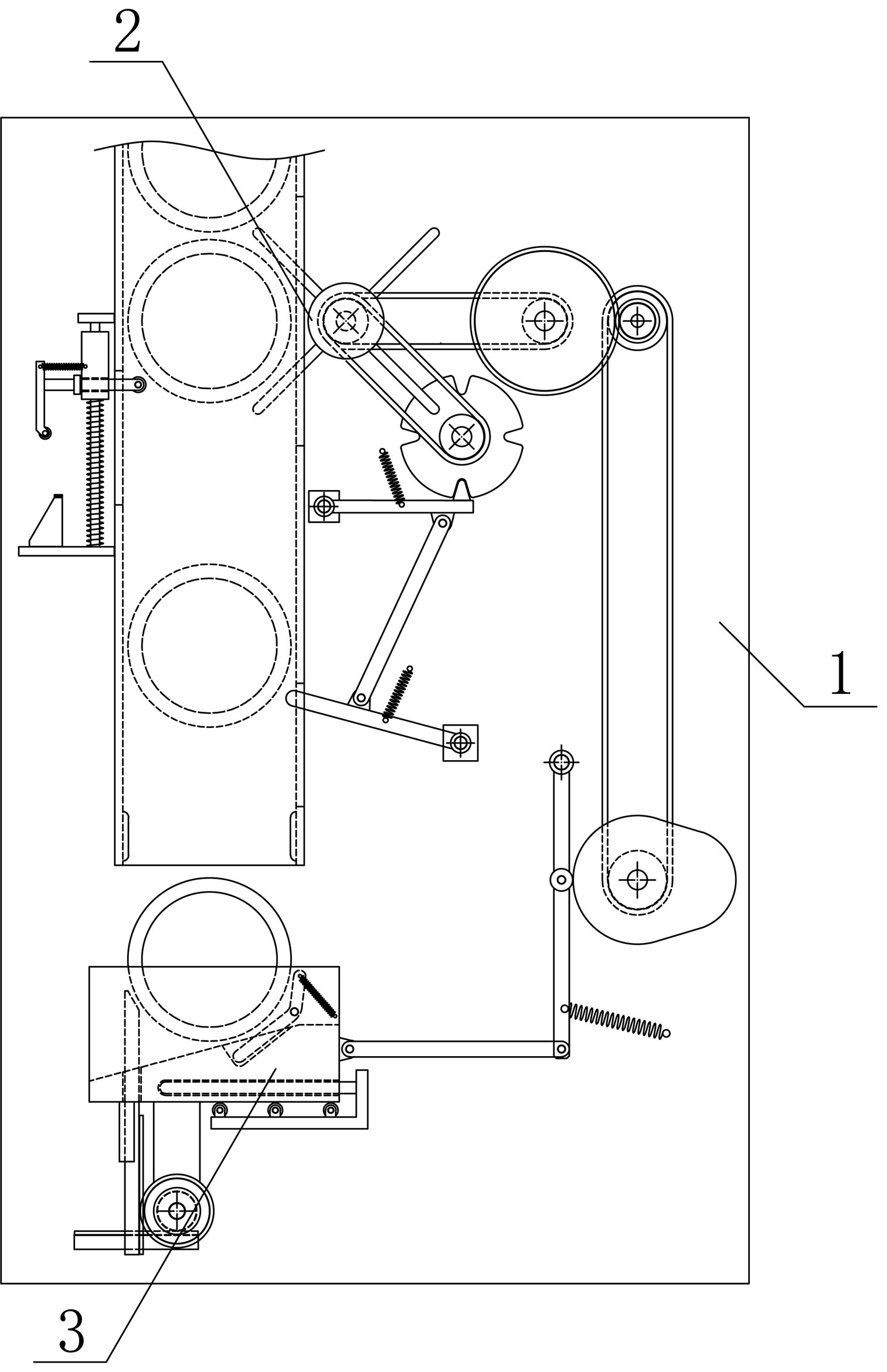
技术摘要:
本发明公开了一种金属圆管连续导送上料装置,属于管件传送机械设备领域。该发明的圆管落料机构和圆管移送机构从上至下依次竖直设置于圆管传送支架,圆管落料导管上方外侧的落料转动圆盘和转动定位圆盘之间采用落料连接链条传动连接,往复定位摆杆设置于转动定位圆盘下 全部
背景技术:
金属圆管是指采用金属材料加工而成,两端开口并具有中空同心圆断面的柱形结 构管材,可用于管道、热工设备、机械工业和化学工业等领域,金属圆管按加工工艺的不同 可以分为无缝圆管和焊接圆管,金属圆管除了按照加工工艺进行分类,还可以将金属圆管 根据用途、连接方式和材料分别进行分类。金属圆管的规格种类很多,不同领域使用的金属 圆管需要使用不同材质的金属材质,金属材质的质量直接决定了圆管的质量,金属圆管在 建筑工程和机械设备内有广泛的应用,在机械系统中金属圆管起到连接、控制、变向、分流、 密封和支撑等作用。金属圆管在生产加工过程中,需要将经过前道工序生产加工的金属圆 管依次逐个进行传送导料使能进行后道工序的加工,现有的金属圆管传送装置结构复杂且 操作麻烦,难以实现金属圆管逐个平稳的依次导料传送,现有金属圆管在导料传送过程中, 难以在金属圆管的导料传送过程中利用金属圆管自身的重力实现金属圆管逐个自动落料 传送,金属圆管的导料传送主要采用机械取料装置将金属圆管进行取料放置,机械取料装 置主要采用驱动电机和液压缸进行驱动使用,导致金属圆管导料传送能耗较高,并且设备 较易产生故障,使用维修成本大,使得不能将金属圆管连续高频的取料移送,现有金属圆管 上料加工也常采用人工手动操作实现,导致操作工人劳动强度大,金属圆管导料上料自动 化程度低,难以满足金属圆管连续规模化的生产加工,降低金属圆管传送加工的效率和质 量,不能满足加工使用的需要。
技术实现要素:
本发明所要解决的技术问题是克服现有技术中所存在的上述不足,而提供一种结 构设计合理,可以平稳高效的将金属圆管连续顺畅的逐个导送上料,提高金属圆管传送自 动化程度,满足加工使用需要的金属圆管连续导送上料装置。 为了解决上述技术问题,本发明所采用的技术方案是:一种金属圆管连续导送上 料装置,其特征在于:所述金属圆管连续导送上料装置包括圆管传送支架、圆管落料机构和 圆管移送机构,所述圆管落料机构和圆管移送机构从上至下依次竖直设置于圆管传送支 架,所述圆管落料机构包括圆管落料导管、落料转动圆盘、转动定位圆盘、往复定位摆杆、落 料摆动承杆、同步牵拉连杆和承管落料机构,所述圆管落料导管竖直固定设置于圆管传送 支架上侧,圆管落料导管为扁平状方形结构,所述圆管落料导管上方外侧的圆管传送支架 上竖直转动连接有落料转动圆盘,落料转动圆盘外侧沿落料转动圆盘的径向均匀固定设置 