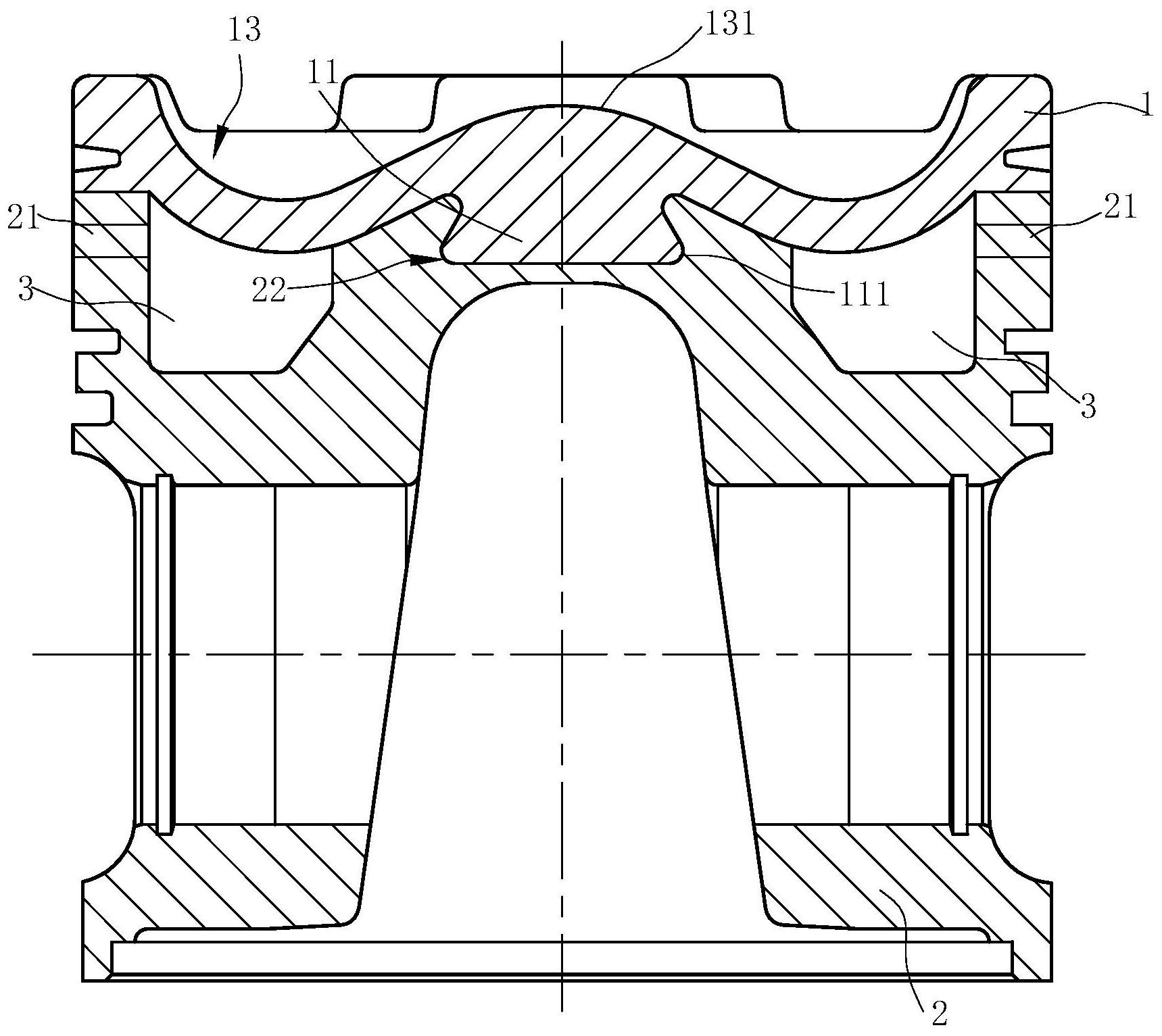
技术摘要:
本发明涉及一种活塞及其制备方法,其中,一种活塞,包括活塞头部及位于活塞头部下方的活塞裙部,其特征在于:所述活塞头部和活塞裙部的对接面之间匹配设置有用来限制两者产生上下移动的第一凸部和第一凹槽,所述第一凸部的端部具有侧向外伸的齿部,所述第一凹槽在对应 全部
背景技术:
活塞作为大功率柴油机最为关键的零件之一,工作条件相当恶劣,高温、高压和高 速往复运动要求活塞具有高强度、高耐磨性、高耐热性、高疲劳性能和低热膨胀、高热传导、 轻量化等综合性能要求。 目前大功率柴油机钢顶铝裙组合式活塞,钢顶采用锻造工艺成形,活塞裙用铸造 或锻造工艺成形,钢顶铝裙之间采用螺栓连接。如中国实用新型专利《一种使用寿命长的汽 车活塞》,其专利号为CN201920206555.X(授权公告号为CN209838550U)公开了一种使用寿 命长的汽车活塞,包括活塞头部和活塞裙部,所述活塞头部上表面的中部开设有螺纹孔,所 述螺纹孔的周向活动安装有活塞垫圈,所述活塞头部的正面开设有第一圆环槽,所述第一 圆环槽的下表面开设有第二圆环槽。又如中国发明专利申请《一种发动机活塞》,其专利申 请号为CN201410620892.5(申请公开号为CN105332813A)公开了一种发动机活塞包括活塞 头部和活塞裙部,活塞头部和活塞裙部为分体式结构;活塞头部加工有环槽、燃烧室和内冷 却油道,活塞头部内腔中间设置有一个单独的中置销座,中置销座远离活塞头部的一端加 工有与活塞头部轴线相垂直的销孔;活塞裙部为筒状;活塞头部的中置销座从活塞裙部的 一端穿入其筒形的内腔;活塞裙部相对于贯穿入其内腔的中置销座,在侧壁上设置有与中 置销座的销孔同轴线的销座孔,活塞头部和活塞裙部通过上述结构实现三销座结构的销连 接。 上述结构活塞钢顶都比较厚(约占活塞高度的1/5~1/3),螺栓连接方式可靠性 差,在使用过程中由于钢和铝的热膨胀系数不同,容易导致螺栓连接失效,造成钢顶脱落; 另外,活塞重量比较大会使活塞在运动过程中的惯性增加,同样会导致活塞过早失效;此 外,这种活塞热传导能力低、制造成本比较高。 因此,需要对现有的活塞作进一步的改进。
技术实现要素:
