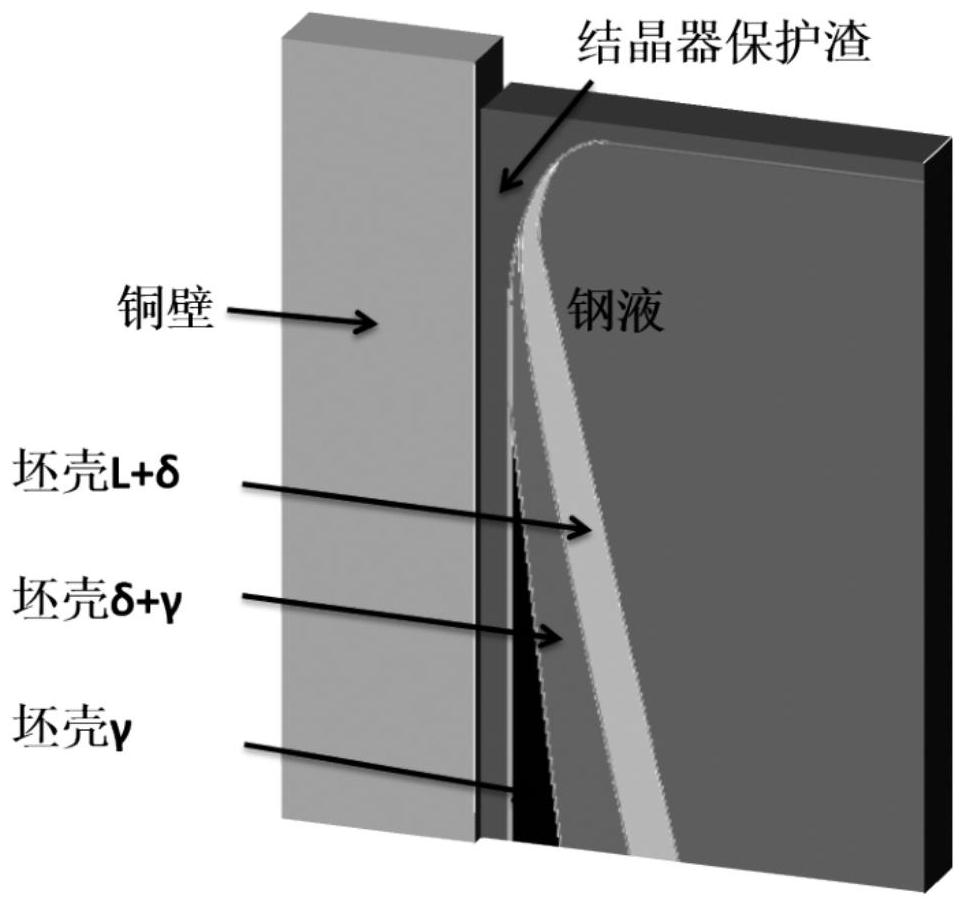
技术摘要:
本发明公开了一种低碳低合金钢用超高拉速薄板坯连铸保护渣,该保护渣的化学成分重量百分比为:CaO:28~30%,SiO2:24~26%,Al2O3:5~7%,MgO:5~7%,Na2O:7~9%,K2O:0~1%,CaF2:7~9%,Fe2O3:0~1%,Li2O:1~2%,C:5~7%,余量为不可避免的杂质 全部
背景技术:
连铸保护渣是一种以硅酸盐为基的含有多种熔剂和骨架材料的功能性材料。随着 连铸拉速的不断提高和电磁制动设备的使用,使得结晶器内保护渣所处环境及表现出的冶 金行为发生较大变化,尤其是熔化均匀性及润滑性能难以保证。另外,由于漏斗型结晶器的 复杂结构,连铸坯的裂纹敏感性也愈发凸显,这就需要同时对保护渣的控制传热、保障初生 坯壳均匀生长方面的性能进行优化。 此外,随着拉速的增加,结晶器液面处钢液更新速度加快,从动力学角度为钢渣反 应和保护渣吸附夹杂物创造了条件,这对保护渣使用过程中的稳定造成了不利影响。既要 使保护渣润滑性能优异,又要具有较强的控制传热的能力,以保证坯壳与结晶器壁有较小 的摩擦力又能均匀生长,避免发生裂纹,这就对保护渣的性能提出了新的更为复杂的技术 要求。 电磁制动不但能影响钢液在结晶器内的流场,对结晶器内的温度场也具有较大的 影响,进而影响保护渣的熔化、结晶、流入、润滑等一系列的行为。 相对于中厚板坯和方坯结晶器,薄板坯坯壳表面温度在不同位置的差异性较大。 此外,随着拉速的升高,保护渣单位时间消耗量加大,振动频率的相应增加,导致结晶器内 保护渣流入趋于困难。同时,结晶器内钢液流速和弯月面的湍动加剧,易将液面上的熔融保 护渣卷入到钢水中,从而引起漏钢和铸坯质量事故。电磁制动设备的引入将会有效降低结 晶器内的钢液流动速度,减少结晶器液面波动,进而减小结晶器卷渣几率。但是电磁制动使 结晶器内温度场也发生较大改变,由此导致保护渣熔化和流入的均匀性下降,危害连铸坯 质量,裂纹和夹渣发生率上升。因此,需要系统地研究保护渣在不同拉速(特别是超高拉速) 下的各项性能,综合评价保护渣在电磁制动下的超高拉速薄板坯连铸过程中的适用性。 尽管添加合金元素后该钢种的平衡相图与经典Fe-C相图相比有所变化,但是仍然 处于低碳钢的范畴。凝固过程中主要为δ-铁素及体,涉到奥氏体相变转化非常少,因此认为 该钢种在凝固过程中产生的体积收缩量较小。针对此类钢种在结晶器内的浇注过程,应加 强关注坯壳与铜壁的润滑和摩擦问题。
技术实现要素:
本发明的目的就是发明一种电磁制动条件下低碳低合金钢用超高拉速薄板坯连 铸保护渣,它能够在超高拉速、使用电磁制动设备和漏斗型结晶器情况下保证足够的液渣 层厚度,同时提高其润滑能力,改善传热,减少铸坯裂纹和夹渣的发生率,为生产稳定、高效 顺行提供保障。换言之,本发明在原有常规<5.0m/min拉速薄板坯低碳低合金钢用连铸保 护渣的基础上设计了一种电磁制动条件下低碳低合金钢用超高拉速薄板坯连铸保护渣,进 3 CN 111604482 A 说 明 书 2/6 页 一步提高其润滑性能,减少铸坯缺陷。 为实现上述目的,本发明所设计的低碳低合金钢用超高拉速薄板坯连铸保护渣, 其化学成分百分比为:CaO:28~30%,SiO2:24~26%,Al2O3:5~7%,MgO:5~7%,Na2O:7~ 9%,K2O:0~1%,CaF2:7~9%,Fe2O3:0~1%,Li2O:1~2%,C:5~7%,余量为不可避免的杂 质。 