有四根落料转动挡杆,圆管落料导管沿落料转动圆盘侧设置有与落料转动挡杆相适配的挡 杆摆动导槽,所述转动定位圆盘竖直转动连接于落料转动圆盘下侧的圆管传送支架,转动 定位圆盘外侧沿转动定位圆盘的径向均匀设置有四个落管定位卡槽,所述落料转动圆盘一 5 CN 111573245 A 说 明 书 2/11 页 侧同轴竖直固定设置有落料主链轮,转动定位圆盘一侧同轴竖直固定设置有落料辅链轮, 落料主链轮和落料辅链轮之间采用落料连接链条传动连接,落料主链轮和落料辅链轮的尺 寸规格相同,所述往复定位摆杆设置于转动定位圆盘下侧的圆管传送支架,往复定位摆杆 一侧的圆管传送支架上固定设置有摆杆连接支座,往复定位摆杆端部铰接连接于摆杆连接 支座,往复定位摆杆沿转动定位圆盘端设置有落管定位卡块,落管定位卡块与落管定位卡 槽的尺寸结构相适配,往复定位摆杆中部上侧与圆管传送支架之间设置有定位牵拉弹簧, 所述落料摆动承杆设置于往复定位摆杆下侧的圆管传送支架,落料摆动承杆一侧的圆管传 送支架上固定设置有挡杆连接支座,落料摆动承杆端部铰接连接于挡杆连接支座,落料摆 动承杆沿圆管落料导管侧端部设置于圆管落料导管内,圆管落料导管沿落料摆动承杆侧设 置有与落料摆动承杆相适配的承杆往复导槽,落料摆动承杆中部上侧与圆管传送支架之间 设置有承杆复位拉簧,所述同步牵拉连杆设置于往复定位摆杆和落料摆动承杆之间,同步 牵拉连杆上下两侧端部分别铰接连接于往复定位摆杆下侧和落料摆杆承杆上侧,所述承管 落料机构竖直设置于圆管落料导管一侧,承管落料机构和落料转动圆盘分别设置于圆管落 料导管两侧,所述承管落料机构包括承管落料支架、往复升降导杆、承管往复导板、圆管落 料承杆和推杆平移楔板,所述承管落料支架竖直固定设置于圆管落料导管一侧,承管落料 支架两侧分别竖直固定设置有往复升降导杆,所述承管往复导板沿竖直方向滑动设置于往 复升降导杆,承管往复导板下侧的往复升降导杆上套装设置有复位提升弹簧,所述圆管落 料承杆沿水平方向滑动设置于承管往复导板,圆管落料承杆沿圆管落料导管侧端部设置于 圆管落料导管内,圆管落料导管上竖直设置有与圆管落料承杆相适配的承杆升降导槽,所 述圆管落料承杆外侧端部竖直固定设置有承杆平移推杆,承杆平移推杆与承管往复导板之 间水平设置有承杆复位拉簧,承管往复导板沿承杆平移推杆侧的圆管落料承杆上固定设置 有承杆复位挡板,承杆平移推杆下端转动连接有承杆平推导轮,所述推杆平移楔板竖直固 定设置于承管落料支架下侧,推杆平移楔板设置于承杆平移推杆下侧,所述圆管移送机构 包括推杆转动凸轮、承板平移摆杆、圆管移送承板和平移限位支架,所述落料转动圆盘一侧 同轴竖直固定设置有第一连接链轮,第一连接链轮和落料主链轮沿水平方向从内到外依次 竖直设置,所述落料转动圆盘一侧的圆管传送支架上沿水平方向依次竖直转动连接有移管 主齿轮和移管辅齿轮,移管主齿轮和移管辅齿轮相互啮合连接,移管主齿轮直径是移管辅 