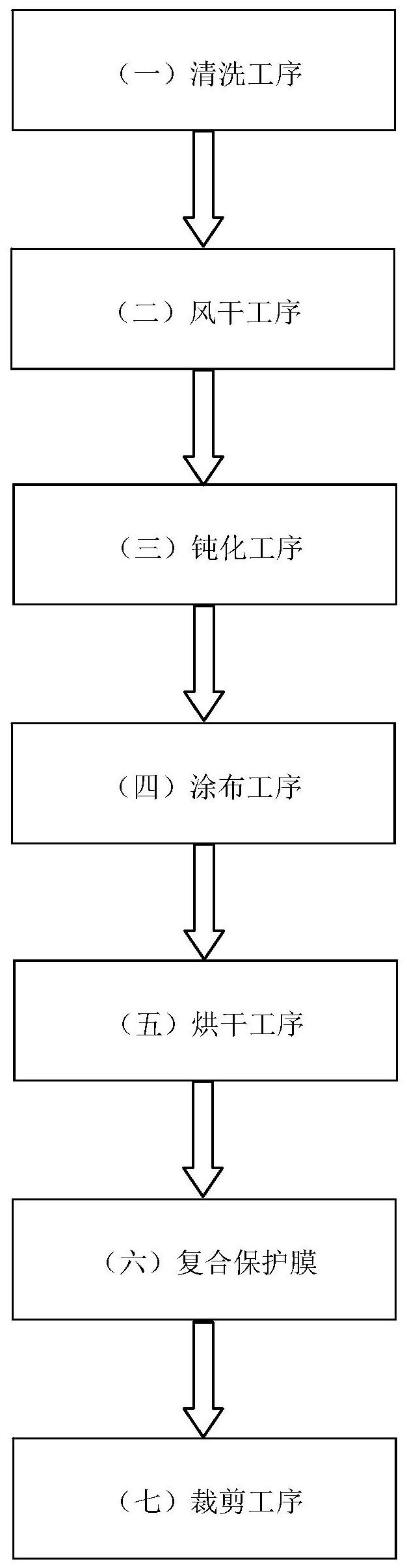
技术摘要:
本发明提供了板材制备工艺,其步骤为:(1)清洗工序;(2)风干工序;(3)钝化工序;(4)涂布工序;(5)烘干工序;(6)复合保护膜;(7)裁剪工序;其中步骤(5)烘干工序中采用红外固化炉对板材进行涂层固化。红外线不会对金属薄板进行加热,不会出现传统热风固化中金属薄板软化 全部
背景技术:
对于家电涂装行业而言,板材制备工艺中的烘干工艺对于最后成品板材的质量有 很大的影响。在现有板材制备工艺中,通常采用热风固化技术对涂层进行固化处理。现有由 于热风固化技术的限制,要想输送板材的速度达到60m/min的话,则热风固化炉的炉腔长度 一般不能小于45m,因此这种固化方式占用的空间大,且耗费巨大的热量,并且对金属薄板 采用此种固化烘干方式容易出现:金属薄板(金属板材厚度在1mm以下的称为薄板)在热风 固化的持续加温的状态下极易出现软化现象,从而金属薄板就会边部就会出现下垂的情 况,使得涂敷在金属薄板表面的涂层流向低温,导致涂层厚度不均匀,而涂层厚度不均匀会 直接导致金属薄板出现色差问题。
技术实现要素:
为了克服上述技术缺陷,本发明提供了板材制备工艺,通过此工艺制备出的板材 颜色均匀,并且节能环保。 为了解决上述问题,采用下述技术方案。 板材制备工艺,其步骤为: (1)清洗工序:去除板材上的油污及灰尘; (2)风干工序:将完成步骤(1)的板材进行风干,去除其上的水分; (3)钝化工序:对完成步骤(2)的板材进行涂敷钝化液; (4)涂布工序:对完成步骤(3)的板材进行涂敷涂料处理; (5)烘干工序:对完成步骤(4)的板材进行烘干处理; (6)复合保护膜:对完成步骤(5)的板材进行复合保护膜处理; (7)裁剪工序:将完成步骤(6)的板材裁剪成合适的尺寸; 其中,在步骤(5)烘干工序中采用红外固化炉对板材进行涂层固化。 进一步地,步骤(5)烘干工序为:将板材悬挂输送进入所述红外固化炉,所述红外 固化炉设有红外固化装置,所述红外固化装置产生波长为750nm~900nm的红外线对板材进 行涂层固化处理。 在所述板材烘干工艺中,板材需要悬挂通过所述红外固化炉,并且所述红外固化 炉中不能设有导轨,其主要原因为:板材在进入固化炉之前,板材上的涂层并未固化,如果 不悬挂通过所述红外固化炉,则会容易破坏涂层;如果固化炉中设有导轨也会很容易破坏 板材上未固化的涂层。 进一步地,输送板材的速率为40~65m/min,且板材通过所述红外固化炉的时间小 于12s。 进一步地,所述红外固化炉设有固化通道,所述固化通道为输送板材的通道;所述 3 CN 111589672 A 说 明 书 2/4 页 红外固化装置设置在所述固化通道的上下两侧。 