进一步地,该保护渣较佳的化学成分百分比为:CaO:28.5~29.5%,SiO2:24.5~ 25.5%,Al2O3:6.1~6.8%,MgO:5.9~6.3%,Na2O:7.8~8.6%,K2O:0.1~0.3%,CaF2:7.9 ~8.2%,Fe2O3:0.4~0.6%,Li2O:1.1~1.3%,C:5.9~6.8%。 更进一步地,该保护渣的碱度最好控制在1.1~1.3范围,该保护渣的熔点最好控 制在1050~1070℃范围,该保护渣1300℃时的粘度最好控制在0.03~0.05Pa·s范围。 本发明的低碳低合金钢用超高拉速薄板坯连铸保护渣中各种化学成分的作用机 理及限定原因如下: CaO:是保护渣的主要成分之一,它和析晶温度有关,属于网络外氧化物。因此,提 高保护渣中CaO的含量,可明显降低渣的粘度,并吸收钢中氧化物夹杂物,尤其是Al2O3和 TiO2。本发明中,由于控制保护渣的碱度为1.1~1.3,同时保证保护渣具有良好的析晶性 能,所以本发明将CaO重量百分含量控制在28~30%范围,优选28.5~29.5%范围。 SiO2:属于网络形成体,提高保护渣中SiO2的含量可明显提高渣的粘度,同时使保 护渣生成玻璃相,易于铸坯润滑。但如果太高,专利CN101954464中指出会形成链状结构 [SiO3]n,使保护渣粘度过高,润滑效果降低;如果太低,不利于保护渣的玻璃相形成,无法满 足连铸坯的润滑需求。本发明中,由于控制保护渣的碱度为1.1~1.3,同时保证保护渣具有 一定的润滑性能,所以本发明中SiO2含量控制在24~26%范围,优选为24.5~25.5%范围。 Al2O3:渣中增加Al2O3会增加渣的粘度,但它可降低渣的凝固点,由此改善结晶器 润滑。但大量进入熔渣易形成高熔点的钙铝黄石(2CaO·Al2O3·SiO2)和霞石(Na2O· Al2O3·2SiO2),恶化润滑作用。本发明中,为了保持较低的粘度,同时保证保护渣具有一定 的润滑性能,所以本发明中Al2O3含量控制在5~7%范围,优选为6.1~6.8%范围。 MgO:高速连铸时,MgO是保护渣的优选成分,可明显降低保护渣的粘度和熔点。MgO 的加入可使保护渣在保持相同粘度及软化点时,增加渣的流动性,提高渣耗。但其配入量过 高,反而会使保护渣的熔化性能变坏。本发明中,为了改善低碳低合金钢的流动性能,将MgO 含量控制在5~7%范围,优选为5.9~6.3%范围。 Na2O:属于网络外体氧化物,能破坏硅酸盐网络结构,在保护渣中起降低熔点和粘 度的作用,加入过高会形成霞石(Na2O·Al2O3·2SiO2),对结晶器润滑不利,应限制其加入 量。本发明中,为了保证保护渣具有一定的润滑性能,将Na2O含量控制在7~9%范围,优选 为7.8~8.6%范围。 CaF2:在<10%范围内增加含量对保护渣降低粘度的影响较大,再增加则作用不 明显。大量加入会形成枪晶石(3CaO·SiO2·CaF2)等高熔点物的析出,从而破坏熔渣的玻璃 性,使润滑条件恶化。另外,F-过高会侵蚀水口。本发明中,为了使保护渣具有适宜的粘度和 一定的玻璃性能,将CaF2含量控制在7~9%范围,优选为7.9~8.2%范围。 Li2O:是一种较强的助熔剂,即使加入渣中Li2O含量较低时,对熔化温度也有较大 的影响。