齿轮直径的四倍,移管主齿轮一侧同轴竖直固定设置有第二连接链轮,第一连接链轮和第 二连接链轮之间采用第一连接链条传动连接,第一连接链轮和第二连接链轮的尺寸规格相 同,移管辅齿轮一侧同轴竖直固定设置有第三连接链轮,所述推杆转动凸轮竖直转动连接 于圆管传送支架下侧,推杆转动凸轮一侧同轴竖直固定设置有第四连接链轮,第三连接链 轮和第四连接链轮之间采用第二连接链条传动连接,第三连接链轮和第四连接链轮的尺寸 规格相同,所述承板平移摆杆设置于推杆转动凸轮一侧的圆管传送支架,承板平移摆杆上 端铰接连接于圆管传送支架,承板平移摆杆下端与圆管传送支架之间设置有摆杆复位拉 簧,承板平移摆杆中部压紧贴合设置于推杆转动凸轮外侧表面,所述平移限位支架水平固 定设置于圆管落料导管下侧的圆管传送支架,圆管移送承板水平设置于平移限位支架上 侧,平移限位支架上方两侧分别水平固定设置有平移限位导杆,圆管移送承板两侧分别水 平设置有与平移限位导杆相适配的平移往复通道,圆管移送承板沿水平方向滑动设置于平 移限位导杆,所述承板平移摆杆与圆管移送承板之间设置有推板平移连杆,推板平移连杆 6 CN 111573245 A 说 明 书 3/11 页 两端分别铰接连接于承板平移摆杆下侧端部和圆管移送承板端部,所述圆管移送承板上侧 竖直设置有圆管放置通道,圆管放置通道下侧的圆管移送承板上设置有圆管滚落斜面,所 述圆管滚落斜面低端的圆管移送承板上竖直滑动设置有升降挡管杆,圆管移送承板上竖直 设置有与升降挡管杆相适配的挡杆升降通道,所述圆管移送承板下侧竖直固定设置有齿轮 转动支架,齿轮转动支架相邻设置于升降挡管杆一侧,所述齿轮转动支架下侧从内到外依 次竖直同轴设置有第一连接齿轮和第二连接齿轮,第一连接齿轮下侧的圆管传送支架上水 平固定设置有与第一连接齿轮啮合连接的第一连接齿板,升降挡管杆下侧竖直贴合设置有 与第二连接齿轮啮合连接的第二连接齿板。 进一步地,所述圆管落料机构的落料摆动承杆沿圆管落料导管侧端部为表面光滑 的半球形结构。 进一步地,所述落料定位卡槽为三角形结构,落管定位卡槽外端两侧与转动定位 圆盘外沿采用弧形边过渡连接,往复定位摆杆端部的落管定位卡块为与落料定位卡槽尺寸 结构相适配的三角形结构,落料定位卡块端部为圆弧形结构。 进一步地,所述承管落料机构的圆管落料承杆沿圆管落料导管侧端部转动连接有 承管落料导轮。 进一步地,所述承管落料机构的推杆平移楔板上侧表面贴合固定设置有承杆缓冲 胶层。 进一步地,所述圆管移送机构的承板平移摆杆中部转动连接有摆杆往复滚轮。 进一步地,所述圆管移送机构的圆管移送承板上侧设置有承管缓冲转板,承管缓 冲转板中部铰接连接于圆管移送承板,承管缓冲转板上端与圆管移送承板之间设置有转板 复位拉簧,圆管滚落斜面上设置有与承管缓冲转板相适配的转板放置卡槽。 