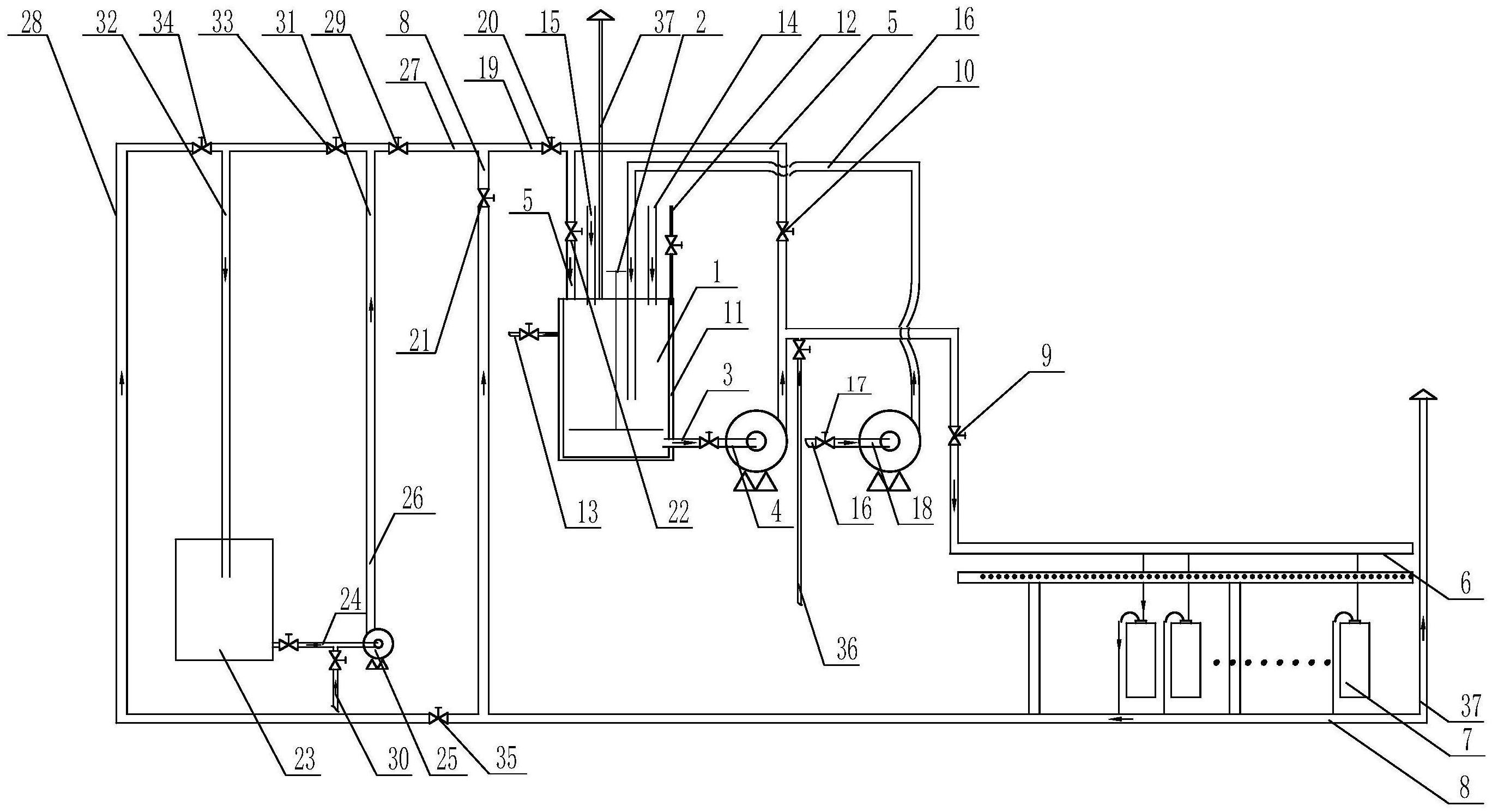
技术摘要:
本发明涉及蓄电池加工技术领域;具体涉及一种胶体循环系统,包括反应釜、循环管组和搅拌装置,循环管组包括与反应釜底部连通的循环出料管,循环出料管依次连接循环泵和循环泵出料管,循环泵出料管管端与反应釜连通,循环泵出料管中间部分通过三通连接电解液加注管,电 全部
背景技术:
随着《铅酸蓄电池准入条件》的出台,胶体蓄电池的制造工艺主要为蓄电池内化成 方式。目前蓄电池内化成主要有两种:一是蓄电池灌注胶体电解液后进行蓄电池内化成,该 种方式的生产工艺相对简单,减少了槽化成工序,降低了生产成本,减少了污染物的排放。 但是蓄电池内化成时需要灌注较高密度(1.200g/cm3以上)的胶体电解液,灌注电解液后遇 到的第一个问题是蓄电池的温升。如果注入常温的胶体电解液,外部不进行降温,蓄电池温 度可达70℃以上,因此,为了避免该现象的发生,通常采用灌注10℃以下的冷酸(将胶体电 解液提前降温冷却),蓄电池灌胶后立即送入带有降温水的水槽中进行外部降温,使蓄电池 温度控制在45℃以下;遇到的第二个问题是蓄电池槽一般是工程塑料制作的,传热效果差 降温效果不好,蓄电池温度高,只能采用小电流长时间的充放电方式,生产周期长,一般为 (5~6)天;遇到的第三个问题是蓄电池在较高密度的情况下进行激活,生成大颗粒的硫酸 铅不易转化,使得初期容量偏低约10%~20%,不易达到产品设计目标,尤其是高度大于 500mm的胶体蓄电池。 二是采用酸循环激活的方法进行化成,化成结束后将蓄电池进行放电,放电后将 蓄电池内的硫酸电解液倒出,灌注胶体电解液,灌胶后的蓄电池进行完全充电。该种生产方 式通过采用蓄电池酸循环激活的方法,化成电解液为低密度酸液,解决采用高密度胶体电 解液化成时初期容量偏低10%~20%的问题,同时利用电解液外循环的方式解决了化成过 程中降温问题,可提高化成电流,缩短化成时间(3~4天),能够很好的解决普通蓄电池内化 成工艺中初期容量偏低、化成时间长、降温效果不好的问题,具有较强的实用性。但是该方 法生产工艺相对繁琐,主要有酸循环化成后蓄电池放电、倒酸、灌胶、充电等过程,生产成本 高。
技术实现要素:
为解决上述技术问题,本发明提供一种胶体循环系统及管式胶体蓄电池的加工方 法,代替了现有的蓄电池内化成工艺,能够有效解决胶体电解液化成初期容量偏低和化成 过程中降温的问题,减化生产工艺,降低生产成本。 本发明所述胶体循环系统,包括反应釜、循环管组和搅拌装置,所述搅拌装置的搅 拌动作端延伸至反应釜底部,所述循环管组包括与反应釜底部连通的循环出料管,循环出 料管依次连接循环泵和循环泵出料管,循环泵出料管管端与反应釜连通,循环泵出料管中 间部分通过三通连接电解液加注管,电解液加注管依次连接电池连接器进酸管、胶体电池、 电池连接器回酸管、电解液回流管,电解液回流管与反应釜内腔连通,电解液加注管上设置 加注阀,电解液加注管两侧的循环泵出料管管段上分别设置循环泵和自循环阀。 