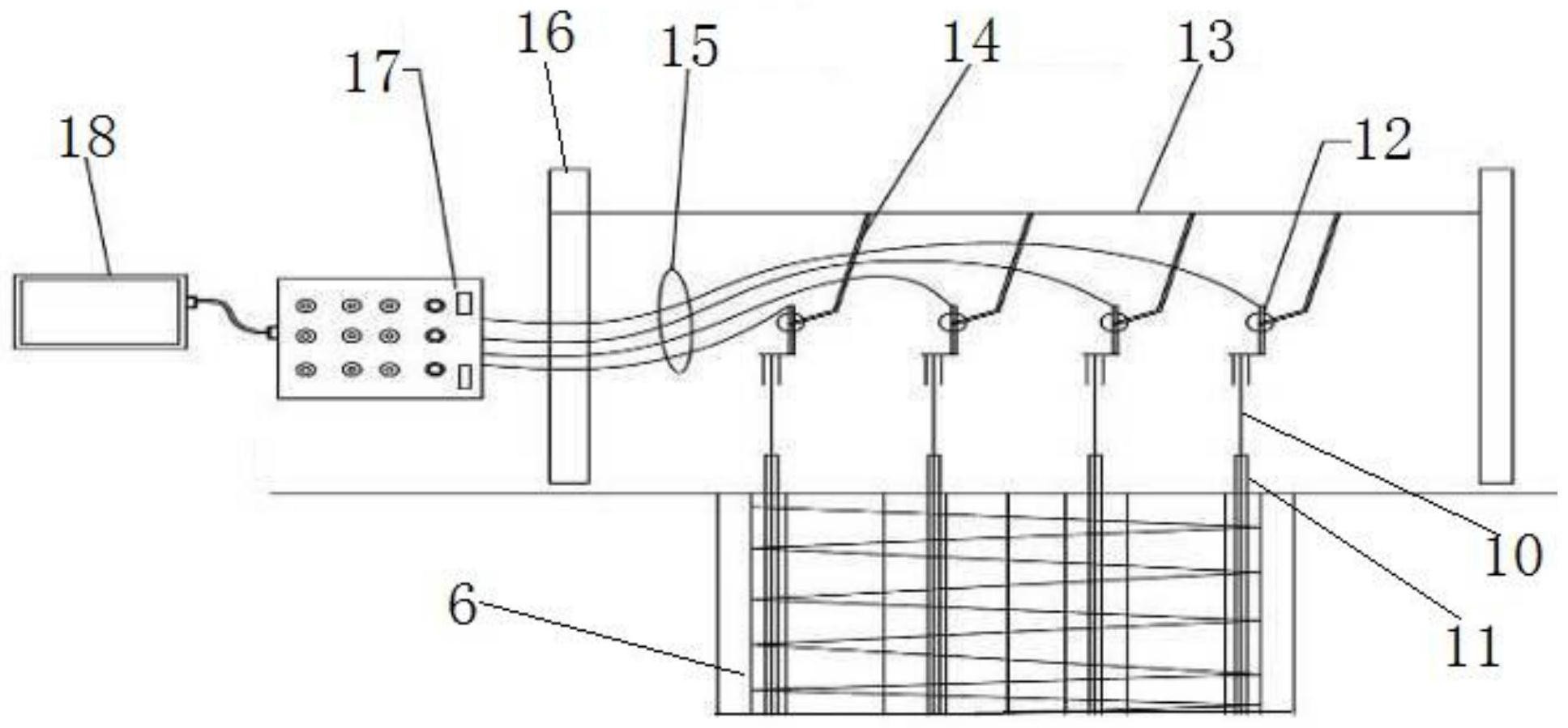
技术摘要:
本发明公开一种建筑基桩自平衡静载试验操作方法,包括准备阶段、安装阶段和检测阶段;所述准备阶段完成混凝土、钢筋笼和荷载箱的生产和运输工作,并选取合适的荷载箱、预先计算自平衡平衡点和所述荷载箱埋设位置;所述安装阶段完成所述荷载箱的安装工作,包括所述荷载 全部
背景技术:
传统的静载试验,通过在桩顶施加一定的负荷进行实施,通常有堆载和锚桩两种 方法。堆载法采用油压千斤顶在桩顶施加荷载,而千斤顶的反力通过反力架上的堆重与之 平衡,一般堆重可选择沙袋、混凝土配重、钢锭等。锚桩法也是采用油压千斤顶在桩顶施加 荷载,千斤顶的反力通过反力架传给锚桩。但这两种方法也存在一些问题,例如堆载法需解 决几百吨甚至上千吨的荷载来源、运输、堆放问题。锚桩法需要设置多根锚桩和反力大梁来 平衡反力,安装中荷载对中不易控制,不仅会增加相关成本和时间,而且受施工现场场地的 限制。所以对有些特殊复杂的施工场地的进度产生了严重的制约。 也有采用自平衡静载试验的方式测试,但是在荷载箱选取、设置、焊接,以及与钢 筋笼对接下放等的操作步骤不系统、规范,影响试验的准确性;而且在操作过程中对管线的 设置和保护不够好,具有安全隐患,影响试验后浇注的操作,不能够确保试桩都能够转变为 合格的工程桩。
技术实现要素:
本发明的目的是针对现有技术存在的问题,提供一种建筑基桩自平衡静载试验操 作方法。 为实现上述目的,本发明采用的技术方案是: 一种建筑基桩自平衡静载试验操作方法,其特征在于,所述操作方法包括准备阶 段、安装阶段和检测阶段; 其中,所述准备阶段完成混凝土、钢筋笼和荷载箱的生产和运输工作,并根据施工 现场选取相适配类型的荷载箱、预先计算自平衡平衡点和所述荷载箱埋设位置; 所述安装阶段完成所述荷载箱的安装工作,包括所述荷载箱预浇混凝土、所述荷 载箱与所述钢筋笼焊接、下放已焊接的钢筋笼及灌注桩身混凝土、桩头管线保护的步骤; 在所述荷载箱与所述钢筋笼焊接的步骤中,将浇注好的荷载箱用吊车侧吊,完成 以下焊接工作:荷载箱箍筋焊接、所述荷载箱与所述钢筋笼对接、布置位移管线及油管、所 述钢筋笼盘筋加密; 在所述下放已焊接的钢筋笼及灌注桩身混凝土的步骤中,当桩顶标高低于地面 时,桩顶到地面放置简易钢筋笼,用于引导保护所述位移管线和所述油管; 所述检测阶段至少包括搭设基准梁和基准桩、搭设帐篷、现场检测、荷载箱断开面 注浆的步骤。 本操作方法,思路清晰,可操作性强,通过各个阶段的布置,明确了每个阶段和步 骤需要完成的任务,能够节省整个试验的周期的时间,能够做到施工标准化,减少人为误 4 CN 111576499 A 说 明 书 2/9 页 差,提高试验准确性; 本操作方法使用到的装置较简单,占用场地空间小,不需要运入数百吨或数千吨 物料,不需构筑笨重的反力架,可多根试桩同时测试,试验准备工作省时、省力、安全; 试验后试桩仍可作为工程桩使用,能够利用预埋的管路对荷载箱进行压力灌浆, 确保试桩能够达到工程桩的性能。 