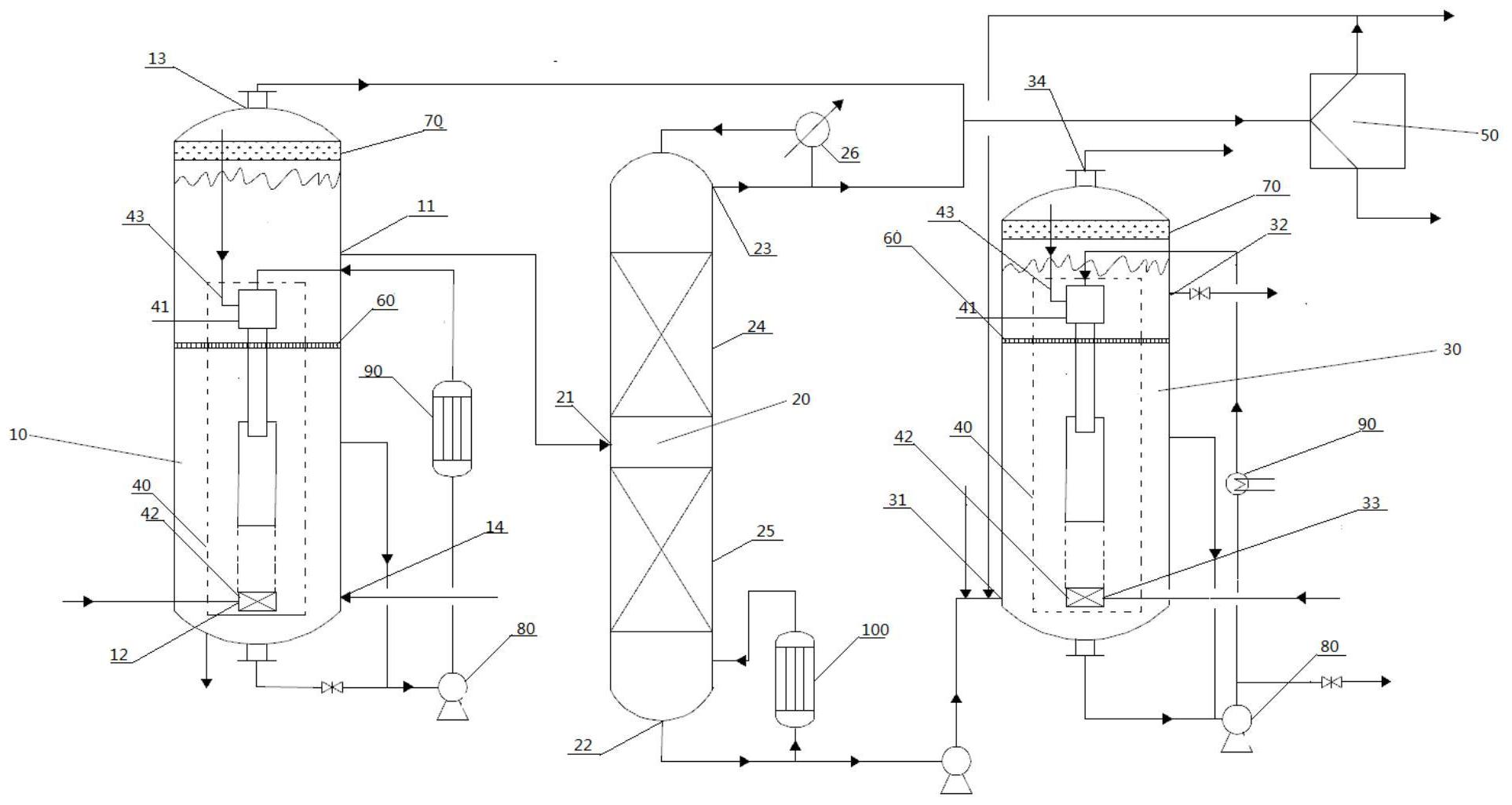
技术摘要:
本发明提供了一种对二甲苯制备对苯二甲酸的内置微界面氧化系统。该氧化系统包括:依次连接的第一反应器、精馏塔、第二反应器,所述第一反应器的侧壁设置有第一出口,所述第二反应器的侧壁设置有第一进口,所述精馏塔的侧壁设置有物料进口,所述精馏塔底部设置有物料出 全部
背景技术:
对苯二甲酸是一种重要的化工原料,通常由对二甲苯与含氧气体通过氧化反应制 得,对二甲苯氧化的反应器通常采用鼓泡式氧化反应器,气泡直接通常大于3mm,乃至厘米 级,其传质界相面积有限,气体利用率低以致反应效率偏低,为强化气液传质,鼓泡反应器 一般在塔内增设塔板、静态混合器等内件以加强混合,然而混合后的气泡直径通常为3- 30mm,所提供的相界面积和传质系数(液侧、气侧)有限,故反应性能较难获得突破性的提 高,进而影响了反应的整体效率,因此工程上不得不采用高温高压操作,通过增加气相和/ 或液相的溶解度以提高传质速率,从而强化反应过程,然而对二甲苯氧化的过程非常复杂, 主要包括4个步骤,即对二甲苯(PX)→对甲基苯甲醛(TALD)→对甲基苯甲酸(p-TA)→对羧 基苯甲醛(4-CBA)→对苯二甲酸(TA),前2个步骤要以醋酸为溶剂,不宜采用高温高压,现有 技术采用混合的反应工艺,能耗高,醋酸消耗量大,反应效率低下。 有鉴于此,特提出本发明。
技术实现要素:
本发明的第一目的在于提供一种对二甲苯制备对苯二甲酸的内置微界面氧化系 统,该内置微界面氧化系统在反应器中设置微界面机组,通过设置了微界面机组后,可以将 空气气泡打碎成微米级别的气泡,从而增加气相和液相之间的相界面积,使得传质空间充 分满足,增加了空气在液相中的停留时间,从而降低了空气的耗量,降低了能耗,同时降低 了操作温度以及压力,提高了反应的安全性,而且采用了分段式工艺,解决了醋酸溶剂不能 承受高温氧化条件的矛盾,提高了反应效率。 本发明的第二目的在于提供一种采用上述内置微界面氧化系统的对二甲苯制备 对苯二甲酸的方法,该方法有利于减少能耗,达到比现有工艺更佳的反应效果。 为了实现本发明的上述目的,特采用以下技术方案: 本发明提供了一种对二甲苯制备对苯二甲酸的内置微界面氧化系统,包括:依次 连接的第一反应器、精馏塔、第二反应器,所述第一反应器的侧壁设置有第一出口,所述第 二反应器的侧壁设置有第一进口,所述精馏塔的侧壁设置有物料进口,所述精馏塔底部设 置有物料出口; 所述第一出口与所述精馏塔的物料进口连接,所述第一进口与所述精馏塔的物料 出口连接; 所述第一反应器与第二反应器内部均设置有微界面机组,所述微界面机组用于分 散破碎空气成气泡。 现有技术中,对二甲苯制备对苯二甲酸的反应步骤如下: 3 CN 111569454 A 说 明 书 2/7 页 即对二甲苯(PX)→对甲基苯甲醛(TALD)→对甲基苯甲酸(p-TA)→对羧基苯甲醛 (4-CBA)→对苯二甲酸(TA) 反应工艺一般采用鼓泡式氧化反应器,在生成过程中,相界面积对体积传质系数 的影响程度较大,而鼓泡式氧化反应器的的普遍传质效率较低,从而在反应效能上很难有 突破性的进展,影响了反应效率和原料转化率。