述量子点微晶胶液亦可喷涂到塑料膜上,再将塑料膜覆盖在标准拼装单元上的保 护胶体层上。 3 CN 111583816 A 说 明 书 2/3 页 所述量子点微晶层较佳的厚度为 100~300μm。 所述胶体为UV胶、紫外光固化胶或热固化胶,优选为紫外光固化胶,是一种必须通 过紫外线光照射才能固化的一类胶粘剂,在本发明中作为粘接剂使用。 步骤4)印刷前优选将印刷油墨进行真空脱泡。 一种拼装式MiniLED量子点微晶发光面板应用于照明方面。 本发明的有益效果:1)厚度比传统方式小,是直下式的五分之一以上,非常地薄, 亮度损失小,达到同样的亮度,功耗小,节能30%以上;2)亮度均匀,看不到明暗分别,形成一 个完美的发光面;3)大大简化了后续的电视机组装,提高产品的良率,降低组装成本;可以 不使用功能膜,大大降低扩散的材料成本。 附图说明 图1显示了本发明实施例1所述一种拼装式MiniLED量子点微晶发光面板的标准拼 装单元的结构示意图; 图2显示了本发明实施例1所述一种拼装式MiniLED量子点微晶发光面板的量子点微晶 层的结构示意图。 图3显示了本发明实施例1所述一种拼装式MiniLED量子点微晶发光面板的量子点 微晶层的剖面示意图。 所述部件的标号:1.电路基板,2. MiniLED芯片,3.保护胶体层,4.扩散材料,5.连 接端子,6.标准拼装单元,7.量子点微晶层,8.量子点微晶,9.塑料膜。