本发明所要解决的第一个技术问题是针对上述现有技术的现状,提供一种连接牢 固且活塞头部不易脱落的活塞。 本发明所要解决的第二个技术问题是,提供一种上述活塞的制备方法。 本发明解决上述第一个技术问题所采用的技术方案为:一种活塞,包括活塞头部 及位于活塞头部下方的活塞裙部,其特征在于:所述活塞头部和活塞裙部的对接面之间匹 配设置有用来限制两者产生上下移动的第一凸部和第一凹槽,所述第一凸部的端部具有侧 向外伸的齿部,所述第一凹槽在对应齿部的位置上具有与齿部相匹配的齿槽,所述活塞头 部通过第一凸部和第一凹槽的限位配合而安装在所述活塞裙部上。 第一凸部可以形成在活塞头部的下表面上,第一凹槽形成在活塞裙部的上表面 4 CN 111608818 A 说 明 书 2/4 页 上,也可以采用:第一凸部形成在活塞裙部的上表面上,而第一凹槽形成在活塞裙部的下表 面上,但是优选地,所述第一凸部设置在所述活塞头部的下表面邻近中间的位置上,且向下 延伸,所述齿部有多个,且沿周向间隔布置在所述第一凸部下端的外周壁上,所述第一凹槽 形成在所述活塞裙部的上表面上且向下凹陷。如此,使得活塞头部和活塞裙部连接更加牢 固。 为了进一步增加活塞头部和活塞裙部连接的牢固性,所述活塞头部和活塞裙部的 对接面之间匹配设置有用来限制两者上下移动的第二凸部和第二凹槽,所述第二凸部与第 一凸部或第一凹槽间隔布置,所述第二凸部的端部具有侧向外伸的延伸部,所述第二凹槽 在对应延伸部的位置上开设有与所述延伸部相匹配的容置槽。如此,活塞头部通过第一凸 部和第一凹槽及第二凸部和第二凹槽的匹配连接而限位在活塞裙部,无需设置螺栓,在保 证连接牢固性的同时降低了成本。 第二凸部的纵截面可以呈L形,也可以呈T形,但是从连接牢固角度来讲,优选地, 所述延伸部为由所述第二凸部的周壁向外延伸而形成,所述第二凸部的纵截面整体基本呈 T形或倒T形。 第二凸部可以形成在活塞裙部的上表面上,也可以形成在活塞头部的下表面上, 但是优选地,所述第二凸部形成在所述活塞裙部的上表面邻近边沿的位置且向上延伸,所 述第二凹槽形成在所述活塞头部的下表面上且向上凹陷,所述第二凹槽的纵截面基本呈T 形。 为了增加活塞头部和活塞裙部的周向连接,所述第二凸部和第二凹槽成组设置, 且至少有两组,并沿周向间隔布置在所述第一凸部或第一凹槽的外围。 优选地,所述活塞头部和活塞裙部之间形成有呈环状的冷却油道,所述冷却通道 内的顶面向下弯曲,且该冷却油道位于所述第一凸部和第二凸部之间。如此,冷却油道与活 塞头部的接触面积增大,使得对活塞头部的冷却作用增强,提高了活塞的耐热能力。 