4 CN 111569805 A 说 明 书 2/8 页 通过本系统进行胶体循环时,将电池连接器进酸管与蓄电池电解液进口连通,将 电池连接器回酸管与蓄电池电解液出口连通,蓄电池安装后,开启循环泵,反应釜内配置好 的电解液在循环泵的作用下通过电解液加注管及电池连接器输送至胶体电池,置换后的电 解液通过胶体电池出口回流至电解液回流管,最终输送回反应釜。在胶体循环的过程中,通 过充电机采用恒压限流的方式对蓄电池进行充电。为防止反应釜内的胶体电解液凝胶,在 蓄电池生产过程批次之间的时间,开启搅拌装置,打开自循环阀和循环泵,使胶体电解液进 行自循环。 优选地,反应釜外部设置水冷套,水冷套进水口和出水口连接冷却水进管和冷却 水出管,冷却水进管上设置进水阀,冷却水出管上设置出水阀;打开进水阀,向反应釜内外 胆之间的水冷套中输送入5℃~10℃冷却水,水冷套中的冷却水通过出水阀和冷却水出管 输送到制造冷却水的主机部分进行冷却。 优选地,所述胶体循环系统还包括与反应釜内腔连通的配胶管组,配胶管组包括 与反应釜内腔连通的第一加料管、第二加料管和第三加料管,第一、二、三加料管上均设置 加料阀,第三加料管的加料阀和反应釜之间的管路上设置加料泵,通过第一加料管向反应 釜输入配方量的蓄电池用水,开启搅拌装置,通过第二加料管向反应釜输入配方量的浓硫 酸,通过第三加料管及加料泵向反应釜中真空输送配方量的二氧化硅。 优选地,所述电解液回流管通过第一过渡管和三通与循环泵出料管连通,电解液 回流管上设置回流阀,第一过渡管上设置第一过渡阀,第一过渡管和反应釜之间的循环泵 出料管上设置进釜阀,电解液回流管通过第一过渡管汇总至循环泵出料管进反应釜,减少 反应釜进釜管路。 优选地,所述胶体循环系统还包括清洗管组,所述清洗管组包括依次连接的回收 罐、第一清洗管、清洗泵、第二清洗管、第二过渡管、电解液加注管、电池连接器进酸管、U形 管、电池连接器回酸管、电解液回流管、清洗回流管,清洗回流管与回收罐连通,清洗回流管 与电解液回流管的中间部分连通,清洗回流管上设置清洗回流阀,第一清洗管连通清洗进 水管,清洗进水管上设置清洗进水阀,第一清洗管上设置第一清洗阀,第二过渡管上设置第 二过渡阀。 清洗时,关闭进釜阀,打开第一清洗阀、清洗进水阀、第二过渡阀、第一过渡阀、自 循环阀、加注阀、清洗回流阀,清洗水通过清洗进水管进入,在清洗泵的作用下,依次经过第 二清洗管、第二过渡管、第一过渡管、循环泵出料管、电解液加注管、胶体电池、电解液回流 管、清洗回流管,最后进入回收罐,清洗时长持续2-3分钟,清洗完成后清洗泵停机。 