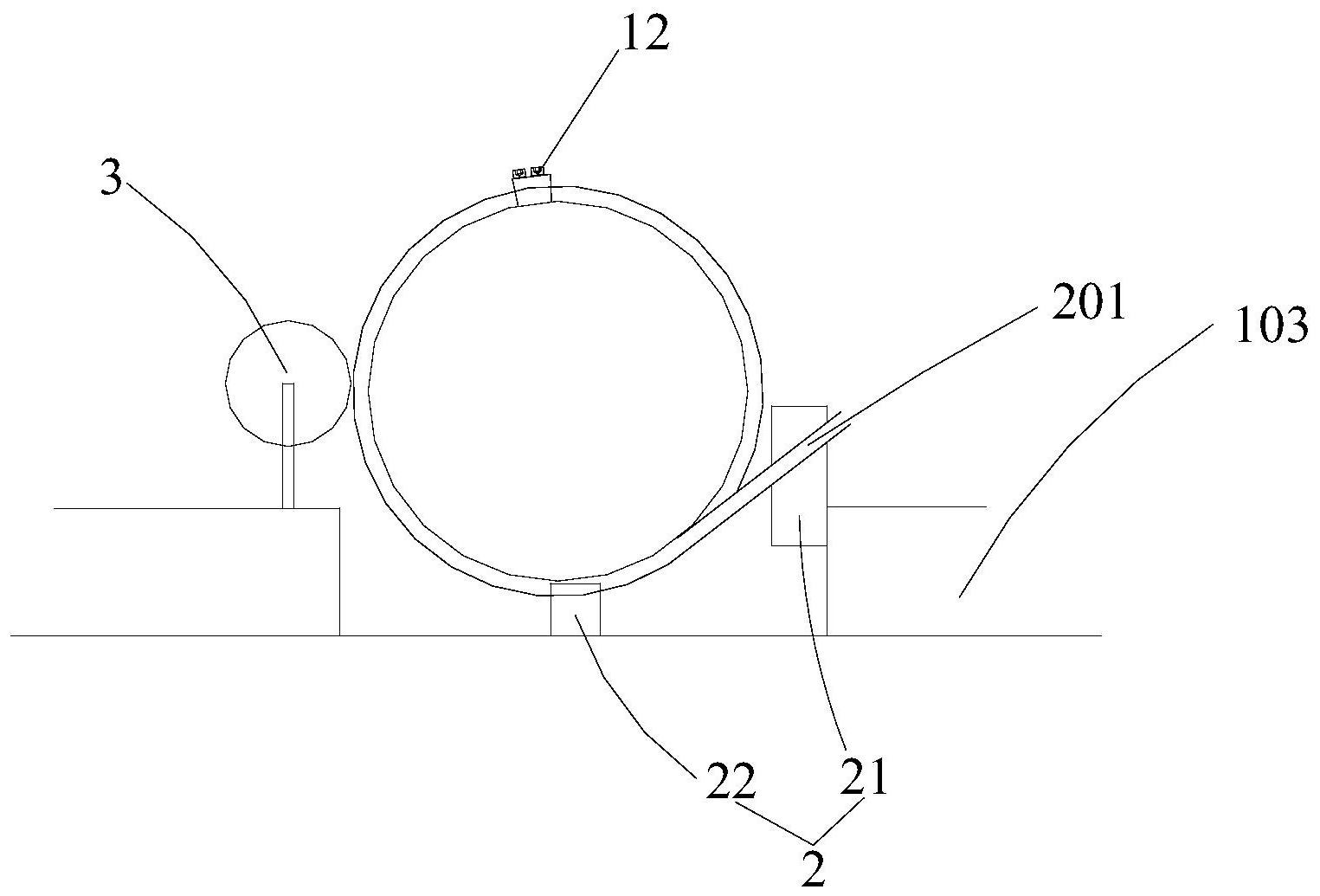
技术摘要:
本发明涉及热核聚变领域,特别涉及一种用于氢同位素气体分离的螺旋状分离柱,具体涉及一种螺旋状分离柱的制造方法,以及实现该方法的设备,该方法通过先在原料管内填充填料,再将原料管成型为螺旋状,实现了螺旋状分离柱填料均匀。该设备包括机床、螺旋胎具、管道夹持 全部
背景技术:
色谱法在一种在化工领域常用的分离方式。热循环吸附法是改进的气相色谱方 法,其原理是基于分离柱中材料对气相中不同组份的吸附差异来实现组份的分离,其核心 部件为分离柱,分离柱的规模决定了气相分离的规模。目前较多的分离柱都用于分析设备, 使用的分离柱较小,而目前已有的大型分离柱通常不具备复杂的形状,在需要极大柱径比 的场景下不适用。 热循环分离柱的长度影响了分离的效率。为了节约空间且便于安装,分离常制造 成螺旋状。将分离柱卷制成螺旋状是解决分离柱长径比的一个合理方法,但是较长的螺旋 分离柱会使得填料难度增加,难得到填充密度均匀的分离柱。尤其是在对填料密度敏感的 循环吸附的分离柱。
技术实现要素:
本发明的目的在于:针对现有技术存在的螺旋状分离柱内填料的填充密度难于控 制均匀的问题,提供一种螺旋状分离柱的制造方法。该方法通过先填料再成型的方式,实现 了填料的均匀填充。 为了实现上述目的,本发明采用的技术方案为: 一种螺旋状分离柱的制造方法,先在原料管内填充填料,再将原料管成型为螺旋状。 通过现在直型或者接近直型的原料管内填充填料,更容易实现分离柱内空间填料 的满填,保证填料的均匀。然后再成型为螺旋状,实现螺旋状分离柱满足填充密实度的要 求。 作为本发明的优选方案,所述原料管由若干段原料管头尾连接而成;先将前段原 料管填充填料,成型为螺旋状,再将后段原料管连接前段原料管,然后将后段原料管填充填 料,并成型为螺旋状;依序将若干根原料管依次连接、填料、成型,得到所述螺旋状分离柱。 后段原料管是相对于之前已经填料并成型的原料管而言的,且前后原料管和后段 原料管是相邻的连接在一起的原料管。例如第一段原料管为前段,第二端原料管为后段;当 第二段原料管为前段时,第三段原料管为后段,依次类推。 即将第一段原料管填充填料,然后成型为螺旋状;将第二段原料管头端连接到第 一段的尾端,向第二段原料管内填充填料,然后成型为螺旋状;依次将若干段原料管连接、 填充填料和成型,得到所述螺旋状分离柱。 在螺旋状分离柱需要的长度较长,例如在几十米的情况下,采用多段原料管分步 骤连接、填充、成型的方案,其中第一段原料管的头端不需要连接,每段填充的长度较短,更 易保证每段的填料均匀的满填,最终填料状态良好的形成螺旋状分离柱。 