本操作方法适用于软土、黏性土、粉土、砂土、碎石土、岩层以及特殊性岩土中的钻 孔灌注桩、人工挖孔桩、管桩的竖向抗压静载试验和竖向抗拔静载试验。 工作原理是将荷载箱放置在试桩的平衡点位置或底部,连接施压油管及位移测量 装置于桩顶部,待砼养护到标准龄期或达到设计强度后,通过顶部加压泵给荷载箱施压向 上顶桩身的同时,向下压桩底,使桩的摩阻力和端阻力互为反力,分别得到荷载-位移曲线, 叠加后得到桩顶的承载力和位移的Q-s曲线;自平衡法是一种基于在桩基内部寻求加载反 力的静荷载试验方法,通过测得上下桩段两条Q-S曲线及相应的S-lgt曲线,采用相应的测 试数据等效转换方法和承载力确定方法,即可确定基桩的极限承载力、桩侧、桩端阻力分担 情况等。 载荷箱的选取:整体式(圆形全液压截面)荷载箱,用于端承桩的试验,满足小桩径 试验的要求,一般使用于1.2米或1.2米以下的摩擦桩;组合式荷载箱,满足大桩径及大吨位 试验的要求,一般使用于1.2米以上的摩擦桩,能够根据加载吨位要求,灵活组合。 进一步的,收集施工场地地质勘探资料,根据岩土类型结合现场工况计算自平衡 平衡点;当试桩的极限端阻小于极限侧摩阻力时,将荷载箱置于平衡点处;当试桩的极限端 阻力大于极限侧摩阻力时,将荷载箱置于桩端;当试桩为抗拔桩时,荷载箱置于桩端;荷载 箱埋设位置满足上桩段桩侧阻力与下段桩侧阻力及端阻力的平衡系数在1.2-1.5之间;桩 荷载箱位置离桩底不小于0.5m。 在所述准备阶段将混凝土、钢筋笼和荷载箱提前制作好并运输至试验场地,同时 根据地勘报告计算出平衡点和确定载荷箱安装位置,能够有效节省安装阶段和检测阶段的 时间,缩短工期。 由于载荷箱是一次性埋入使用的设备,其100%的可靠性是测试成功的前提,荷载 箱在出厂之前,均应经过率定试压(率定荷载是要求最大加载力的1.3倍)和标定,确保产生 足够的精确的加载力,避免试验失败。 进一步的,在所述荷载箱与所述钢筋笼焊接的步骤中,所述荷载箱箍筋焊接为:在 荷载箱的底侧焊接一个箍筋,箍筋外径应和钢筋笼内径一致; 所述荷载箱与所述钢筋笼对接的方法为:首先荷载箱分别与钢筋笼、箍筋焊接,焊 接时钢筋笼与荷载箱必须保证垂直,偏心度控制在5度之内;然后焊接上下喇叭状导向筋, 所述导向筋直径应不小于Φ16mm,导向筋与荷载箱夹角应大于60°;所述导向筋的一端焊接 在所述荷载箱上面板中孔内壁或导管孔边缘上,另一端与相对应的钢筋笼的主筋焊接;所 述导向筋的数量不小于钢筋笼的主筋数量,间距小于混凝土导管的口径;采用这样的焊接 方式能够保证足够的连接强度,同时减少焊接工作量,而且能够引导混凝土导管通过荷载 箱中心孔进行二次清孔及浇注; 所述钢筋笼盘筋加密的方法为:在所述荷载箱上下各2米范围内,对所述钢筋笼横 向箍筋进行加密处理,使其间距小于10cm。