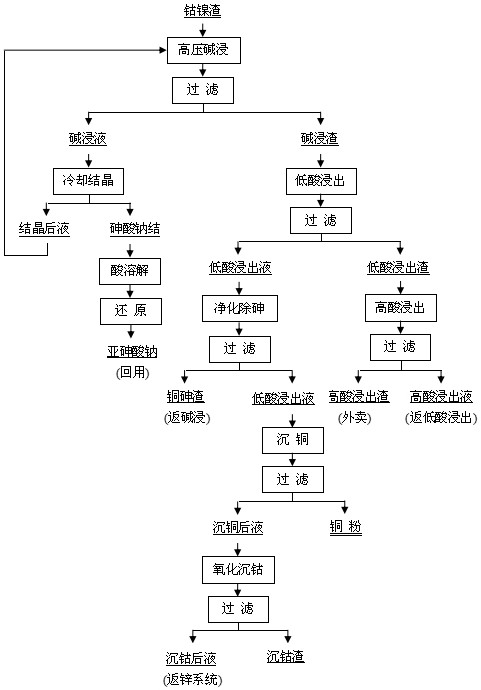
技术摘要:
本发明公开了一种湿法炼锌砷盐净化钴镍渣的资源综合利用方法,将湿法炼锌砷盐净化钴镍渣进行碱性浸出,过滤得到碱浸液和碱浸渣;将碱浸液冷却结晶得到砷酸钠,用水将砷酸钠溶解并调节pH至2‑4,再通入SO2还原,得到亚砷酸钠溶液;将碱浸渣进行二段浸出,第一段低酸浸出 全部
背景技术:
国内外湿法炼锌过程中,采用锌粉 三氧化二砷净化(简称砷盐净化)除钴具有锌 粉消耗低、净化效果好,且产出的铜渣和钴镍渣有价金属富集度高。国内某湿法炼锌厂硫酸 锌溶液净化采用砷盐净化除钴,年产钴镍渣1500-1800吨,其中含有价金属Cu42-53%、 Co1.5-5.0%、Zn8-13%,同时含As8-15%。 钴镍渣中有价元素铜、钴、锌和砷含量较高,同时含有一定量的铅银,回收价值较 高。但是,渣中砷与铜、钴和镍等元素以合金形式存在,稳定性较高,且成份复杂,处理难度 相对较大,有些工厂都未做处理或仅仅简单处理后回收钴镍渣中的铜,造成了资源浪费,并 且易引起环境污染。如送铜鼓风炉回收铜,锌、钴等有价金属未进行回收,且As进入烟气中 或少部分进入粗铜或渣中,从而导致烟尘难于回收,粗铜中含As也对电解造成影响,同时进 入渣中的锌、钴和砷等使渣量增加,铜冶炼能耗增加,单位生产成本增加。 《资源再生》2010年第9期对于锑盐除钴净化渣的处理提出的工艺:采用酸性浸出 锌、镉、钴等有价金属使其进入溶液,并控制铜进入渣,浸出液氧化除铁、锌粉除铜,再沉钴, 沉钴渣经过酸洗除杂后焙烧得到四氧化三钴。该法的缺点是渣中的镍及锌没有得到有效回 收。《中南大学学报》2001年第32卷第4期提出了氨-硫酸铵体系处理湿法炼锌锑盐净化钴渣 的工艺。本方法中可直接提取钴或钴盐,同时制取活性锌粉,但该工艺采用铵-氨水溶液作 浸出剂,操作环境较为恶劣。《锌加压浸出工艺与装备国产化及液态铅渣直接还原专题研讨 会论文集》中论文报道了砷盐净化工艺产出的钴镍渣中有价元素的火法及湿法联合提取工 艺。先对二段浸出渣进行选择性浸锌,并对浸锌渣进行焙烧,使砷开路,同时使铜、钴、镍等 有价金属转化成易经酸浸出的氧化物。焙烧渣酸浸后,采用铁粉置换除铜使铜与钴镍分离。 该工艺明显存在除铜后液中铁含量过高问题。 CN 102534235 A 公布了一种从湿法炼锌砷盐净化钴镍渣中回收有价金属的方 法,包括步骤:硫酸选择性浸出、煅烧、硫酸二次浸出、沉砷铜和沉钴镍,从而能将钴镍渣中 的有价金属锌、铜、钴和镍分别分离并回收。CN 102965499 B公布了一种湿法炼锌砷盐净化 渣中有价元素提取方法。该方法采用全湿法流程处理湿法炼锌砷盐净化渣,通过选择性浸 锌,氧化浸出铅、中和沉砷铜、沉淀法回收钴镍;中和沉砷得到的沉砷铜渣碱浸分离铜砷。