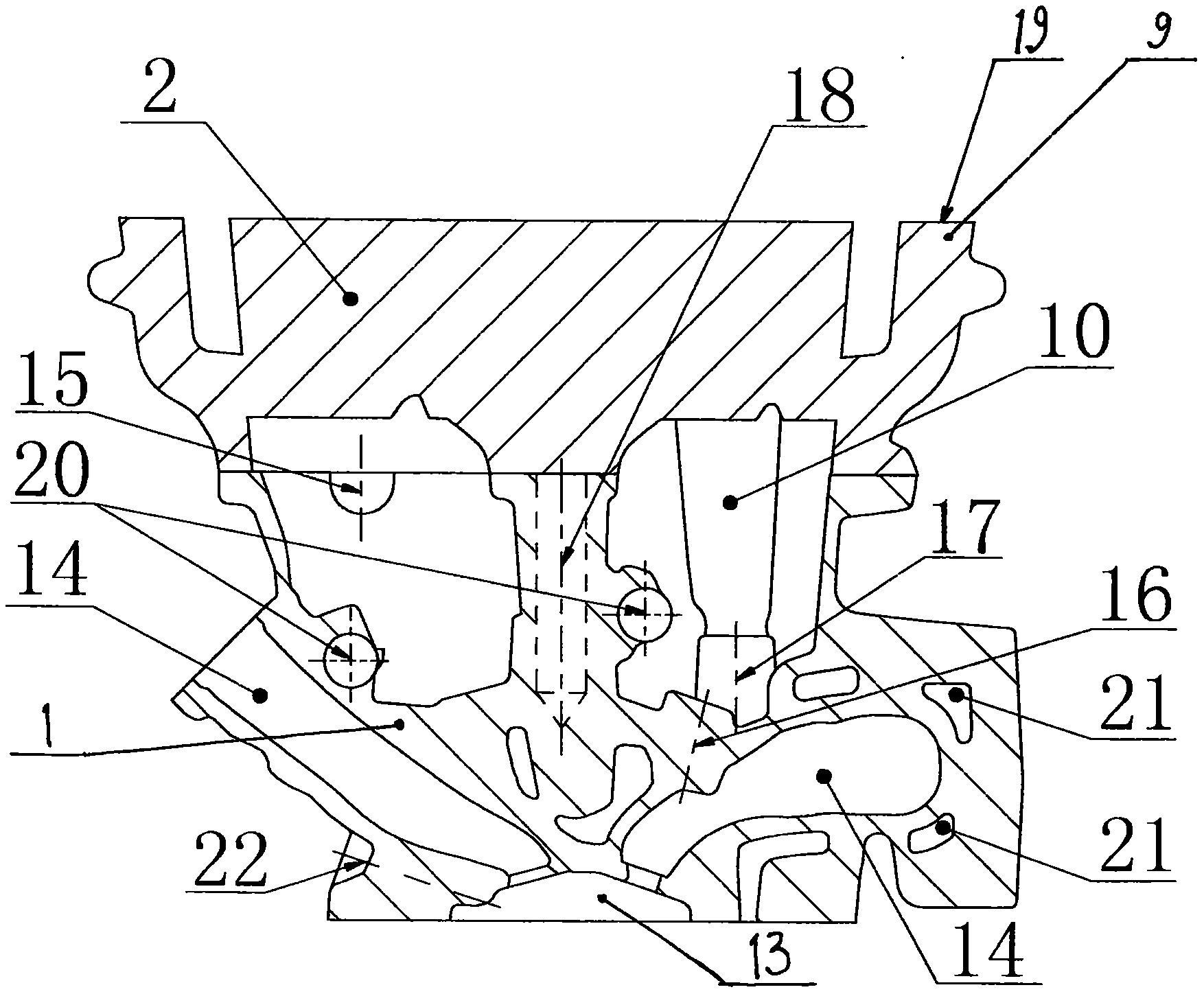
技术摘要:
一种高强度铝合金集成排气缸盖及其倾转式铸造浇注成型工艺,在其缸盖本体的顶部、并在火花塞安装孔上设有冒口,在所述冒口下通过内部冒口依次与螺栓柱、挺杆台相接,在所述冒口的进料口部、并对应于内部冒口的上方处设有截流口;开始90度倾转过程中,铝液在较低的高度 全部
背景技术:
目前,对于铝合金集成排气缸盖的轮廓为512mm×314mm×141mm,其上下两层水 道,水道芯的结构复杂且细长,水道与排气道之间有狭长薄壁,这些对制芯及浇注成型工艺 带来技术上挑战。采用金属模具重力底注式铸造工艺的缺点是:从铸件底部(燃烧室)进料, 不利于从铸件底部到顶部(冒口)的顺序进行凝固,需要加大冒口体积则此工艺出品率约低 12%;从铸件底部进料致温度过高则凝固速率慢,很难满足产品机械性能及燃烧室SDAS要 求;因带有浇道致使金属模具结构庞大、浇注时易漏铝,制作及维护成本高,固化时间长、生 产效率低,容易产生渣孔、加工后暴露等铸造缺陷,铸造综合料废一般能控制在5%以内。采 用金属模具重力顶注式铸造工艺的缺点是:铝液的进浇口位于铸件顶部罩边处,充填金属 模具型腔时,由于落差过大造成铝液流动不平稳,发生飞溅、冲砂、卷气现象,容易引起铝液 氧化,形成铸件内部二次氧化夹渣、浇口对应铸件的下表面氧化流痕及浇口周边产生大气 孔,此铸造工艺铸件质量很难控制。采用金属模具低压铸造式工艺的缺点是:进浇口一般设 置在铸件底面燃烧室周边,则凝固速率很慢,难于满足产品机械性能及燃烧室SDAS要求;在 低压力下成型水道腔易粘砂而难于清理;砂芯在密闭的模具型腔内受热后而发出的气体不 易排出,造成铸件内部气孔;火花塞安装孔与油板交接处壁厚变差较大,且离铸件底部浇冒 口较远,则凝固时铸造应力大,往往热处理后出现裂纹现象,故此铸造工艺对缸盖质量很难 控制。
技术实现要素:
针对现有技术上存在的不足,本发明提供一种高强度铝合金集成排气缸盖及其倾 转式铸造浇注成型工艺,其结构简单、工艺简捷,利用倾转铝液方式而在低位平稳进入金属 模具型腔,避免二次氧化夹渣及气孔风险;从缸盖顶部冒口处进料,有利于铸件从底部至顶 部的顺序进行凝固。 