本发明的内置微界面氧化系统通过在反应 器内部设置微界面机组后,空气和原料通入微界面机组后,内部实现强化传质、分散破碎, 破碎形成了微气泡,使得传质空间充分满足,从而降低了空气的耗量,即使温度和压力不需 要太高的条件下,也可以保证反应本身的高反应效率。而且本发明采用分段式工艺,解决了 醋酸溶剂不能承受高温氧化条件的矛盾,提高了反应效率。 进一步的,所述微界面机组中所包含的微界面发生器设置方式不限、设置位置不 限,数量不限。更优选地所述微界面机组包括上下布置的第一微界面发生器和第二微界面 发生器,所述第一微界面发生器连接有导气管,所述导气管的顶端伸出所述第一反应器的 液面用于回收空气,反应过程中大量未反应完的空气和部分醋酸和水蒸气积聚在反应器的 上方,为了充分回收,通过导气管再次进入底部多次循环反应,从而提高传质效率。所述第 一反应器的侧壁还设置有第二进口,所述第二进口末端延伸至所述第二微界面发生器内, 所述第二反应器内的微界面机组结构与所述第一反应器相同。 进一步的,所述第一微界面发生器为液动式微界面发生器,通过液相物料(包括反 应得到的对甲基苯甲醛、醋酸、水、少量未反应完全的对二甲苯、中间产物等)作为动力循 环,将反应器上方的大量未反应完的空气和部分醋酸和水蒸气通过导气管卷吸进来,从而 增加气液两相之间的传质效果,以充分回收液面上的空气。 进一步的,所述第一反应器的外侧设置有给所述第一微界面发生器提供动力的循 环管道,循环管道上流经包括反应得到的对甲基苯甲醛、醋酸、水、少量未反应完全的对二 甲苯、中间产物等液相物料,具体地循环管道的一端与所述第一微界面发生器的顶部连通, 另一端与所述第一反应器的侧壁连通。 此外,更优选地,第一反应器的底部还设置有管路,管路中的物料主要有对甲基苯 甲醛、醋酸、水等,该管路与循环管道汇集后,从第一位微界面发生器的顶部通入,给第一微 界面发生器提供卷吸动力,形成循环物流,从而实现这部分物料的回收利用,循环管道上还 设置有提供动力的循环泵,所述循环泵泵壳内壁设有金属传感探头,金属传感探头一侧的 泵壳外壁设有温度传感器,金属传感探头和温度传感器通过导线连接,可以随时监控循环 泵中通液相物料的温度。所述循环管道上还设置有换热器,用来控制循环物料的温度,从而 使得第一反应器内部温度保持稳定,优选板式换热器,相比其他换热器,板式换热器具有换 热效率高,热损失小,高效节能,容易清洗拆装方便等特点。 进一步的,所述第二微界面发生器为气动式微界面发生器,通过将空气通入微界 面发生器后与反应器内的反应物料(包括对二甲苯,醋酸和催化剂等混合物)接触后破碎形 成微气泡的方式,提高传质效果。 4 CN 111569454 A 说 明 书 3/7 页 第一微界面发生器与第二微界面发生器的出口相对,这样第一微界面发生器产生 的气泡向下运动,第二微界面发生器产生的气泡向上运动,两者碰撞产生更小的气泡,进一 步增大了接触面积,加快反应效率。 进一步的,所述第一微界面发生器与所述第二微界面发生器之间设置有用于相互 固定的连接杆。连接杆起到了良好的加固作用,以防反应器内部液体的流动对微界面发生 器本身造成冲击。