本发明解决上述第二个技术问题所采用的技术方案为:一种上述活塞的制备方 法,其特征在于,依次包括以下步骤: S1:将合金钢锻造后加工成所述的活塞头部的形状; S2:将活塞挤压铸造模具安装到挤压铸造设备上,使其工作正常; S3:将铝合金放入熔炼电炉中进行熔化、精炼、变质处理,并将铝合金熔液的温度 稳定在750℃~760℃; S4:将活塞挤压铸造模具进行预热,其预热温度为T0; S5:将成形冷却油道的陶瓷可溶盐芯及活塞头部进行预热,预热温度为T1,T1>T0; S6:将陶瓷可溶盐芯放置在活塞头部对应冷却油道的位置上,随后将活塞头部放 置到活塞挤压铸造模具内,该活塞头部的第一凸部朝上,随后向活塞挤压铸造模具中浇入 步骤S3的铝合金熔液,合模加压,保压后开模取出铸件; S7:用水将陶瓷可溶盐芯溶解掉,制备得到具有冷却油道的活塞。 具体地,在步骤S4中的预热温度T0为200℃~280℃;在步骤S5中的预热温度T1为 500℃~550℃,预热时间为1h~2h;在步骤S6中的加压压力为100MPa~120MPa,保压120s~ 180s。模具温度过低,会导致铝合金熔液与活塞头部结合不良,裙部也容易形成冷隔、浇不 足等缺陷,温度过高,挤压铸造过程中铝合金熔液在合模加压时溅出,模具寿命会显著降 5 CN 111608818 A 说 明 书 3/4 页 低,因此,T0采用200℃~280℃;预热温度T1过低在挤压铸造过程中会导致陶瓷盐芯急剧受 热产生裂纹,铝液挤入陶瓷盐芯中,阻断内冷油腔畅通,活塞报废;预热温度T1过高,陶瓷盐 芯和活塞膨胀量过大,导致变形。压力过高时间过长,导致陶瓷盐芯断裂过低,压力过低时 间过短,裙部铝合金组织不致密与头部的结合率会有所降低。 具体地,所述活塞头部采用38MnVS6钢或者42CrMo钢。其耐热性能和体积稳定性 好。 与现有技术相比,本发明的优点在于:该活塞的活塞头部和活塞裙部通过相匹配 的第一凸部和第一凹槽相固定连接,其中,第一凸部的周壁上具有齿部,而第一凹槽内具有 与齿部相匹配的齿槽,则第一凸部和第一凹槽的匹配连接限制活塞头部和活塞裙部产生上 下相对移动,如此,使得活塞头部和活塞裙部的连接更加地牢固,避免了现有技术中采用螺 栓连接所引起的活塞失效的问题;活塞的制备方法简单,制造成本降低。 附图说明 图1为本发明实施例一的剖面图; 图2为图1中的活塞裙部的剖面图; 图3为实施例一中的活塞裙部的俯视图; 图4为实施例一中的活塞头部的仰视图; 图5为实施例一中在第二凸部所在位置处的局部剖面图; 图6为图5中的活塞头部的局部剖面图; 图7为图5中的活塞裙部的局部剖面图。