CN 105567999 B公布了一种从湿法炼锌砷盐净化钴镍渣中回收有价金属的方法,包括步骤:锌 电解废液浸出、焙烧、锌电解废液二次酸浸、高锰酸钾氧化沉钴,从而实现了有价金属Zn、Co 和Ni等有价金属的回收。这三种方法类似,都存在废水排放问题,且在选择性浸锌步骤会产 生有毒气体砷化氢。 因此,如何找到一种有效分离钴镍渣中的有价金属的方法,并分别加以回收是有 待进一步探索的难题。 3 CN 111575491 A 说 明 书 2/5 页
技术实现要素:
本发明的目的在于针对现有技术之不足,提供一种湿法炼锌砷盐净化钴镍渣的资 源综合利用方法,该方法具有绿色环保特点,简单易行,钴镍渣中的有价元素砷、锌、铜、钴、 银和铅都得到了回收,砷以亚砷酸钠的形式返砷盐净化系统回用,回收率达95%;锌回锌系 统得到了回收;铜通过控电位沉铜得到高纯铜粉,回收率达超过98%;钴以四氧化三钴的形 式分离并回收,回收率超过92%,铅银在第二段酸浸渣中得以富集。本发明技术无特殊设备 要求,无“三废”产生,属于绿色环保湿法冶炼工艺。 本发明的技术方案是: 一种湿法炼锌砷盐净化钴镍渣的资源综合利用方法,其特征在于,包括以下步骤: A、高压碱性浸砷:把湿法炼锌砷盐净化钴镍渣(以下简称钴镍渣)在碱浓度为3.8- 5.2mol/L,浸出温度为125-130℃,浸出时间3-5h,过滤得到碱浸液和碱浸渣; B、砷还原:把步骤A所得的碱浸液冷却结晶得到砷酸钠结晶,用水将砷酸钠结晶溶解, 得到砷酸钠溶液,调节砷酸钠溶液的pH至2-4,再通入SO2还原,得到亚砷酸钠溶液;其中,还 原时间1.5-3.0h,SO2用量为SO2与砷酸钠溶液中的砷的摩尔比(2.05-2.15):1; C、酸性浸出:把步骤A所得的碱浸渣进行二段浸出,第一段低酸浸出,低酸浸出液的硫 酸浓度为15g/L-25g/L,控制终点pH=1.5-2.8,得到的低酸浸出液,所述低酸浸出液中的Cu 离子浓度为80-95g/L,低酸浸出渣进第二段高酸浸出,高酸浸出液的硫酸浓度为60g/L- 90g/L; D、净化除砷:将步骤C所得的低酸浸出液进行铜粉除砷,温度82-88℃,时间3-5h,铜粉 用量3-5g/L,过滤得到除砷液和除砷渣; E、控电位沉铜:将步骤D所得的除砷液进行控电位沉铜,沉铜温度55-65℃,沉铜时间为 60-90min,终点pH=3.2-4.5,终点电位80~100mv,过滤得到沉铜后液和铜粉; F、氧化沉钴:将步骤E所得的除铜后液中加入次氯酸钠进行氧化沉钴,温度为75~85 ℃,时间为60~90min,终点pH=3.5~5.0。 作为对本发明的进一步改进,所述的步骤A中的液固比为(4-6):1,氧分压为2.6- 3.0MPa,通入的氧气为纯氧。 作为对本发明的进一步改进,所述的步骤B中的调节溶液酸度使用硫酸,还原过程 中饱和析出的三氧化二砷晶体用氢氧化钠溶液溶解,得到含As100-130g/L的亚砷酸钠溶 液,返湿法炼锌用于砷盐净化除钴。 