Li2O的微量加入(Li2O<2%),对保护渣的玻璃化程度有所改善,析晶率降低,但其 4 CN 111604482 A 说 明 书 3/6 页 过量加入(Li2O>4%),反而会因大量的黄长石晶体析出而使其玻璃化程度大大降低。因 此,Li2O的适量加入可获得低熔点、低粘度、玻璃性好的保护渣,其适宜的量为Li2O<2%。本 发明中,为了适当降低保护渣的熔点和转折温度,提高保护渣的润滑性能,将Li2O含量控制 在1~2%范围,优选为1.1~1.3%范围。 C:在保护渣的理化性能中,碳质元素主要起到的是调节熔速的作用,目前制作保 护渣一般采用的复合配碳的方法,要想获得较高的熔速,配碳的含量一般控制在10%以内。 本发明中,为了使保护渣加入到结晶器中后具有足够厚度的液渣层,应进一步提高保护渣 的熔化速度,这样也能使其更好地流入到结晶器与铸坯之间的缝隙中,改善润滑性能,将C 含量控制在5~7%范围,优选为5.9~6.8%范围。 碱度:反映保护渣控制传热能力和吸收钢液中夹杂物能力的重要指标,同时也反 映了保护渣润滑性能的优劣。碱度过大,吸收夹杂物的能力也大,但它的析晶温度变大,不 利于传热和润滑性能;碱度过小,保护渣粘度较高,润滑效果降低。本发明中,为了使保护渣 的粘度在合理范围之内,同时保证保护渣具有一定的润滑和传热性能,将保护渣碱度控制 在1.1~1.3范围。 熔点:过低易造成卷渣、夹渣,形成铸坯缺陷,同时提高渣耗量,不利于铸坯成型; 过高容易凝固结晶,导致润滑性不好。本发明通过调节各成分含量,将保护渣熔点控制在 1050~1070℃之间,能保证保护渣在结晶器内形成足够厚度的液渣层,使铸坯在结晶器内 实现全程润滑。 粘度(1300℃):是保护渣的主要理化性能之一,代表着保护渣熔化时分子层间相 对粘滞力的大小,它同时也是表观保护渣润滑性能的重要参数之一。粘度太大时,保护渣流 动性变差,润滑效果降低;粘度太低会造成渣耗增加,铸坯难以成型,同时易造成卷渣、夹 渣。根据超高拉速、薄板坯的特殊工艺条件,本发明将低碳低合金钢保护渣的粘度控制在 0.03~0.05Pa·s,既能有效防止卷渣又能保证良好的润滑。 本发明的保护渣,为了能够适应超高拉速、薄板坯以及在电磁制动作用下的特殊 环境,根据试验情况,有必要在原有基础上提高液渣层厚度,改善保护渣的润滑性能,同时 降低熔点,增大熔化区间。因此如上所述,适当增加渣中Li2O的含量,降低熔点,提高保护渣 的润滑性能;同时减少配碳量,提高熔化速度,增加保护渣加入到结晶器中后的液渣层厚 度,从而满足在上述特殊情况下对保护渣性能的需求。 附图说明 此处所说明的附图用来提供对本发明的进一步理解,构成本发明的一部分,本发 明的示意性实施例及其说明用于解释本发明,并不构成对本发明的不当限定。在附图中: 图1A和图1B例示了本发明一实施例中结晶器的结构示意图; 图2A至图2D例示了应用了根据本发明实施例的保护渣的薄板坯与未应用根据本 发明实施例的保护渣的薄板坯的表面粘渣的对比图; 图3A至图3D例示了应用了根据本发明实施例的保护渣的薄板坯与未应用根据本 发明实施例的保护渣的薄板坯的表面裂纹的对比图; 图4A和图4B例示了应用了根据本发明实施例的保护渣的薄板坯与未应用根据本 发明实施例的保护渣的薄板坯的红热铸坯粘渣情况的对比照片。 5 CN 111604482 A 说 明 书 4/6 页