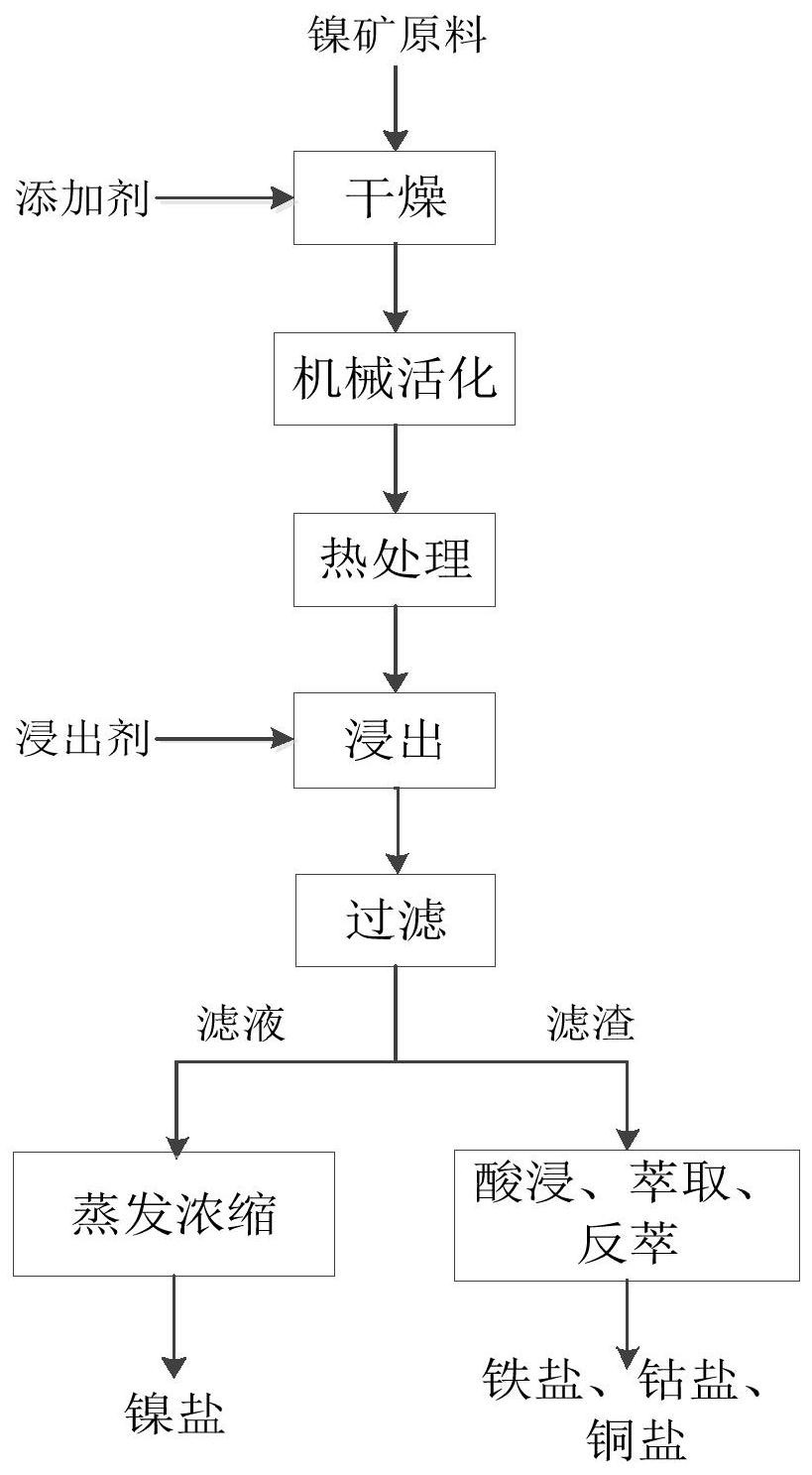
技术摘要:
本发明提供了一种从镍矿中提取镍元素的方法,所述方法包括以下步骤:将镍矿原料与添加剂混合后进行机械活化,然后进行热处理;所得产物用浸出剂浸出,固液分离,得到富镍溶液和固体渣;富镍溶液制得镍盐,固体渣分别制得相应盐类。本发明采用机械活化后热处理的方法, 全部
背景技术:
镍是一种重要的战略金属元素,可广泛应用于不锈钢、高温合金、电镀和化工等行 业。自然界中镍矿资源主要分为硫化镍矿和红土镍矿,其中,硫化镍矿占比40%左右,其余 为红土镍矿,而受红土镍矿选冶技术的限制,目前镍工业中镍的主要来源是硫化镍矿,因 此,对硫化镍矿的处理工艺仍需不断改进,以满足各行业对镍的需求。 目前,硫化镍矿的处理工艺一般可分为火法和湿法,火法处理工艺是采用造锍熔 炼,将硫化镍矿中的镍熔炼成低镍锍,再将低镍锍用转炉吹炼成高镍锍,再经不同精炼方法 生产出不同的镍产品,其主要的工艺有硫化镍矿鼓风炉熔炼、硫化镍矿电炉熔炼、硫化镍矿 闪速熔炼和硫化镍矿熔池熔炼等。硫化镍精矿是硫化镍原矿经选矿处理达到一定指标的精 矿,实际上以铁为主,其含量远高于镍、铜、钴等。CN 104152714 A公开了一种硫化矿镍铜火 法冶炼与提铁方法,该方法以生石灰、石英砂和镍矿的混合物为原料在冶炼炉中冶炼铜和 镍,以炉渣为原料在还原炉中提取铁。但在火法处理过程中,铁最终以氧化物的形式进入渣 中,且造渣时还需配入二氧化硅等造渣剂,目前硫化镍精矿冶炼厂的废渣排放量大,且存在 回转窑结圈等问题。 湿法处理工艺一般是指将镍矿石浸出到溶液中的提镍过程,其主要工艺有加压浸 出法、氯化浸出法和焙烧浸出法等,浸出既可用酸液,也可用碱液。CN 105755283 A公开了 一种氯盐选择性浸出红土镍矿中有价金属的方法,将矿样破碎研磨后,采用盐酸氯盐溶液 直接浸出,同时从底部通入氧化性气体来强化有价金属的浸出和抑制杂质金属的浸出,但 该方法浸出的有价金属难以分离,铁的浸出率过低,且操作步骤多,成本高。CN 104263909 A公开了一种从氧化镍矿中焙烧水浸回收镍钴铁的工艺,该工艺包括:先将原料氧化镍矿和 焦粉破碎球磨,加入氯化剂混合焙烧,焙烧产物浸出后加入中和剂,得到含镍钴铁化合物的 混合物,该方法提取的金属元素难以分离,去除杂质困难,无法得到高纯度单一化合物。 综上所述,镍矿中镍元素的提取还需寻求新的工艺,不仅能够实现有价金属短程 高效地提取,且能够实现提取元素的有效分离而无需后续除杂,简化操作步骤,避免二次污 染。
技术实现要素:
针对现有技术存在的问题,本发明的目的在于提供一种从镍矿中提取镍元素的方 法,本发明采用机械活化后热处理的方法,改变不同金属元素的存在形式,实现镍矿原料中 镍、铁、钴和铜等有价金属的提取与分离,所述方法流程短、效率高,无需后续除杂操作,所 得产物纯度高,降低提取成本,且不会造成二次污染。 为达此目的,本发明采用以下技术方案: 本发明提供了一种从镍矿中提取镍元素的方法,所述方法包括以下步骤: 4 CN 111575502 A 说 明 书 2/9 页 (1)将镍矿原料与添加剂混合后进行机械活化; (2)将步骤(1)得到的混合物料进行热处理; (3)将步骤(2)得到的产物用浸出剂浸出,固液分离,得到富镍溶液和固体渣; (4)将步骤(3)得到的富镍溶液制得镍盐,固体渣分别制得相应盐类。 