3 CN 111569657 A 说 明 书 2/5 页 作为本发明的优选方案,在向后段原料管内填充填料前,检查后段原料管和前段 原料管之间的密封性。 在第一段原料管的前端设置排气阀门,将后段原料管焊接到前段原料管后,将排 气阀门关闭,在后段原料管的尾端注入惰性气体保持一定压力进行密封性检测。 作为本发明的优选方案,向每段原料管填充填料后,通入惰性气体将原料管内的 填料压实。 在第一段原料管的前端设置排气阀门,在完成后段原料管道填料后,将排气阀门 打开,在后段原料管的尾端注入惰性气体,采用高压惰性气体进行吹扫,将原料管内的填料 进一步压实。 作为本发明的优选方案,每段原料管成型时,该段原料管的尾端留有一段未成型 段。 在前段原料管的尾端留有一段未成形段,未成型段未缠绕在模具上,在将后段原 料管的头端连接到所述未成型段时,连接更为方便。在最后一段原料管成型时,可不保留尾 端的连接段。 作为本发明的优选方案,在每一段原料管成型后,将每一圈相邻的分离柱连接。 每一段原料管可以支撑若干圈分离柱,在每一段原料管成型后,将相邻的分离柱 之间通过焊接的方式焊接到一起,保证螺旋状分离柱不易发生变形。 本发明还提供了一种实现上述方法的设备,该设备包括机床、螺旋胎具、管道夹持 器; 所述机床连接所述螺旋胎具,并用于带动所述螺旋胎具旋转; 所述螺旋胎具与所述螺旋状分离柱匹配;所述螺旋胎具上设有固定装置,所述固定装 置用于固定所述原料管的头端; 所述管道夹持器位于所述螺旋胎具的侧面,用于定位未成形的原料管。 所述机床是基础的设备,其他部件固定在机床上,实现各部件的功能。机床的结构 为常规机床的结构,只要能满足螺旋胎具的直径和高度需求即可。螺旋胎具为圆柱形的模 具,其尺寸根据螺旋状分离柱的尺寸设计。所述固定装置为沉孔,沉孔的直径与原料管的外 径匹配。所述管道夹持器位于所述螺旋胎具的侧面,是指管道夹持器位于圆柱形的侧面。所 述管道夹持器安装在机床上,保持原料管进入螺旋胎具的角度,避免管道的划伤,在原料管 成型过程中,螺旋胎具和管道夹持器沿螺旋胎具的轴向相对移动。 作为本发明的优选方案,该设备还包括止回轮,所述止回轮位于所述螺旋胎具的 侧面,用于限制加工成型的原料管回弹。通过设置止回轮,在螺旋胎具转动的同时,止回轮 跟随转动,压迫成型的原料管,避免原料管回弹,使得整个螺旋状分离柱形状精度更高,在 整个成型过程中分离柱均与螺旋胎具保持良好的贴合状态。 作为本发明的优选方案,所述螺旋胎具上设有螺旋沟槽,所述螺旋沟槽与所述螺 旋状分离柱匹配。 