进一步地,所述圆管移送承板下侧的平移限位支架上沿水平方向均匀转动连接有 多个平移支承滚轮。 进一步地,所述圆管移送机构的升降挡管杆上端表面设置有承管斜面,圆管移送 承板下侧竖直固定设置有与升降挡管杆相适配的挡杆升降支架。 进一步地,所述圆管落料导管下端内部两侧分别贴合固定设置有落管阻尼胶层。 本发明与现有技术相比,具有以下优点和效果:本发明结构设计合理,通过圆管落 料机构和圆管移送机构从上至下依次竖直设置于圆管传送支架,利用圆管落料机构使能实 现金属圆管利用自身重力平稳高效的逐个落料传送,利用圆管移送机构和圆管落料机构的 连动作用,使得圆管移送机构能够在金属圆管逐个落料传送过程中自动平稳的往复移送, 使能实现金属圆管便捷顺畅的平移上料,提高金属圆管传送自动化程度,通过圆管落料导 管竖直固定设置于圆管传送支架上侧,落料转动圆盘外侧沿落料转动圆盘的径向均匀固定 设置有四根落料转动挡杆,转动定位圆盘外侧沿转动定位圆盘的径向均匀设置有四个落管 定位卡槽,落料转动圆盘一侧的落料主链轮和转动定位圆盘一侧的落料辅链轮之间采用落 料连接链条传动连接,往复定位摆杆沿转动定位圆盘端设置有落管定位卡块,往复定位摆 杆中部上侧与圆管传送支架之间设置有定位牵拉弹簧,落料摆动承杆沿圆管落料导管侧端 部设置于圆管落料导管内,落料摆动承杆中部上侧与圆管传送支架之间设置有承杆复位拉 簧,同步牵拉连杆设置于往复定位摆杆和落料摆动承杆之间,利用上述结构,圆管落料导管 内的金属圆管在沿竖直方向平稳下落过程中能够推动落料摆动承杆进行逆时针摆动,当落 7 CN 111573245 A 说 明 书 4/11 页 料摆动承杆在进行逆时针摆动时,落料摆动承杆能够利用同步牵拉连杆带动往复定位摆杆 同步进行顺时针摆动,使得往复定位摆杆的落管定位卡块与转动定位圆盘的落料定位卡槽 脱离连接,利用圆管落料导管上侧的依次堆叠放置的多个金属圆管利用自身重力沿竖直方 向推动落料转动圆盘外侧的落料转动挡杆,使得落料转动圆盘能够进行逆时针转动,落料 转动圆盘能够利用落料连接链条带动转动定位圆盘同步同向进行转动,当圆管落料导管下 侧的金属圆管与落料摆动承杆脱离接触后,落料摆动承杆能够在承杆复位拉簧的作用下迅 速进行顺时针摆动复位,往复定位摆杆能够与落料摆动承杆同步进行复位摆动,使得往复 定位摆杆端部的落料定位卡块与转动定位圆盘外沿紧密压紧接触,当转动定位圆盘在落料 转动圆盘的带动下进行垂直角度的转动后,往复定位摆杆端部的落料定位卡块能够准确顺 畅的与转动定位圆盘的落料定位卡槽配合连接,使得转动定位圆盘能够迅速停止转动,确 保落料转动圆盘在进行垂直角度的转动后能够与转动定位圆盘同步停止转动,实现金属圆 管依次逐个平稳落料导送,利用落料摆动承杆在金属圆管的重力推动下进行逆时针摆动, 使得落料摆动承杆还能够实现对金属圆管落料导送的降速缓冲,确保金属圆管能够平稳的 