连接杆的具体材质、形状和数量不限,只要能起到固定效果,优选为长杆 形状。 本领域所属技术人员可以理解的是,本发明所采用的微界面发生器在本发明人在 先专利中体现,如公开号106215730A的专利,微界面发生器其核心在于气泡破碎,气泡破碎 器的原理是高速射流所携带的气体相互撞击进行能量传递,使气泡破碎,关于微界面发生 器的结构在上述专利中公开其中一实施例,此不再赘述。关于微界面发生器与第一、第二反 应器、以及其他设备的连接,包括连接结构、连接位置,根据微界面发生器的结构而定,此不 作限定。关于微界面发生器的反应机理及控制方法,在本发明人在先专利CN107563051B中 已经公开,此不再赘述。 第二反应器与第一反应器内部结构是一致的。只不过区别在于第一反应器与第二 反应器的进料口、出料口不同。 第一反应器的混合原料进口设置在侧壁靠下位置,第二进口通入空气,混合原料 进口通入反应混合原料(包括对二甲苯,醋酸和催化剂等混合物),第一反应器的第一出口 设置在侧壁中上部,通过溢流管道,产出中间产物(主要成分为对甲基苯甲酸,还包括醋酸、 水、少量未反应完全的对二甲苯、中间产物等)进入精馏塔的中部,在精馏塔中进行纯化分 离。 第二反应器的第一进口位置设置与第一反应器第二进口位置相同,精馏塔塔底产 出的物料(对甲基苯甲酸和水)、补充的催化剂(氢溴酸)以及从酸水分离器中分离的水一起 从第一进口进入第二反应器中继续反应,空气从第二反应器的空气进口进入,充分反应后, 生成的产物对苯二甲酸溶液从第二反应器的侧壁上部的第三出口采出。 更进一步的,所述第一微界面发生器采用防浪格栅固定在所述第一反应器和第二 反应器的内部,防浪格栅主要起隔离支撑和滤除泡沫的作用,一方面固定第一微界面反应 器于反应器的内部,另一方面除去夹带的雾沫,以保证传质效率,降低有价值的物料损失, 所述防浪格栅可采用国产进口优质材质,如:Q235、304、304L、321、316L、F46、NS-80、镍丝、 钛丝及合金等材质。 进一步的,所述第一反应器和第二反应器内部上方均设置有除滤网,反应器的上 方积聚了大量未反应的空气和部分气体物质,这些气体通过导气管进入第一微界面发生器 内部,设置除滤网可以防止气体中的杂质进入第一微界面发生器内部。 进一步的,所述第一反应器顶部还设置有第二出口,所述第二出口连接有酸水分 离器。精馏塔塔顶采出的部分醋酸和水,与第一反应器顶部采出的尾气共同汇合后进入到 酸水分离器中,分离出的醋酸重新回到第一反应器内部循环使用,分离出的水一部分排出, 一部分进入第二反应器内部循环使用。 进一步的,本发明所采用的精馏塔,主要有轻组分分离段和重组分分离段组成,所 述轻组分分离段和重组分分离段之间的塔节上设置有物料进口,用于将第一反应器中的氧 5 CN 111569454 A 说 明 书 4/7 页 化产物通入所述精馏塔中,从精馏塔的物料进口进来的物料主要有对甲基苯甲酸,还包括 醋酸、水、少量未反应完全的对二甲苯、中间产物等,对甲基苯甲酸和少量水经过位于物料 进口下方的重组分分离段被精馏分离到塔底,醋酸、和大部分水经过轻组分分离段后朝着 塔顶方向被精馏分离,从馏出物出口引出的醋酸和水蒸汽经过冷凝,一部分作为回流液从 塔顶返回精馏塔,其余部分通过管道与第一反应器中的尾气混合后进入酸水分离器,塔底 产物对甲基苯甲酸和少量水等液相物料采出后,一部分经过塔釜再沸器后作为回流液返回 重组分分离段继续精馏,另一部分通入第一进口进入第二反应器内后继续进行反应。 