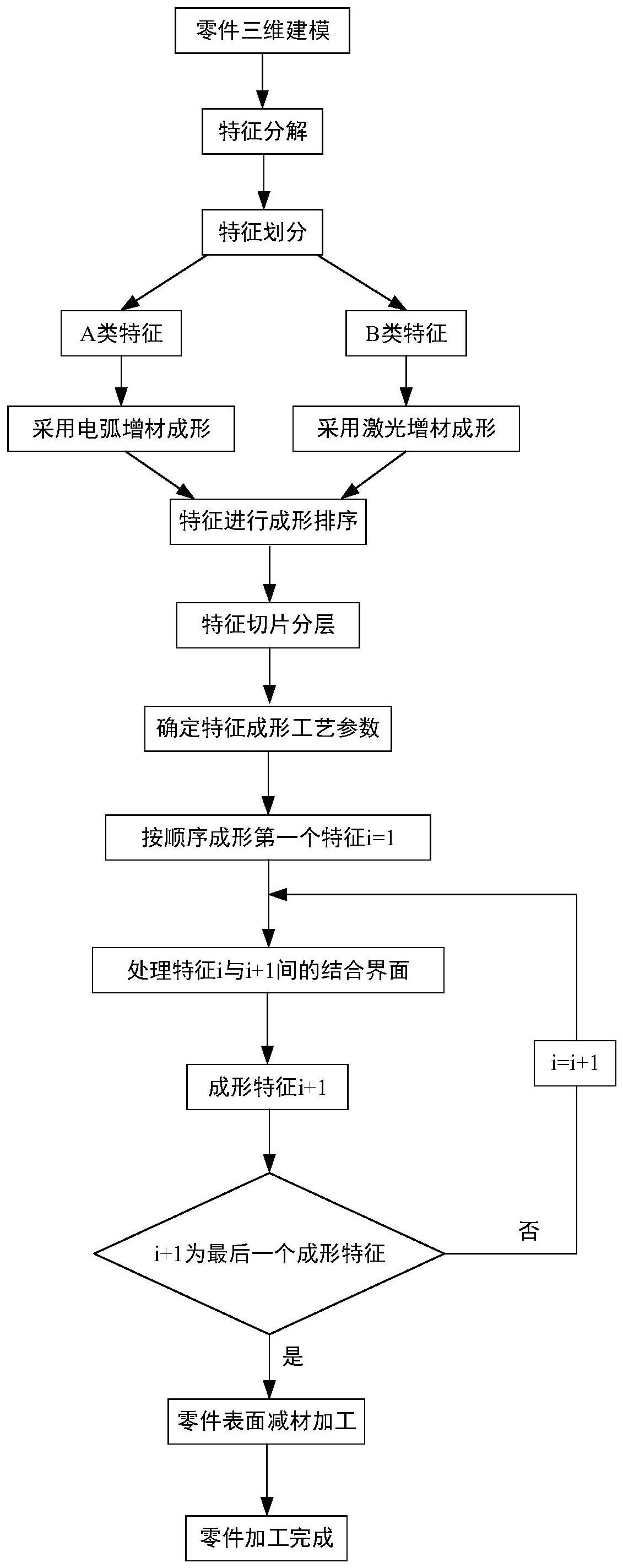
技术摘要:
本发明公开了一种采用电弧增材与激光增材复合的复杂金属零件成形方法,包括对零件实体进行三维建模,对三维实体模型进行几何特征分解,零件特征增材成形方法划分,确定各特征成形工艺参数,对各特征成形排序,针对各特征进行切片分层处理,根据特征成形排序及相邻特征 全部
背景技术:
目前航空航天领域中存在着许多结构复杂、精度要求高的零件,例如航空发动机 的机匣等。传统加工方法加工复杂零件时,主要采用锻件毛坯铣削加工的工艺方法,其工序 复杂,材料利用率低,切削余量大,往往需要数月的加工工时。而数月的加工周期也明显限 制了产能和设备利用率,成为航空航天领域部分复杂产品研制及制造的瓶颈问题。 增材制造能够实现毛坯近净成形,其缺陷控制优于铸件毛坯,材料利用率显著优 于锻件毛坯,增材制造的应用对减少加工余量以及缩短产品研发周期具有显著改善作用。 目前金属增材制造方法主要有激光增材和电弧增材,激光增材的优势主要在于成 形零件的精度高,电弧增材的技术优势主要在于成形效率高,丝材利用率高,且材料成本 低。然而两种工艺也存在各自的缺点,激光增材技术的缺点关键在于成形效率和粉末利用 率较低。而电弧增材技术的缺点在于成形精度较低,工艺稳定性控制难度大。 通过特征分解和工艺复合,利用电弧增材工艺实现高效成形,同时利用激光增材 工艺实现精细成形,可实现两种工艺的优势互补。而目前,实现电弧增材与激光增材的工艺 复合,其难点在于结合界面组织与力学性能较差,容易导致成形零件性能不达标,因此,优 化结合界面的组织与性能,成为了工艺复合的核心问题。
技术实现要素:
本发明的目的在于针对上述现有技术高精度及结构复杂零件的高效加工问题,提 供一种采用电弧增材与激光增材复合的复杂金属零件成形方法,有效结合电弧增材与激光 增材两种工艺方式的优点,并且改善结合界面的组织与力学性能,缩短生产周期,提高材料 利用率。 为了实现上述目的,本发明采用如下的技术方案: 一种采用电弧增材与激光增材复合的复杂金属零件成形方法,包括以下步骤: 步骤一、对零件实体进行三维建模,在零件实体表面法向向外增加后续切削加工 需要的余量,生成增材成形毛坯的三维实体模型,并对三维实体模型进行几何特征分解; 步骤二、对分解得到的几何特征逐个进行分析,选择特征的堆积方向,提取各特征 的名义尺寸,根据特征名义尺寸判断该特征是否适合采用电弧增材成形; 若该特征不适合采用电弧增材成形,则将其直接划分为B类特征;若该特征适合采 用电弧增材成形,分别估算采用电弧增材和激光增材的时间及成本,并据此将特征划分为A 类特征或B类特征,其中,A类特征采用电弧增材成形,B类特征采用激光增材成形; 步骤三、对分解得到的几何特征进行成形排序,依据各个几何特征所确定的增材 成形方法进行切片分层处理,并确定各个几何特征所选用的成形工艺参数; 4 CN 111545915 A 说 明 书 2/7 页 步骤四、相邻特征成形过程中,在前一特征成形后对结合界面进行加工处理,根据 前后特征的增材成形方法以及前一特征成形后的表面粗糙度确定结合界面处理方法,具体 如下: ①当相邻特征的增材成形方法相同时,若表面粗糙度≤界定值,直接成形后一特 征;若表面粗糙度>界定值,则首先对结合界面进行减材加工,使表面粗糙度≤界定值后, 然后继续成形后一特征;②当相邻特征的增材方法不同时,若表面粗糙度≤界定值,则对结 合界面直接进行激光重熔,并继续成形后一特征;若表面粗糙度>界定值,则首先对结合界 面进行减材加工,使表面粗糙度≤界定值,然后对结合界面进行激光重熔,之后继续成形后 一特征; 步骤五、根据特征成形排序及相邻特征间结合界面的处理方法,将各特征依次成 形,直至增材过程全部完成后,对零件表面进行减材加工,使零件尺寸和形状各精度达到设 计要求。 