本发明中,以镍矿为原料,通过与添加剂混合后进行机械活化和热处理,破坏了各 元素离子间的结合力,使各金属元素与添加剂的酸根离子形成可溶性盐,再根据金属盐热 化学性质的差异控制热处理条件,利用不同金属盐的转化温度不同,使部分金属盐转化为 金属氧化物,浸出时得到富镍溶液和固体渣,再分别进行产品化,实现镍矿原料中有价金属 元素的提取并分离,具有流程短、提取率高、产物纯度高的优势。 以下作为本发明优选的技术方案,但不作为本发明提供的技术方案的限制,通过 以下技术方案,可以更好的达到和实现本发明的技术目的和有益效果。 作为本发明优选的技术方案,步骤(1)所述镍矿原料包括硫化镍矿和/或红土镍 矿,优选为硫化镍矿。 优选地,步骤(1)所述添加剂为含硫氧酸根离子的物质。 优选地,所述添加剂包括硫酸、硫酸钠、硫酸氢钠、亚硫酸氢钠、焦硫酸钠、硫酸钾 或硫酸铵中任意一种或至少两种的组合,所述组合典型但非限制性实例有:硫酸和硫酸钠 的组合,硫酸钠和硫酸氢钠的组合,焦硫酸钠和硫酸铵的组合,硫酸钠、硫酸氢钠和亚硫酸 氢钠的组合,硫酸、亚硫酸氢钠和焦硫酸钠的组合等,优选为硫酸。 本发明中,添加剂也可采用废酸,对镍矿原料进行处理,可以有效降低原料成本。 其中,所用硫酸的浓度为1~19mol/L,例如1mol/L、3mol/L、5mol/L、7mol/L、10mol/L、 12mol/L、15mol/L、17mol/L、18.4mol/L或19mol/L等,但并不仅限于所列举的数值,该数值 范围内其他未列举的数值同样适用。 本发明中,所用的添加剂均含硫氧酸根离子,原因在于:在热处理过程中,硫氧酸 根离子可以使镍矿中的金属转化成相应的硫酸盐,在热处理的温度范围内,根据不同金属 盐的稳定性不同,其中部分过渡金属硫酸盐,如硫酸铁等,发生分解转化成氧化物,而硫酸 镍在该温度范围相对稳定,分解较少。 优选地,步骤(1)所述镍矿原料与添加剂的摩尔比为(0.05~5):1,例如0.05:1、 0.1:1、0.2:1、0.5:1、1:1、2:1、3:1、4:1或5:1等,但并不仅限于所列举的数值,该数值范围 内其他未列举的数值同样适用,优选为(2~3):1。 本发明中,镍矿原料与添加剂的摩尔比是影响金属元素提取效果的重要因素,当 两者的摩尔比限定在(0.05~5):1的范围时,可以达到更好的效果。若镍矿原料与添加剂的 摩尔比过大,则会使则镍矿原料不能完全转化为硫酸盐;若镍矿原料与添加剂的摩尔比过 小,则会导致热处理物料泡沫化,影响热处理转型过程的进行。 作为本发明优选的技术方案,步骤(1)所述混合后,先进行干燥处理,再进行机械 活化。 优选地,所述干燥处理的温度为50~300℃,例如50℃、100℃、150℃、200℃、250℃ 或300℃等,但并不仅限于所列举的数值,该数值范围内其他未列举的数值同样适用,优选 为100~150℃。 优选地,所述干燥处理的时间为0.1~24h,例如0.1h、1h、4h、8h、12h、16h、20h或 5 CN 111575502 A 说 明 书 3/9 页 24h等,但并不仅限于所列举的数值,该数值范围内其他未列举的数值同样适用,优选为8~ 15h。 作为本发明优选的技术方案,步骤(1)所述机械活化的方式包括球磨。 