从圆管落料导管下侧端部滑出,通过承管落料机构和落料转动圆盘分别设置于圆管落料导 管两侧,承管往复导板下侧的往复升降导杆上套装设置有复位提升弹簧,圆管落料承杆沿 水平方向滑动设置于承管往复导板,圆管落料承杆沿圆管落料导管侧端部设置于圆管落料 导管内,圆管落料承杆外侧端部的承杆平移推杆与承管往复导板之间水平设置有承杆复位 拉簧,承管往复导板沿承杆平移推杆侧的圆管落料承杆上固定设置有承杆复位挡板,承杆 平移推杆下端转动连接有承杆平推导轮,推杆平移楔板竖直固定设置于承管落料支架下 侧,利用圆管落料承杆对金属圆管在下落过程中进行承托,使得圆管落料导管内的金属圆 管能够平稳顺畅的竖直下落,在承管往复导板沿竖直方向滑落至往复升降导杆下侧时,承 杆平移推杆下端的承杆平推导轮沿推杆平移楔板表面滚动,使得承杆平移推杆能够带动圆 管落料承杆沿水平方向进行平移运动,实现圆管落料承杆端部与金属圆管脱离接触,在金 属圆管利用自身重力沿竖直方向继续下落后,承管往复导板能够在复位提升弹簧的作用下 迅速提升复位,圆管落料承杆能够在承杆复位拉簧的作用下迅速平移复位,使能继续进行 金属圆管的承托落料,实现金属圆管高效平稳的落料导送,利用圆管落料承杆沿圆管落料 导管侧端部转动连接有承管落料导轮,使得圆管落料承杆在承杆平移推杆的带动下进行平 移运动时,圆管落料承杆端部的承管落料导轮能够沿金属圆管外侧表面顺畅滚动,既能实 现圆管落料承杆便捷顺畅的进行平移运动,也能确保金属圆管平稳高效的落料传送,利用 推杆平移楔板上侧表面贴合固定设置有承杆缓冲胶层,使得在对金属圆管进行承托落料的 过程中,利用承杆缓冲胶层使能实现圆管落料承杆与推杆平移楔板的平缓接触,利用上述 机构,使得金属圆管的依次逐个落料导送过程能够完全利用金属圆管自身重力实现,不需 要外接驱动机构,实现金属圆管高效节能的落料导送,通过落料转动圆盘一侧的圆管传送 支架上沿水平方向依次竖直转动连接有移管主齿轮和移管辅齿轮,落料转动圆盘一侧的第 一连接链轮和移管主齿轮一侧的第二连接链轮之间采用第一连接链条传动连接,使得在圆 管落料导管内的金属圆管推动落料转动圆盘进行逆时针转动时,落料转动圆盘能够带动移 管主齿轮同步进行转动,利用移管主齿轮和移管辅齿轮相互啮合连接,使得移管辅齿轮能 够与移管主齿轮同步相向进行转动,利用移管主齿轮直径是移管辅齿轮直径的四倍,使得 移管主齿轮在落料转动圆盘的带动下进行垂直角度转动时,移管辅齿轮能够同步转动一 8 CN 111573245 A 说 明 书 5/11 页 周,通过推杆转动凸轮竖直转动连接于圆管传送支架下侧,移管辅齿轮一侧的第三连接链 轮和推杆转动凸轮一侧的第四连接链轮之间采用第二连接链条传动连接,推杆转动凸轮一 侧承板平移摆杆上端铰接连接于圆管传送支架,承板平移摆杆下端与圆管传送支架之间设 