步骤二所述的特征名义尺寸包括:垂直于特征堆积方向的特征最大长度为名义长 度l,垂直于特征堆积方向的壁厚或宽度最小值为名义厚度d;电弧增材成形的起弧与熄弧 不稳定段长度为a,单熔道宽度为f,若名义长度l相对起弧与熄弧不稳定段长度a较短,或名 义厚度d与单熔道宽度f的比例较小,即当l≤αa或d≤βf时,则该特征不适合电弧增材成形, 认定该特征为B类特征,其中,α、β为比例系数,取值范围为:α≤2,β≤0.6。 步骤二所述估算采用电弧增材和激光增材的时间及成本的方法如下:当T电弧≤γ T激光且P电弧≤δP激光时,认定该特征为A类特征,否则,认定该特征为B类特征;其中,T电弧与T激光分 别为电弧增材和激光增材的时间,P电弧与P激光分别为电弧增材和激光增材的成本; γ、δ为比例系数,结合零件制造要求选定,取值范围为:γ≤1,δ≤1。 步骤四所述的激光重熔是指采用激光熔覆头在不送物料的情况下采用设定的光 斑直径和扫描速度对前一特征成形或加工表面进行激光扫描熔融;激光重熔采用的激光功 率1kW~2kW,激光光斑直径0.25mm~3mm,扫描速度3mm/s~30mm/s,表面粗糙度界定值≤ Ra6.3。 所述激光重熔采用的扫描方法包括轮廓偏置、分区往复扫描,激光重熔的扫描轨 迹覆盖前后特征的结合界面,前后特征扫描轨迹间的搭接率控制在5%~40%。 所述电弧增材的工艺种类包括:熔化极惰性气体保护焊MIG、熔化极活性气体保护 焊MAG、激光熔丝、非熔化极惰性气体保护焊TIG以及等离子弧焊PAW。 所述的减材加工方法根据相邻特征结合界面的处理要求包括车削、铣削以及磨 削。 相较于现有技术,本发明具有如下的有益效果: 采用增材制造相比于传统的加工方式,能够实现无模近净成形,成形的零件不仅 形状复杂,而且力学性能比锻造方法制造的零件高,大幅度缩短了生产周期,提高了材料利 用率。本发明将电弧增材和激光增材复合,零件中结构简单且尺寸较大的A类特征采用电弧 增材成形,而结构复杂且精细的B类特征采用激光增材完成。相比于单一的增材方法,本发 明结合了两者的优势,既保证了零件整体的成形性,又保证了精细、复杂结构的质量,大幅 提高了生产效率,降低了加工成本。同时,本发明采用激光重熔的方法,减少了异种增材工 艺结合界面区域的裂纹和气孔数量,同时也使组织分布更加均匀,提高了结合界面的力学 5 CN 111545915 A 说 明 书 3/7 页 性能。 附图说明 为了更清楚地说明本发明实施例中的技术方案,下面将对实施例描述中所需要使 用的附图作简单地介绍,显而易见地,下面描述中的附图是本发明的一些实施例,对于本领 域普通技术人员来讲,在不付出创造性劳动的前提下,还可以根据这些附图获得其他的附 图。 图1是基于电弧增材与激光增材复合工艺方法流程图; 图2是特征增材方法判断流程图; 图3是特征间结合界面处理方法判断流程图; 图4是激光重熔原理示意图; 图5是本发明实施例的零件示意图; 图6是本发明实施例的零件剖面图; 图7是本发明实施例的零件特征分解图; 图8是电弧增材成形等径回转a特征示意图; 图9是激光增材成形局部外凸特征示意图。