原料管能够沿着沟槽成型,并且保证形状,使得螺旋形状更为均匀一致。 作为本发明的优选方案,所述止回轮上设有止回凹槽,所述止回凹槽与所述螺旋 钩槽配合后,形成与所述原料管匹配的穿孔。 作为本发明的优选方案,所述螺旋胎具由多瓣模具拼接而成。 4 CN 111569657 A 说 明 书 3/5 页 将螺旋胎具设置为多瓣模具拼接,在分离柱制作完成后,方便螺旋胎具的取出,完 成脱模。 作为本发明的优选方案,所述螺旋胎具由圆柱筒沿轴向切割为若干块模具,所述 若干块模具,所述若干块模具的两端分别连接圆形端头组装为中空的圆柱形。优选模具为 三块。切割线的方向优选平行于圆柱筒的轴线。 通过上述设置,在分离柱制作完成后,将两个端口与若干块模具分离,从螺旋胎具 内侧将各个模具取出,更易实现脱模操作。 综上所述,由于采用了上述技术方案,本发明的有益效果是: 1、本发明的螺旋状分离柱的制造方法,通过先在原料管内填充填料再成型的方式,实 现了螺旋状分离柱满足填充密实度的要求。 2、本发明的螺旋状分离柱的制造方法,通过将若干段原料管依次连接、填料、成型 的方式,实现了较长的分离柱的制造,并保证了最终填料状态良好。 3、本发明的螺旋状分离柱的制造方法,通过在每段原料管填充填料后,使用高压 气体进行吹扫压实,使得原料管内的填料更为密实。 4、本发明的螺旋状分离柱的制造方法,通过在每一段原料管成型后,将每一圈相 邻的分离柱连接。使已成型的部分连为一体,避免了螺旋状分离柱发生变形。 5、本发明的实现上述制造方法的设备,通过机床、螺旋胎具、管道夹持器和止回轮 的合理设置,将原料管绕在螺旋胎具上,通过管道夹持器控制原料管和螺旋胎具的相对位 置,通过止回轮压迫已成型的原料管,避免发生形变,更好的实现了上述制造方法。 6、本发明的实现上述制造方法的设备,通过在螺旋胎具和止回轮上设置与原料管 匹配的沟槽和凹槽,使得螺旋形状更为均匀一致。 7、本发明的实现上述制造方法的设备,通过将螺旋胎具设置为多瓣模具拼接的形 式,方便在螺旋状分离柱制作完成后,方便的完成脱模。 附图说明 图1是本发明的实现螺旋状分离柱制造方法的设备结构示意图。 图2是本发明的实现螺旋状分离柱制造方法的设备结构示意图。 图3是本发明实施例3中螺旋状分离柱成型后未脱模的示意图。 图标:100-机床;101-机床花盘;102-机床尾座;103-机床刀架;201-无缝钢管; 202-焊点;1-螺旋胎具;11-螺旋沟槽;12-固定装置;2-管道夹持器;21-第一管道夹持器; 22-第二管道夹持器;3-止回轮。