置有摆杆复位拉簧,承板平移摆杆中部压紧贴合设置于推杆转动凸轮外侧表面,利用移管 辅齿轮能够带动推杆转动凸轮同步同向进行转动,推杆转动凸轮在转动过程中能够推动承 板平移摆杆进行摆动,承板平移摆杆能够在推杆转动凸轮和摆杆复位拉簧的作用下连续往 复进行摆动,利用承板平移摆杆中部转动连接有摆杆往复滚轮,使得推杆转动凸轮在推动 承板平移摆杆进行往复摆动的过程中,承板平移摆杆中部的摆杆往复滚轮能够沿推杆转动 凸轮外侧平稳顺畅的滚动,实现推杆转动凸轮高效顺畅的推动承板平移摆杆往复摆动,通 过平移限位支架水平固定设置于圆管落料导管下侧的圆管传送支架,圆管移送承板沿水平 方向滑动设置于平移限位支架,承板平移摆杆与圆管移送承板之间设置有推板平移连杆, 使得承板平移摆杆在连续往复摆动过程中能够利用推板平移连杆带动圆管移送承板连续 往复进行平移运动,利用平移限位支架上沿水平方向均匀转动连接有多个平移支承滚轮, 使得圆管移送承板在往复运动过程中能够利用平移支承滚轮实现平稳有效的支承,避免圆 管移送承板在承托放置金属圆管后产生偏移歪斜,通过圆管移送承板的圆管放置通道下侧 的圆管移送承板上设置有圆管滚落斜面,圆管滚落斜面低端的圆管移送承板上竖直滑动设 置有升降挡管杆,圆管移送承板下侧的齿轮转动支架上从内到外依次竖直同轴设置有第一 连接齿轮和第二连接齿轮,第一连接齿轮下侧的圆管传送支架上水平固定设置有与第一连 接齿轮啮合连接的第一连接齿板,升降挡管杆下侧竖直贴合设置有与第二连接齿轮啮合连 接的第二连接齿板,利用圆管移送承板上的圆管放置通道,使得沿着圆管落料导管滑落的 金属圆管能够竖直准确的落至圆管放置通道内,当圆管移送承板在承板平移摆杆的推动作 用下进行平移运动时,第一连接齿轮在第一连接齿板的作用下逆时针转动,第二连接齿轮 与第一连接齿轮同步同向进行转动,第二连接齿轮能够带动升降挡管杆沿竖直方向向下运 动,使得圆管移送承板在承板平移摆杆的带动下平移至端部时,升降挡管杆能够向下运动 至失去对金属圆管的承托阻挡,使得金属圆管能够利用自身重力沿圆管移送承板的圆管滚 落斜面高效顺畅的滚落下滑,确保金属圆管能够便捷准确的移送上料,在承板平移摆杆带 动圆管移送承板进行复位平移时,升降挡管杆能够沿竖直方向平稳准确的向上运动,实现 金属圆管连续平稳的平移运送,利用圆管移送机构的升降挡管杆上端表面设置有承管斜 面,圆管移送承板下侧竖直固定设置有与升降挡管杆相适配的挡杆升降支架,利用升降挡 管杆端部的承管斜面使能与金属圆管表面实现有效的承托接触,利用挡杆升降支架能够确 保升降挡管杆沿竖直方向平稳准确的升降运动,通过圆管移送承板上侧的承管缓冲转板中 部铰接连接于圆管移送承板,承管缓冲转板上端与圆管移送承板之间设置有转板复位拉 簧,圆管滚落斜面上设置有与承管缓冲转板相适配的转板放置卡槽,使得圆管落料导管内 的金属圆管在落料至圆管移送承板上侧时,利用承管缓冲转板对金属圆管的承托缓冲作 