作为对本发明的进一步改进,所述的步骤C中的浸出剂为硫酸溶液,第一段浸出为 低酸浸出,浸出温度为55-65℃,浸出时间为60-90min;第二段浸出为高酸浸出,浸出的液固 比(即浸出剂与一段浸出渣的质量百分比)为(8-12):1,浸出温度为80-85℃,浸出时间为3- 5h,浸出终点硫酸含量为15 -30g/L,接近终点时每升溶液加入双氧水10-20mL。 作为对本发明的进一步改进,所述的步骤D中的铜粉为活化铜粉,粒度控制为180- 260目。 作为本发明的进一步改进,所述的步骤D中的活化铜粉为下一步控电位沉铜得到 的新鲜海绵铜粉经进一步活化处理得到。 作为对本发明的进一步改进,所述的步骤E中的沉铜锌粉为置换铜所需要的理论 量(理论量即1摩尔铜离子需要1摩尔锌粉进行置换)的0.98-1.0倍;所用锌粉质量要求:Zn 4 CN 111575491 A 说 明 书 3/5 页 ≥99.9%,锌粉的粒度为0.25-0.09mm;沉铜后液中铜含量为0.23-0.32g/L。 作为对本发明的进一步改进,所述的步骤E中控电位沉铜得到的铜粉先经含硫酸 为20-30g/L的硫酸溶液酸洗,酸洗温度50℃-60℃,时间60-90分钟,液固比(5-8): 1。 作为对本发明的进一步改进,所述的步骤E中酸洗后的铜粉经2次去离子水洗,洗 温度45-55℃,时间30-45min,液固比(5-8):1,过滤得到的铜粉再经真空干燥处理。 作为对本发明的进一步改进,所述的步骤E中干燥后的铜粉在氮气或氩气等保护 条件下或煤油中进行球磨,得到产品超细铜粉。 作为对本发明的进一步改进,所述的步骤F中的次氯酸钠中游离碱在0.1-0.5%之 间,有效率5-11%,所需次氯酸钠的量为氧化二价钴成三价钴的理论量的12-15倍。 与现有技术相比,本发明的有益效果在于: 本发明优先对钴镍渣采用高压碱浸与碱浸渣经第一段低酸浸出所得低酸浸出液采取 净化除砷工艺,保证了后续控电位沉铜所得铜粉的品位和杜绝有毒气体砷化氢的产生;高 压碱浸得到的砷酸钠溶液采用碱浸还原技术,生成的亚砷酸盐用于湿法炼锌砷盐净化除 钴,在系统内部形成了砷的循环利用,达到了绿色环保和资源的综合回收;通过高压碱浸和 第二段酸性浸出,酸浸渣中铅银与钴镍渣相比富集了30-40倍,可作为回收铅银的原料或外 卖;同时通过控电位技术回收的铜粉经过处理得到超细铜粉;钴以四氧化三钴的形式沉淀 加以回收。其中砷、铜、锌、钴、铅和银的回收率分别为95%、98%、96%、92%、98.5%和98.5%。本 发明提供的方法,能将钴镍渣中的有价金属砷、铜、锌、钴、铅和银分别分离并加以回收,工 艺简单,生产成本低。本发明提供的方法,消除了现有技术中钴镍渣堆存对环境的污染影响 或铜鼓风炉处理带来的砷金属的污染物的风险,形成了砷在系统内部循环利用,真正实现 了钴镍渣中有价资源的综合回收。 附图说明 图1为本发明的工艺流程图。