能够明显提高所述荷载箱上下面的抗压强度。 5 CN 111576499 A 说 明 书 3/9 页 进一步的,所述荷载箱与所述钢筋笼对接的方法中,对于环形的荷载箱:制作L型 筋,一端与上钢筋笼主筋焊接,另一端与荷载箱上盖板焊接,L型筋的规格与钢筋笼主筋的 规格一致,L型筋与荷载箱焊接部分长度比荷载箱的环形宽度少5cm,与钢筋笼主筋连接部 分,保证与主筋重合焊接20cm;对于组合式的荷载箱:荷载箱分别与上下面的钢筋笼的主 筋、上下面的箍筋焊接;对于整体式的荷载箱:钢筋笼的主筋与荷载箱上表面加焊的箍筋焊 接。L型筋的布置能够进一步提高连接强度。 进一步的,在所述布置位移管线及油管的方法中,所述位移管线包含位移杆和位 移护管,所述位移杆的外径≥16mm、壁厚≥1.5mm,所述位移护管外径≥32mm、壁厚≥2.0mm, 根据孔深设计长度,顺着钢筋笼连接至地面,采用丝扣连接,拧紧时缠生料带,连接完成后 耐压强度≥2MPa。呈90度布置,分别用于测量桩体上下位移。尺寸较大的位移护管一方面便 于位移杆及线路的穿插安放,另一方面能够作为注浆管使用,在试验完成后对裂缝处注浆。 进一步的,在所述布置位移管线及油管的方法中,预先将所述油管盘好在所述荷 载箱处,待下所述钢筋笼时连续展开,沿导向筋绑扎至地面;所述油管为高压软管,连接所 述油管在所述荷载箱与所述钢筋笼焊接完毕至少半小时后进行,并设置保护引导钢筋,把 所述油管藏在所述保护引导钢筋下方引至所述钢筋笼。该种布置方式能够防止焊接时的高 温烫坏油管接头内的密封圈,减少油管受损;也能够为防止灌注混凝土损坏油管。 进一步的,在下放已焊接的钢筋笼及灌注桩身混凝土步骤中,使用两个吊钩起吊, 主勾连接所述钢筋笼的上部,副勾连接所述钢筋笼的中下部,所述主勾和所述副勾同时升 起水平吊起所述钢筋笼;收所述主勾使所述钢筋笼的上部逐渐吊起,同时放所述副勾使所 述钢筋笼的下部逐渐下降,直至所述钢筋笼为竖直状态,撤掉所述副勾,通过所述主勾将竖 直的所述钢筋笼下放桩孔内,在下放的过程中对位移管线和油管进行绑扎。 采用该种起吊方式能够快速的将水平放置的荷载箱及钢筋笼竖立起来,省时省 力,并能够防止荷载箱受弯。 进一步的,在钢筋笼下放完毕到现场开始检测之间的休止期内进行所述桩头管线 保护,并在桩头设置警示标记,保护所述位移管线及油管。防止水泥浆漏入,保证管线不受 破坏,防止人员误入桩孔,安全性好。 检测阶段,确保数据采集系统及油压泵的正常使用,现场需配备一只电压稳定不 间断三相四线制配电箱。配电箱带漏电保护,有380V、220V两种电源,容量不小于10千瓦。 