优选地,所述第二清洗管通过三通连接第二过渡管和回收循环管路,回收循环管 路通过三通分别连接至清洗回流管和回流总管,回流总管与回收罐连通,回收循环管路上 设置回收循环阀,为防止电解液回流管中的电解液和回收循环管路中的清洗水进入清洗回 流管,在清洗回流管的两端分别设置第一清洗回流阀和第二清洗回流阀。 优选地,所述电解液加注管连接循环泵出料管的一端连接清洗气管,清洗气管上 设置清洗气阀,清洗泵停机后,关闭第一进水阀和第一清洗阀,打开清洗气阀,通入压缩空 气,压缩空气将电解液加注管、电解液回流管、第二过渡管、回收循环管路和回流总管中的 残留水分吹扫干净。 本发明还提供一种管式胶体蓄电池的加工方法,采用上述胶体循环系统,包括以 5 CN 111569805 A 说 明 书 3/8 页 下步骤: 1.1、配胶:在反应釜中根据成品电池出厂时胶体中硫酸含量的密度和二氧化硅含 量配制胶体电解液; 1 .2、胶体循环:激活后的蓄电池运送至胶体循环系统,将蓄电池与充电机电气连 接,将蓄电池连接器安装于蓄电池电解液进、出口,打开加注阀、启动循环泵和充电机,进行 胶体循环及充电; 1.3、二次配胶;向反应釜中加入定量的二氧化硅并搅拌,以步骤1.2中胶体循环时 蓄电池内的硫酸总量为依据计算加入反应釜的二氧化硅的量; 1.4、二次胶体循环:重复步骤1.2,直至胶体循环系统内的电解液密度在一定时间 内无变化,停止充电和循环。 配胶之前先启动冷却部分:打开冷却水进管上的进水阀,向反应釜水冷套中输送 入5℃~10℃冷却水,再打开出水阀,通过冷却水出管,将反应釜水冷套内的水输送到制造 冷却水的主机部分进行冷却。 配胶时,通过第一加料管向反应釜输入配方量的蓄电池用水,开启搅拌装置,通过 第二加料管向反应釜输入配方量的浓硫酸,打开第三加料管上的加料阀,启动加料泵,二氧 化硅通过第三加料管向反应釜中真空输送配方量的二氧化硅,自二氧化硅全部进入反应釜 后,胶体电解液配制完成,此时配制的胶体电解液中硫酸和二氧化硅含量同胶体蓄电池出 厂时的含量。 为方便控制,在循环泵出料管上设置循环出料阀,胶体循环时,打开循环出料阀和 加注阀,启动循环泵,反应釜中的胶体电解液通过电解液加注管和电池连接器进酸管进入 蓄电池,蓄电池内流出的电解液通过电解液回流管回流至反应釜,充电机采用恒压限流的 充电方式对蓄电池进行充电。胶体循环和充电持续1-2小时后停止。 电解液回流管未与反应釜连通的一端设置排气管道,在反应釜上也设置排气管 道,便于电池充电时产生气体的排出;胶体循环过程中反应釜搅拌装置不停止搅拌,胶体循 环过程冷却系统持续工作;采用铅酸蓄电池酸循环化成的方法对蓄电池进行激活;步骤1.4 中,胶体循环系统循环1.5-2.5小时后开始测量胶体电解液密度,之后每0.3-0.5小时测量 一次电解液密度,直至胶体电解液密度至少保持2小时无变化,停止充电和胶体循环系统, 步骤1.3反应釜中加入二氧化硅后搅拌8-15分钟。 