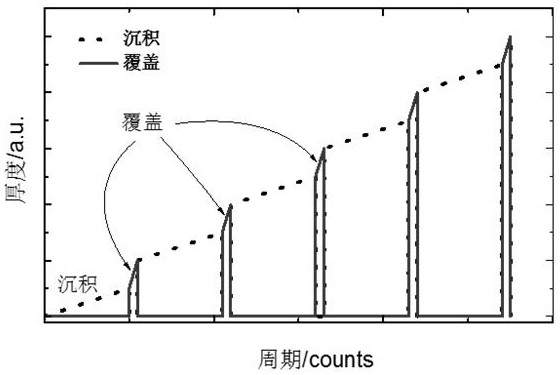
技术摘要:
本发明公开一种稳定高效率硅异质结太阳电池的制备方法,在累积薄膜的表面沉积本征非晶硅薄膜,所述累积薄膜包括沉积腔室内的累积薄膜,对沉积腔室内沉积的本征非晶硅薄膜为高氢含量且高无序度非晶硅薄膜,所述高氢含量是指通过对单位体积内氢原子个数的计算,相对于硅 全部
背景技术:
硅异质结SHJ太阳电池是一种高效率晶体硅太阳电池,因为其转换效率高、温度系 数低等特点受到光伏行业的广泛关注。SHJ电池是一种双面率很高的双面电池,由于背面对 发电量的贡献度大,在相同条件下其发电输出功率高于普通晶体硅太阳电池10%以上,因此 具有更高的性价比。SHJ电池以n型单晶硅片为衬底,基本制作工艺包括制绒清洗,非晶硅薄 膜沉积,透明导电氧化物薄膜沉积,金属电极制作。与常规晶体硅太阳电池相比,工艺过程 更简单,容易管控。 非晶硅薄膜沉积是SHJ太阳电池制作工艺的关键工艺,也是SHJ电池制作技术的难 点。非晶硅薄膜一般使用等离子体增强化学气相沉积(PECVD)、触媒化学气相沉积(Cat- CVD)、光化学气相沉积(Photo-CVD)等设备沉积,在经过制绒并清洗的硅片第一表面沉积本 征非晶硅和n型掺杂非晶硅叠层,形成第一受光面,在第二表面沉积本征非晶硅和p型掺杂 非晶硅薄膜叠层,形成第二受光面。本征非晶硅层对n型单晶硅表面形成良好的表面钝化, 降低表面缺陷对光生载流子的复合。n型和p型掺杂非晶硅与N型单晶硅之间形成内建电场, 分离并收集电子和空穴,形成电力输出。 在硅片表面沉积非晶硅薄膜钝化层的过程中,在腔室的电极表面和腔室侧壁表面 以及放置硅片的托盘表面同时都会沉积非晶硅薄膜,随着沉积时间的增加逐步形成累积薄 膜,当其累计厚度达到2-3微米或者更厚的时候容易剥离产生粉末甚至较大的颗粒散落在 硅片的表面,引起薄膜质量劣化,导致电池的光电转换性能和可靠性下降。尤其在n型和p型 掺杂非晶硅沉积腔,当非晶硅薄膜的累计厚度变厚,掺杂原子累计浓度变高,这种变化将影 响掺杂非晶硅薄膜层和电池整体的性能,造成生产不稳定,因此,在大批量生产和长期实验 中,当腔室和托盘表面的非晶硅累积薄膜累积沉积厚度达到2.0微米甚至更厚的时候就要 利用等离子体对腔室进行清洗,以消除粉末和掺杂原子对薄膜均匀性和电池性能的影响, 提高生产的稳定性。 现有技术中,真空腔室和托盘清洗一般采用对硅材料有刻蚀功能的含氟气体产生 等离子体进行刻蚀,去除表面沉积的非晶硅薄膜和粉末,然而这类气体成本较高,而且,含 氟气体分解产生的氟原子可能残留在腔室内,混入到后续沉积的非晶硅薄膜中,薄膜中的 氟原子在紫外光的照射或者热环境下释放出来,与水气结合形成氢氟酸,影响薄膜的稳定 性。
技术实现要素:
针对连续生产过程中沉积腔室表面累积薄膜,因内应力增加容易剥离导致掉粉, 造成太阳电池的光电转换性能下降,传统方法使用的在线化学清洗频繁使用会造成成本上 4 CN 111599893 A 说 明 书 2/5 页 升、产能下降等问题,本发明提供一种对腔室内表面进行处理的非晶硅薄膜沉积方法,采用 一层或者多层本征非晶硅对腔室内表面处理,可以快速恢复腔室沉积环境,并改善太阳电 池产品持续生产时的光电性能。 为了实现上述目的,本发明采用如下技术方案: 一种稳定高效率硅异质结太阳电池的制备方法,在沉积腔室内沉积本征非晶硅薄膜, 沉积腔室内包括沉积腔室的内表面以及腔室的电极表面。 优选的,沉积本征非晶硅薄膜的周期为,每当累积薄膜的厚度积累到0.01~2.00 µ m时,沉积一层本征非晶硅薄膜。 优选地,为了降低n型和p型掺杂非晶硅薄膜在托盘上积累造成污染界面的风险, 同样需要覆盖5-10 nm任意微结构的本征型非晶硅薄膜。 优选地,对沉积腔室内沉积的本征非晶硅薄膜为高氢含量且高无序度非晶硅薄 膜,所述高氢含量是指通过对单位体积内氢原子个数的计算,相对于硅原子个数5.22× 1022,氢的百分比含量在10%~25%;高无序度是指微结构因子R为15%~80%,且波数2060~2150 cm-1范围内的伸缩振动模数量与总伸缩振动膜(波数1900 ~2200 cm -1)数量相比定义为微 结构因子R。 优选的,所述本征非晶硅薄膜的厚度为2~100 nm。 优选地,在沉积腔室内沉积缓解累计薄膜内应力的本征非晶硅薄膜时,沉积速率 为0.1~2.0 nm/s。 所述稳定高效率硅异质结太阳电池的制备方法,具体包括以下步骤: S1.制绒、清洗,获得表面清洁的晶体硅基底; S2.沉积非晶硅薄膜钝化层:在晶体硅基底的第一表面依次沉积第一受光面的本征硅 基薄膜钝化层和第一受光面的掺杂硅基薄膜钝化层;在晶体硅基底的第二表面依次沉积第 二受光面的本征硅基薄膜钝化层和第二受光面的掺杂硅基薄膜钝化层; S3.制作电极:分别在第一受光面的掺杂硅基薄膜钝化层和第二受光面的掺杂硅基薄 膜钝化层上沉积第一受光面的透明导电氧化物薄膜和第二受光面的透明导电氧化物薄膜, 分别形成第一受光面和第二受光面,接着在第一受光面的透明导电氧化物薄膜和第二受光 面的透明导电氧化物薄膜上制作第一受光面的银栅线电极和第二受光面的银栅线电极; S4.重复S1-S3连续制备电池; S5.处理积累薄膜:S2中沉积非晶硅薄膜钝化层的沉积腔室中,每当沉积腔室内的连续 累积薄膜厚度达到0.01~2.00 µm时,采用厚度为2~100 nm的本征非晶硅薄膜覆盖沉积腔 室;然后再重复S1-S3制作电池。 优选的,S5利用PECVD、Cat-CVD、Photo-CVD等薄膜沉积设备的n型和p型参杂非晶 硅薄膜沉积腔中,生产累计厚度达到0.01微米至2.00微米的厚度后,托盘不放置硅片,在腔 室和托盘表面沉积一层或者多层本征非晶硅薄膜,对腔室和托盘表面进行镀膜处理,覆盖 表面沉积的n型和p型非晶硅层,降低腔室内薄膜的内应力和托盘表面累计沉积的掺杂层对 后续掺杂浓度的影响,提高电池性能稳定性和生产性的硅异质结太阳电池制作方法。用于 覆盖托盘上掺杂元素的任意结构非晶硅薄膜,可与对内腔薄膜改性处理同时进行。 优选的,S1中制绒、清洗具体为,利用碱溶液对单晶硅各向异性腐蚀特性对n型单 晶进行制绒,利用RCA1和RCA2溶液对硅片进行清洗。 