进一步的,在所述安装阶段中,对于试验中涉及到检测的各类管线需进行安装前 保护和安装后保护;所述安装前保护的方案为,以试桩为中心,采用“U”形路线优先对试桩 四周的工程桩进行施工,最后完成“U”形路线开口处的工程桩施工;按上述顺序施工,能够 最大限度保证工程桩施工时,试桩检测设施不因周边工程桩施工破坏,且不必再铺设施工 场地(留有试桩施工通道); 所述安装后保护方案为:试桩采用全钢筋笼,空孔部分钢筋笼的主筋及加紧箍配 筋与有效桩长上端钢筋笼配筋一致;螺旋箍筋采用Φ8×200mm。 工程桩空孔较深(平均约18m),采用全笼可将自平衡检测用的位移杆、位移护管及 其他检测附属管/线绑扎在钢筋笼主筋上,避免因空孔过深、检测用管/线无附着发生弯折; 因工程桩孔壁在无保护的情况下容易发生垮塌,采用全笼对孔壁有一定的支护作用,避免 因孔壁垮塌对检测用管/线造成破坏。该保护方案综合考虑成本、工期及可操作性等因素, 6 CN 111576499 A 说 明 书 4/9 页 以确保检测的各类管线在试桩成型后不被破坏。 进一步的,所述荷载箱断开面注浆的步骤为:在试验完成后,取出位移杆及检测用 线,通过位移护管,用压浆泵将不低于桩身强度的水泥浆注入所述荷载箱处的混凝土被拉 开的地方;逐根管子或多根管子交替进行压浆,通过压浆压力与压浆量双重要求进行控制。 试验时,荷载箱处的混凝土被拉开(缝隙宽度等于卸载后向上向下残余位移之 和),但桩身其他部位并未破坏,上下两段桩仍被荷载箱连在一起,试验后,充分利用遗留的 位移护管进行注浆,注浆后受检桩仍可作为工程桩使用,节约了成本和时间。 与现有技术相比,本发明的有益效果是:1、本操作方法,思路清晰,可操作性强,通 过各个阶段的布置,明确了每个阶段和步骤需要完成的任务,能够节省整个试验的周期的 时间,能够做到施工标准化,减少人为误差,提高试验准确性;2、钢筋笼与荷载箱的焊接结 构合理稳固,焊接方式简单有效,确保了荷载箱的承载能力;3、钢筋笼的下放起吊方式能够 快速的将水平放置的荷载箱及钢筋笼竖立起来,省时省力,并能够防止荷载箱受弯;4、在整 个操作过程中,对于检测用到的管线保护措施较好,避免了管线损坏造成的试验失败或工 程延期;而且能够合理利用这些管路进行最后的注浆工作。 附图说明 图1为本发明一种建筑基桩自平衡静载试验操作方法中用到的环形荷载箱结构示 意图; 图2为本发明一种建筑基桩自平衡静载试验操作方法中用到的环形荷载箱与钢筋 笼对接示意图; 图3为本发明一种建筑基桩自平衡静载试验操作方法中地面检测设备布置示意 图; 图4为本发明一种建筑基桩自平衡静载试验操作方法中用到的组合式荷载箱结构 示意图; 图5为本发明一种建筑基桩自平衡静载试验操作方法中试桩与工程桩位置示意 图; 图6为本发明一种建筑基桩自平衡静载试验操作方法中荷载箱断面浇注示意图; 图中:1、环形荷载箱;2、压力单元;3、导流体;4、油管;5、箍筋;6、钢筋笼;7、主筋; 8、导向筋;9、L型筋;10、位移杆;11、位移护管;12、位移传感器;13、基准梁;14、支架;15、数 据线;16、基准桩;17、数据记录器;18、显示器;19、试桩;20、工程桩;21、泵车。