为了实现上述目的,本发明是通过如下的技术方案来实现:高强度铝合金集成排 气缸盖,包括缸盖本体、凸轮轴安装孔及挺杆台、火花塞安装孔、油嘴安装孔、燃烧室,在该 缸盖本体内设有进排气道、上下水套、油道,在所述缸盖本体的顶部、并在火花塞安装孔上 设有冒口,在所述冒口下通过内部冒口依次与螺栓柱、挺杆台相接,在所述冒口的进料口 部、并对应于内部冒口的上方处设有截流口。 在所述缸盖本体的进排气道的侧边处设置水冷镶块。在所述冒口的外两侧装有夹 紧台,所述冒口的顶部设有冒口最低高度刻度线。 所述高强度铝合金集成排气缸盖所采用的倾转式铸造浇注成型工艺为:在90度倾 转进料前,金属模具的顶部、对应于缸盖铸件顶部的冒口的进料口部与浇口杯对接,浇口杯 3 CN 111570731 A 说 明 书 2/3 页 内的铝液面高度处于冒口的根部;开始90度倾转过程中,铝液在较低的高度平稳地进入金 属模具的集成排气腔,确保铝液前沿的氧化膜不会破裂,减少毛坯夹渣及气孔风险,降低铸 件毛坯废品率,在冒口的进料口部设置截流口,防止浇口杯的液面氧化膜提前进入金属模 具型腔内而浮在冒口顶部;所述冒口下的内部冒口连接螺栓柱及挺杆台,防止其缩松同时 对周边的挺杆台进行补缩;在金属模具的排气进料模块内、对应于缸盖本体的进排气道的 侧边处设置有水冷镶块。 在该缸盖本体的设计阶段确保其排气侧罩边的壁厚为4.5-5.5mm,在铸造时排气 侧罩边壁厚走正偏差;在该缸盖本体的设计阶段确保其进气侧罩边的壁厚为5.0-5.5mm,在 铸造时进气侧罩边壁厚走正偏差。 采用本发明后,从缸盖的冒口进料,有利于从铸件底部燃烧室到火花塞安装孔顶 部的顺序凝固方式成形,设置内部冒口连接螺栓柱及挺杆台,能进行有效补缩,保证了产品 性能满足要求。本发明在排气进料模块内设置有水冷镶块,对于17kg毛坯批量连续生产固 化时间在250S能长期稳定生产,体现了突破大铸件能够高效率生产优势。铸造综合废料率 控制在2.3%以内。由于国六的实施对缸盖性能要求提升,其抗拉强度280Mpa、屈服强度 220Mpa、延伸率≥4%、燃烧室SDAS(二次枝晶间距)≤25um;相对原整体性能要求提高15% 以上。此铸造工艺在质量水平、生产效率、铸件机械性能上,在铝合金集成排气缸盖铸造领 域位于领先水平,符合高质量、高效率、高性能的总体要求。 附图说明 下面结合附图和