优选地,所述球磨速率为50~1000r/min,例如50r/min、100r/min、200r/min、 400r/min、500r/min、600r/min、800r/min或1000r/min等,但并不仅限于所列举的数值,该 数值范围内其他未列举的数值同样适用。 优选地,所述球磨时间为0.1~24h,例如0.1h、1h、4h、8h、12h、16h、20h或24h等,但 并不仅限于所列举的数值,该数值范围内其他未列举的数值同样适用。 优选地,步骤(1)所述机械活化后得到的混合物料的粒径为0.01~10μm,例如0.01 μm、0.05μm、0.1μm、0.5μm、0.8μm、1μm、3μm、5μm、8μm或10μm等,但并不仅限于所列举的数值, 该数值范围内其他未列举的数值同样适用。 本发明中,通过镍矿原料与添加剂的共同球磨,高能球磨作用有助于镍矿颗粒与 添加剂之间的活化作用,之后进行热处理时有助于多金属复合物或混合物转化为各自的金 属盐,降低热处理的温度,降低矿石原料的处理难度。 作为本发明优选的技术方案,步骤(2)所述热处理在真空或有气氛条件下进行。 优选地,所述气氛包括空气、氧气、氮气、氖气或氩气中任意一种或至少两种的组 合,所述组合典型但非限制性实例有:空气和氧气的组合,氧气和氮气的组合,氖气、氮气和 氩气的组合,空气、氮气和氩气的组合等,优选为空气。 优选地,步骤(2)所述热处理的温度为300~600℃,例如300℃、350℃、400℃、450 ℃、500℃、550℃或600℃等,但并不仅限于所列举的数值,该数值范围内其他未列举的数值 同样适用。 本发明中,热处理温度是影响硫化镍矿原料提取分离效果的重要因素之一,当热 处理温度过低时,硫化镍矿硫酸盐后的硫酸铁不易转化成氧化物,使得铁与镍共同浸出,无 法实现有价金属的短程高效提取;而当热处理温度过高时,则会使硫酸镍发生分解,既造成 镍的损失,也会造成不必要的能耗损失。 优选地,所述热处理的时间为0.1~12h,例如0.1h、1h、2h、4h、6h、8h、10h或12h等, 但并不仅限于所列举的数值,该数值范围内其他未列举的数值同样适用,优选为1~6h。 优选地,步骤(2)所述热处理的升温速率为1~20℃/min,例如1℃/min、2℃/min、5 ℃/min、8℃/min、10℃/min、12℃/min、15℃/min、18℃/min或20℃/min等,但并不仅限于所 列举的数值,该数值范围内其他未列举的数值同样适用。 作为本发明优选的技术方案,步骤(3)所述浸出剂包括中性浸出剂或酸性浸出剂, 优选为中性浸出剂,进一步优选为水。 优选地,所述酸性浸出剂的pH值为6.0~7.0,例如6.0、6.2、6.4、6.5、6.6、6.8或 6.9等,但并不仅限于所列举的数值,该数值范围内其他未列举的数值同样适用,其中,酸性 浸出剂的pH值不取到7.0。 优选地,步骤(3)所述产物和浸出剂的固液比为0.1~1000g·L-1,例如0.1g·L-1、 1g·L-1、10g·L-1、20g·L-1、50g·L-1、100g·L-1、200g·L-1、400g·L-1、600g·L-1、800g·L -1或1000g·L-1等,但并不仅限于所列举的数值,该数值范围内其他未列举的数值同样适 用,优选为100~800g·L-1。 