5 CN 111599893 A 说 明 书 3/5 页 优选地,S2中硅基薄膜钝化层沉积的方法包括等离子体增强化学气相沉积、热丝 化学气相沉积和光敏化化学气相沉积,所述第一受光面的本征硅基薄膜钝化层、第一受光 面的掺杂硅基薄膜钝化层、第二受光面的本征硅基薄膜钝化层和第二受光面的掺杂硅基薄 膜钝化层在同一腔室内沉积,或者独立的腔室内完成沉积,同一沉积腔室内硅基薄膜钝化 层沉积的方法与用于覆盖腔室和托盘的非晶硅薄膜的沉积方法相同。 优选地,S5中对沉积腔室内和托盘表面进行镀膜处理的本征非晶硅薄膜的工艺气 体为硅烷和氢气,氢气与硅烷([H2]/[SiH4])的流量比为0~5:1 优选地,覆盖沉积腔室内时,本征非晶硅薄膜沉积速率为0.1~2.0 nm/s。 与现有技术相比,本发明的有益效果在于: (1)随着沉积腔室内硅薄膜的累积,腔内加热器的热量和沉积薄膜过程中的等离子体 弛豫会使累积薄膜内的氢逐渐逸出,造成硅网络内出现少氢现象且薄膜内应力增加。当累 积的薄膜达到一定厚度,内应力大于附着力后,累积的薄膜存在剥落的风险,甚至就会从腔 室内壁剥落。本发明在沉积腔室内沉积本征非晶硅薄膜,且该本征非晶硅薄膜为高氢含量 且高无序度非晶硅薄膜,高氢含量且高无序代表薄膜内有很多SiH2、SiHx或SiH2构成的孔 洞,此种结构耐受热量和等离子体轰击影响,周期性覆盖可以增多累积薄膜内的氢含量,同 时也可缓冲累积薄膜中强内应力的产生。腔室内累积薄膜越厚,需要的本征非晶硅薄膜的 厚度越厚,可以有效减小累积薄膜的内应力而避免腔内累积薄膜的脱落,在累积薄膜的膜 厚为0.01 µm~2.00 µm内,实施本征非晶硅薄膜覆盖改性处理以减小累积薄膜的内应力,降 低剥离风险,既可以解决累积薄膜因内应力造成的剥落的掉粉问题,快速恢复腔室沉积环 境、延长腔室和托盘清洗周期,降低在线化学清洗频率可以提升设备有效生产的时间,实现 产能增加而降低成本;又可以通过本征层的有效覆盖,降低掺杂元素在腔壁内表面和托盘 上累积的影响,提升产线持续生产时太阳电池的光电转换效率。 (2)本征非晶硅薄膜被周期性引入覆盖腔室和托盘后,可以有效改善腔壁内部和 电极上累积薄膜的内应力,达到一个清洗周期时腔壁内累积的薄膜厚度可以由1.5 µm提高 至5 µm以上,大幅度延长一个清洗周期的时间,提高生产效率,减少NF3和Ar气体耗量,提高 产量的同时降低成本。 (3)本发明可以快速处理累积薄膜,获得稳定高效率硅异质结太阳电池。 附图说明 图1显示为SHJ太阳电池结构示意图; 图2显示为本发明本征非晶硅薄膜的周期性沉积、覆盖腔室和托盘的示意图; 图3显示为本发明用本征非晶硅薄膜盖腔室和托盘后电池IV参数的变化; 图中,101-晶体硅基底,102-第一受光面的本征硅基薄膜钝化层,103-第一受光面的掺 杂硅基薄膜钝化层,104-第二受光面的本征硅基薄膜钝化层,105-第二受光面的掺杂硅基 薄膜钝化层,106-第一受光面的透明导电氧化物薄膜,107-第二受光面的透明导电氧化物 薄膜,108-第一受光面的银栅线电极,109-第二受光面的银栅线电极。