优选地,上述管式胶体蓄电池的加工方法,还包括管道清洗,管道清洗的步骤为: 2.1、从蓄电池上取下电池连接器,用U型管将电池连接器的进、回酸管连接,关闭 进釜阀,打开第一清洗阀、第一进水阀、第二过渡阀、第一过渡阀、自循环阀、加注阀、回流 阀,从清洗进水管输送蓄电池用水,经第二清洗管、第二过渡管、第一过渡管、循环泵出料 管、电解液加注管、电池连接器进酸管、U型管、电池连接器回酸管、电解液回流管流至回收 罐,清洗时间2-3分钟,停止清洗泵,关闭清洗进水阀和自循环阀; 2.2、打开清洗气阀,压缩空气依次经过清洗气管、电解液加注管、电池连接器进酸 管、U型管、电池连接器回酸管、电解液回流管、第二过渡管、回收循环管路和回流总管,将管 道壁内多余的水冲入回收罐; 2.3、关闭清洗气阀,拆卸蓄电池连接器上的U型管。 优选地,上述管式胶体蓄电池的加工方法,还包括胶体回收,具体为: 6 CN 111569805 A 说 明 书 4/8 页 配胶时,回收罐中含胶回收水溶液通过第一清洗管、清洗泵、第二清洗管、第二过 渡管、第一过渡管和循环泵出料管输送至反应釜,回收利用。 为了防止反应釜内的胶体电解液凝胶,在蓄电池生产过程批次之间的时间,需开 启搅拌装置,打开自循环阀和进釜阀,启动循环泵,进行胶体电解液的搅拌和自循环。 为了防止回收罐内的胶体电解液凝胶,回收罐内的含胶水溶液被反应釜使用前, 需打开第一清洗阀、回收循环阀,启动清洗泵,进行含胶水溶液的自循环,回收罐内含弱胶 体的水回收利用,作为反应釜中的溶剂。 与现有技术相比,本发明具有以下有益效果: 本发明通过采用胶体循环的方法,代替了现有的蓄电池内化成工艺,有效解决胶 体电解液化成初期容量偏低和化成过程中降温的问题,减化了生产工艺,缩短生产20h,减 少能量损失(1.8-2.0)Ca安时(Ca指额定容量),降低了生产成本,具有较强的实用性。 附图说明: 图1、实施例1结构图。 图中:1、反应釜;2、搅拌装置;3、循环出料管;4、循环泵;5、循环泵出料管;6、电解 液加注管;7、胶体电池;8、电解液回流管;9、加注阀;10、自循环阀;11、水冷套;12、冷却水进 管;13、冷却水出管;14、第一加料管;15、第二加料管;16、第三加料管;17、加料阀;18、加料 泵;19、第一过渡管;20、第一过渡阀;21、回流阀;22、进釜阀;23、回收罐;24、第一清洗管; 25、清洗泵;26、第二清洗管;27、第二过渡管;28、清洗回流管;29、第二过渡阀;30、清洗进水 管;31、回收循环管路;32、回流总管;33、回收循环阀;34、第一清洗回流阀;35、第二清洗回 流阀;36、清洗气管;37、排气管道。