由于板材的上下表面都涂敷有涂层,因此板材的上下表面都要进行烘干固化处 理,这样在所述固化通道的上下两侧都设有红外固化装置就实现对板材上下表面同时进行 烘干处理。 进一步地,板材与所述固化通道上侧的红外固化装置的距离为10~20cm,板材与 所述固化通道下侧的红外固化装置的距离为10~20cm。 将红外固化装置与板材之间的距离设置在此范围内,可以避免板材在通过固化炉 的过程中触碰到所述红外灯管将所述红外灯管碰碎;并且所述红外固化装置与板材之间的 距离在此范围内,可以在较低的能耗下保证板材上涂敷的涂层具有优秀的固化效果。 进一步地,板材上涂敷的涂层厚度为20~25微米,则所述红外固化装置的功率为 650~700KW。 进一步地,板材上涂敷的涂层厚度为10~15微米,则所述红外固化装置的功率为 300~350KW。 板材不同厚度的涂层对应的不同功率的红外固化装置,这样有有益于节约能源。 进一步地,所述红外固化装置包括若干红外灯管,所述红外灯管按照所述红外固 化炉的宽度方向均匀间隔排列。 进一步地,所述红外灯管为石英玻璃灯管。 石英玻璃具有优秀的耐高温性能,能在1100℃下长时间使用,短时间最高使用温 度可达到1450℃;石英玻璃在紫外线到红外线的整个光谱波段都具有优秀的透光性;石英 玻璃还具有优秀的耐腐蚀性能,除氢氟酸外,石英玻璃几乎不与其他酸类物质发生化学反 应,尤其是是在高温下的化学稳定性,是其他任何工程材料都无法比拟的。因此所述红外灯 管采用石英玻璃灯管可以保证所述红外灯管的使用稳定性,在所述板材烘干工艺中所述红 外灯管的使用稳定性是关键,因此保证了所述红外灯管的使用稳定性,从而保证了所述板 材烘干工艺的稳定性。 与现有技术相比,本发明中所述涂层板制备工艺具有以下有益效果:本发明所述 的涂层板制备工艺中的烘干工序采用红外固化炉对板材进行烘干固化处理,红外固化炉产 生红外线对板材上的涂层进行烘干固化处理,红外线具有良好的穿透性,能直接穿透涂层, 使得涂层中的树脂分子受热反应,释放溶剂,进而使得涂层获得固化;并且红外线不会对金 属薄板进行加热,不会出现传统热风固化中金属薄板软化的现象,进而避免了烘干固化后 的板材出现色差问题;传统涂层烘干工艺中所用的热风交换固化炉是需要预热的,将热风 交换固化炉的温度从常温加热至涂层所需固化的温度一般需要花费2~3小时,而本发明所 述的固化炉不需要预热,即开即用;因此本发明所述的固化炉比传统热风交换固化炉所需 的能耗小,本发明中所述的板材烘干工艺比传统的热风交换固化更为环保节能。 附图说明 下面结合附图对本发明的