用,使能实现金属圆管高效平稳的落至圆管移送承板上侧,避免金属圆管在下落过程中与 圆管移送承板产生剧烈撞击而影响圆管移送机构连续长周期平稳使用,利用上述机构,使 得金属圆管的依次水平移送能够利用金属圆管在自身重力作用下逐个落料传送同步带动 实现,不需要外接驱动机构,实现金属圆管高效节能的平移运送,通过这样的结构,本发明 结构设计合理,可以平稳高效的将金属圆管连续顺畅的逐个导送上料,提高金属圆管传送 9 CN 111573245 A 说 明 书 6/11 页 自动化程度,满足加工使用的需要。 附图说明 图1是本发明一种金属圆管连续导送上料装置的主视结构示意图。 图2是本发明的圆管落料机构的主视结构示意图。 图3是本发明的承管落料机构的主视结构示意图。 图4是本发明的圆管移送机构的主视结构示意图。 图5是本发明的落料转动圆盘和第二连接链条的连接俯视结构示意图。 图6是本发明的圆管移送承板及其相关机构的主视结构示意图。 图7是本发明的圆管移送机构的使用状态主视结构示意图。 图中:1. 圆管传送支架,2. 圆管落料机构,3. 圆管移送机构,4. 圆管落料导管, 5. 落料转动圆盘,6. 转动定位圆盘,7. 往复定位摆杆,8. 落料摆动承杆,9. 同步牵拉连 杆,10. 承管落料机构,11. 落料转动挡杆,12. 挡杆摆动导槽,13. 落管定位卡槽,14. 落 料主链轮,15. 落料辅链轮,16. 落料连接链条,17. 摆杆连接支座,18. 落管定位卡块, 19. 定位牵拉弹簧,20. 挡杆连接支座,21. 承杆往复导槽,22. 承杆复位拉簧,23. 承管 落料支架,24. 往复升降导杆,25. 承管往复导板,26. 圆管落料承杆,27. 推杆平移楔板, 28. 复位提升弹簧,29. 承杆升降导槽,30. 承杆平移推杆,31. 承杆复位拉簧,32. 承杆 复位挡板,33. 承杆平推导轮,34. 推杆转动凸轮,35. 承板平移摆杆,36. 圆管移送承板, 37. 平移限位支架,38. 第一连接链轮,39. 移管主齿轮,40. 移管辅齿轮,41. 第二连接 链轮,42. 第一连接链条,43. 第三连接链轮,44. 第四连接链轮,45. 第二连接链条,46. 摆杆复位拉簧,47. 平移限位导杆,48. 平移往复通道,49. 推板平移连杆,50. 圆管放置 通道,51. 圆管滚落斜面,52. 升降挡管杆,53. 挡杆升降通道,54. 齿轮转动支架,55. 第 一连接齿轮,56. 第二连接齿轮,57. 第一连接齿板,58. 第二连接齿板,59. 承管落料导 轮,60. 承杆缓冲胶层,61. 摆杆往复滚轮,62. 承管缓冲转板,63. 转板复位拉簧,64. 转 板放置卡槽,65. 平移支承滚轮,66. 承管斜面,67. 挡杆升降支架,68. 落管阻尼胶层。