精馏塔中的轻组分分离段和重组分分离段可由若干塔板、填料任意组合而成,优 选地靠近塔釜位置采用塔板的结构,靠近塔顶位置采用填料的结构,因为塔板本身压降比 较大,填料压降比较小。 进一步的,所述精馏塔的塔顶设置有塔顶冷凝器,塔釜设置有塔釜再沸器,所述塔 釜再沸器的类型为降膜式再沸器,这种类型的再沸器与普通的再沸器类型相比,在管壁上 成膜,换热效率很高,滞留时间短,不容易结焦,避免了塔釜的物质发生聚合有副产物生成。 除此之外,本发明还提供了一种采用上述内置微界面氧化系统的对二甲苯制备对 苯二甲酸的方法,其特征在于,包括如下步骤: 空气通过第一反应器内置的微界面机组进行分散破碎; 反应物料进入第一反应器中与分散破碎后的空气进行反应; 通过反应得到的液相物料进入到精馏塔中进行分离; 精馏塔分离出的物料进入第二反应器中与分散破碎后的空气进行反应得到对苯 二甲酸。 进一步的,所述第一反应器内温度为120-155℃,压强为0.20-0.66MPa。 进一步的,所述第二反应器内温度为135-180℃,压强为0.56-0.82MPa。 与现有技术相比,本发明的有益效果在于: (1)本发明通过设置微界面机组,增大接触面积,提高了反应相之间的传质效率, 进而达到在较低的压强范围内强化反应的目的,提高了反应效率,极大的减少了反应过程 中的能耗和生成成本,降低了投资强度、延长了设备操作周期、确保了反应过程中的本质安 全性差,有效地保证了反应成品的工业化大规模生产。 (2)本发明通过分段式工艺,针对不同反应给予不同的反应条件,解决了对二甲苯 制备对苯二甲酸过程中,醋酸作为溶剂不能承受高温氧化条件的矛盾,并且能及时取出产 物,这种分段氧化有利于减少投资和消耗,达到比现有工艺更佳的反应效果。 附图说明 通过阅读下文优选实施方式的详细描述,各种其他的优点和益处对于本领域普通 技术人员将变得清楚明了。附图仅用于示出优选实施方式的目的,而并不认为是对本发明 的限制。而且在整个附图中,用相同的参考符号表示相同的部件。在附图中: 图1为本发明实施例提供的对二甲苯制备对苯二甲酸的内置微界面氧化系统的结 构示意图。 附图说明: 10-第一反应器; 11-第一出口; 6 CN 111569454 A 说 明 书 5/7 页 12-第二进口; 13-第二出口; 14-混合原料进口; 20-精馏塔; 21-物料进口; 22-物料出口; 23-馏出物出口; 24-轻组分分离段; 25-重组分分离段; 26-冷凝器; 30-第二反应器; 31-第一进口; 32-第三出口; 33-空气进口; 34-废气出口; 40-微界面机组; 41-第一微界面发生器; 42-第二微界面反应器; 43-导气管; 50-酸水分离器; 60-防浪格栅; 70-除滤网; 80-循环泵; 90-换热器; 100-塔釜再沸器。