6 CN 111575502 A 说 明 书 4/9 页 优选地,步骤(3)所述浸出的时间为1~600min,例如1min、10min、50min、100min、 150min、200min、300min、400min、500min或600min等,但并不仅限于所列举的数值,该数值 范围内其他未列举的数值同样适用,优选为10~200min。 优选地,步骤(3)所述浸出的温度为20~100℃,例如20℃、30℃、40℃、50℃、60℃、 70℃、80℃、90℃或100℃等,但并不仅限于所列举的数值,该数值范围内其他未列举的数值 同样适用,优选为20~80℃。 作为本发明优选的技术方案,步骤(3)所述固液分离为过滤。 优选地,步骤(3)所述富镍溶液的浓度为1~30g·L-1,例如1g·L-1、5g·L-1、10g· L-1、15g·L-1、20g·L-1、25g·L-1或30g·L-1等,但并不仅限于所列举的数值,该数值范围内 其他未列举的数值同样适用。 作为本发明优选的技术方案,步骤(4)所述富镍溶液通过蒸发浓缩法制备镍盐。 优选地,所述蒸发浓缩在蒸发结晶器中进行。 优选地,所述镍盐的纯度不低于98wt%,例如98wt%、98 .4wt%、98 .8wt%、 99wt%、99.2wt%、99.4wt%、99.6wt%或99.8wt%等,但并不仅限于所列举的数值,该数值 范围内其他未列举的数值同样适用。 作为本发明优选的技术方案,步骤(4)所述固体渣包括铁氧化物、钴氧化物和铜氧 化物,或铁氧化物和镁氧化物。 优选地,步骤(4)所述固体渣依次通过酸浸、萃取和反萃分别得到铁盐、钴盐和铜 盐,或铁盐和镁盐。 本发明中,根据镍矿原料中所含金属的种类吗,所得固体渣为金属氧化物的混合 物,将其进行酸浸溶剂,再分别萃取和反萃,可以将几种金属盐进行分离。 优选地,所述酸浸所用的酸为硫酸。 优选地,所述萃取和反萃均在分液漏斗内进行。 作为本发明优选的技术方案,所述方法包括以下步骤: (1)将摩尔比为(0.05~5):1的镍矿原料与添加剂混合后,先进行干燥处理,干燥 处理温度为50~300℃,干燥处理时间为0.1~24h,再进行球磨处理,球磨速率为50~ 1000r/min,球磨时间为0.1~24h,得到粒径为0.01~10μm的混合物料; (2)将步骤(1)得到的混合物料进行热处理,热处理温度为300~600℃,时间为0.1 ~12h,升温速率为1~20℃/min; (3)将步骤(2)得到的产物用中性浸出剂浸出,所述产物和浸出剂的固液比为0.1 ~1000g·L-1,浸出的时间为1~600min,浸出的温度为20~100℃,过滤分离后得到富镍溶 液和滤渣; (4)将步骤(3)得到的富镍溶液通过蒸发浓缩法制得镍盐,将滤渣依次通过硫酸酸 浸、萃取和反萃分别得到铁盐、钴盐和铜盐,或铁盐和镁盐。 与现有技术相比,本发明具有以下有益效果: (1)本发明采用机械活化后热处理的方法,实现镍矿原料中有价金属元素的短程 高效选择性提取及分离,镍的提取率达92%以上,其他有价金属的提取率达90%左右; (2)本发明通过机械活化极大地降低热处理温度,解决了传统火法处理技术中回 转窑结圈的问题,所述方法也解决了传统湿法处理方法浸出液中杂质离子含量高、除杂方 7 CN 111575502 A 说 明 书 5/9 页 式困难且复杂的问题; (3)本发明所述方法流程短,不引入其他杂质离子,可以避免二次污染和废液处 理,节约回收成本,易于实现工业化应用。 附图说明 图1是本发明实施例1提供的从镍矿中提取镍元素方法的工艺流程图。